SAWE Technical Papers
Technical Library
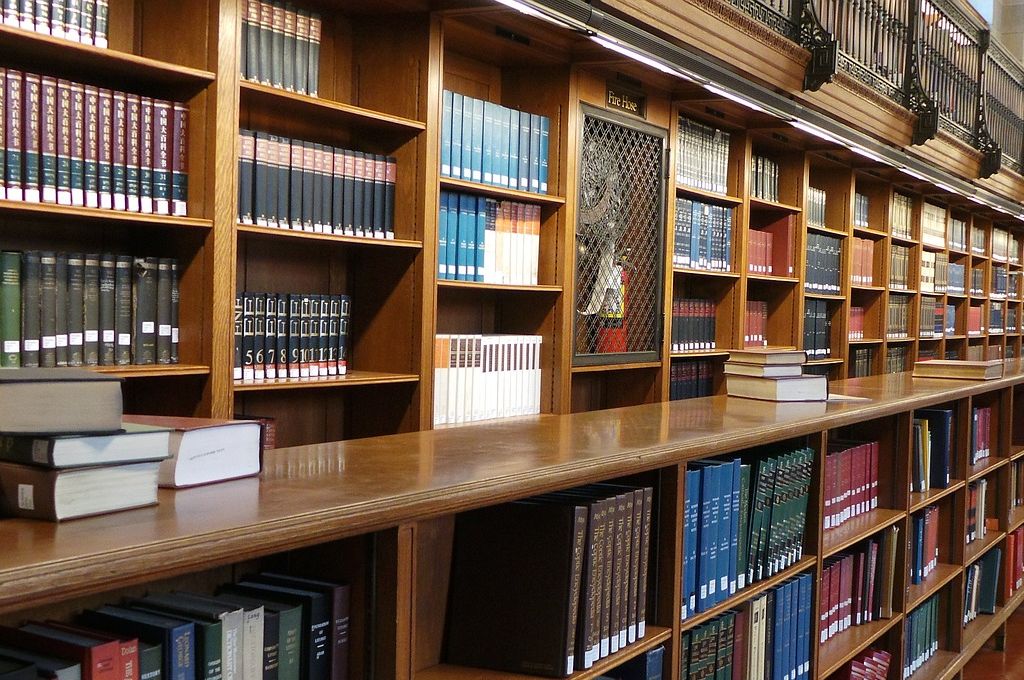
SAWE Paper Database
The SAWE Technical Library contains nearly 4000 technical papers available here for purchase and download. Use the search options below to find what you need.
3767. Determining Center of Gravity of Irregular-Shaped Bodies via Suspension Markovich, Emma In: 81st Annual Conference, Savannah, Georgia, pp. 23, Society of Allied Weight Engineers, Inc., Savannah, Georgia, 2022. Abstract | Buy/Download | BibTeX | Tags: 03. Center Of Gravity, Student Papers 3779. Determining the Center of Gravity of the Electric No Emissions Low Drag Airframe (NELDA) Haley, Christl K. In: 81st Annual Conference, Savannah, Georgia, pp. 27, Society of Allied Weight Engineers, Inc., Savannah, Georgia, 2022. Abstract | Buy/Download | BibTeX | Tags: 03. Center Of Gravity, 10. Weight Engineering - Aircraft Design, Student Papers 3771. A Look at Inclining Experiment Heel Angles: Measurement Tools and Sensitivity Tellet, David In: 2021 SAWE Tech Fair, pp. 27, Society of Allied Weight Engineers, Inc., Virtual Conference, 2021. Abstract | Buy/Download | BibTeX | Tags: 03. Center Of Gravity, Marine 3752. A Portable Device for Measuring the Cog: Design, Error Analysis and Calibration Previati, Giorgio; Ballo, Federico; Gobbi, Massimiliano In: 2020 SAWE Tech Fair, pp. 18, Society of Allied Weight Engineers, Inc., Virtual Conference, 2020. Abstract | Buy/Download | BibTeX | Tags: 03. Center Of Gravity, 09. Weighing Equipment 3725. HERMES: Hazard Examination and Reconnaissance Messenger for Extended Surveillance Sandoval, Alexander; Sotomayor, Alexis; Santori, Brandon; Adhikari, Brindan; Chen, Colin; He, Junzhe; Griego, Katelyn; Mejia, Marcos; Tenardi, Michely; Nyland, Quinter In: 78th Annual Conference, Norfolk, VA, pp. 11, Society of Allied Weight Engineers, Inc., Norfolk, Virginia, 2019. Abstract | Buy/Download | BibTeX | Tags: 03. Center Of Gravity, 31. Weight Engineering - Surface Transportation, 33. Unmanned Vehicles 3553. Vehicle Inertia Measurement Machine (VIMM) Wegener, Daniel In: 71st Annual Conference, Bad Gögging, Germany, pp. 11, Society of Allied Weight Engineers, Inc., Bad Gögging, Germany, 2012. Abstract | Buy/Download | BibTeX | Tags: 03. Center Of Gravity 3570. Center of Mass Uncertainty Coordinate Transformation Nakai, J H; Tsai, Wen In: 71st Annual Conference, Bad Gögging, Germany, pp. 73, Society of Allied Weight Engineers, Inc., Bad Gögging, Germany, 2012. Abstract | Buy/Download | BibTeX | Tags: 03. Center Of Gravity, 21. Weight Engineering - Statistical Studies 3491. The Secret Life of the Center of Gravity Zimmerman, Robert L.; Terry, Kristen M. In: 69th Annual Conference, Virginia Beach, Virginia, pp. 22, Society of Allied Weight Engineers, Inc., Virginia Beach, Virginia, 2010. Abstract | Buy/Download | BibTeX | Tags: 03. Center Of Gravity 3494. An Error Propagation Analysis of Small Engine Mass Properties Measurements Primozich, P. E. Anthony In: 69th Annual Conference, Virginia Beach, Virginia, pp. 16, Society of Allied Weight Engineers, Inc., Virginia Beach, Virginia, 2010. Abstract | Buy/Download | BibTeX | Tags: 03. Center Of Gravity, 08. Weighing, 17. Weight Engineering - Procedures 3500. Technical Feasibility Study for the Measurement of the Inertia Properties of an Aircraft Previati, Giorgio; Mastinu, G.; Gobbi, M. In: 69th Annual Conference, Virginia Beach, Virginia, pp. 21, Society of Allied Weight Engineers, Inc., Virginia Beach, Virginia, 2010. Abstract | Buy/Download | BibTeX | Tags: 03. Center Of Gravity, 06. Inertia Measurements, 32. Product of Inertia Measurement 3465. Advances on Inertia Tensor and Centre of Gravity Measurement: The Intenso+ System Previati, Giorgio; Mastinu, Giamiero; Gobbi, Massimiliano In: 68th Annual Conference, Wichita, Kansas, pp. 20, Wichita, Kansas, 2009. Abstract | Buy/Download | BibTeX | Tags: 03. Center Of Gravity, 32. Product of Inertia Measurement 3466. Feasibility Study for the Measurement of the Inertia Properties of Huge Bodies Previati, Giorgio; Mastinu, Giamiero; Gobbi, Massimiliano In: 68th Annual Conference, Wichita, Kansas, pp. 18, Wichita, Kansas, 2009. Abstract | Buy/Download | BibTeX | Tags: 03. Center Of Gravity, 32. Product of Inertia Measurement Vanginhoven, Paul; Ouellette, Andrew In: 68th Annual Conference, Wichita, Kansas, pp. 26, Wichita, Kansas, 2009. Abstract | Buy/Download | BibTeX | Tags: 02. Aircraft Loading - Payload, 03. Center Of Gravity Kalaghatagi, Amith In: 67th Annual Conference, Seattle, Washington, pp. 16, Seattle, Washington, 2008. Abstract | Buy/Download | BibTeX | Tags: 03. Center Of Gravity, 09. Weighing Equipment 3404. Weighing B747-400 Nose Up to Determine the Vertical Center of Gravity Pery, Asher In: 66th Annual Conference, Madrid, Spain, pp. 33, Society of Allied Weight Engineers Society of Allied Weight Engineers, Madrid, Spain, 2007. Abstract | Buy/Download | BibTeX | Tags: 03. Center Of Gravity, 08. Weighing 3381. Weight and Balance Management and Control: A Conceptual Integrated Balance Management Approach Shachar, Oran In: 65th Annual Conference, Valencia, California, pp. 14, Society of Allied Weight Engineers Society of Allied Weight Engineers, Valencia, California, 2006. Abstract | Buy/Download | BibTeX | Tags: 03. Center Of Gravity 3302. Some Considerations about Aircraft Center of Gravity Huber, Bernard In: 62nd Annual Conference, New Haven, Connecticut, pp. 110, Society of Allied Weight Engineers, Inc., New Haven, Connecticut, 2003. Abstract | Buy/Download | BibTeX | Tags: 03. Center Of Gravity Boynton, Richard; Weiner,; Kennedy, Paul; Rathbun, In: 62nd Annual Conference, New Haven, Connecticut, pp. 44, Society of Allied Weight Engineers, Inc., New Haven, Connecticut, 2003. Abstract | Buy/Download | BibTeX | Tags: 03. Center Of Gravity Boynton, Richard In: 61st Annual Conference, Virginia Beach, Virginia, May 18-22, pp. 22, Society of Allied Weight Engineers, Inc., Virginia Beach, Virginia, 2002. Abstract | Buy/Download | BibTeX | Tags: 03. Center Of Gravity 3130. Inertia Measurements of Large MilitaryVehicles Andretta,; Heydinger,; Bixel, R A; Coovert, In: 60th Annual Conference, Arlington, Texas, May 19-23, pp. 13, Society of Allied Weight Engineers, Inc., Arlington, Texas, 2001. Abstract | Buy/Download | BibTeX | Tags: 03. Center Of Gravity, 06. Inertia Measurements2022
@inproceedings{3767,
title = {3767. Determining Center of Gravity of Irregular-Shaped Bodies via Suspension},
author = {Emma Markovich},
url = {https://www.sawe.org/product/paper-3767},
year = {2022},
date = {2022-05-21},
urldate = {2022-05-21},
booktitle = {81st Annual Conference, Savannah, Georgia},
pages = {23},
publisher = {Society of Allied Weight Engineers, Inc.},
address = {Savannah, Georgia},
abstract = {The precise determination of the center of gravity of an aircraft is essential for the balance, stability, and overall safety of flight. Military aircraft often carry additional attachments, such as wing-mounted surveillance equipment, fuel tanks, or weaponry, which alter the weight and balance characteristics of the aircraft. In the application explored in this paper, a novel suspension system for determining the center of gravity of surveillance pods varying in shape and size is developed. This allows for the calculation of the center of gravity of aircraft attachments utilizing a two-point connection - the same attachment method as used on an aircraft. The tool features a hinged testbed that is suspended from a rigid frame by three load sensing devices. Two measurement sets are taken at different inclinations using an inverted three-point weighing method which allows the center of gravity to be calculated in all three dimensions. To recover measurement accuracy lost due to the limitation of inclination angles to less than 20 degrees, a high precision inclinometer is utilized. Based on the specifications of the sensing equipment and extensive Monte Carlo simulation of errors in force measurement, inclination angle, geometric dimensions, and data sampling, it is expected that the center of gravity can be reliably calculated to within 0.1 inches of the true value. Using the tool, objects ranging from 180 lb to 2000 lb with sizes of up to 12 x 4 x 4 feet can be measured with this accuracy. The modular design of the apparatus, data acquisition methods, and analysis relating to computation of the center of gravity will be presented. Additionally, the paper will discuss error analysis for the measurements, as well as verification and validation methods.},
keywords = {03. Center Of Gravity, Student Papers},
pubstate = {published},
tppubtype = {inproceedings}
}
@inproceedings{3779,
title = {3779. Determining the Center of Gravity of the Electric No Emissions Low Drag Airframe (NELDA)},
author = {Christl K. Haley},
url = {https://www.sawe.org/product/paper-3779},
year = {2022},
date = {2022-05-21},
urldate = {2022-05-21},
booktitle = {81st Annual Conference, Savannah, Georgia},
pages = {27},
publisher = {Society of Allied Weight Engineers, Inc.},
address = {Savannah, Georgia},
abstract = {Although climate change has become an impending issue for all of humanity, it has brought nations together to design and create a variety of systems that leave little to no carbon footprint. The No Emission Low Drag Airframe (NELDA) is a unique electric aircraft design which aims to join this world-wide mission. The author (the airframe design lead) and her senior design team from the University of Colorado Boulder spent the fall semester of 2021 designing this commuter aircraft. NELDA can fly 6 passengers at a cruise altitude of 12,000 ft MSL, at a cruise speed of 150 knots for 1.5 hours with a 30-minute reserve, making this a perfect aircraft for short, direct flights. The characteristics for this aircraft aim to be certified under Federal Aviation Regulation (FAR) 23 to ensure the safety of every passenger. Multiple trade studies were conducted to determine the design choices that make up this innovative aircraft. These studies resulted in an aft-mid-mounted wing, a canard, fixed tricycle landing gear, butterfly doors, and a pusher-propeller powertrain configuration. The specific energy, density, volume, and weight of the electric powertrain were estimated using a 5-year prediction for solid-state batteries. Since these batteries do not exist today, it was very challenging to accurately model and place the power system. The range and endurance of NELDA were used to determine the volume, number, and weight of the batteries. The safety of passengers, size of the batteries, and functionality of each battery were all considered while determining where and how to place the batteries among the other major components of NELDA. Additionally, it was critical to strategically place each of the components to achieve an acceptable static margin of 10%, as well as predictable dynamic and static flight characteristics. The designers of NELDA believe that their successful commuter electric airplane design will be part of the beginning of new, improved, clean aerial transportation.},
keywords = {03. Center Of Gravity, 10. Weight Engineering - Aircraft Design, Student Papers},
pubstate = {published},
tppubtype = {inproceedings}
}
2021
@inproceedings{3771,
title = {3771. A Look at Inclining Experiment Heel Angles: Measurement Tools and Sensitivity},
author = {David Tellet},
url = {https://www.sawe.org/product/paper-3771},
year = {2021},
date = {2021-11-01},
urldate = {2021-11-01},
booktitle = {2021 SAWE Tech Fair},
pages = {27},
publisher = {Society of Allied Weight Engineers, Inc.},
address = {Virtual Conference},
abstract = {An inclining experiment is used to indirectly measure the vertical center of gravity of a ship by measuring resultant heel angles for a given weight moved athwartships. The methods for measuring these angles are considered tried and true even though the uncertainties of their accuracy and precision are not well understood. This paper explores the impact of errors from traditional inclining methods and compares them with modern methods. The paper looks at a simulated inclining experiment and explores the change in results when errors are introduced into the measurements. It then looks at electronic inclinometers used in an actual inclining and discusses how that data can be analyzed and how that might affect the results of the experiment. Finally the paper discusses the advantages and disadvantages of old and new methods and provides recommendations for improved results from future inclinings.},
keywords = {03. Center Of Gravity, Marine},
pubstate = {published},
tppubtype = {inproceedings}
}
2020
@inproceedings{3752,
title = {3752. A Portable Device for Measuring the Cog: Design, Error Analysis and Calibration},
author = {Giorgio Previati and Federico Ballo and Massimiliano Gobbi},
url = {https://www.sawe.org/product/paper-3752},
year = {2020},
date = {2020-07-01},
booktitle = {2020 SAWE Tech Fair},
pages = {18},
publisher = {Society of Allied Weight Engineers, Inc.},
address = {Virtual Conference},
abstract = {The paper is devoted to the design, error estimation and calibration of a portable device for the measurement of the centre of gravity of rigid bodies. The device consists in a simple but effective implementation of the knife edge method. The design of the device including safety considerations is fully described. An error estimation approach is employed in the very early stage of the design to assess the required instrumentation accuracy and the manufacturing tolerances. A calibration of the portable device is performed by means of proper calibrated masses. After calibration, the accuracy of the device corresponds to the target accuracy defined in the a-priori error analysis.The design procedure described in the paper shows a straightforward approach for the design of devices for the measurement of the inertia properties. By such a procedure, it is possible to identify the most critical design areas and make the correct choices in the early stage of the design process. Also, a deep understanding of the measuring process can be gained allowing the definition of an effective calibration procedure.},
keywords = {03. Center Of Gravity, 09. Weighing Equipment},
pubstate = {published},
tppubtype = {inproceedings}
}
2019
@inproceedings{3725,
title = {3725. HERMES: Hazard Examination and Reconnaissance Messenger for Extended Surveillance},
author = {Alexander Sandoval and Alexis Sotomayor and Brandon Santori and Brindan Adhikari and Colin Chen and Junzhe He and Katelyn Griego and Marcos Mejia and Michely Tenardi and Quinter Nyland},
url = {https://www.sawe.org/product/paper-3725},
year = {2019},
date = {2019-05-01},
booktitle = {78th Annual Conference, Norfolk, VA},
pages = {11},
publisher = {Society of Allied Weight Engineers, Inc.},
address = {Norfolk, Virginia},
abstract = {The University of Colorado at Boulder Aerospace Engineering Senior Projects Team HERMES (Hazard Examination and Reconnaissance Messenger for Extended Surveillance) is currently designing, building, and testing a child scout rover (CSR). This is the fourth installment in the Jet Propulsion Laboratory's (JPL) Fire Tracker System. The Fire Tracker System is designed to operate in forest fire-prone areas for early fire identification. HERMES aims to improve the Fire Tracker System by navigating through a forest like environment to a location of interest (LOI) while determining a viable path for the Fire Tracker System's previous installment, a large less maneuverable mother rover. To do this, the CSR must traverse over obstacles up to 2.4 inches in height, vertical discontinuities (9 inches wide by 2.4 inches deep), over leaves, dirt, grass, and up or down 20 degree inclined slopes in both open and wooded area. Additionally, the CSR must drive forward and in reverse, as well as perform 360 degree turns in place. To complete these mission objectives, the CSR uses a sensor suite for obstacle and discontinuity detection, a two-motor configuration with a drivetrain and gearbox powering 6 wheels for traversing obstacles, and a moving linear mass stage that shifts the CSR's center of mass to enable traversing over discontinuities. While on a mission, the CSR will have the capability to detect any discontinuities using two downward angled, single beam LiDAR sensors. If a discontinuity is detected, the CSR will stop and notify the user at the ground station. The user at the ground station then commands the CSR into a semi-autonomous discontinuity traversal mode, where the CSR utilizes two ultrasonic sensors mounted on the bottom of the CSR to determine whether it is over a discontinuity or flat ground. These sensors signal the software to move the linear mass stage to shift the center of mass depending on the CSR's position over the discontinuity. The unique challenge of crossing discontinuities, and the solution, is discussed in this paper.},
keywords = {03. Center Of Gravity, 31. Weight Engineering - Surface Transportation, 33. Unmanned Vehicles},
pubstate = {published},
tppubtype = {inproceedings}
}
2012
@inproceedings{3553,
title = {3553. Vehicle Inertia Measurement Machine (VIMM)},
author = {Daniel Wegener},
url = {https://www.sawe.org/product/paper-3553},
year = {2012},
date = {2012-05-01},
booktitle = {71st Annual Conference, Bad Gögging, Germany},
pages = {11},
publisher = {Society of Allied Weight Engineers, Inc.},
address = {Bad Gögging, Germany},
abstract = {For the design of modern vehicles the knowledge of mass and moments of inertia is of great importance in terms of their vibration behaviour. Next to the type of incitation the inertia tensor (mass, position of centre of gravity, moments of inertia and products of inertia) is crucial for the translational and rotational vibration behaviour.
In vehicle development simulation models are used increasingly to investigate the dynamic behaviour of motor vehicles. These models are indispensable in the development of modern vehicle controls (e.g. ESP, antilock brake system). The knowledge of the inertia parameters of a vehicle is an important requirement to be able to represent a realistic driving behaviour in the simulation model.
Moreover, the inertia parameters of a vehicle are used for the evaluation of the rollover stability. The National Highway Traffic Safety Administration (NHTSA) awards 'stars' for classification of the roll over stability.
Because of this, the identification of parameters by measurement is of great importance and increasingly moves in the centre of interest of producers and public institutions.
Traditional test methods for the determination of vehicle parameters split the investigation in several processing steps, whereas for each inertia parameter a separate test is required. This leads to disadvantages with regard to the reproducibility of the measurement and the required time. Newer test benches use an active movement mechanism as well as a sensor system to detect the movement and the forces and moments, which affects the body. Therefore the technical burden on the active movement mechanism and the sensory is high.
A representative of those test benches is the VIMM (Vehicle Inertia Measuring Machine), which has been developed at ika. It is able to measure all inertia parameters and consists of a spherically seated platform, which can be moved by servo-hydraulic actuators around the three axes. The vehicle, whose inertia parameters are to be measured, is adapted on the platform. During the measurement the angular positions and the forces affecting the platform are measured. Afterwards the inertia parameters are calculated with these values.},
keywords = {03. Center Of Gravity},
pubstate = {published},
tppubtype = {inproceedings}
}
In vehicle development simulation models are used increasingly to investigate the dynamic behaviour of motor vehicles. These models are indispensable in the development of modern vehicle controls (e.g. ESP, antilock brake system). The knowledge of the inertia parameters of a vehicle is an important requirement to be able to represent a realistic driving behaviour in the simulation model.
Moreover, the inertia parameters of a vehicle are used for the evaluation of the rollover stability. The National Highway Traffic Safety Administration (NHTSA) awards 'stars' for classification of the roll over stability.
Because of this, the identification of parameters by measurement is of great importance and increasingly moves in the centre of interest of producers and public institutions.
Traditional test methods for the determination of vehicle parameters split the investigation in several processing steps, whereas for each inertia parameter a separate test is required. This leads to disadvantages with regard to the reproducibility of the measurement and the required time. Newer test benches use an active movement mechanism as well as a sensor system to detect the movement and the forces and moments, which affects the body. Therefore the technical burden on the active movement mechanism and the sensory is high.
A representative of those test benches is the VIMM (Vehicle Inertia Measuring Machine), which has been developed at ika. It is able to measure all inertia parameters and consists of a spherically seated platform, which can be moved by servo-hydraulic actuators around the three axes. The vehicle, whose inertia parameters are to be measured, is adapted on the platform. During the measurement the angular positions and the forces affecting the platform are measured. Afterwards the inertia parameters are calculated with these values.@inproceedings{3570,
title = {3570. Center of Mass Uncertainty Coordinate Transformation},
author = {J H Nakai and Wen Tsai},
url = {https://www.sawe.org/product/paper-3570},
year = {2012},
date = {2012-05-01},
booktitle = {71st Annual Conference, Bad Gögging, Germany},
pages = {73},
publisher = {Society of Allied Weight Engineers, Inc.},
address = {Bad Gögging, Germany},
abstract = {The center of mass (CM) is the mean location of all the system mass, and is typically expressed as a vector in a selected coordinate system. When combining CM data defined in multiple coordinate systems, coordinate transformations are performed using well-known vector transformation algorithms to bring data into a common coordinate system for summation or comparison. CM uncertainties (also known as dispersions) are typically expressed as a set of plus (+) and minus (-) values around the nominal value. CM uncertainties may be visualized as a volume of possible CM locations surrounding the mean value. Uncertainty coordinate transformation is not a well-defined process because it involves transforming boundaries of a volumetric region without a defined shape. There is currently no standard, well-documented method for transforming the coordinates of CM uncertainties. This situation has resulted in CM uncertainty data being handled inconsistently and incorrectly when coordinate transformations are applied. This paper proposes methods and algorithms for performing coordinate transformations on CM uncertainty data, and describes the pros and cons of the various approaches.},
keywords = {03. Center Of Gravity, 21. Weight Engineering - Statistical Studies},
pubstate = {published},
tppubtype = {inproceedings}
}
2010
@inproceedings{3491,
title = {3491. The Secret Life of the Center of Gravity},
author = {Robert L. Zimmerman and Kristen M. Terry},
url = {https://www.sawe.org/product/paper-3491},
year = {2010},
date = {2010-05-01},
booktitle = {69th Annual Conference, Virginia Beach, Virginia},
pages = {22},
publisher = {Society of Allied Weight Engineers, Inc.},
address = {Virginia Beach, Virginia},
abstract = {In the world of mass properties, indeed in the world at large, the mass property that gets all the 'press' is weight, or more correctly, mass. The unsung 'hero' of mass properties, with at least as much influence as mass in the behavior of an object in a force field, is the Center of Gravity.
The Center of Gravity exerts its influence in myriad ways. This paper presents a compendium of manifestations of the effect the CG has on an object's behavior, some of which are surprising even to those who have studied the growing field of mass properties engineering. As a result, the authors put forth the proposition that the Center of Gravity should be raised from secondary importance to primary in the mass properties hierarchy.},
keywords = {03. Center Of Gravity},
pubstate = {published},
tppubtype = {inproceedings}
}
The Center of Gravity exerts its influence in myriad ways. This paper presents a compendium of manifestations of the effect the CG has on an object's behavior, some of which are surprising even to those who have studied the growing field of mass properties engineering. As a result, the authors put forth the proposition that the Center of Gravity should be raised from secondary importance to primary in the mass properties hierarchy.@inproceedings{3494,
title = {3494. An Error Propagation Analysis of Small Engine Mass Properties Measurements},
author = {P. E. Anthony Primozich},
url = {https://www.sawe.org/product/paper-3494},
year = {2010},
date = {2010-05-01},
booktitle = {69th Annual Conference, Virginia Beach, Virginia},
pages = {16},
publisher = {Society of Allied Weight Engineers, Inc.},
address = {Virginia Beach, Virginia},
abstract = {This paper investigates the impact of measurement error propagation on the accuracy of calculated weights and centers of gravity of small turbofan engines. Three variations of the two-load-cell crane-and-cable weighing technique were explored. The potential sources of measurement error were identified and analytical expressions for calculating the total error in the weight and center of gravity calculations were derived. A generic engine example was used to conduct a sensitivity analysis to illustrate the magnitude of error that could result from various weighing configurations. Results show that incorrect mass properties values can have an effect on modern aircraft flying qualities, such as fuel burn, aircraft handling, and trim.},
keywords = {03. Center Of Gravity, 08. Weighing, 17. Weight Engineering - Procedures},
pubstate = {published},
tppubtype = {inproceedings}
}
@inproceedings{3500,
title = {3500. Technical Feasibility Study for the Measurement of the Inertia Properties of an Aircraft},
author = {Giorgio Previati and G. Mastinu and M. Gobbi},
url = {https://www.sawe.org/product/paper-3500},
year = {2010},
date = {2010-05-01},
booktitle = {69th Annual Conference, Virginia Beach, Virginia},
pages = {21},
publisher = {Society of Allied Weight Engineers, Inc.},
address = {Virginia Beach, Virginia},
abstract = {A feasibility study for the measurement of the inertia properties of a full-scale aircraft is presented. The employment of the InTenso+ system developed at Politecnico di Milano is discussed referring to the measurement of the inertia properties of a fighter aircraft. Preliminarily, the InTenso+ system is introduced to highlight its basic features. Then, referring to the addressed non standard aeronautic application, the accuracy of the measurement method is investigated. Both analytical and numerical analyses are presented to estimate the uncertainties of the measurement method. The measurement of the inertia properties of a full scale aircraft is technically feasible within the accuracy quantified in this report. Economic and financial issues are not critical, being the InTenso+ system very simple and consequently inexpensive (the implementation costs are not given in this paper as they depend on the customization of the system). The main result of this paper is that, maybe for the first time since the beginning of aeronautical engineering, the measurement of the full inertia tensor and of the location of the centre of gravity of aircrafts appears feasible in a simple way. Such a measurement can be performed by using the InTenso+ system.},
keywords = {03. Center Of Gravity, 06. Inertia Measurements, 32. Product of Inertia Measurement},
pubstate = {published},
tppubtype = {inproceedings}
}
2009
@inproceedings{3465,
title = {3465. Advances on Inertia Tensor and Centre of Gravity Measurement: The Intenso+ System},
author = {Giorgio Previati and Giamiero Mastinu and Massimiliano Gobbi},
url = {https://www.sawe.org/product/paper-3465},
year = {2009},
date = {2009-05-01},
booktitle = {68th Annual Conference, Wichita, Kansas},
pages = {20},
address = {Wichita, Kansas},
abstract = {The accurate and quick measurement of the inertia properties of rigid bodies is dealt with in the paper. Firstly, a survey of the current measurement/identification methods is given, highlighting the expected accuracy and practical implementation issues for each method. The test rigs developed at the Politecnico di Milano (Technical University of Milan) for the identification of the inertia properties are
presented. These test rigs (named InTenso and InTensino, being InTensino just a scaled version of the InTenso system) have been in use since 2001 for the identification of the inertia tensor of rigid bodies ranging from 50 to 3500 kg. Such test rigs are multi-cable/rod pendulums carrying the body under identification. The cables can be configured in order to let the body swing around (approximately) its
centre of mass. From the recorded motion the inertia tensor is identified by a proper numerical procedure.
In the second part of the paper, the attention is focused on a new implementation of the InTenso and
InTensino test rigs. In such a new implementation, the new test rigs (InTenso+ and InTensino+) are able to identify both the inertia tensor and the centre of gravity location during one single experiment. Due to the very simple hardware and instrumentation involved, the very short measurement time and the
relatively high accuracy, these test rigs seem suitable for commercial development.},
keywords = {03. Center Of Gravity, 32. Product of Inertia Measurement},
pubstate = {published},
tppubtype = {inproceedings}
}
presented. These test rigs (named InTenso and InTensino, being InTensino just a scaled version of the InTenso system) have been in use since 2001 for the identification of the inertia tensor of rigid bodies ranging from 50 to 3500 kg. Such test rigs are multi-cable/rod pendulums carrying the body under identification. The cables can be configured in order to let the body swing around (approximately) its
centre of mass. From the recorded motion the inertia tensor is identified by a proper numerical procedure.
In the second part of the paper, the attention is focused on a new implementation of the InTenso and
InTensino test rigs. In such a new implementation, the new test rigs (InTenso+ and InTensino+) are able to identify both the inertia tensor and the centre of gravity location during one single experiment. Due to the very simple hardware and instrumentation involved, the very short measurement time and the
relatively high accuracy, these test rigs seem suitable for commercial development.@inproceedings{3466,
title = {3466. Feasibility Study for the Measurement of the Inertia Properties of Huge Bodies},
author = {Giorgio Previati and Giamiero Mastinu and Massimiliano Gobbi},
url = {https://www.sawe.org/product/paper-3466},
year = {2009},
date = {2009-05-01},
booktitle = {68th Annual Conference, Wichita, Kansas},
pages = {18},
address = {Wichita, Kansas},
abstract = {The identification of the inertial properties of complex bodies is a well discussed issue. The importance of the accurate knowledge of these quantities for the correct simulation of mechanical systems has been recognized by many authors. In the literature, many different methods and often complicated test rigs have been proposed. In most cases these test rigs are able to identify the inertia properties of compact bodies and in only few cases body as large as ground vehicles can be measured. At the best knowledge of the authors methods for the measurement of the inertia tensor of very large rigid bodies such as airplanes and ships have not been yet proposed.
In this paper the feasibility of such measurements is discussed. The proposed method is based on the test rig for the measurement of the inertial properties of car vehicle size rigid bodies developed at the Politecnico di Milano (Technical University of Milan). This test rig is basically a three or four bar pendulums carrying the body under investigation. The body is made rotate around three axes passing nearby the body centre of gravity and the resulting highly non linear motion is recorded. By a proper identification procedure, the centre of gravity location and the inertia tensor can be assessed with a single experimental test. The absence of any dynamic excitation of the motion of the system makes this method suitable for the very large bodies discussed here.},
keywords = {03. Center Of Gravity, 32. Product of Inertia Measurement},
pubstate = {published},
tppubtype = {inproceedings}
}
In this paper the feasibility of such measurements is discussed. The proposed method is based on the test rig for the measurement of the inertial properties of car vehicle size rigid bodies developed at the Politecnico di Milano (Technical University of Milan). This test rig is basically a three or four bar pendulums carrying the body under investigation. The body is made rotate around three axes passing nearby the body centre of gravity and the resulting highly non linear motion is recorded. By a proper identification procedure, the centre of gravity location and the inertia tensor can be assessed with a single experimental test. The absence of any dynamic excitation of the motion of the system makes this method suitable for the very large bodies discussed here.@inproceedings{3472,
title = {3472. Factors Affecting and Methods for the Prevention of Freighter Aircraft Tipping During Ground Operations},
author = {Paul Vanginhoven and Andrew Ouellette},
url = {https://www.sawe.org/product/paper-3472},
year = {2009},
date = {2009-05-01},
booktitle = {68th Annual Conference, Wichita, Kansas},
pages = {26},
address = {Wichita, Kansas},
abstract = {Since the design of commercial civil aircraft evolved into a tricycle landing gear
configuration to improve ground handling and landing characteristics over the taildragger arrangement, weight/balance engineers and load masters have had to contend with the potentially catastrophic concern of an airplane tipping onto its tail during load/unload. A carelessly placed pallet on a particularly sensitive aircraft can result in severe injury to ground personnel and millions of dollars of damage to an aircraft.
This paper will explore the considerations that make an aircraft more or less susceptible to tipping, briefly explain analysis methods used to determine tip sensitivity, and discuss methods both current and proposed to prevent tip up.
The paper will show:
- Tip-up to be a practical problem in need of a solution through the use of
historical examples.
- How environmental factors can influence an aircraft's susceptibility to tipping.
- Some general aircraft configuration differences that have major influences on
aircraft ground stability.
- That load sequencing is the most important factor to consider in tip prevention.
- Methods, with varying degrees of complexity and effectiveness, that are
currently in use to prevent tip-up incidents.
- How the latest Boeing designed tip alarm on the 777F provides an effective and
simple method for alerting ground crews of a potentially hazardous situation.},
keywords = {02. Aircraft Loading - Payload, 03. Center Of Gravity},
pubstate = {published},
tppubtype = {inproceedings}
}
configuration to improve ground handling and landing characteristics over the taildragger arrangement, weight/balance engineers and load masters have had to contend with the potentially catastrophic concern of an airplane tipping onto its tail during load/unload. A carelessly placed pallet on a particularly sensitive aircraft can result in severe injury to ground personnel and millions of dollars of damage to an aircraft.
This paper will explore the considerations that make an aircraft more or less susceptible to tipping, briefly explain analysis methods used to determine tip sensitivity, and discuss methods both current and proposed to prevent tip up.
The paper will show:
- Tip-up to be a practical problem in need of a solution through the use of
historical examples.
- How environmental factors can influence an aircraft's susceptibility to tipping.
- Some general aircraft configuration differences that have major influences on
aircraft ground stability.
- That load sequencing is the most important factor to consider in tip prevention.
- Methods, with varying degrees of complexity and effectiveness, that are
currently in use to prevent tip-up incidents.
- How the latest Boeing designed tip alarm on the 777F provides an effective and
simple method for alerting ground crews of a potentially hazardous situation.2008
@inproceedings{3436,
title = {3436. Instant CG},
author = {Amith Kalaghatagi},
url = {https://www.sawe.org/product/paper-3436},
year = {2008},
date = {2008-05-01},
booktitle = {67th Annual Conference, Seattle, Washington},
pages = {16},
address = {Seattle, Washington},
abstract = {This paper describes in detail a method to measure the CG of any aircraft at any pitch angle, without having to adjust the aircraft to flight level conditions. This method reduces the time required for weighing, eliminates human error, and eliminates possibility of aircraft damage due to jacking accidents and possibility of injury to weighing personnel. This method is applicable to all aircraft types and configurations. A system of linear equations is solved to compute the CG of the aircraft. The known variables in the system of equations are the pitch angle, oleo extensions and the wheel reactions. The unknowns in the system are the Weight, Arm lengths and CG. The first equation of the system consists of the Moment of all forces computed about the Reference Datum. The remaining equations consist of the functions defining the relation between Arm lengths with respect to the Reference Datum for each wheel and the Oleo extensions of the respective wheels. The pitch angle is measured accurately within one-tenths of a degree, the oleo extensions are measured accurately within one-hundredths of an inch and the wheel reactions within one pound. For each aircraft configuration, we use a GEC custom complex algorithm to compute the arm lengths from the measured oleo extensions. Once the aircraft is rolled onto the GEC platform scales, the reactions are wirelessly transmitted to the GEC handheld equipment through RF. The pitch angle and the oleo extensions are measured and manually entered into the GEC handheld. With these input variables the CG, %MAC and Total Weight of the aircraft are instantaneously computed by the GEC handheld equipment. A test aircraft was weighed both level and off-level to test the algorithm. The computed CG was within 0.1 inches and the %MAC was within 0.1%.},
keywords = {03. Center Of Gravity, 09. Weighing Equipment},
pubstate = {published},
tppubtype = {inproceedings}
}
2007
@inproceedings{3404,
title = {3404. Weighing B747-400 Nose Up to Determine the Vertical Center of Gravity},
author = {Asher Pery},
url = {https://www.sawe.org/product/paper-3404},
year = {2007},
date = {2007-05-01},
booktitle = {66th Annual Conference, Madrid, Spain},
pages = {33},
publisher = {Society of Allied Weight Engineers},
address = {Madrid, Spain},
organization = {Society of Allied Weight Engineers},
abstract = {The report describes in detail the test carried out at Israel Aerospace Industries (IAI) in January 2006 to determine the vertical center of gravity of the Boeing 747-400 airplane. The Boeing 747-400 airplane underwent a conversion to an all cargo aircraft at IAI. IAI was therefore required to substantiate the conversion modifications for an airplane of another manufacturer. The vertical center of gravity is one of the parameters required in the analysis for the aircraft loads and dynamics, control and stability, ground loads, dynamic braking, and loadability. Essentially the method in the test was to weigh the airplane in two different airplane attitudes. The first weighing was performed with the aircraft in level attitude. Then the aircraft was lifted at the nose wheel and weighed again in the nose up position. The report includes full details of the setup (including photos), actual test results, computations, and evaluation of the tolerances. A derivation to in service cargo configuration is included. The results obtained were considered to be very satisfactory. It is our hope that this report will be of practical help to anyone who wishes to carry out a similar test on a large airplane.},
keywords = {03. Center Of Gravity, 08. Weighing},
pubstate = {published},
tppubtype = {inproceedings}
}
2006
@inproceedings{3381,
title = {3381. Weight and Balance Management and Control: A Conceptual Integrated Balance Management Approach},
author = {Oran Shachar},
url = {https://www.sawe.org/product/paper-3381},
year = {2006},
date = {2006-05-01},
booktitle = {65th Annual Conference, Valencia, California},
pages = {14},
publisher = {Society of Allied Weight Engineers},
address = {Valencia, California},
organization = {Society of Allied Weight Engineers},
abstract = {Each aircraft has a definition of an approved Weight and Balance envelope during all phases of flight. The current used methodology derives non- optimal usage of resources. The Integrated Balance Management ("I.B.M.") suggests a new fashioned definition to the approved envelope for the basic aircraft, while taking into consideration other parameters that were not involved in the described indirect approach. The methodology suggested here defines optimal regimes in the aspects of maintenance, Performance and W&B, therefore asks for a unique intersection of each polygon in the W-CG diagram. The conceptual methodology suggested here is still under investigation. Nevertheless, the integration of the indirect approach into the I.B.M. polygon has its own promise to develop the same level of safety of flight, while reducing the maintenance costs, and increasing the specific range of the aircraft.},
keywords = {03. Center Of Gravity},
pubstate = {published},
tppubtype = {inproceedings}
}
2003
@inproceedings{3302,
title = {3302. Some Considerations about Aircraft Center of Gravity},
author = {Bernard Huber},
url = {https://www.sawe.org/product/paper-3302},
year = {2003},
date = {2003-05-01},
booktitle = {62nd Annual Conference, New Haven, Connecticut},
pages = {110},
publisher = {Society of Allied Weight Engineers, Inc.},
address = {New Haven, Connecticut},
abstract = {Why is the center of gravity so important for an aircraft? Handling qualities, stability, loads depend on center of gravity position. Unacceptable domains exist where flying the aircraft could be hazardous, difficult, and even dangerous. An aircraft has to stay within a center of gravity domain and therefore has center of gravity limits. In general operation mode, a passenger civil subsonic aircraft only has longitudinal center of gravity limits depending on the aircraft weight and the flight phase: take-off, flight, or landing. If lateral and vertical limits exist, they are not usually reached in operation on passenger civil subsonic aircraft. This paper gives an overview of this technical subject: the aircraft center of gravity.
First preliminary definitions are given: center of gravity, reference axis, reference chord, center of gravity calculation, center of gravity diagram, certified center of gravity limits, aircraft loading, and operational center of gravity limits.
The origins of these longitudinal, lateral, and vertical limits are then explained, such as the determination and control of the aircraft center of gravity.
The longitudinal limits include handling qualities, loads, and loadability. We examine the impact that limits have on the aircraft definition. Then loadability considerations in the preliminary phase are considered. A loadability index is defined to measure the loadability of an aircraft and to permit comparison between different configurations and aircraft. The impact of fuel management and fuel transfer is analyzed, as well as how limits can be redefined for derived aircraft. On supersonic aircraft, longitudinal limits also depend on speed (mach number). This property is illustrated by the example of the Concorde. The center of gravity determination and control during operation are shown.
Lateral limits have properties similar to the longitudinal ones but generally are such that they do not lead to operational constraints.
Vertical limits generally appear on cargo aircraft. The example of an A300-600 Super Transporter (Beluga) is shown with the presentation of its limits and the measure of vertical CG for the empty aircraft.
Finally the certified weight-center of gravity domain has to be explored during flight tests. The flight test installation must allow achieving any point of this domain. A340-500/-600 flight test installations are shown.
In conclusion, the apparently simple technical subject, aircraft center of gravity, is not so simple and is very large, so it was not possible in one paper to go deeper in some points (operational limits, handling qualities) and also some other points were not treated (CG variation due to fuel, with pitch and roll angles, in static, in dynamic: fuel slosh effect; flexible aircraft; risks of exceeding the limits). But nevertheless the objective was to give a good understanding of what is behind the aircraft center of gravity, from the aircraft definition, architecture of CG control by airlines in operation, to explain where the limits came from, to show that the incorporation of loadability during preliminary design is a necessity of the aircraft sizing process, what is done by the manufacturers to optimize the aircraft, if there are loading constraints where they came from, and the benefits for the aircraft.},
keywords = {03. Center Of Gravity},
pubstate = {published},
tppubtype = {inproceedings}
}
First preliminary definitions are given: center of gravity, reference axis, reference chord, center of gravity calculation, center of gravity diagram, certified center of gravity limits, aircraft loading, and operational center of gravity limits.
The origins of these longitudinal, lateral, and vertical limits are then explained, such as the determination and control of the aircraft center of gravity.
The longitudinal limits include handling qualities, loads, and loadability. We examine the impact that limits have on the aircraft definition. Then loadability considerations in the preliminary phase are considered. A loadability index is defined to measure the loadability of an aircraft and to permit comparison between different configurations and aircraft. The impact of fuel management and fuel transfer is analyzed, as well as how limits can be redefined for derived aircraft. On supersonic aircraft, longitudinal limits also depend on speed (mach number). This property is illustrated by the example of the Concorde. The center of gravity determination and control during operation are shown.
Lateral limits have properties similar to the longitudinal ones but generally are such that they do not lead to operational constraints.
Vertical limits generally appear on cargo aircraft. The example of an A300-600 Super Transporter (Beluga) is shown with the presentation of its limits and the measure of vertical CG for the empty aircraft.
Finally the certified weight-center of gravity domain has to be explored during flight tests. The flight test installation must allow achieving any point of this domain. A340-500/-600 flight test installations are shown.
In conclusion, the apparently simple technical subject, aircraft center of gravity, is not so simple and is very large, so it was not possible in one paper to go deeper in some points (operational limits, handling qualities) and also some other points were not treated (CG variation due to fuel, with pitch and roll angles, in static, in dynamic: fuel slosh effect; flexible aircraft; risks of exceeding the limits). But nevertheless the objective was to give a good understanding of what is behind the aircraft center of gravity, from the aircraft definition, architecture of CG control by airlines in operation, to explain where the limits came from, to show that the incorporation of loadability during preliminary design is a necessity of the aircraft sizing process, what is done by the manufacturers to optimize the aircraft, if there are loading constraints where they came from, and the benefits for the aircraft.@inproceedings{3320,
title = {3320. Static Balancing a Device with Two or More Degrees of Freedom - (The Key to Obtaining High Performance on Gimbled Missile},
author = {Richard Boynton and Weiner and Paul Kennedy and Rathbun},
url = {https://www.sawe.org/product/paper-3320},
year = {2003},
date = {2003-05-01},
booktitle = {62nd Annual Conference, New Haven, Connecticut},
pages = {44},
publisher = {Society of Allied Weight Engineers, Inc.},
address = {New Haven, Connecticut},
abstract = {When a police officer in a helicopter is trying to use a telescope to read a license plate on a car, it is vital that the image not jitter; otherwise it will be too blurred to read. There is a constant vibration on a helicopter, plus there are g forces introduced by the motion of the helicopter. Normally, these external forces would cause the telescope image to jump around. However, if the telescope is balanced so its CG is exactly at the center of rotation of the gimbaled mount, then the image miraculously settles down.
The same dramatic improvement in performance occurs when a gimbaled seeker in a missile or smart weapon is balanced. In addition to affecting targeting accuracy, the degree of balance is the driving force that determines the torque requirement of the positioning motors in the seeker. If the seeker can be balanced with high precision, then the motors can be made much smaller, allowing the entire seeker to decrease in size. So this is a case where center of gravity control drives the limits of performance and also sets the requirements for basic elements in the design.
In addition to unbalance due to CG offset, unbalance due to product of inertia is a critical factor in the performance of a seeker. Rapid changes in direction introduce disturbing forces if the principal axes of the seeker are not coincident with the rotational axes. This paper outlines the current state of the art in gimbal balance. Some questions answered in this paper are:
1. How do you balance a gimbaled device (such as a missile seeker)?
2. Where should you locate the ballast weights on the gimbaled device for optimum reduction of unbalance?
3. How do you calculate the position and mass of the ballast weights, given that the seeker has at least two degrees of freedom, and sometimes has as many as five?
4. How do you fixture the seeker in the gimbal balance instrument?
5. How do you minimize practical limitations to minimum unbalance such as wire bundle movement and uncertainty in protective cover location?
6. What considerations should be given to minimizing product of inertia?
The gimbal balance machine described in this paper is one of the most accurate mechanical measuring devices in the world. The full-scale moment of each axis is 10,000 g-cm. The readability of the moment measurement is 0.03 g-cm, and the combined error due to drift, moment uncertainty, and linearity when measuring the final unbalance of a gimbal after ballast correction is 0.1 g-cm. This is a 0.001% error expressed in terms of full-scale moment! In other words, the gimbal balance machine is capable of reliably detecting unbalance as small as 1 part in 100,000. It is often hard for engineers to fully appreciate the incredible accuracy of this balancing machine. What makes this even more remarkable is that we now are able to achieve this with a single range of readout. It is no longer necessary to switch ranges as the unbalance is reduced. This extraordinary performance has driven the industry. Missile seekers can now be made smaller and lighter because the higher degree of balance has reduced the torque requirements on the positioning motors.},
keywords = {03. Center Of Gravity},
pubstate = {published},
tppubtype = {inproceedings}
}
The same dramatic improvement in performance occurs when a gimbaled seeker in a missile or smart weapon is balanced. In addition to affecting targeting accuracy, the degree of balance is the driving force that determines the torque requirement of the positioning motors in the seeker. If the seeker can be balanced with high precision, then the motors can be made much smaller, allowing the entire seeker to decrease in size. So this is a case where center of gravity control drives the limits of performance and also sets the requirements for basic elements in the design.
In addition to unbalance due to CG offset, unbalance due to product of inertia is a critical factor in the performance of a seeker. Rapid changes in direction introduce disturbing forces if the principal axes of the seeker are not coincident with the rotational axes. This paper outlines the current state of the art in gimbal balance. Some questions answered in this paper are:
1. How do you balance a gimbaled device (such as a missile seeker)?
2. Where should you locate the ballast weights on the gimbaled device for optimum reduction of unbalance?
3. How do you calculate the position and mass of the ballast weights, given that the seeker has at least two degrees of freedom, and sometimes has as many as five?
4. How do you fixture the seeker in the gimbal balance instrument?
5. How do you minimize practical limitations to minimum unbalance such as wire bundle movement and uncertainty in protective cover location?
6. What considerations should be given to minimizing product of inertia?
The gimbal balance machine described in this paper is one of the most accurate mechanical measuring devices in the world. The full-scale moment of each axis is 10,000 g-cm. The readability of the moment measurement is 0.03 g-cm, and the combined error due to drift, moment uncertainty, and linearity when measuring the final unbalance of a gimbal after ballast correction is 0.1 g-cm. This is a 0.001% error expressed in terms of full-scale moment! In other words, the gimbal balance machine is capable of reliably detecting unbalance as small as 1 part in 100,000. It is often hard for engineers to fully appreciate the incredible accuracy of this balancing machine. What makes this even more remarkable is that we now are able to achieve this with a single range of readout. It is no longer necessary to switch ranges as the unbalance is reduced. This extraordinary performance has driven the industry. Missile seekers can now be made smaller and lighter because the higher degree of balance has reduced the torque requirements on the positioning motors.2002
@inproceedings{3238,
title = {3238. Measuring weight and all three axes of center of gravity of a rocket motor without having to reposition the motor},
author = {Richard Boynton},
url = {https://www.sawe.org/product/paper-3238},
year = {2002},
date = {2002-05-01},
booktitle = {61st Annual Conference, Virginia Beach, Virginia, May 18-22},
pages = {22},
publisher = {Society of Allied Weight Engineers, Inc.},
address = {Virginia Beach, Virginia},
abstract = {Large live rocket motors are dangerous and time consuming to move. Therefore, it is advantageous to measure mass properties with a minimum of handling operations. This paper describes an instrument, which is capable of measuring weight and all three axes of center of gravity in a single setup. Two axes are measured using a reaction type two-axis CG instrument. The mounting surface of the machine then tilts to measure the third axis. By using force restoration technology and flexure pivots, CG measurement accuracy is in the order of a few thousandths of an inch. Weight and CG are measured independently by using a parallelogram structure with a single force transducer, upon which are mounted the X and Y moment measuring structure. This permits optimization of the design. This paper discusses details of the process and the means of verifying the accuracy of the instrument, using a mass properties standard that has been designed to permit the application of work reversal techniques.},
keywords = {03. Center Of Gravity},
pubstate = {published},
tppubtype = {inproceedings}
}
2001
@inproceedings{3130,
title = {3130. Inertia Measurements of Large MilitaryVehicles},
author = {Andretta and Heydinger and R A Bixel and Coovert},
url = {https://www.sawe.org/product/paper-3130},
year = {2001},
date = {2001-05-01},
booktitle = {60th Annual Conference, Arlington, Texas, May 19-23},
pages = {13},
publisher = {Society of Allied Weight Engineers, Inc.},
address = {Arlington, Texas},
abstract = {This paper describes the design and operation of a facility for measuring vehicle center-of-gravity height; roll, pitch, and yaw moments of inertia; and roll/yaw cross product of inertia for a broad range of test specimens. The facility is configurable such that it is capable of measuring these properties for light, single axle trailers; long, heavy vehicles; and tank turrets. The design was driven by the need for accurate, repeatable measurement results and the desire to have a single facility capable of making measurements on a broad range of vehicle sizes.},
keywords = {03. Center Of Gravity, 06. Inertia Measurements},
pubstate = {published},
tppubtype = {inproceedings}
}