SAWE Technical Papers
Technical Library
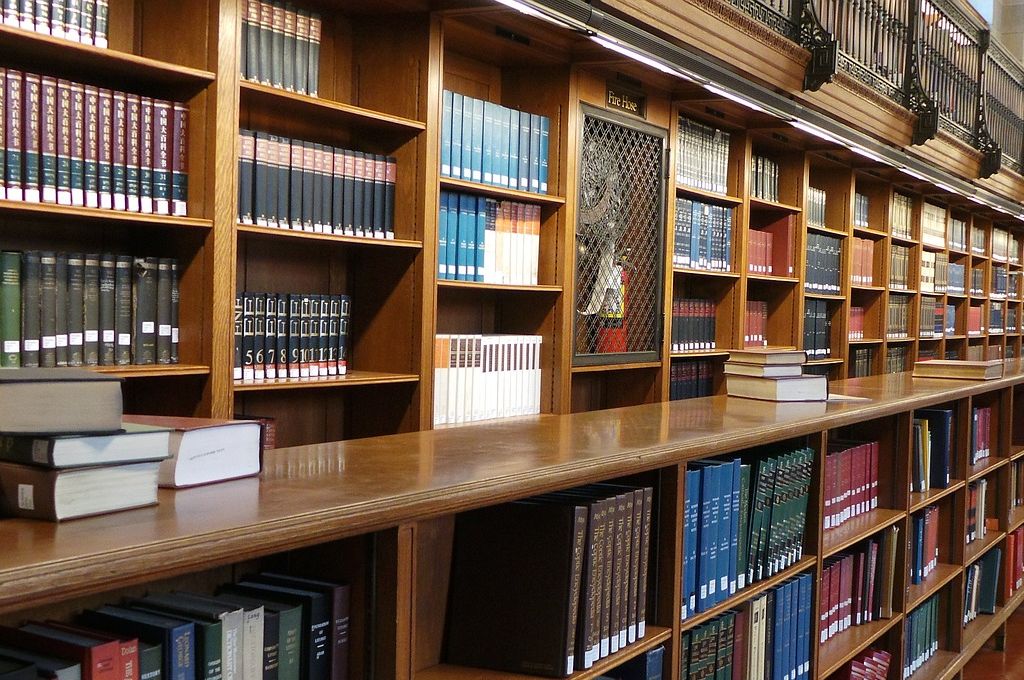
SAWE Paper Database
The SAWE Technical Library contains nearly 4000 technical papers available here for purchase and download. Use the search options below to find what you need.
3766. Mass Properties and Automotive Braking Wiegand, Brian Paul In: 81st Annual Conference, Savannah, Georgia, pp. 63, Society of Allied Weight Engineers, Inc., Savannah, Georgia, 2022. Abstract | Buy/Download | BibTeX | Tags: 31. Weight Engineering - Surface Transportation 3770. Mass Management of a High Energy-Efficient Battery Electric Vehicle Stabile, Pietro; Ballo, Federico; Previati, Giorgio In: 81st Annual Conference, Savannah, Georgia, pp. 15, Society of Allied Weight Engineers, Inc., Savannah, Georgia, 2022. Abstract | Buy/Download | BibTeX | Tags: 31. Weight Engineering - Surface Transportation, Student Papers 3775. Influence of the Inertia Parameters on a Dynamic Driving Simulator Performances Previati, Giorgio; Mastinu, Gianpiero; Gobbi, Massimiliano In: 81st Annual Conference, Savannah, Georgia, pp. 14, Society of Allied Weight Engineers, Inc., Savannah, Georgia, 2022. Abstract | Buy/Download | BibTeX | Tags: 05. Inertia Calculations, 31. Weight Engineering - Surface Transportation 3765. Mass Properties and Automotive Directional Stability Wiegand, B P In: 2021 SAWE Tech Fair, pp. 61, Society of Allied Weight Engineers, Inc., Virtual Conference, 2021. Abstract | Buy/Download | BibTeX | Tags: 31. Weight Engineering - Surface Transportation Stegmiller, Marcus; Albers, Albert In: 78th Annual Conference, Norfolk, VA, pp. 18, Society of Allied Weight Engineers, Inc., Norfolk, Virginia, 2019. Abstract | Buy/Download | BibTeX | Tags: 31. Weight Engineering - Surface Transportation 3725. HERMES: Hazard Examination and Reconnaissance Messenger for Extended Surveillance Sandoval, Alexander; Sotomayor, Alexis; Santori, Brandon; Adhikari, Brindan; Chen, Colin; He, Junzhe; Griego, Katelyn; Mejia, Marcos; Tenardi, Michely; Nyland, Quinter In: 78th Annual Conference, Norfolk, VA, pp. 11, Society of Allied Weight Engineers, Inc., Norfolk, Virginia, 2019. Abstract | Buy/Download | BibTeX | Tags: 03. Center Of Gravity, 31. Weight Engineering - Surface Transportation, 33. Unmanned Vehicles 3602. Mass Properties and Advanced Automotive Design Wiegand, B P In: 74th Annual Conference, Alexandria, Virginia, pp. 325, Society of Allied Weight Engineers, Inc., Alexandria, Virginia, 2015, (Revision C (2016)). Abstract | Buy/Download | BibTeX | Tags: 31. Weight Engineering - Surface Transportation 3634. Mass Properties and Automotive Crash Survival Wiegand, B P In: 74th Annual Conference, Alexandria, Virginia, pp. 145, Society of Allied Weight Engineers, Inc., Alexandria, Virginia, 2015. Abstract | Buy/Download | BibTeX | Tags: 31. Weight Engineering - Surface Transportation 3640. Colin Chapman and Automotive Mass Properties Wiegand, B P In: 74th Annual Conference, Alexandria, Virginia, pp. 75, Society of Allied Weight Engineers, Inc., Alexandria, Virginia, 2015. Abstract | Buy/Download | BibTeX | Tags: 31. Weight Engineering - Surface Transportation 3521. Mass Properties and Automotive Vertical Acceleration Wiegand, B P In: 70th Annual Conference, Houstion, Texas, pp. 112, Society of Allied Weight Engineers, Inc., Houston, Texas, 2011, (Mike Hackney Best Paper Award). Abstract | Buy/Download | BibTeX | Tags: 31. Weight Engineering - Surface Transportation, Mike Hackney Best Paper Award 3528. Mass Properties and Automotive Lateral Accelerations Wiegand, B P In: 70th Annual Conference, Houstion, Texas, pp. 92, Society of Allied Weight Engineers, Inc., Houston, Texas, 2011. Abstract | Buy/Download | BibTeX | Tags: 31. Weight Engineering - Surface Transportation 3490. Automotive Mass Properties Estimation Wiegand, B P In: 69th Annual Conference, Virginia Beach, Virginia, pp. 102, Society of Allied Weight Engineers, Inc., Virginia Beach, Virginia, 2010. Abstract | Buy/Download | BibTeX | Tags: 31. Weight Engineering - Surface Transportation 3469. Comparison of Power Distribution Systems for Land Vehicles Al-Kahwati, Jack In: 68th Annual Conference, Wichita, Kansas, pp. 10, Wichita, Kansas, 2009. Abstract | Buy/Download | BibTeX | Tags: 24. Weight Engineering - System Design, 31. Weight Engineering - Surface Transportation Kaiser, Scott In: 68th Annual Conference, Wichita, Kansas, pp. 16, Wichita, Kansas, 2009. Abstract | Buy/Download | BibTeX | Tags: 17. Weight Engineering - Procedures, 25. Weight Engineering - System Estimation, 31. Weight Engineering - Surface Transportation 3417. On the Influence of the Inertia Properties on the Vibrations of a Car Engine Muñoz, Luis; Scalmana, Claudio; Troccoli, Stefano In: 66th Annual Conference, Madrid, Spain, pp. 21, Society of Allied Weight Engineers Society of Allied Weight Engineers, Madrid, Spain, 2007, (Student Paper). Abstract | Buy/Download | BibTeX | Tags: 05. Inertia Calculations, 31. Weight Engineering - Surface Transportation Eberhard, Peter; Henninger, Christoph; Gobbi, Massimiliano; Mastinu, Giampiero; Muoz, Luis; Schiehlen, Werner In: 66th Annual Conference, Madrid, Spain, pp. 18, Society of Allied Weight Engineers Society of Allied Weight Engineers, Madrid, Spain, 2007. Abstract | Buy/Download | BibTeX | Tags: 05. Inertia Calculations, 31. Weight Engineering - Surface Transportation 3129. Ford's Weight Engineering Academy Carson, Frank; Cross, Tim; Mont, Harry; Schulz, Ken In: 60th Annual Conference, Arlington, Texas, May 19-23, pp. 15, Society of Allied Weight Engineers, Inc., Arlington, Texas, 2001. Abstract | Buy/Download | BibTeX | Tags: 31. Weight Engineering - Surface Transportation 2473. Lightweight Vehicle Processes of the 21st Century Carson, Frank In: 58th Annual Conference, San Jose, California, May 24-26, pp. 8, Society of Allied Weight Engineers, Inc., San Jose, California, 1999. Abstract | Buy/Download | BibTeX | Tags: 31. Weight Engineering - Surface Transportation Harrison, A R; Blanchard, P Dr. In: 58th Annual Conference, San Jose, California, May 24-26, pp. 12, Society of Allied Weight Engineers, Inc., San Jose, California, 1999. Abstract | Buy/Download | BibTeX | Tags: 31. Weight Engineering - Surface Transportation 2425. Magnesium Exposition and Symposium to Champion Automotive Applications Balzer, J In: 57th Annual Conference, Wichita, Kansas, May 18-20, pp. 15, Society of Allied Weight Engineers, Inc., Wichita, Kansas, 1998. Abstract | Buy/Download | BibTeX | Tags: 31. Weight Engineering - Surface Transportation2022
@inproceedings{3766,
title = {3766. Mass Properties and Automotive Braking},
author = {Brian Paul Wiegand},
url = {https://www.sawe.org/product/paper-3766},
year = {2022},
date = {2022-05-21},
urldate = {2022-05-21},
booktitle = {81st Annual Conference, Savannah, Georgia},
pages = {63},
publisher = {Society of Allied Weight Engineers, Inc.},
address = {Savannah, Georgia},
abstract = {In 1984, for the 43rd Annual International Conference of the SAWE, this author presented Paper Number 1634, “Mass Properties and Automotive Longitudinal Acceleration”. In that paper the effects upon automotive acceleration of varying the relevant mass property parameters were explored by use of a computer simulation. The computer simulation of automotive longitudinal acceleration allowed for the study of each individual parameter because a simulation allows for the decoupling of the parameters in a way that is not possible physically. The principal mass property parameters involved were the vehicle weight and rotating component inertias, collectively known as the “effective mass”, plus the longitudinal and vertical coordinates of the vehicle center of gravity.
However, just as it is important for a vehicle to be able to accelerate, it is perhaps even more important for a vehicle to be able to decelerate. The same mass properties that were relevant to the matter of automotive acceleration are also relevant to the matter of automotive deceleration, a.k.a. braking, although for the braking case that collective of vehicle translational inertia and rotational component inertias known as the “effective mass” requires somewhat different handling. As was the case with automotive acceleration, automotive braking will be explored by use of a computer simulation whereby the effect of variation of each of the mass property parameters can be studied independently. However, this task is considerably easier as the creation of a braking simulation is a minor effort compared to the creation of an acceleration simulation.
Rev B - 2023},
keywords = {31. Weight Engineering - Surface Transportation},
pubstate = {published},
tppubtype = {inproceedings}
}
However, just as it is important for a vehicle to be able to accelerate, it is perhaps even more important for a vehicle to be able to decelerate. The same mass properties that were relevant to the matter of automotive acceleration are also relevant to the matter of automotive deceleration, a.k.a. braking, although for the braking case that collective of vehicle translational inertia and rotational component inertias known as the “effective mass” requires somewhat different handling. As was the case with automotive acceleration, automotive braking will be explored by use of a computer simulation whereby the effect of variation of each of the mass property parameters can be studied independently. However, this task is considerably easier as the creation of a braking simulation is a minor effort compared to the creation of an acceleration simulation.
Rev B - 2023@inproceedings{3770,
title = {3770. Mass Management of a High Energy-Efficient Battery Electric Vehicle},
author = {Pietro Stabile and Federico Ballo and Giorgio Previati},
url = {https://www.sawe.org/product/paper-3770},
year = {2022},
date = {2022-05-21},
urldate = {2022-05-21},
booktitle = {81st Annual Conference, Savannah, Georgia},
pages = {15},
publisher = {Society of Allied Weight Engineers, Inc.},
address = {Savannah, Georgia},
abstract = {The paper presents a detailed analysis of the mass-induced power demand of an ultra-efficient battery electric vehicle. The vehicle belongs to a special class of lightweight quadricycles, designed for participating to efficiency competitions. The influence of reducing the mass of the entire vehicle and the mass of the wheels on the vehicle energy consumption is assessed. A sensitivity analysis is performed by exploiting a “tank-to- wheel” multi-physics model of the vehicle. The model includes the main vehicle subsystems and the principal sources of power dissipation are modelled. A three-step sensitivity analysis is carried out: firstly, the influence of the mass reduction on the energy saving is analysed for two different race tracks; then, two different driving behaviour on the same track are compared; finally, the potential energy saving due to actual lightweighting interventions performed on the vehicle is computed. In this phase, secondary mass reduction effects (battery downsizing) are included in the simulation. Results are expressed in terms of Energy Reduction Value (ERV), a parameter widely used in the literature to quantify the correlation between mass reduction and energy saving. The vehicle studied in this paper shows an ERV due to vehicle mass reduction ranging from 0.23 to 0.36 kWh/(100 km∙100 kg), while wheel lightweighting leads to an ERV ranging from 1.03 to 1.74 kWh/(100 km∙100 kg).},
keywords = {31. Weight Engineering - Surface Transportation, Student Papers},
pubstate = {published},
tppubtype = {inproceedings}
}
@inproceedings{3775,
title = {3775. Influence of the Inertia Parameters on a Dynamic Driving Simulator Performances},
author = {Giorgio Previati and Gianpiero Mastinu and Massimiliano Gobbi},
url = {https://www.sawe.org/product/paper-3775},
year = {2022},
date = {2022-05-21},
urldate = {2022-05-21},
booktitle = {81st Annual Conference, Savannah, Georgia},
pages = {14},
publisher = {Society of Allied Weight Engineers, Inc.},
address = {Savannah, Georgia},
abstract = {This paper deals with the analysis of the effects of inaccuracies in the knowledge of the inertia properties of a dynamic driving simulator on the performances of its motion control. Dynamic motion simulators aim to reproduce the motion of a vehicle with a high degree of fidelity. The simulators are moved by actuators up to relatively high frequencies. Special algorithms are used to scale the motion of the actual vehicle in order to comply with the travel allowed by the simulator while maintaining the more significant motion characteristics. Such algorithms are fine tuned to reproduce the feeling of each vehicle and suit the expectations of each user. Therefore, the motion controllers of the driving simulators must be able to accomplish the desired motion. Errors in the knowledge of the inertia parameters of the driving simulator can reduce the performances of the controller and increase the tracking error with respect to the desired trajectory.},
keywords = {05. Inertia Calculations, 31. Weight Engineering - Surface Transportation},
pubstate = {published},
tppubtype = {inproceedings}
}
2021
@inproceedings{3765,
title = {3765. Mass Properties and Automotive Directional Stability},
author = {B P Wiegand},
url = {https://www.sawe.org/product/paper-3765},
year = {2021},
date = {2021-11-01},
urldate = {2021-11-01},
booktitle = {2021 SAWE Tech Fair},
pages = {61},
publisher = {Society of Allied Weight Engineers, Inc.},
address = {Virtual Conference},
abstract = {The quantification of automotive directional stability may be expressed through various stability metrics, but perhaps the most basic of these automotive stability metrics is the “Understeer Gradient” (Kus). The Understeer Gradient (in degrees or radians per unit gravity) appears extremely uncomplicated when viewed in its most common formulation. Kus =[ Wf / gCsf - Wr / gCsr ]
This metric appears to depend only on the front and rear axle weight loads (Wf, Wr), and on the front and rear axle cornering stiffnesses (Csf, Csr). However, those last quantities vary with lateral acceleration, and the nature of that variation is dependent upon many other parameters of which some of the most basic are: Total Weight, Sprung Weight, Unsprung Weight, Forward Unsprung Weight, Rear Unsprung Weight, Total Weight LCG, Sprung Weight LCG, Total Weight VCG, Sprung Weight VCG, Track, Front Track, Rear Track, Roll Stiffness, Front Roll Stiffness, Rear Roll Stiffness, Roll Axis Height, Front Roll Center Height, and Rear Roll Center Height. Note that exactly half of these automotive directional stability parameters as listed herein are mass properties.
The purpose of this paper is to explore, through a skidpad simulation, the relative sensitivity of automotive directional stability (as quantified through the Understeer Gradient) to variation in each of the noted vehicle parameters, with special emphasis on the mass property parameters.
The simulation is constructed in a spreadsheet format from the relevant basic automotive dynamics equations; the normal and lateral loads on the tires are determined as the lateral acceleration is increased incrementally by a small amount (thereby maintaining a “quasi-static” or “steady-state” condition). The normal loads are used for the calculation of the lateral traction force potentials at each tire, with the required (centripetal) lateral traction forces apportioned accordingly. From those required (actual) lateral tire forces the corresponding tire cornering stiffnesses are determined; this determination is based upon a tire model developed through a regression analysis of tire test data.
This construction of a fairly comprehensive lateral acceleration simulation from basic automotive dynamic relationships, instead of depending upon commercial automotive software such as “CarSim” (vehicle model) and Pacjeka “Magic Formula” (tire model), constitutes a unique aspect of this paper; this return to basics hopefully provides a clearer view and understanding of the results than would be the case otherwise. Even more unique is this paper’s emphasis on, and exploration of, the role specific mass property parameters play in determining automotive directional stability.},
keywords = {31. Weight Engineering - Surface Transportation},
pubstate = {published},
tppubtype = {inproceedings}
}
This metric appears to depend only on the front and rear axle weight loads (Wf, Wr), and on the front and rear axle cornering stiffnesses (Csf, Csr). However, those last quantities vary with lateral acceleration, and the nature of that variation is dependent upon many other parameters of which some of the most basic are: Total Weight, Sprung Weight, Unsprung Weight, Forward Unsprung Weight, Rear Unsprung Weight, Total Weight LCG, Sprung Weight LCG, Total Weight VCG, Sprung Weight VCG, Track, Front Track, Rear Track, Roll Stiffness, Front Roll Stiffness, Rear Roll Stiffness, Roll Axis Height, Front Roll Center Height, and Rear Roll Center Height. Note that exactly half of these automotive directional stability parameters as listed herein are mass properties.
The purpose of this paper is to explore, through a skidpad simulation, the relative sensitivity of automotive directional stability (as quantified through the Understeer Gradient) to variation in each of the noted vehicle parameters, with special emphasis on the mass property parameters.
The simulation is constructed in a spreadsheet format from the relevant basic automotive dynamics equations; the normal and lateral loads on the tires are determined as the lateral acceleration is increased incrementally by a small amount (thereby maintaining a “quasi-static” or “steady-state” condition). The normal loads are used for the calculation of the lateral traction force potentials at each tire, with the required (centripetal) lateral traction forces apportioned accordingly. From those required (actual) lateral tire forces the corresponding tire cornering stiffnesses are determined; this determination is based upon a tire model developed through a regression analysis of tire test data.
This construction of a fairly comprehensive lateral acceleration simulation from basic automotive dynamic relationships, instead of depending upon commercial automotive software such as “CarSim” (vehicle model) and Pacjeka “Magic Formula” (tire model), constitutes a unique aspect of this paper; this return to basics hopefully provides a clearer view and understanding of the results than would be the case otherwise. Even more unique is this paper’s emphasis on, and exploration of, the role specific mass property parameters play in determining automotive directional stability.2019
@inproceedings{3724,
title = {3724. Methods and Processes for Robust Mass Properties Management in the Automotive Industry with a Main Focus on Mass Uncertainties},
author = {Marcus Stegmiller and Albert Albers},
url = {https://www.sawe.org/product/paper-3724},
year = {2019},
date = {2019-05-01},
booktitle = {78th Annual Conference, Norfolk, VA},
pages = {18},
publisher = {Society of Allied Weight Engineers, Inc.},
address = {Norfolk, Virginia},
abstract = {The mass of an automobile represents a crucial parameter for development because it influences the design of the automobile as well as decisive purchasing characteristics such as driving dynamics, fuel consumption and range. The dimensioning effect of the automobile mass has so far led to the definition of challenging and fixed mass targets. Since the automotive industry is characterized by high cost pressure, product complexity (e.g. due to modular and platform strategies, supplier chains and manufacturing constraints), increasing product range and volatile boundary conditions (e.g. due to regulation) automobile masses are permanently changing during development. This can no longer be robustly controlled by fixed mass targets. In practice, this often results in late missed mass targets, which lead to heavy and costly countermeasures.Therefore, the specific requirements of the automotive industry demand a highly developed mass properties management (MPM). This paper presents such a MPM through a practice oriented and flexible methodology. The methodology is based on existing MPM approaches (including SAWE practices) and adapted to the automotive industry. It consists of a mass target framework enriched by a mass prognosis tool, an economic evaluation method for automobile mass scenarios, methods for identifying lightweight design measures and a phase-adequate determination of mass uncertainties. The methods are strongly based on the approach of PGE - Product Generation Engineering, which says that products are developed in generations and therefore information can be reused.This paper deals in particular with the determination of mass uncertainties. Five types of mass uncertainties are identified, compared to the SAWE mass change codes and quantified on the basis of real automobile projects. Since the uncertainties provide transparency on mass potentials and risks, a suitable approach corridor for mass target guidance is derived from them. Furthermore, approaches are presented how mass uncertainties can be interpreted as quality indicators of current MPM processes and how the entire method can be automated. Finally, the mentioned methods above are combined to form a process to derive and manage robust mass targets, buffers and design masses for automobile development.},
keywords = {31. Weight Engineering - Surface Transportation},
pubstate = {published},
tppubtype = {inproceedings}
}
@inproceedings{3725,
title = {3725. HERMES: Hazard Examination and Reconnaissance Messenger for Extended Surveillance},
author = {Alexander Sandoval and Alexis Sotomayor and Brandon Santori and Brindan Adhikari and Colin Chen and Junzhe He and Katelyn Griego and Marcos Mejia and Michely Tenardi and Quinter Nyland},
url = {https://www.sawe.org/product/paper-3725},
year = {2019},
date = {2019-05-01},
booktitle = {78th Annual Conference, Norfolk, VA},
pages = {11},
publisher = {Society of Allied Weight Engineers, Inc.},
address = {Norfolk, Virginia},
abstract = {The University of Colorado at Boulder Aerospace Engineering Senior Projects Team HERMES (Hazard Examination and Reconnaissance Messenger for Extended Surveillance) is currently designing, building, and testing a child scout rover (CSR). This is the fourth installment in the Jet Propulsion Laboratory's (JPL) Fire Tracker System. The Fire Tracker System is designed to operate in forest fire-prone areas for early fire identification. HERMES aims to improve the Fire Tracker System by navigating through a forest like environment to a location of interest (LOI) while determining a viable path for the Fire Tracker System's previous installment, a large less maneuverable mother rover. To do this, the CSR must traverse over obstacles up to 2.4 inches in height, vertical discontinuities (9 inches wide by 2.4 inches deep), over leaves, dirt, grass, and up or down 20 degree inclined slopes in both open and wooded area. Additionally, the CSR must drive forward and in reverse, as well as perform 360 degree turns in place. To complete these mission objectives, the CSR uses a sensor suite for obstacle and discontinuity detection, a two-motor configuration with a drivetrain and gearbox powering 6 wheels for traversing obstacles, and a moving linear mass stage that shifts the CSR's center of mass to enable traversing over discontinuities. While on a mission, the CSR will have the capability to detect any discontinuities using two downward angled, single beam LiDAR sensors. If a discontinuity is detected, the CSR will stop and notify the user at the ground station. The user at the ground station then commands the CSR into a semi-autonomous discontinuity traversal mode, where the CSR utilizes two ultrasonic sensors mounted on the bottom of the CSR to determine whether it is over a discontinuity or flat ground. These sensors signal the software to move the linear mass stage to shift the center of mass depending on the CSR's position over the discontinuity. The unique challenge of crossing discontinuities, and the solution, is discussed in this paper.},
keywords = {03. Center Of Gravity, 31. Weight Engineering - Surface Transportation, 33. Unmanned Vehicles},
pubstate = {published},
tppubtype = {inproceedings}
}
2015
@inproceedings{3602,
title = {3602. Mass Properties and Advanced Automotive Design},
author = {B P Wiegand},
url = {https://www.sawe.org/product/paper-3602},
year = {2015},
date = {2015-05-01},
urldate = {2015-05-01},
booktitle = {74th Annual Conference, Alexandria, Virginia},
pages = {325},
publisher = {Society of Allied Weight Engineers, Inc.},
address = {Alexandria, Virginia},
abstract = {The history of the automobile constitutes a long list of remarkable vehicles, each of which is usually associated with some equally remarkable individual who provided the impetus behind the vehicle's creation. Henry Royce, Hans Ledwinka, Ferdinand Porsche, Enzo Ferrari, and Colin Chapman constitute just a small sample of those who put the forceful stamp of their personal design philosophies upon the automobile. The design philosophies of such men reflected a focused viewpoint, such as an emphasis on quality and refinement (Royce), efficient structure and aerodynamics (Ledwinka, Porsche), exquisite engines of high specific power (Ferrari), or performance from extreme light weight (Chapman). The emphasis on a particular aspect of vehicle design hardly means that other design aspects were ignored, just that the emphasis was on some particular aspect(s) around which all else evolved, whether by preference or necessity. Colin Chapman's relentless concern with mass properties, and in particular with light weight, was born of necessity, but would become a personal obsession. As a small start-up company competing against long established automotive concerns such as Ferrari, Chapman's Lotus Engineering Company1 did not have the capability to gain advantage through advanced engine design, or even the design of most of the other major mechanical systems. Most Lotus components were commercially sourced, and so the only way a decisive advantage could be obtained was through an uncompromising emphasis on gaining performance 'edges' from the remaining design aspects of structure, body, and suspension. Because the automotive performance aspects of acceleration, braking, and handling are so dependent on various vehicle mass properties the optimization of those mass properties became the 'Holy Grail' of Lotus design as directed by Colin Chapman. In fact, with regard to light weight Chapman would come to demonstrate what could be termed a mania. Although the automotive design philosophy of Colin Chapman was the closest ever to being one that could be termed 'designing from the viewpoint of the mass properties engineer', the key word is 'closest'. There is much more to mass properties engineering than simply minimizing weight, which Chapman often did with a disregard for reliability and even safety. It was despite an unenviable record of DNF's and driver casualties that Lotus still obtained an outstanding record in automotive competition, and Formula One in particular. This raises the fascinating question of what would result from applying an automotive design philosophy based on a balanced professional mass properties viewpoint. The intent of this paper is to show that a vehicle designed in true accordance with the balanced viewpoint of a professional mass properties engineer may not only demonstrate superior acceleration, braking, and handling, but superior ride, stability, fuel economy, and safety as well. If a design begins with the first principles of how mass properties affect automotive performance in all its aspects2, and is optimized accordingly in an integrated manner, then the resulting advanced automotive design may truly 'go where none have gone before'.
Rev G - 2023},
note = {Revision C (2016)},
keywords = {31. Weight Engineering - Surface Transportation},
pubstate = {published},
tppubtype = {inproceedings}
}
Rev G - 2023@inproceedings{3634,
title = {3634. Mass Properties and Automotive Crash Survival},
author = {B P Wiegand},
url = {https://www.sawe.org/product/paper-3634},
year = {2015},
date = {2015-05-01},
booktitle = {74th Annual Conference, Alexandria, Virginia},
pages = {145},
publisher = {Society of Allied Weight Engineers, Inc.},
address = {Alexandria, Virginia},
abstract = {Problems in dynamics may be solved by any one or more of three basic methods: force and acceleration, work and kinetic energy, impulse and momentum; these are just different ways of looking at a common underlying reality1. The method(s) used to investigate a particular dynamics problem depends upon the specific nature of the problem. Problems involving that most severe form of automotive longitudinal deceleration, crashing, are no exception. Even at the most elementary level, as represented by the previous equations, the unifying role of mass properties is evident. Notable in the basic formulae of all three methods for the solution of problems in dynamics is the common parameter m (mass). However, this represents just the tip of the iceberg ; at the detailed level representative of actual engineering problems the full role played by mass properties is often revealed to be far more complicated than that indicated by such simple basic equations. For instance, an automobile traveling at a particular velocity will possess a certain amount of kinetic energy which must be dissipated for the vehicle to come to a stop. The dissipation can be controlled and orderly as in the case of braking a car to a stop at an intersection, or it can be somewhat more violent as in the case of a collision with a concrete abutment. In both cases the outcome is directly dependent upon the magnitude of the kinetic energy involved. Initially the mass properties involvement seems to be very simple: the kinetic energy of any body of mass m moving at a velocity V is expressible as; to come to a stop that energy must be dissipated through the work done by a deceleration force F times the distance d traveled during the deceleration. However, the kinetic energy possessed by an automobile is much more than would be indicated by a simple determination of its mass m from its weight. Many components of an automobile possess not only translational kinetic energy, but rotational as well. Thus the simple mass m is not the appropriate value needed for kinetic energy determination; there is a greater value me , termed the effective mass . The calculation of me involves the rotational inertia of such components as the wheels, tires, brakes, shafts, bearings, etc. Thus not only the mass of the automobile as a whole, but that of various components, come into play when calculating the amount of kinetic energy which, in turn, determines the magnitude of the deceleration forces required to affect a complete stop in a certain distance. When the deceleration is a matter of braking, certain other vehicle mass properties come into play: the vehicle longitudinal, lateral, and vertical CG. When the deceleration is a matter of crashing, then the vehicle mass density and mass density distribution also have significance. The purpose of this paper is to make explicit the exact role that all the mass properties play in determining the automotive deceleration performance during a crash. This has a direct bearing on the survivability of a crash, which can be enhanced through thoughtful mass properties engineering.},
keywords = {31. Weight Engineering - Surface Transportation},
pubstate = {published},
tppubtype = {inproceedings}
}
@inproceedings{3640,
title = {3640. Colin Chapman and Automotive Mass Properties},
author = {B P Wiegand},
url = {https://www.sawe.org/product/paper-3640},
year = {2015},
date = {2015-05-01},
urldate = {2015-05-01},
booktitle = {74th Annual Conference, Alexandria, Virginia},
pages = {75},
publisher = {Society of Allied Weight Engineers, Inc.},
address = {Alexandria, Virginia},
abstract = {As a small start-up company competing against long established automotive concerns such as Ferrari, Colin Chapman's Lotus Engineering Company1 did not have the capability to gain advantage through advanced engine design, or even via the design of most of the other major mechanical systems. Most such components were commercially sourced, and so the only way a decisive advantage could be obtained was through an uncompromising emphasis on gaining performance 'edges' from the remaining design elements of structure, body, and suspension. Because the automotive performance aspects of acceleration, braking, and handling are so dependent on various vehicle mass properties the optimization of those mass properties became the 'Holy Grail' of Lotus design as directed by Colin Chapman.
Rev A - 2023},
keywords = {31. Weight Engineering - Surface Transportation},
pubstate = {published},
tppubtype = {inproceedings}
}
Rev A - 20232011
@inproceedings{3521,
title = {3521. Mass Properties and Automotive Vertical Acceleration},
author = {B P Wiegand},
url = {https://www.sawe.org/product/paper-3521},
year = {2011},
date = {2011-05-01},
urldate = {2011-05-01},
booktitle = {70th Annual Conference, Houstion, Texas},
pages = {112},
publisher = {Society of Allied Weight Engineers, Inc.},
address = {Houston, Texas},
abstract = {The mass properties of a vehicle affect its' motion in all directions, translational and rotational. Previously this author has dealt with how mass properties affect automotive longitudinal acceleration1 and automotive lateral acceleration2. Now a consideration is in order of how mass properties affect automotive vertical acceleration. Of course, lateral or longitudinal inputs can lead to vertical responses, etc., every aspect of a vehicle's dynamics is interconnected with every other aspect, but it is convenient to divide up automotive dynamics as if the subject were purely a matter of independent accelerations in the longitudinal, lateral, and vertical directions. Initially, this paper will investigate the significance of mass properties with regard to automotive ride (transmission of road shock & vibration) and road-holding (maintaining contact at the tire/road interface) through the use of simple, undamped, 1 DOF models. Later, the full story of how mass properties influence the bounce and pitch motions of the sprung mass will necessitate recourse to more complex 2 DOF models. The mass properties of greatest relevance to this investigation will prove to be the 'sprung' mass, the 'unsprung' masses, the 'sprung' mass distribution (longitudinal, lateral, and vertical c.g. location), the rotational inertias of the rotating portions of the 'unsprung' masses, and the 'sprung' mass longitudinal and lateral mass moments of inertia. The basic intent of this paper is to counter the commonly held simplistic concept of the role mass properties play in determining ride and road-contact. For those that have never undertaken any study of the matter, the general presumption seems to be that all that is required to achieve optimum performance is to minimize the weight and to obtain a balanced mass distribution. The reality is that there are many aspects to automotive performance, and what constitutes an optimum mass properties condition is generally a very complex matter which often necessitates difficult compromises. Tailoring some mass property parameters so as to achieve a desirable level of behavior with regard to one performance criteria will often adversely affect other performance criteria. Although this paper is restricted to mass properties issues related to performance resulting from motion in the vertical direction, occasional reference will be made to those mass properties requirements necessitated by performance considerations associated with the longitudinal (acceleration, braking) and lateral (maneuver, roll-over, and directional stability) directions, as revealed in the previous investigations noted earlier. To do otherwise would be to work in a vacuum; the nature of reality tends to be such that all things are ultimately interrelated. To the fullest extent possible, the greater intent herein is to approach reality through the totality of the papers and articles written by this author on the subject of mass properties and automotive performance.
Rev B - 2023},
note = {Mike Hackney Best Paper Award},
keywords = {31. Weight Engineering - Surface Transportation, Mike Hackney Best Paper Award},
pubstate = {published},
tppubtype = {inproceedings}
}
Rev B - 2023@inproceedings{3528,
title = {3528. Mass Properties and Automotive Lateral Accelerations},
author = {B P Wiegand},
url = {https://www.sawe.org/product/paper-3528},
year = {2011},
date = {2011-05-01},
urldate = {2011-05-01},
booktitle = {70th Annual Conference, Houstion, Texas},
pages = {92},
publisher = {Society of Allied Weight Engineers, Inc.},
address = {Houston, Texas},
abstract = {There are a number of automotive performance aspects which are associated with accelerations in the lateral direction: maneuver (transient and steady state), roll-over, and directional stability. For each of these automotive performance aspects certain mass property parameters play significant roles; it is the intent of this paper to make explicit exactly how those mass property parameters affect each of those automotive performance aspects.
With regard to maneuver, the maximum lateral acceleration which can be attained in steady-state turning is an important index of performance and safety. The obtaining of high maximum lateral acceleration levels has inherent vehicle weight and center of gravity (longitudinal, lateral, and vertical) implications. However, before attaining a steady-state condition, a turning maneuver must first go through a transient phase. When the transient phase is included in the full maneuver picture, the previous list of significant vehicle mass properties parameters acquires two more members: the mass moments of inertia about the roll and yaw axes.
For modern passenger vehicles, the lateral acceleration point at which roll-over can occur is generally at a value significantly greater than the maximum lateral acceleration level. That is, a modern car will tend to slide out of control long before there is a possibility of overturn. Accidents involving rollover generally occur because the vehicle was 'flipped' or 'tripped' by obstacles in the roadway, not because the vehicle traction was great enough to reach the critical lateral acceleration level. However, the level at which rollover could occur is still an important index of safety, and the most significant mass property for the determination of that level is the vertical center of gravity.
Lastly, there is the matter of directional stability, which has to do with the 'drift angle' relationship of the vehicle tires front-to-rear, and the lateral force balance front-to-rear due to those drift angles. The lateral force/drift angle relationship is dependent upon normal load, so the most significant mass property with regard to directional stability is the vehicle static weight distribution.
However, the static normal loads are dynamically modified in response to directional 'disturbance' forces. Such disturbances generate initial inertial lateral reactions at the vehicle c.g.; the consequent roll moment not only causes lateral changes in the normal load distribution, but also longitudinal changes due to suspension roll resistance. Such changes readjust the lateral force/drift angle relationship front to rear, and thereby generate a secondary directional reaction. If the secondary reaction is such as to augment the effect of the original disturbance, then the vehicle is termed unstable or 'oversteering'; if the reaction is such as to diminish the effect of the original disturbance, then the vehicle is termed stable or 'understeering'. Therefore, for directional stability, the primary parameters are the vehicle mass properties of weight, and weight distribution (longitudinal, lateral, and vertical c.g.).
Rev G - 2023},
keywords = {31. Weight Engineering - Surface Transportation},
pubstate = {published},
tppubtype = {inproceedings}
}
With regard to maneuver, the maximum lateral acceleration which can be attained in steady-state turning is an important index of performance and safety. The obtaining of high maximum lateral acceleration levels has inherent vehicle weight and center of gravity (longitudinal, lateral, and vertical) implications. However, before attaining a steady-state condition, a turning maneuver must first go through a transient phase. When the transient phase is included in the full maneuver picture, the previous list of significant vehicle mass properties parameters acquires two more members: the mass moments of inertia about the roll and yaw axes.
For modern passenger vehicles, the lateral acceleration point at which roll-over can occur is generally at a value significantly greater than the maximum lateral acceleration level. That is, a modern car will tend to slide out of control long before there is a possibility of overturn. Accidents involving rollover generally occur because the vehicle was 'flipped' or 'tripped' by obstacles in the roadway, not because the vehicle traction was great enough to reach the critical lateral acceleration level. However, the level at which rollover could occur is still an important index of safety, and the most significant mass property for the determination of that level is the vertical center of gravity.
Lastly, there is the matter of directional stability, which has to do with the 'drift angle' relationship of the vehicle tires front-to-rear, and the lateral force balance front-to-rear due to those drift angles. The lateral force/drift angle relationship is dependent upon normal load, so the most significant mass property with regard to directional stability is the vehicle static weight distribution.
However, the static normal loads are dynamically modified in response to directional 'disturbance' forces. Such disturbances generate initial inertial lateral reactions at the vehicle c.g.; the consequent roll moment not only causes lateral changes in the normal load distribution, but also longitudinal changes due to suspension roll resistance. Such changes readjust the lateral force/drift angle relationship front to rear, and thereby generate a secondary directional reaction. If the secondary reaction is such as to augment the effect of the original disturbance, then the vehicle is termed unstable or 'oversteering'; if the reaction is such as to diminish the effect of the original disturbance, then the vehicle is termed stable or 'understeering'. Therefore, for directional stability, the primary parameters are the vehicle mass properties of weight, and weight distribution (longitudinal, lateral, and vertical c.g.).
Rev G - 20232010
@inproceedings{3490,
title = {3490. Automotive Mass Properties Estimation},
author = {B P Wiegand},
url = {https://www.sawe.org/product/paper-3490},
year = {2010},
date = {2010-05-01},
urldate = {2010-05-01},
booktitle = {69th Annual Conference, Virginia Beach, Virginia},
pages = {102},
publisher = {Society of Allied Weight Engineers, Inc.},
address = {Virginia Beach, Virginia},
abstract = {Mass properties have a profound effect on automotive fuel economy, emissions, safety, ride, acceleration, braking, and maneuver. Because of this fact, it is important to have a reliable and comprehensive methodology for the estimation of key mass property parameters in the conceptual design stage. Also, such a methodology would be important for researchers investigating aspects of automotive dynamics, for programmers creating realistic automotive simulations, and for investigators studying the dynamics of automotive crash scenarios.
There is a scarcity of published information of sufficient accuracy and/or completeness so as to constitute a viable methodology. Published automotive mass property estimation methods seem to be available only in a non-comprehensive fashion through a variety of scattered sources. It is the intent of this paper to systematize the information drawn from published sources and, with the employment of techniques based on those used in the aerospace industry, to augment and improve upon the published information so as to develop a basis for a comprehensive automotive mass properties estimation methodology.
Rev A - 2023
Note the use of the word 'basis'; it is not to be imagined that this paper will represent the 'last word' in automotive mass properties estimation. What is presented herein is intended to provide a possible overall framework for, and an initial 'first cut' at, the development of a comprehensive methodology. Automotive design practitioners working within the established industry may have a far more potent estimation methodology available to them, but in the form of proprietary techniques that they are not at liberty to divulge. Yet even such automotive industry insiders may find an independently derived methodology interesting, and perhaps even useful for comparison with in-house procedures. However, it is the independent designer or researcher that is most likely to find this paper to be of great value, and it is the purpose of this paper to aid such independent efforts through promoting the development of a publicly accessible methodology.
To that end this paper presents the development of a preliminary 'top-down' methodology which requires as input only those most basic and common overall parameters as would be available in the earliest of design stages or, for existing designs, from the commonly available literature. This includes such parameters as vehicle dimensions, applicable general legal specification or regulation, general vehicle configuration and category, type of suspension, and level of technology (which is generally time dependent). The desired output consists of the curb weight/c.g. coordinates/inertias, the unsprung weight/c.g. coordinates/inertias, the sprung weight/c.g. coordinates/inertias, and the sprung weight roll moment of inertia (i.e., a rotational inertia about an essentially longitudinal axis, the location of which is determined by the suspension geometry).},
keywords = {31. Weight Engineering - Surface Transportation},
pubstate = {published},
tppubtype = {inproceedings}
}
There is a scarcity of published information of sufficient accuracy and/or completeness so as to constitute a viable methodology. Published automotive mass property estimation methods seem to be available only in a non-comprehensive fashion through a variety of scattered sources. It is the intent of this paper to systematize the information drawn from published sources and, with the employment of techniques based on those used in the aerospace industry, to augment and improve upon the published information so as to develop a basis for a comprehensive automotive mass properties estimation methodology.
Rev A - 2023
Note the use of the word 'basis'; it is not to be imagined that this paper will represent the 'last word' in automotive mass properties estimation. What is presented herein is intended to provide a possible overall framework for, and an initial 'first cut' at, the development of a comprehensive methodology. Automotive design practitioners working within the established industry may have a far more potent estimation methodology available to them, but in the form of proprietary techniques that they are not at liberty to divulge. Yet even such automotive industry insiders may find an independently derived methodology interesting, and perhaps even useful for comparison with in-house procedures. However, it is the independent designer or researcher that is most likely to find this paper to be of great value, and it is the purpose of this paper to aid such independent efforts through promoting the development of a publicly accessible methodology.
To that end this paper presents the development of a preliminary 'top-down' methodology which requires as input only those most basic and common overall parameters as would be available in the earliest of design stages or, for existing designs, from the commonly available literature. This includes such parameters as vehicle dimensions, applicable general legal specification or regulation, general vehicle configuration and category, type of suspension, and level of technology (which is generally time dependent). The desired output consists of the curb weight/c.g. coordinates/inertias, the unsprung weight/c.g. coordinates/inertias, the sprung weight/c.g. coordinates/inertias, and the sprung weight roll moment of inertia (i.e., a rotational inertia about an essentially longitudinal axis, the location of which is determined by the suspension geometry).2009
@inproceedings{3469,
title = {3469. Comparison of Power Distribution Systems for Land Vehicles},
author = {Jack Al-Kahwati},
url = {https://www.sawe.org/product/paper-3469},
year = {2009},
date = {2009-05-01},
booktitle = {68th Annual Conference, Wichita, Kansas},
pages = {10},
address = {Wichita, Kansas},
abstract = {For combat vehicles, power distribution systems face a
multitude of challenges caused by shrinking space availability,
demanding thermal environments, reliability constraints, and the
need to reduce system weight. This paper investigates the trade
between two different design methodologies: cable conductors and
bus bar concepts. The design approach and thermal assessments are
investigated to achieve a weight optimized solution for high
powered applications.
In this study, a 2D Computation Fluid Dynamic (CFD) model is
created to simulate the natural convection and conduction cooling
of the cable conductor and a laminated bus structure.},
keywords = {24. Weight Engineering - System Design, 31. Weight Engineering - Surface Transportation},
pubstate = {published},
tppubtype = {inproceedings}
}
multitude of challenges caused by shrinking space availability,
demanding thermal environments, reliability constraints, and the
need to reduce system weight. This paper investigates the trade
between two different design methodologies: cable conductors and
bus bar concepts. The design approach and thermal assessments are
investigated to achieve a weight optimized solution for high
powered applications.
In this study, a 2D Computation Fluid Dynamic (CFD) model is
created to simulate the natural convection and conduction cooling
of the cable conductor and a laminated bus structure.@inproceedings{3479,
title = {3479. Managing and Controlling Weight and Center of Gravity for Combat Ground Vehicle Development Programs},
author = {Scott Kaiser},
url = {https://www.sawe.org/product/paper-3479},
year = {2009},
date = {2009-05-01},
booktitle = {68th Annual Conference, Wichita, Kansas},
pages = {16},
address = {Wichita, Kansas},
abstract = {BAE Systems Inc. is the U.S, subsidiary ofBAE Systems pIc, an intcmational company engaged in the development, delivery and support of advanced defense and aerospace systems in the air, on land, at sea and in space. US Combat Systems, one of BAE Systems Inc.'s Land & Armaments lines of business is a leader in designing, rapidly prototyping and manufacturing protected fighting vehicle plattbrms and survivability solutions that support and protect the current and future forces. Improving and increasing military transformation capabilities, that is increasing the speed with which the military forces deploy and engage by reducing the logistics tail is directly related to the successes of managing and controlling the development and fielded weight of combat ground vehicles. This paper discusses methods of controlling and managing weight of complex design combat vehicle solutions tbr the customer that has various design constraints such as high level of component commonality, low cost, high reliability, speed to market, and increased performance capabilities over the current force systems. The mass properties control and management methods presented in this paper focus on developing an accurate estimate, reconciling this estimate with the customer's requirements, advocating a program mass properties and control plan, establishing and enforcing weight allocations/targets, monitoring and mitigating development weight, organizing and presenting data. The final conclusions of this paper will include lessons learned based on implementation ofthese methods.},
keywords = {17. Weight Engineering - Procedures, 25. Weight Engineering - System Estimation, 31. Weight Engineering - Surface Transportation},
pubstate = {published},
tppubtype = {inproceedings}
}
2007
@inproceedings{3417,
title = {3417. On the Influence of the Inertia Properties on the Vibrations of a Car Engine},
author = {Luis Muñoz and Claudio Scalmana and Stefano Troccoli},
url = {https://www.sawe.org/product/paper-3417},
year = {2007},
date = {2007-05-01},
booktitle = {66th Annual Conference, Madrid, Spain},
pages = {21},
publisher = {Society of Allied Weight Engineers},
address = {Madrid, Spain},
organization = {Society of Allied Weight Engineers},
abstract = {The paper presents a study about the influence of the inertia properties on the dynamic behavior of a vehicle powertrain (in our specific case we considered a system composed of the engine and the gearbox of a front wheel drive car). The dynamic performance of such a powertrain was studied both theoretically and experimentally by means of proper sensitivity analyses. The information provided by the measurements was used for the validation of two mathematical models of the powertrain. Both the experimental and the theoretical simulations confirmed that the powertrain vibrations in the range 10 ? 15 Hz are particularly sensitive to slight variations of the inertia properties. According to the common knowledge referring to the dynamic behavior of cars, at relatively high speed, the vibrations of the powertrain in the range 10-15 Hz can seriously decrease comfort and even affect safety. The conclusions derived from the analysis of the examined particular case can be extended easily to a broad class of road vehicles.},
note = {Student Paper},
keywords = {05. Inertia Calculations, 31. Weight Engineering - Surface Transportation},
pubstate = {published},
tppubtype = {inproceedings}
}
@inproceedings{3435,
title = {3435. Providing The Inertia Properties of Vehicles and Their Subsystems for Virtual Reality and Mechatronics Applications},
author = {Peter Eberhard and Christoph Henninger and Massimiliano Gobbi and Giampiero Mastinu and Luis Muoz and Werner Schiehlen},
url = {https://www.sawe.org/product/paper-3435},
year = {2007},
date = {2007-05-01},
booktitle = {66th Annual Conference, Madrid, Spain},
pages = {18},
publisher = {Society of Allied Weight Engineers},
address = {Madrid, Spain},
organization = {Society of Allied Weight Engineers},
abstract = {There are many methods available to measure (and/or compute) the inertia properties of vehicles and their subsystems. But no standards are presently available defining the appropriate measurement tolerances that are needed for engineering activities. This paper addresses this problem by means of both experimental and theoretical investigations. Two different validated mathematical models were used, one for the entire vehicle and the other for the powertrain. A sensitivity analysis over a selected set of performance indices was performed by using the two models. After defining reasonable tolerances on the performance indices defining the dynamic behavior of the vehicle and its powertrain, the proper tolerances on the inertia properties were obtained. Relatively small variations of the inertia properties may produce significant variation in the considered dynamic performances of a vehicle and its subsystem.},
keywords = {05. Inertia Calculations, 31. Weight Engineering - Surface Transportation},
pubstate = {published},
tppubtype = {inproceedings}
}
2001
@inproceedings{3129,
title = {3129. Ford's Weight Engineering Academy},
author = {Frank Carson and Tim Cross and Harry Mont and Ken Schulz},
url = {https://www.sawe.org/product/paper-3129},
year = {2001},
date = {2001-05-01},
booktitle = {60th Annual Conference, Arlington, Texas, May 19-23},
pages = {15},
publisher = {Society of Allied Weight Engineers, Inc.},
address = {Arlington, Texas},
abstract = {Automotive weight engineers need to blend technical, business, and people skills together to best deploy the vehicle weight attribute. Ford recently developed a training approach called the 'Weight Engineering Academy' to enhance these critical work force skills.},
keywords = {31. Weight Engineering - Surface Transportation},
pubstate = {published},
tppubtype = {inproceedings}
}
1999
@inproceedings{2473,
title = {2473. Lightweight Vehicle Processes of the 21st Century},
author = {Frank Carson},
url = {https://www.sawe.org/product/paper-2473},
year = {1999},
date = {1999-05-01},
booktitle = {58th Annual Conference, San Jose, California, May 24-26},
pages = {8},
publisher = {Society of Allied Weight Engineers, Inc.},
address = {San Jose, California},
abstract = {Automotive Weight Engineering processes continue to evolve to meet the emerging vehicle requirements for the 21st Century. Recent realignment of Weight Engineering into the Attribute Engineering Office improves the delivery of the Weight Attribute to Vehicle Programs. Throughout the history of the automobile, engineers have always calculated loading conditions under expected customer usage to design suspension components. Understanding the conditions of the roads and customer needs contributed to the tremendous success of the first mass-produced, car, Ford?s Model T. In 1923, Henry Ford described his philosophy about vehicle weight. ?Saving even a few pounds of a vehicle?s weight...could mean that they would also go faster and consume less fuel. Reducing weight involves reducing materials which in turn, means reducing cost as well.? A philosophy that we still embrace as we enter the second automotive century. Trucks also were a part of the early automotive industry . About 444 truck makers attempted to enter the growing automotive business in the first decade of the 20th Century. Although only a few survived, trucks added the concept of payload ? a significant element of chassis systems design. Trucks need to meet customer usage requirements in the unloaded as well as the fully loaded vehicle condition. Weight Engineering as a distinct activity at Ford sprang from the need to meet the challenging U.S. emission and fuel economy standards. The Clean Air Act of 1970 regulated tail pipe emissions and the Energy Policy and Conservation Act of 1980 mandated increases in fuel economy. The latter was enacted as a response to the oil crisis of the 1970s ? gasoline spiked at $1.30/gallon (1979 dollars) or about $3/gallon in 1999 dollars.},
keywords = {31. Weight Engineering - Surface Transportation},
pubstate = {published},
tppubtype = {inproceedings}
}
@inproceedings{2474,
title = {2474. A Low Investment Cost Route for Lightweight Tooling and Lightweight Composite Roof for the Ford Transit Van},
author = {A R Harrison and P Dr. Blanchard},
url = {https://www.sawe.org/product/paper-2474},
year = {1999},
date = {1999-05-01},
booktitle = {58th Annual Conference, San Jose, California, May 24-26},
pages = {12},
publisher = {Society of Allied Weight Engineers, Inc.},
address = {San Jose, California},
abstract = {This paper outlines the use of low cost and lightweight shell tooling and (RTM) Resin Transfer Molding to manufacture a lightweight composite high roof for the Ford Transit. The full use of CAD/CAM/CAE was utilized to give an optimized design solution for the tooling, process machinery, and the roof molding.},
keywords = {31. Weight Engineering - Surface Transportation},
pubstate = {published},
tppubtype = {inproceedings}
}
1998
@inproceedings{2425,
title = {2425. Magnesium Exposition and Symposium to Champion Automotive Applications},
author = {J Balzer},
url = {https://www.sawe.org/product/paper-2425},
year = {1998},
date = {1998-05-01},
booktitle = {57th Annual Conference, Wichita, Kansas, May 18-20},
pages = {15},
publisher = {Society of Allied Weight Engineers, Inc.},
address = {Wichita, Kansas},
abstract = {This paper examines the organization of Ford Motor Company's MagExpo97. MagExpo97 was held November 19 and 20, 1997, at the Ford Technology Review Center and was the largest display of magnesium parts in the world to date. The goals of MagExpo97 were to: ? Educate the Ford engineering community and Tier 1 suppliers on current uses of magnesium in the Automotive Industry. ? Determine why most of the current magnesium applications are not considered ''core'' applications for Ford. ? Communicate to the Tier 1 suppliers Ford's effort in weight reduction, specifically with the use of magnesium. To achieve these goals, the Expo was organized into four different activities: ? Exhibits ? Roundtable Brainstorming Sessions ? Executive Reception ? Presentations This paper discusses each activity in detail including the organization efforts, perceived benefits, and improvement opportunities. Each activity was important as it provided a variety of forums for the various types of MagExpo97 attendees (Ford design engineers, suppliers, executives) to expand their knowledge in magnesium automotive components. The final ideas discussed in this paper are Lessons Learned. Following the Expo, the Project Management team held wrap-up meetings to reflect on MagExpo97. These lessons learned can be incorporated in future Expos at Ford Motor Company and, though structured for the automotive/magnesium arena, the principles discussed can easily be applied to other industries and materials that will assist in the weight reduction efforts.},
keywords = {31. Weight Engineering - Surface Transportation},
pubstate = {published},
tppubtype = {inproceedings}
}