SAWE Technical Papers
Technical Library
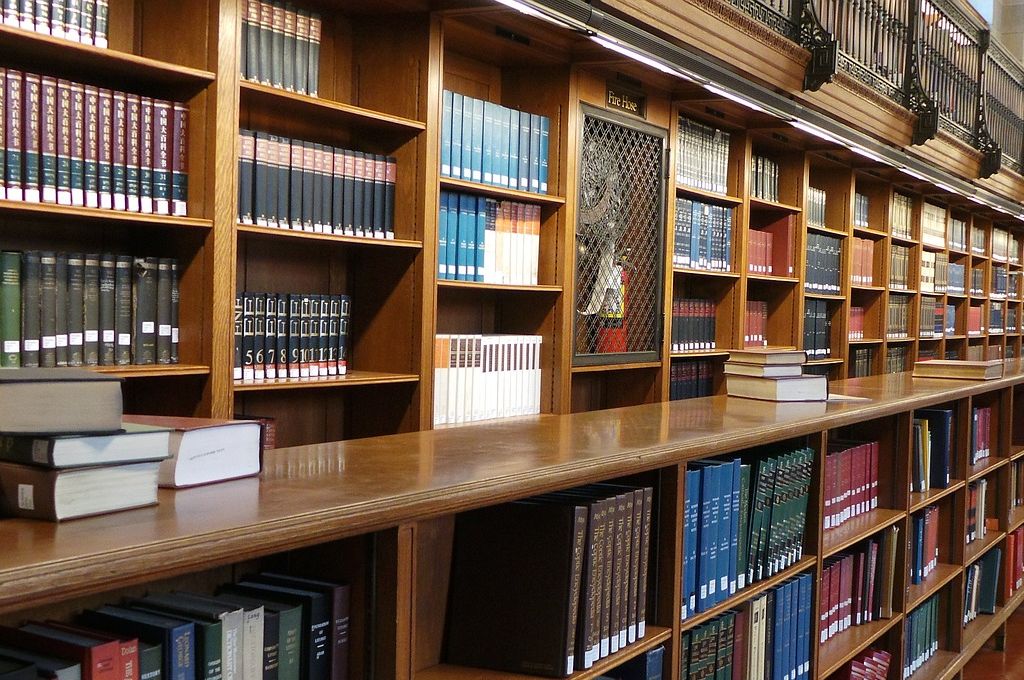
SAWE Paper Database
The SAWE Technical Library contains nearly 4000 technical papers available here for purchase and download. Use the search options below to find what you need.
González-González, Rubén; García-Pérez, Dr. Andrés; Alonso-Rodrigo, Dr. Gustavo In: 82nd Annual Conference, Cocoa Beach, Florida, pp. 23, Society of Allied Weight Engineers, Inc., Cocoa Beach, Florida, 2023. Abstract | Buy/Download | BibTeX | Tags: Missiles and Space - Launch Vehicles, Student Papers 3793. Effects of Mass and Pitch Moment of Inertia on Vehicle Suspension Design With Race Car Example Stabile, Pietro; Ballo, Federico; Previati, Giorgio In: 82nd Annual Conference, Cocoa Beach, Florida, pp. 11, Society of Allied Weight Engineers, Inc., Cocoa Beach, Florida, 2023. Abstract | Buy/Download | BibTeX | Tags: Ground Vehicles, Student Papers 3767. Determining Center of Gravity of Irregular-Shaped Bodies via Suspension Markovich, Emma In: 81st Annual Conference, Savannah, Georgia, pp. 23, Society of Allied Weight Engineers, Inc., Savannah, Georgia, 2022. Abstract | Buy/Download | BibTeX | Tags: 03. Center Of Gravity, Student Papers 3770. Mass Management of a High Energy-Efficient Battery Electric Vehicle Stabile, Pietro; Ballo, Federico; Previati, Giorgio In: 81st Annual Conference, Savannah, Georgia, pp. 15, Society of Allied Weight Engineers, Inc., Savannah, Georgia, 2022. Abstract | Buy/Download | BibTeX | Tags: 31. Weight Engineering - Surface Transportation, Student Papers 3779. Determining the Center of Gravity of the Electric No Emissions Low Drag Airframe (NELDA) Haley, Christl K. In: 81st Annual Conference, Savannah, Georgia, pp. 27, Society of Allied Weight Engineers, Inc., Savannah, Georgia, 2022. Abstract | Buy/Download | BibTeX | Tags: 03. Center Of Gravity, 10. Weight Engineering - Aircraft Design, Student Papers 3763. MauSPAF: Design of an Open-Source Mass Properties Management Framework Nuño, M.; Schröder, K. In: 81st Annual Conference, Savannah, Georgia, pp. 18, Society of Allied Weight Engineers, Inc., Savannah, Georgia, 2022. Abstract | Buy/Download | BibTeX | Tags: 12. Weight Engineering - Computer Applications, Student Papers 3768. Mass Properties Reporting Ma, Yiyuan; Yan, Jin; Elham, Ali In: 2021 SAWE Tech Fair, pp. 28, Society of Allied Weight Engineers, Inc., Virtual Conference, 2021. Abstract | Buy/Download | BibTeX | Tags: 10. Weight Engineering - Aircraft Design, 11. Weight Engineering - Aircraft Estimation, Student Papers 3772. Scenario-based Prediction of Lightweight Costs - an Approach across Industries Wätzold, Florian In: 2021 SAWE Tech Fair, pp. 38, Society of Allied Weight Engineers, Inc., Virtual Conference, 2021. Abstract | Buy/Download | BibTeX | Tags: 29. Weight Value-Of-Pound, Student Papers 3774. Weight Control For Floating Wind Installation Crowle, A. P.; Thies, P. R. In: 2021 SAWE Tech Fair, pp. 10, Society of Allied Weight Engineers, Inc., Virtual Conference, 2021. Abstract | Buy/Download | BibTeX | Tags: 24. Weight Engineering - System Design, 35. Weight Engineering - Offshore, Marine, Student Papers Konersmann, M.; Schmidt, M.; Neveling, S.; Scholjegerdes, M.; Diekmann, F.; Moxter, T.; Nuño, Miguel In: 2020 SAWE Tech Fair, pp. 16, Society of Allied Weight Engineers, Inc., Virtual Conference, 2020. Abstract | Buy/Download | BibTeX | Tags: 11. Weight Engineering - Aircraft Estimation, 21. Weight Engineering - Statistical Studies, Student Papers 3749. One Fits All? A Comparison of Weight Estimation Methods for Preliminary Aircraft Design Kluender, Arthur; Gobbin, Andreas In: 2020 SAWE Tech Fair, pp. 17, Society of Allied Weight Engineers, Inc., Virtual Conference, 2020. Abstract | Buy/Download | BibTeX | Tags: 11. Weight Engineering - Aircraft Estimation, 21. Weight Engineering - Statistical Studies, Student Papers 3758. Strategies for the Grid Stiffened Composite Panel Topology Optimization for Minimum Weight Talele, Mohit; Elham, Ali In: 2020 SAWE Tech Fair, pp. 25, Society of Allied Weight Engineers, Inc., Virtual Conference, 2020. Abstract | Buy/Download | BibTeX | Tags: 22. Weight Engineering - Structural Design, 27. Weight Reduction - Materials, Student Papers 3760. Design for Positive Static Margin for a Radio-Controlled Box-Wing Aircraft Bellerjeau, Charlotte In: 2020 SAWE Tech Fair, pp. 12, Society of Allied Weight Engineers, Inc., Virtual Conference, 2020. Abstract | Buy/Download | BibTeX | Tags: 10. Weight Engineering - Aircraft Design, 34. Advanced Design, Student Papers 3702. Uncertainty Modelling in a Wing Weight Convergence Simulation Framework Ries, T; Sartor, P; Cooper, J; Cheeseman, J In: 77th Annual Conference, Irving, Texas, pp. 14, Society of Allied Weight Engineers, Inc., Irving, Texas, 2018. Abstract | Buy/Download | BibTeX | Tags: Student Papers 3703. DRIFT: Drone-Rover Integrated Fire Tracker System Rashid, Nur; Deen, Syaminmah; Bishop, Amber; Collins, Daniel; Cott, Brandon; Growley, Samantha; Lieberman, Pierce; Owens, Kelsey; Stanco, Anthony; Stoffle, Matthew; Wiemelt, Nick In: 77th Annual Conference, Irving, Texas, pp. 11, Society of Allied Weight Engineers, Inc., Irving, Texas, 2018. Abstract | Buy/Download | BibTeX | Tags: Student Papers 3679. Design and Optimization of an Aluminum Structure Assembled by Elastic Fastening Laverne, Clément; Desrochers, Alain; Maslouhi, Ahmed In: 76th Annual Conference, Montreal, Canada, pp. 26, Society of Allied Weight Engineers, Inc., Montreal, Canada, 2017. Abstract | Buy/Download | BibTeX | Tags: 22. Weight Engineering - Structural Design, Student Papers Klim, Graeme; Hashemi, Dr. Seyed M. In: 76th Annual Conference, Montreal, Canada, pp. 25, Society of Allied Weight Engineers, Inc., Montreal, Canada, 2017. Abstract | Buy/Download | BibTeX | Tags: 22. Weight Engineering - Structural Design, 34. Advanced Design, Student Papers 3685. Design of an internal aerodynamic load cell for static for oscillating airfoils Miloud, Kamal Ben; Fellouah, Hachimi In: 76th Annual Conference, Montreal, Canada, pp. 7, Society of Allied Weight Engineers, Inc., Montreal, Canada, 2017. Abstract | Buy/Download | BibTeX | Tags: 11. Weight Engineering - Aircraft Estimation, Student Papers 3691. Methods to Evaluate the Mass Properties of a Scale Model Aircraft Kohtanen, Eetu; Davis, R. Benjamin In: 76th Annual Conference, Montreal, Canada, pp. 12, Society of Allied Weight Engineers, Inc., Montreal, Canada, 2017. Abstract | Buy/Download | BibTeX | Tags: 06. Inertia Measurements, 08. Weighing, 11. Weight Engineering - Aircraft Estimation, Student Papers 3662. Minimizing Mass of a Spacecraft Structure Burkey, Larry; Cervantes, Jorge; Gillis, Lewis; Graser, Evan; Howard, Megan; Iskra, Andrei; Maurer, Taylor; Peterson, Davis; Williams, Margaret In: 75th Annual Conference, Denver, Colorado, pp. 26, Society of Allied Weight Engineers, Inc., Denver, Colorado, 2016. Abstract | Buy/Download | BibTeX | Tags: 10. Weight Engineering - Aircraft Design, Student Papers2023
@inproceedings{3787,
title = {3787. Small Satellites Launcher Mass Properties Estimation for Design Efficiency Improvement in Preliminary Conceptual Phase},
author = {Rubén González-González and Dr. Andrés García-Pérez and Dr. Gustavo Alonso-Rodrigo},
url = {https://www.sawe.org/product/paper-3787},
year = {2023},
date = {2023-05-20},
urldate = {2023-05-20},
booktitle = {82nd Annual Conference, Cocoa Beach, Florida},
pages = {23},
publisher = {Society of Allied Weight Engineers, Inc.},
address = {Cocoa Beach, Florida},
abstract = {The aim of this paper is to introduce the current research at “Universidad Politécnica de Madrid” to increase the design efficiency of small space launchers in the preliminary conceptual phases based on a new approach in MBSE methodology that introduces efficient and fast simulations reducing their costs by finding an optimal balance with design weights.
In the last decade, the nano and micro satellites market has emerged as the most promising in the space sector with a profit of $143.7M in 2017 and a growth forecast of 13.43% until 2023 [1]. Despite this significant market growth, the current supply of launching services offer for these small payloads is almost non-existent and satellites manufacturers must share rides as secondary customers on larger heavy launchers, what often causes schedule and targeted orbit conflicts. Because of this market demand, over the past few years many small companies have started plans to develop small launchers but only RocketLab was successful with its Electron launcher (a two-stage-to-orbit launcher with 225kg payload capacity to Low-Earth-Orbits at 185km) reaching orbital injection several times and presenting a public service. However, Electron ́s launch price is around $33k/kg, far away from initial SpaceX Falcon1 2008 offer (11k$/kg) [2]. This market analysis demonstrates the urgent need for finding a design solution that will let to present a competitive small launcher offer.},
keywords = {Missiles and Space - Launch Vehicles, Student Papers},
pubstate = {published},
tppubtype = {inproceedings}
}
In the last decade, the nano and micro satellites market has emerged as the most promising in the space sector with a profit of $143.7M in 2017 and a growth forecast of 13.43% until 2023 [1]. Despite this significant market growth, the current supply of launching services offer for these small payloads is almost non-existent and satellites manufacturers must share rides as secondary customers on larger heavy launchers, what often causes schedule and targeted orbit conflicts. Because of this market demand, over the past few years many small companies have started plans to develop small launchers but only RocketLab was successful with its Electron launcher (a two-stage-to-orbit launcher with 225kg payload capacity to Low-Earth-Orbits at 185km) reaching orbital injection several times and presenting a public service. However, Electron ́s launch price is around $33k/kg, far away from initial SpaceX Falcon1 2008 offer (11k$/kg) [2]. This market analysis demonstrates the urgent need for finding a design solution that will let to present a competitive small launcher offer.@inproceedings{3793,
title = {3793. Effects of Mass and Pitch Moment of Inertia on Vehicle Suspension Design With Race Car Example},
author = {Pietro Stabile and Federico Ballo and Giorgio Previati},
url = {https://www.sawe.org/product/paper-3793},
year = {2023},
date = {2023-05-20},
urldate = {2023-05-20},
booktitle = {82nd Annual Conference, Cocoa Beach, Florida},
pages = {11},
publisher = {Society of Allied Weight Engineers, Inc.},
address = {Cocoa Beach, Florida},
abstract = {The present paper addresses the topic of studying the influence of the main vehicle inertia parameters on the suspension design. A simple four degrees-of-freedom half-car model is used to describe the dynamic behaviour of vehicles running on randomly profiled roads. The response of the system is analysed by evaluating three performance indexes, namely driver discomfort, road holding and working space, referring to the standard deviations of driver seat vertical acceleration, force at ground and relative displacement between wheels, respectively. The effect of varying wheel mass, vehicle mass, centre of gravity longitudinal location and pitch moment of inertia on the three performance indexes is investigated. The proposed approach is applied to the design of the suspension system of a vehicle conceived for efficiency-based competitions. Based on these results, considerations on the best location for battery pack and ballast are drawn.},
keywords = {Ground Vehicles, Student Papers},
pubstate = {published},
tppubtype = {inproceedings}
}
2022
@inproceedings{3767,
title = {3767. Determining Center of Gravity of Irregular-Shaped Bodies via Suspension},
author = {Emma Markovich},
url = {https://www.sawe.org/product/paper-3767},
year = {2022},
date = {2022-05-21},
urldate = {2022-05-21},
booktitle = {81st Annual Conference, Savannah, Georgia},
pages = {23},
publisher = {Society of Allied Weight Engineers, Inc.},
address = {Savannah, Georgia},
abstract = {The precise determination of the center of gravity of an aircraft is essential for the balance, stability, and overall safety of flight. Military aircraft often carry additional attachments, such as wing-mounted surveillance equipment, fuel tanks, or weaponry, which alter the weight and balance characteristics of the aircraft. In the application explored in this paper, a novel suspension system for determining the center of gravity of surveillance pods varying in shape and size is developed. This allows for the calculation of the center of gravity of aircraft attachments utilizing a two-point connection - the same attachment method as used on an aircraft. The tool features a hinged testbed that is suspended from a rigid frame by three load sensing devices. Two measurement sets are taken at different inclinations using an inverted three-point weighing method which allows the center of gravity to be calculated in all three dimensions. To recover measurement accuracy lost due to the limitation of inclination angles to less than 20 degrees, a high precision inclinometer is utilized. Based on the specifications of the sensing equipment and extensive Monte Carlo simulation of errors in force measurement, inclination angle, geometric dimensions, and data sampling, it is expected that the center of gravity can be reliably calculated to within 0.1 inches of the true value. Using the tool, objects ranging from 180 lb to 2000 lb with sizes of up to 12 x 4 x 4 feet can be measured with this accuracy. The modular design of the apparatus, data acquisition methods, and analysis relating to computation of the center of gravity will be presented. Additionally, the paper will discuss error analysis for the measurements, as well as verification and validation methods.},
keywords = {03. Center Of Gravity, Student Papers},
pubstate = {published},
tppubtype = {inproceedings}
}
@inproceedings{3770,
title = {3770. Mass Management of a High Energy-Efficient Battery Electric Vehicle},
author = {Pietro Stabile and Federico Ballo and Giorgio Previati},
url = {https://www.sawe.org/product/paper-3770},
year = {2022},
date = {2022-05-21},
urldate = {2022-05-21},
booktitle = {81st Annual Conference, Savannah, Georgia},
pages = {15},
publisher = {Society of Allied Weight Engineers, Inc.},
address = {Savannah, Georgia},
abstract = {The paper presents a detailed analysis of the mass-induced power demand of an ultra-efficient battery electric vehicle. The vehicle belongs to a special class of lightweight quadricycles, designed for participating to efficiency competitions. The influence of reducing the mass of the entire vehicle and the mass of the wheels on the vehicle energy consumption is assessed. A sensitivity analysis is performed by exploiting a “tank-to- wheel” multi-physics model of the vehicle. The model includes the main vehicle subsystems and the principal sources of power dissipation are modelled. A three-step sensitivity analysis is carried out: firstly, the influence of the mass reduction on the energy saving is analysed for two different race tracks; then, two different driving behaviour on the same track are compared; finally, the potential energy saving due to actual lightweighting interventions performed on the vehicle is computed. In this phase, secondary mass reduction effects (battery downsizing) are included in the simulation. Results are expressed in terms of Energy Reduction Value (ERV), a parameter widely used in the literature to quantify the correlation between mass reduction and energy saving. The vehicle studied in this paper shows an ERV due to vehicle mass reduction ranging from 0.23 to 0.36 kWh/(100 km∙100 kg), while wheel lightweighting leads to an ERV ranging from 1.03 to 1.74 kWh/(100 km∙100 kg).},
keywords = {31. Weight Engineering - Surface Transportation, Student Papers},
pubstate = {published},
tppubtype = {inproceedings}
}
@inproceedings{3779,
title = {3779. Determining the Center of Gravity of the Electric No Emissions Low Drag Airframe (NELDA)},
author = {Christl K. Haley},
url = {https://www.sawe.org/product/paper-3779},
year = {2022},
date = {2022-05-21},
urldate = {2022-05-21},
booktitle = {81st Annual Conference, Savannah, Georgia},
pages = {27},
publisher = {Society of Allied Weight Engineers, Inc.},
address = {Savannah, Georgia},
abstract = {Although climate change has become an impending issue for all of humanity, it has brought nations together to design and create a variety of systems that leave little to no carbon footprint. The No Emission Low Drag Airframe (NELDA) is a unique electric aircraft design which aims to join this world-wide mission. The author (the airframe design lead) and her senior design team from the University of Colorado Boulder spent the fall semester of 2021 designing this commuter aircraft. NELDA can fly 6 passengers at a cruise altitude of 12,000 ft MSL, at a cruise speed of 150 knots for 1.5 hours with a 30-minute reserve, making this a perfect aircraft for short, direct flights. The characteristics for this aircraft aim to be certified under Federal Aviation Regulation (FAR) 23 to ensure the safety of every passenger. Multiple trade studies were conducted to determine the design choices that make up this innovative aircraft. These studies resulted in an aft-mid-mounted wing, a canard, fixed tricycle landing gear, butterfly doors, and a pusher-propeller powertrain configuration. The specific energy, density, volume, and weight of the electric powertrain were estimated using a 5-year prediction for solid-state batteries. Since these batteries do not exist today, it was very challenging to accurately model and place the power system. The range and endurance of NELDA were used to determine the volume, number, and weight of the batteries. The safety of passengers, size of the batteries, and functionality of each battery were all considered while determining where and how to place the batteries among the other major components of NELDA. Additionally, it was critical to strategically place each of the components to achieve an acceptable static margin of 10%, as well as predictable dynamic and static flight characteristics. The designers of NELDA believe that their successful commuter electric airplane design will be part of the beginning of new, improved, clean aerial transportation.},
keywords = {03. Center Of Gravity, 10. Weight Engineering - Aircraft Design, Student Papers},
pubstate = {published},
tppubtype = {inproceedings}
}
@inproceedings{3763,
title = {3763. MauSPAF: Design of an Open-Source Mass Properties Management Framework},
author = {M. Nuño and K. Schröder},
url = {https://www.sawe.org/product/paper-3763},
year = {2022},
date = {2022-05-21},
urldate = {2022-05-21},
booktitle = {81st Annual Conference, Savannah, Georgia},
pages = {18},
publisher = {Society of Allied Weight Engineers, Inc.},
address = {Savannah, Georgia},
abstract = {In this paper, an open-source mass properties calculation and management created using Python 3 is presented. The program implements uncertainty calculations using Monte Carlo simulations, mass properties calculations and basic tree structures. It also includes a library with aircraft mass estimation and calculation functions for simple geometrical shapes. To argument the design decisions, a thorough review of available literature about mass calculation tools is performed.},
keywords = {12. Weight Engineering - Computer Applications, Student Papers},
pubstate = {published},
tppubtype = {inproceedings}
}
2021
@inproceedings{3768,
title = {3768. Mass Properties Reporting},
author = {Yiyuan Ma and Jin Yan and Ali Elham},
url = {https://www.sawe.org/product/paper-3768},
year = {2021},
date = {2021-11-01},
urldate = {2021-11-01},
booktitle = {2021 SAWE Tech Fair},
pages = {28},
publisher = {Society of Allied Weight Engineers, Inc.},
address = {Virtual Conference},
abstract = {The Ultra-High Aspect Ratio Wing (UHARW) concept can improve the aircraft's aerodynamic efficiency and reduce fuel consumption. The Twin-Fuselage (TF) configuration is one of the most promising concepts for the UHARW design to reduce the wing bending moments and shear forces. This paper presents the development of a semi-empirical method for the weight estimation of TF aircraft in the initial sizing stage. A physics-based wing weight estimation method is improved for higher aerodynamic analysis fidelity and composite materials, which is used in the design of experiments and the results are applied for regression analysis to establish a semi-empirical method. Eventually, the established semi- empirical weight estimation method is integrated into a TF aircraft conceptual design and performance analysis framework, and a mid-range TF aircraft and a long-range TF aircraft are designed and sized to illustrate its application and efficiency in rapidly estimating the TF aircraft weight breakdown.},
keywords = {10. Weight Engineering - Aircraft Design, 11. Weight Engineering - Aircraft Estimation, Student Papers},
pubstate = {published},
tppubtype = {inproceedings}
}
@inproceedings{3772,
title = {3772. Scenario-based Prediction of Lightweight Costs - an Approach across Industries},
author = {Florian Wätzold},
url = {https://www.sawe.org/product/paper-3772},
year = {2021},
date = {2021-11-01},
urldate = {2021-11-01},
booktitle = {2021 SAWE Tech Fair},
pages = {38},
publisher = {Society of Allied Weight Engineers, Inc.},
address = {Virtual Conference},
abstract = {To decide on which technology is best for a vehicle in development, technical and economical constraints need to be considered. The objective of this paper is to provide a generic, conceptual approach to estimating the value (€ or $) per weight unit (kg or lb), referred as lightweight cost, for all industries. It combines general project management and cost estimation techniques with mass property management. As cost and weight are unknown until the actual weighing or billing, this paper focuses on scenario-based assumptions. For an easy understanding, this lens is applied to a recently developed battery concept.
The described approach integrates basic project management processes such as risk management, estimation considerations and cost assessment. In this pursuit, mass and cost are rolled-up based on the breakdown structure. Taking the uncertainties into account a most likely, best, and worst case are evaluated and a cone of respective lightweight cost is generated. For the ease of use in industrial daily business exactly one value per pound for decision making is derived, condensing the lightweight cost range by superimposing the mass and cost according to their specific scenario probability.},
keywords = {29. Weight Value-Of-Pound, Student Papers},
pubstate = {published},
tppubtype = {inproceedings}
}
The described approach integrates basic project management processes such as risk management, estimation considerations and cost assessment. In this pursuit, mass and cost are rolled-up based on the breakdown structure. Taking the uncertainties into account a most likely, best, and worst case are evaluated and a cone of respective lightweight cost is generated. For the ease of use in industrial daily business exactly one value per pound for decision making is derived, condensing the lightweight cost range by superimposing the mass and cost according to their specific scenario probability.@inproceedings{3774,
title = {3774. Weight Control For Floating Wind Installation},
author = {A. P. Crowle and P. R. Thies},
url = {https://www.sawe.org/product/paper-3774},
year = {2021},
date = {2021-11-01},
urldate = {2021-11-01},
booktitle = {2021 SAWE Tech Fair},
pages = {10},
publisher = {Society of Allied Weight Engineers, Inc.},
address = {Virtual Conference},
abstract = {Floating offshore wind is a growing market within the renewable energy sector. The floating offshore wind turbines give access to deeper water sites, with minimal visual impact from land. The paper includes the weight control requirements for Spars, barges, semi submersibles and Tension Leg Platforms (TLPs) as floating wind platforms.
There are weight control challenges for the various substructure types during the temporary phases of construction and offshore installation. An accurate assessment of the buoyancy of the floating wind turbine for different drafts and trims is required. Allowances need to be included in the weight calculation for temporary buoyancy, sea-fastenings and grillage.
Weight control for installation has an influence on the weather window for the floating substructures during transportation to the offshore site and mooring and electrical connection. The paper will cover weight calculation methods during early design, detailed design, construction, installation, operation and demolition.
The installation process for a floating wind turbine varies with substructure type and this paper will give an overview of the weight control requirements for loadout, ocean transport and mooring connection. The floating offshore wind turbine weight and centre of gravity has a direct bearing on draft, intact stability and motions. As part of the weight control process the centre of gravity and radii of gyration need to be accurately determined for each stage of the installation.},
keywords = {24. Weight Engineering - System Design, 35. Weight Engineering - Offshore, Marine, Student Papers},
pubstate = {published},
tppubtype = {inproceedings}
}
There are weight control challenges for the various substructure types during the temporary phases of construction and offshore installation. An accurate assessment of the buoyancy of the floating wind turbine for different drafts and trims is required. Allowances need to be included in the weight calculation for temporary buoyancy, sea-fastenings and grillage.
Weight control for installation has an influence on the weather window for the floating substructures during transportation to the offshore site and mooring and electrical connection. The paper will cover weight calculation methods during early design, detailed design, construction, installation, operation and demolition.
The installation process for a floating wind turbine varies with substructure type and this paper will give an overview of the weight control requirements for loadout, ocean transport and mooring connection. The floating offshore wind turbine weight and centre of gravity has a direct bearing on draft, intact stability and motions. As part of the weight control process the centre of gravity and radii of gyration need to be accurately determined for each stage of the installation.2020
@inproceedings{3743,
title = {3743. FVA30: Application of Probabilistic Mass Estimation Methods to the Design of a Touring Motor Glider},
author = {M. Konersmann and M. Schmidt and S. Neveling and M. Scholjegerdes and F. Diekmann and T. Moxter and Miguel Nuño},
url = {https://www.sawe.org/product/paper-3743},
year = {2020},
date = {2020-07-01},
booktitle = {2020 SAWE Tech Fair},
pages = {16},
publisher = {Society of Allied Weight Engineers, Inc.},
address = {Virtual Conference},
abstract = {In early design phases the mass and position of many aircraft components is uncertain. So, it is not possible to accurately calculate key aircraft parameters such as the total mass and center of gravity. A possible approach to deal with these uncertainties is using pessimistic and optimistic estimations for every component. This approach considers only the boundary values and can therefore lead to very conservative decisions. To reduce the uncertainty of the calculations and get a better estimation of the expected mass properties probabilistic mass estimation methods can be used.The FVA 30 is a hybrid electric motorglider being developed by students at the Flugwissenschaftliche Vereinigung Aachen (FVA). The configuration of the prototype features two electric engines in the V-tail unit and is therefore especially sensitive to mass changes. In this paper the usage of probabilistic mass estimation and propagation methods to design the FVA 30 is presented. Several methods to estimate probability distributions of different components are described. The propagation of uncertainties is calculated using Monte Carlo simulations with random sampling. At last, the probabilistic calculation results are discussed and compared with the ones using a deterministic method.},
keywords = {11. Weight Engineering - Aircraft Estimation, 21. Weight Engineering - Statistical Studies, Student Papers},
pubstate = {published},
tppubtype = {inproceedings}
}
@inproceedings{3749,
title = {3749. One Fits All? A Comparison of Weight Estimation Methods for Preliminary Aircraft Design},
author = {Arthur Kluender and Andreas Gobbin},
url = {https://www.sawe.org/product/paper-3749},
year = {2020},
date = {2020-07-01},
booktitle = {2020 SAWE Tech Fair},
pages = {17},
publisher = {Society of Allied Weight Engineers, Inc.},
address = {Virtual Conference},
abstract = {Is there any compelling way to precisely determine the major masses of an aircraft in preliminary design stages? If so, do the results match the real airplane weight properties, when it is built? This paper presents a comprehensive overview of commonly used approaches, highlighting their individual (dis)advantages and eligibility for typical transport missions. The study evaluates widely used, of-the-book-methods for weight estimation and searches for the most accurate approach among them. Each method is applied to determine the masses of four different aircraft, each of them representing a typical aircraft category. The results are put in relation to the real masses, extracted from the corresponding manufacturers manual. In addition, an extended and modified method, already existing and being used at the Department for Aircraft Design and Lightweight Structures at the Technical University of Berlin, is included in the study and tested for its reliability. The overall objective of this paper is to evaluate, whether there is a method that precisely calculates all relevant masses or else, which one delivers the most accurate results for various aircraft types. In order to differentiate even further, the set of required input parameters is considered. In early design phases, typically only a few of those are known. Hence, a method that leads to accurate results with minimal input is favorable for preliminary design. The study indicates that none of the methods covers all the aircraft types. However, tendencies show that some approaches suit certain aircraft types better than others. Most of them provide satisfactory results for an average, jet-engine propelled, single aisle, medium range aircraft in conventional twinjet configuration. Regarding more unusual configurations, for example with turboprop engines, the outcome differs noticeably. Also, for long range aircraft, only a few methods produce realistic numbers. According to this exploration, guidelines on when to use which method are provided. This is followed by an outlook, giving recommendations on the development of new methods. Ultimately, a suggestion on how to consider new technologies and implement them into existing methods of weight estimation is given.},
keywords = {11. Weight Engineering - Aircraft Estimation, 21. Weight Engineering - Statistical Studies, Student Papers},
pubstate = {published},
tppubtype = {inproceedings}
}
@inproceedings{3758,
title = {3758. Strategies for the Grid Stiffened Composite Panel Topology Optimization for Minimum Weight},
author = {Mohit Talele and Ali Elham},
url = {https://www.sawe.org/product/paper-3758},
year = {2020},
date = {2020-07-01},
booktitle = {2020 SAWE Tech Fair},
pages = {25},
publisher = {Society of Allied Weight Engineers, Inc.},
address = {Virtual Conference},
abstract = {In this paper, a topology optimization methodology for the minimum weight of the composite stiffened panel with the constraint on the criticial buckling load is presented. An existing finite element solver [1] for the analysis of the stiff- ened tow steered composite panels is extended to perform the topology optimiza- tion for the minimum weight. The panel and the stiffeners are modelled using 3 node traingular Classical Laminate Plate elements (CLPT) and 2 node timoshenko beam elements, respectively. To achieve the independent meshing of the plate and stringers, the Lagrange multiplier based on a weak formulation of the continuity requirements between the plate elements and the beam elements is used. For a specific critical buckling load, the optimum topology of the stiffeners in the stiff- ened composite panel depends not only on the stiffeners but also on the fiber patten of the composite panel. Therefore, design variables corrosponding to both fiber pattern in the skin and stiffeners needs to be considered. Manufacturing mesh ap- proach presented in [1], is used to define the design variables corrosponding to the fiber pattern. The ground structure method is implemented to optimize stringers topology. The cross-sectional area of the stringers in the ground structure are de- fined as the design variables corrosponding to the stiffeners. To perform the robust the optimization, the analytical gradients of the buckling load and the weight of the stiffened panel with respect to design variables are implemented and verified using finite difference. The optimization for the minimum weight is performed for the varied complexities of the ground structures with the constraints on the critical buckling load.},
keywords = {22. Weight Engineering - Structural Design, 27. Weight Reduction - Materials, Student Papers},
pubstate = {published},
tppubtype = {inproceedings}
}
@inproceedings{3760,
title = {3760. Design for Positive Static Margin for a Radio-Controlled Box-Wing Aircraft},
author = {Charlotte Bellerjeau},
url = {https://www.sawe.org/product/paper-3760},
year = {2020},
date = {2020-07-01},
booktitle = {2020 SAWE Tech Fair},
pages = {12},
publisher = {Society of Allied Weight Engineers, Inc.},
address = {Virtual Conference},
abstract = {This paper will detail the aerodynamic design of a small unmanned box-wing aircraft to facilitate the study of turbulence by Dr. Brian Argrow at the CU Boulder. A design with no fuselage was necessary for the data collection, which presented a longitudinal stability challenge. The key to eventually achieving a stable design was weight placement for positive static margin. This paper will include the design process used to confront these issues. The initial choices of stagger, gap, decalage, and relative sweep are made using a simple model leveraging previous box-wing research. These, as well as the airfoil selection, are then investigated further using Athena Vortex Lattice (AVL) to analyze lift, drag, and stability. The final airframe design has a gap and stagger of 1 chord length, decalage of 5 degrees, and relative sweep of 30 degrees. A cambered NACA 6412 airfoil on the top wing and a reflexed NACA23112 airfoil on the bottom wing are selected, which combine to induce a positive pitching moment and aid in longitudinal stability. The resulting box-wing aircraft was flight tested successfully and will serve as an ideal platform for research at CU Boulder.},
keywords = {10. Weight Engineering - Aircraft Design, 34. Advanced Design, Student Papers},
pubstate = {published},
tppubtype = {inproceedings}
}
2018
@inproceedings{3702,
title = {3702. Uncertainty Modelling in a Wing Weight Convergence Simulation Framework},
author = {T Ries and P Sartor and J Cooper and J Cheeseman},
url = {https://www.sawe.org/product/paper-3702},
year = {2018},
date = {2018-05-01},
booktitle = {77th Annual Conference, Irving, Texas},
pages = {14},
publisher = {Society of Allied Weight Engineers, Inc.},
address = {Irving, Texas},
abstract = {Weight is a key element in aircraft design, having a major influence on its performance and being a common factor to all disciplines involved in the decision making process, i.e. aero- dynamics, structural sizing, materials, loads, geometry, cost, manufacturing, etc. To ensure an optimal trade-off is achieved, alongside a smooth convergence to the desired final aircraft weight, it is essential to be able to model the aircraft weight estimation process throughout the design, including assessment of uncertainty and risk. Weight estimation processes and uncer- tainty analysis are well established bodies of literature. Yet, its unification into a framework that can deliver meaningful managerial information is a new research branch.This paper presents a new methodology for quantifying uncertainty and performing sensi- tivity studies on aircraft weight estimation. A framework has been developed that emulates the weight convergence corridor for an aircraft wing. It combines a traditional wing-box sizing method for primary weight with alternative methods for secondary weight. The alternative methods mimic the different phases of design in the aircraft development cycle. Maturity of design translates to the status of the information available, which translates to accuracy in the weight estimation method in use.This process incorporates uncertainty in the form of modelling the desired input parame- ters as probability density functions (PDFs). The uncertain input space may include wing and engine planform geometry, wing-box material properties, load cases, general aircraft weights and fuselage dimensions. Design features and aircraft components are correlated and there- fore an underlying dependency grid prevails. Combining the PDFs on the grid propagates the uncertainty towards an ultimate distribution of the total wing weight.This paper investigates the use of the framework developed for wing weight estimation by quantifying design sensitivities impact on wing weight. The methodology is demonstrated on a representative commercial jet airliner wing.},
keywords = {Student Papers},
pubstate = {published},
tppubtype = {inproceedings}
}
@inproceedings{3703,
title = {3703. DRIFT: Drone-Rover Integrated Fire Tracker System},
author = {Nur Rashid and Syaminmah Deen and Amber Bishop and Daniel Collins and Brandon Cott and Samantha Growley and Pierce Lieberman and Kelsey Owens and Anthony Stanco and Matthew Stoffle and Nick Wiemelt},
url = {https://www.sawe.org/product/paper-3703},
year = {2018},
date = {2018-05-01},
booktitle = {77th Annual Conference, Irving, Texas},
pages = {11},
publisher = {Society of Allied Weight Engineers, Inc.},
address = {Irving, Texas},
abstract = {Wildfire reconnaissance and mitigation efforts are a primary concern for the United States Department of the Interior and National Forest Service. The critical consequences of climate change are becoming more prevalent with longer fire seasons throughout the Western United States [1]. The fire seasons are characterized by hotter and drier conditions, allowing for a wildfire to easily start and rapidly spread with the potential to burn millions of acres and cause billions of dollars in property loss. The National Forest Service (NFS) predicts that it will spend over half of its budget in the fight against wildfires within the next decade [2]. Wildfires can have devastating impacts on communities, ecosystems and wildlife, but also pose a dangerous threat to the fire fighters responsible for their mitigation and containment. A Mother Rover-Child Drone Firetracker System will assist firefighters by traveling to locations at risk of wildfire and gather environmental data which it then transmits back to the designated ground station. This provides information on a fire's intensity, severity, and extent while firefighters remain a safe distance away from the threat. Team DRIFT is a group of eleven undergraduate Aerospace Engineering Sciences students at the University of Colorado Boulder currently developing the Mother-Rover for the Firetracker System with the purpose to secure and carry the Child Drone (Unmanned Aerial Vehicle) to a desired location of interest. The development of this Mother- Rover involves integrating the hardware and software of the already completed Child Drone and Landing Platform. The Mother Rover, approximately 46.3 by 58.9 inches, weighing 450 lbs and driven by a remote operator, is capable of traversing rough terrain, defined by small gravel, fine dirt, and slopes up to 20 degrees. Due to the image recognition system utilized on the landing platform for the autonomous landing of the Child Drone, the landing platform must be level to within 3.5 degrees in order for the child drone to safely take off and land. Therefore, the Mother Rover utilizes an internal leveling jack system to level in the landing platform to within 3.5 degrees if the child drone is to be deployed on a slope. The considerable weight of the Mother Rover presents a unique engineering challenge as it must be capable of traversing over the defined rough terrain while also maintaining the security of the onboard Child Drone. The design solution for this Mother Rover and associated leveling system will be discussed in this paper.},
keywords = {Student Papers},
pubstate = {published},
tppubtype = {inproceedings}
}
2017
@inproceedings{3679,
title = {3679. Design and Optimization of an Aluminum Structure Assembled by Elastic Fastening},
author = {Clément Laverne and Alain Desrochers and Ahmed Maslouhi},
url = {https://www.sawe.org/product/paper-3679},
year = {2017},
date = {2017-05-01},
booktitle = {76th Annual Conference, Montreal, Canada},
pages = {26},
publisher = {Society of Allied Weight Engineers, Inc.},
address = {Montreal, Canada},
abstract = {Actual research tends to replace some steel structures by aluminum ones, leading to a better resistance to corrosion and mass reduction, for example in automobile frames, bridge decks, in the navy and in aeronautical fields. These structural decks are often welded, which need tools and labor, hence the idea of an assembly based on a fastening.This technology consists in an elastic deformation of the male part of the structure to fit into the female part by a springback of the material. This kind of assembly has the advantage to be quickly set up, with little labor and without any intermediate component. However, the elastic fastening introduces a mechanical weakness of the structure insofar as this technology is based on an important elastic deformation of an area of the part to enable the insertion.That is why the main issue of this project is to design and dimension an extruded aluminum structure assembled by an elastic fastening in order to withstand loads defined by the specifications of a bus floor while minimizing mass.Firstly, the general geometry of the deck has been chosen among several patterns usually used in aluminum structures thanks to a finite element study of their mechanical behavior exposed to loads defined by the specifications. The chosen pattern is composed of tilted stiffeners between two plates. Then, the Gauss- Newton method of optimization has been realized to calculate the optimal set of geometric parameters of the stiffeners. The four parameters to optimize were the gaps between the stiffeners, their angle and their length while the functions to minimize were the stresses and strains of typical loading conditions and the standards found in buses specifications. After that, the thicknesses have been dimensioned by a loop based on the dichotomy principle to respect the specifications. These operations were realized with an interface between Matlab and Ansys. Finally, the thickness of the deformable part of the fastening has been calculated with a simple analytical model to enable the insertion.An experimental approach with a prototype was included to validate the results of the optimization and the dimensioning by a measurement of stresses and deflections on critical points and to compare the welding, the bounding and the elastic fastening.},
keywords = {22. Weight Engineering - Structural Design, Student Papers},
pubstate = {published},
tppubtype = {inproceedings}
}
@inproceedings{3680,
title = {3680. Designing Mass-Optimized Parts Using Solidthinking Inspire with Application to the Hyperloop Deployable Wheel System},
author = {Graeme Klim and Dr. Seyed M. Hashemi},
url = {https://www.sawe.org/product/paper-3680},
year = {2017},
date = {2017-05-01},
booktitle = {76th Annual Conference, Montreal, Canada},
pages = {25},
publisher = {Society of Allied Weight Engineers, Inc.},
address = {Montreal, Canada},
abstract = {Today's automotive and aerospace engineers are often faced with conflicting design goals; design for low cost or low weight. While advancements in aerospace materials, such as carbon fiber composites, have allowed engineers to design lighter parts, the cost to manufacture these parts is still very high. Similarly, recent advancements in additive manufacturing demonstrate an ability to produce lightweight, stiff structures, with a promise of future economic benefits including fuel savings, a result of optimized production part design. To realize additive manufacturing's benefits as they pertain to weight savings, design engineers must re-examine their approach to part and product design. This well-known challenge to improve the state of current design methods is being addressed through a 'design for additive manufacturing' movement that remains an ongoing subject of interest in the additive manufacturing and design communities. The present paper demonstrates the use of the industrial software tool, solidThinking Inspire, as a preliminary study and detail design weight reduction tool for additive manufacturing. To illustrate the software's usefulness, a primary structural component of the Hyperloop Deployable Wheel System, developed at Ryerson University, was selected for optimization, and designed for additive metal manufacturing production. The significant weight savings and material savings realized are presented while the potential for fast design, development and production of the part are highlighted in a step-by-step process.},
keywords = {22. Weight Engineering - Structural Design, 34. Advanced Design, Student Papers},
pubstate = {published},
tppubtype = {inproceedings}
}
@inproceedings{3685,
title = {3685. Design of an internal aerodynamic load cell for static for oscillating airfoils},
author = {Kamal Ben Miloud and Hachimi Fellouah},
url = {https://www.sawe.org/product/paper-3685},
year = {2017},
date = {2017-05-01},
booktitle = {76th Annual Conference, Montreal, Canada},
pages = {7},
publisher = {Society of Allied Weight Engineers, Inc.},
address = {Montreal, Canada},
abstract = {This project concerns the design of a three components internal aerodynamic load cell. This load cell will be used to measure the lift, drag and pitching moment in static or oscillating airfoils enduring air loads. The end objective is to study the complex unsteady 3 dimensional (3D) air flows interaction with airfoils. This interaction is often characterized by flow recirculation and massive flow separations that lead to reduction of both aerodynamic performance and structure fatigue.The Computer-aided design (CAD) of the internal load cell will be presented. Finite element analysis (FEA), through ANSYS software, is used to assess the design before its construction. The result shows the good response of the balance to simulated air loads.},
keywords = {11. Weight Engineering - Aircraft Estimation, Student Papers},
pubstate = {published},
tppubtype = {inproceedings}
}
@inproceedings{3691,
title = {3691. Methods to Evaluate the Mass Properties of a Scale Model Aircraft},
author = {Eetu Kohtanen and R. Benjamin Davis},
url = {https://www.sawe.org/product/paper-3691},
year = {2017},
date = {2017-05-01},
booktitle = {76th Annual Conference, Montreal, Canada},
pages = {12},
publisher = {Society of Allied Weight Engineers, Inc.},
address = {Montreal, Canada},
abstract = {Scale model ditching tests are sometimes conducted to study the loads and dynamic behavior associated with an aircraft during water impact. To ensure scalability of the results, the model's mass properties including weight, center of gravity, and pitch moment of inertia in particular must proportionally reflect the characteristics of the full-scale aircraft. This paper presents the experimental methods used to evaluate these mass characteristics for a 1/20th scale Gulfstream G550 model prior to ditching tests conducted at the University of Georgia. These methods can be used for any similarly sized model.To determine the center of gravity the aircraft model is placed on a v-block assembly resting on three force transducers arranged in an isosceles triangle formation. The model's center of gravity along longitudinal and lateral axes is found by summing moments about a known reference axes system using the static forces measured at each transducer. To find the vertical center of gravity, the model is rotated about its longitudinal axis in a v-block fixture, and the force readings along the projection of the rotated plane are then manipulated.For pitch inertia, a compound pendulum is used to measure the aircraft's period of oscillation which is related to the inertia about the axis of oscillation through an analytical method [1]. The inertia of the pendulum apparatus by itself is then subtracted from the total experimental inertia, and the parallel axis theorem is used to determine the model's pitch inertia about its center of gravity. To evaluate the accuracy of the pendulum method, aluminum and steel brackets with known mass properties are attached to the model's tail, and the pitch inertia is measured again for each bracket. The increase in inertia is then compared against the theoretical increase.},
keywords = {06. Inertia Measurements, 08. Weighing, 11. Weight Engineering - Aircraft Estimation, Student Papers},
pubstate = {published},
tppubtype = {inproceedings}
}
2016
@inproceedings{3662,
title = {3662. Minimizing Mass of a Spacecraft Structure},
author = {Larry Burkey and Jorge Cervantes and Lewis Gillis and Evan Graser and Megan Howard and Andrei Iskra and Taylor Maurer and Davis Peterson and Margaret Williams},
url = {https://www.sawe.org/product/paper-3662},
year = {2016},
date = {2016-05-01},
booktitle = {75th Annual Conference, Denver, Colorado},
pages = {26},
publisher = {Society of Allied Weight Engineers, Inc.},
address = {Denver, Colorado},
abstract = {The commercialization of the International Space Station (ISS) has created the opportunity for a wider variety of minisatellites to be launched to and deployed from the ISS. By utilizing ISS resupply vehicles, these spacecraft are launched to the ISS in a soft stowed configuration and undergo much lower vibration loads than in a typical launch configuration. The FeatherCraft spacecraft is designed to fully exploit this opportunity by offering a 100-kilogram spacecraft with 45 kilograms available for science payload use. This leaves only 5 kilograms for the required side panels and internal mounting surfaces that constitute the spacecraft structure. Most spacecraft structures represent approximately 20% of the total spacecraft mass, so the reduction of the structure to 5% of the total mass requires innovative mass-relieving techniques. To solve this problem, undergraduate aerospace engineering students at the University of Colorado at Boulder created FISH, the FeatherCraft Integrated Structural Housing, which achieves the required mass reduction and integrates with other spacecraft components. This unprecedented mass reduction is accomplished by utilizing composite materials, minimizing structure area and thickness, and finally using adhesives for attachments on nearly every interface. Critical components of the structure design were preliminarily verified through bending tests, Finite Element Analysis (FEA), and adhesive tests. A complete structural full-scale model will be tested under the expected vibrational loads and acceleration measurements will be taken to verify expected performance. The success of this novel design creates a new cost-effective approach to Low-Earth-orbiting missions.},
keywords = {10. Weight Engineering - Aircraft Design, Student Papers},
pubstate = {published},
tppubtype = {inproceedings}
}