SAWE Technical Papers
Technical Library
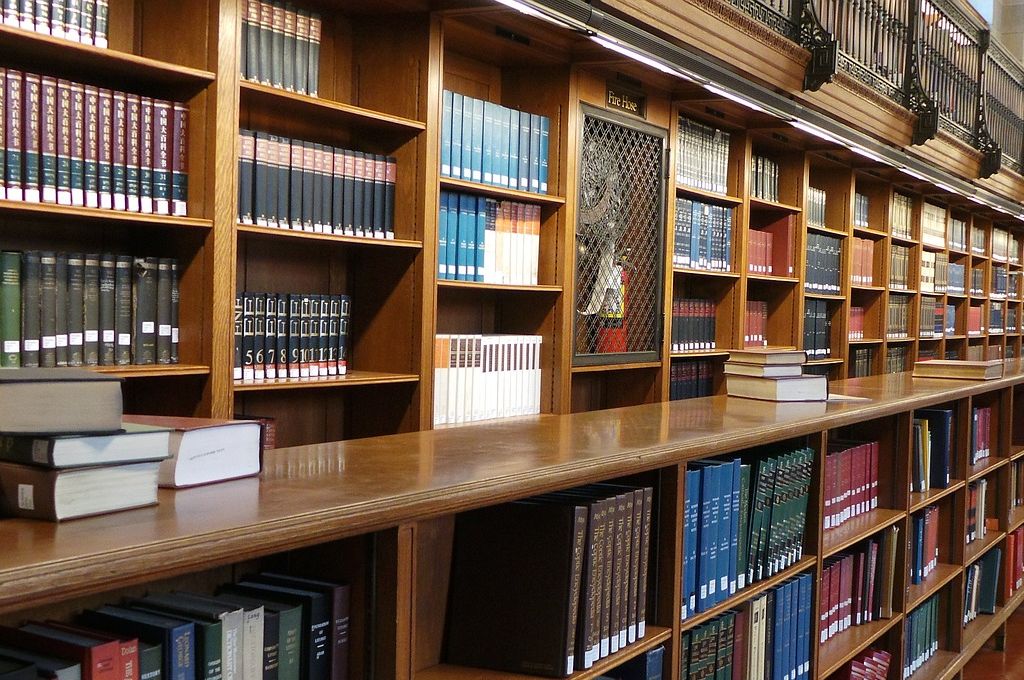
SAWE Paper Database
The SAWE Technical Library contains nearly 4000 technical papers available here for purchase and download. Use the search options below to find what you need.
3709. A Wing Weight Estimation Method Based on Wing-box Beam Design Bai, Lu; Deng, Zhi; Zhang, Xintan; Xia, Ming; Wang, Jianli In: 2020 SAWE Tech Fair, pp. 12, Society of Allied Weight Engineers, Inc., Virtual Conference, 2020. Abstract | Buy/Download | BibTeX | Tags: 11. Weight Engineering - Aircraft Estimation, 23. Weight Engineering - Structural Estimation 3732. Class II & 1/2 Mass Estimation of Light Aircraft Composite Wings Nuño, Miguel; Schröder, K. U. In: 2020 SAWE Tech Fair, pp. 12, Society of Allied Weight Engineers, Inc., Virtual Conference, 2020. Abstract | Buy/Download | BibTeX | Tags: 11. Weight Engineering - Aircraft Estimation, 23. Weight Engineering - Structural Estimation Dorbath, Felix In: 73rd Annual Conference, Long Beach, California, pp. 23, Society of Allied Weight Engineers, Inc., Long Beach, California, 2014. Abstract | Buy/Download | BibTeX | Tags: 10. Weight Engineering - Aircraft Design, 23. Weight Engineering - Structural Estimation Dorbath, Felix; Nagel, Björn; Gollnick, Volker In: 71st Annual Conference, Bad Gögging, Germany, pp. 21, Society of Allied Weight Engineers, Inc., Bad Gögging, Germany, 2012, (Mike Hackney Best Paper Award). Abstract | Buy/Download | BibTeX | Tags: 10. Weight Engineering - Aircraft Design, 23. Weight Engineering - Structural Estimation, Mike Hackney Best Paper Award 3564. Multi-Fidelity Wing Mass Estimations Based On A Central Model Approach Böhnke, Daniel; Dorbath, Felix; Nagel, Björn; Gollnick, Volker In: 71st Annual Conference, Bad Gögging, Germany, pp. 18, Society of Allied Weight Engineers, Inc., Bad Gögging, Germany, 2012. Abstract | Buy/Download | BibTeX | Tags: 11. Weight Engineering - Aircraft Estimation, 23. Weight Engineering - Structural Estimation 3405. A Methodology of Weight Prediction for Joints in Aircraft Design Beilstein, Laura In: 66th Annual Conference, Madrid, Spain, pp. 9, Society of Allied Weight Engineers Society of Allied Weight Engineers, Madrid, Spain, 2007. Abstract | Buy/Download | BibTeX | Tags: 23. Weight Engineering - Structural Estimation 3409. Landing Gear Mass Prediction. A Combined Analytic and Parametric Approach Harrison, Adrian; Smith, Sidney; Kay, Edward; Vekris, Evangelos In: 66th Annual Conference, Madrid, Spain, pp. 20, Society of Allied Weight Engineers Society of Allied Weight Engineers, Madrid, Spain, 2007. Abstract | Buy/Download | BibTeX | Tags: 22. Weight Engineering - Structural Design, 23. Weight Engineering - Structural Estimation 3410. Initial Sizing Optimization of Anisotropic Composite Panels with T-Shape Stiffeners Herencia, J. Enrique; Weaver, Paul; Friswell, Michael In: 66th Annual Conference, Madrid, Spain, pp. 31, Society of Allied Weight Engineers Society of Allied Weight Engineers, Madrid, Spain, 2007. Abstract | Buy/Download | BibTeX | Tags: 10. Weight Engineering - Aircraft Design, 23. Weight Engineering - Structural Estimation 3303. Evolutionary Feature Based Weight Prediction Baker, Anna; Smith, Douglas In: 62nd Annual Conference, New Haven, Connecticut, pp. 23, Society of Allied Weight Engineers, Inc., New Haven, Connecticut, 2003. Abstract | Buy/Download | BibTeX | Tags: 23. Weight Engineering - Structural Estimation 3201. Structural Weight Estimation for Launch Vehicles Cerro, Jeffrey In: 61st Annual Conference, Virginia Beach, Virginia, May 18-22, pp. 19, Society of Allied Weight Engineers, Inc., Virginia Beach, Virginia, 2002. Abstract | Buy/Download | BibTeX | Tags: 23. Weight Engineering - Structural Estimation 2410. Aircraft Structural Mass Property Prediction Using Conceptual-Level Structural Analysis Sexstone, M G In: 57th Annual Conference, Wichita, Kansas, May 18-20, pp. 16, Society of Allied Weight Engineers, Inc., Wichita, Kansas, 1998. Abstract | Buy/Download | BibTeX | Tags: 23. Weight Engineering - Structural Estimation 2421. Analytic Air Induction Weight Analysis Burns, J W In: 57th Annual Conference, Wichita, Kansas, May 18-20, pp. 23, Society of Allied Weight Engineers, Inc., Wichita, Kansas, 1998. Abstract | Buy/Download | BibTeX | Tags: 23. Weight Engineering - Structural Estimation 2406. Advanced Fuselage Weight Estimation for the New Generation of Transport Aircraft Schmidt, A; Lapple, M; Kelm, R In: 56th Annual Conference, Bellevue, Washington, May 19-21, pp. 48, Society of Allied Weight Engineers, Inc., Bellevue, Washington, 1997, (L. R. 'Mike' Hackney Award). Abstract | Buy/Download | BibTeX | Tags: 23. Weight Engineering - Structural Estimation, Mike Hackney Best Paper Award 2407. Aeroelastic Effects on the Weight of an Aircraft in the Pre-Design Phase Kelm, R; Grabietz, M In: 56th Annual Conference, Bellevue, Washington, May 19-21, pp. 20, Society of Allied Weight Engineers, Inc., Bellevue, Washington, 1997. Abstract | Buy/Download | BibTeX | Tags: 23. Weight Engineering - Structural Estimation 2283. Wing Primary Structure Weight Estimation of Transport Aircrafts in the Pre-Development Phase Kelm, R; Lapple, M; Grabietz, M In: 54th Annual Conference, Huntsville, Alabama, May 22-24, pp. 29, Society of Allied Weight Engineers, Inc., Huntsville, Alabama, 1995, (L. R. 'Mike' Hackney Award). Abstract | Buy/Download | BibTeX | Tags: 23. Weight Engineering - Structural Estimation, Mike Hackney Best Paper Award 2287. Application of Mass Cruciforms to Finite Element Models for Inertial Representation Mitchell, P M In: 54th Annual Conference, Huntsville, Alabama, May 22-24, pp. 11, Society of Allied Weight Engineers, Inc., Huntsville, Alabama, 1995. Abstract | Buy/Download | BibTeX | Tags: 23. Weight Engineering - Structural Estimation 2169. Advanced Finite Element Weight Estimation Process on the High Speed Civil Transport Mitchell, P M In: 52nd Annual Conference, Biloxi, Mississippi, May 24-26, pp. 32, Society of Allied Weight Engineers, Inc., Biloxi, Mississippi, 1993. Abstract | Buy/Download | BibTeX | Tags: 23. Weight Engineering - Structural Estimation 2172. Introduction to Stealth Technology and Stealth Aircraft Weight Penalties Burns, J W In: 52nd Annual Conference, Biloxi, Mississippi, May 24-26, pp. 36, Society of Allied Weight Engineers, Inc., Biloxi, Mississippi, 1993, (L. R. 'Mike' Hackney Award). Abstract | Buy/Download | BibTeX | Tags: 23. Weight Engineering - Structural Estimation, Mike Hackney Best Paper Award 2089. Finite Element Model Weight Estimation Droegkamp, M In: 51st Annual Conference, Hartford, Connecticut, May 18-20, pp. 14, Society of Allied Weight Engineers, Inc., Hartford, Connnecticut, 1992. Abstract | Buy/Download | BibTeX | Tags: 23. Weight Engineering - Structural Estimation 2090. Advanced Composites Sizing Guide for Preliminary Weight Estimates Burns, J W In: 51st Annual Conference, Hartford, Connecticut, May 18-20, pp. 37, Society of Allied Weight Engineers, Inc., Hartford, Connnecticut, 1992, (L. R. 'Mike' Hackney Award). Abstract | Buy/Download | BibTeX | Tags: 23. Weight Engineering - Structural Estimation, Mike Hackney Best Paper Award2020
@inproceedings{3709,
title = {3709. A Wing Weight Estimation Method Based on Wing-box Beam Design},
author = {Lu Bai and Zhi Deng and Xintan Zhang and Ming Xia and Jianli Wang},
url = {https://www.sawe.org/product/paper-3709},
year = {2020},
date = {2020-07-01},
urldate = {2020-07-01},
booktitle = {2020 SAWE Tech Fair},
pages = {12},
publisher = {Society of Allied Weight Engineers, Inc.},
address = {Virtual Conference},
abstract = {In this paper, a wing weight estimation method for transport aircraft is presented. By establishing related computational framework, a wing-box model is developed based on wing-box beam design, from where a wing weight estimation method is derived. The key steps of this work include parametric modeling based on structural model simplification, aerodynamic study, finite element method, and aeroelastic analysis. The influence of the mounted pylon has been considered for the wing-box sizing. This method has been validated using data of two different transport aircrafts, which shows that this method is robust and efficient. Outcome of this paper could be rapidly integrated in the conceptual design phase.},
keywords = {11. Weight Engineering - Aircraft Estimation, 23. Weight Engineering - Structural Estimation},
pubstate = {published},
tppubtype = {inproceedings}
}
@inproceedings{3732,
title = {3732. Class II & 1/2 Mass Estimation of Light Aircraft Composite Wings},
author = {Miguel Nuño and K. U. Schröder},
url = {https://www.sawe.org/product/paper-3732},
year = {2020},
date = {2020-07-01},
urldate = {2020-07-01},
booktitle = {2020 SAWE Tech Fair},
pages = {12},
publisher = {Society of Allied Weight Engineers, Inc.},
address = {Virtual Conference},
abstract = {An accurate mass estimation is key to better evaluate aircraft concepts during conceptual and preliminary design. The influence of composite materials on the structural mass estimation of large commercial aircraft has been reviewed on several studies. For light aircraft however, few methods besides applying a fudge factor to scale down masses of an equivalent metallic wing are available. On aircraft concepts deviating from a classical con- figuration statistical methods can not be reliably used for the mass estimation. Therefore Class II & 1/2 and Class III methods, which account for the loading of the structure, are expected to provide a better estimation.In this paper we develop a Class II & 1/2 method to estimate structural masses of composite light aircraft wings. For this, the primary structure of several wings is dimensioned according to static strength criteria. The structure is modeled using a stick beam model. Static aerodynamic loads are calculated using a vortex lattice method. The masses of the dimensioned structures are then compared to the published masses of the considered wings. The comparison is used to calibrate the estimation method and account for sec- ondary structures and miscellaneous items. At last, the deviations between the real masses and the estimated ones using different methods are compared to evaluate the suitability of the developed method.},
keywords = {11. Weight Engineering - Aircraft Estimation, 23. Weight Engineering - Structural Estimation},
pubstate = {published},
tppubtype = {inproceedings}
}
2014
@inproceedings{3615,
title = {3615. Application Of A Flexible Wing Modeling And Physical Mass Estimation System For Early Aircraft Design Stages},
author = {Felix Dorbath},
url = {https://www.sawe.org/product/paper-3615},
year = {2014},
date = {2014-05-01},
booktitle = {73rd Annual Conference, Long Beach, California},
pages = {23},
publisher = {Society of Allied Weight Engineers, Inc.},
address = {Long Beach, California},
abstract = {State-of-the-art models in preliminary wing design apply physics-based methods for primary structures while using empirical correlations for secondary structures. Using those methods, a detailed optimization such as e.g. rear spar positions or flap size is only possible within a limited design space. Novel structural concepts such as multi-spar flap layouts or the introduction of composite materials cannot be analyzed using statistical methods and require extended higher level structural modeling.
Therefore, a flexible wing modeling and physical mass estimation system for early aircraft design stages is developed - the WINGmass system. The core of the interdisciplinary tool chain is a central model generator that automatically generates all analysis models from the DLR aircraft data format CPACS (Common Parametric Aircraft Configuration Scheme). For the automatic model generation, a large amount of engineering rules are implemented in the model generator, to reduce the amount of required input parameters and therefore to relieve the aircraft designer. Besides the multi-model generator, the tool chain consist of a structural finite element model (incl. wing primary structures, flaps, flap tracks, ailerons, engine pylon and landing gear), a structural sizing algorithm and loads models for aerodynamic, fuel, landing gear and engine loads.
The wing mass estimation system is calibrated against real mass values of the wing primary structures and the trailing edge devices of the Airbus A320 and A340-200. The results of the calibrated tool chain are compared to the masses of the primary structures of the B747-100 and the aluminum baseline version of the MD-90-40X. The calibration factors for composite primary structures are derived from the composite version of the MD-90-40X.
Finally, the benefits of the extended physics-based modeling and the application of the WINGmass system in an interdisciplinary aircraft design environment are shown in an aircraft design study. The objective of this study is to compute the optimal wing shape in terms of mission fuel as a function of the take-off field length. Therefore, a parameter variation of the wing and flap geometry is performed, the engine scaled correspondingly and the mission fuel evaluated.},
keywords = {10. Weight Engineering - Aircraft Design, 23. Weight Engineering - Structural Estimation},
pubstate = {published},
tppubtype = {inproceedings}
}
Therefore, a flexible wing modeling and physical mass estimation system for early aircraft design stages is developed - the WINGmass system. The core of the interdisciplinary tool chain is a central model generator that automatically generates all analysis models from the DLR aircraft data format CPACS (Common Parametric Aircraft Configuration Scheme). For the automatic model generation, a large amount of engineering rules are implemented in the model generator, to reduce the amount of required input parameters and therefore to relieve the aircraft designer. Besides the multi-model generator, the tool chain consist of a structural finite element model (incl. wing primary structures, flaps, flap tracks, ailerons, engine pylon and landing gear), a structural sizing algorithm and loads models for aerodynamic, fuel, landing gear and engine loads.
The wing mass estimation system is calibrated against real mass values of the wing primary structures and the trailing edge devices of the Airbus A320 and A340-200. The results of the calibrated tool chain are compared to the masses of the primary structures of the B747-100 and the aluminum baseline version of the MD-90-40X. The calibration factors for composite primary structures are derived from the composite version of the MD-90-40X.
Finally, the benefits of the extended physics-based modeling and the application of the WINGmass system in an interdisciplinary aircraft design environment are shown in an aircraft design study. The objective of this study is to compute the optimal wing shape in terms of mission fuel as a function of the take-off field length. Therefore, a parameter variation of the wing and flap geometry is performed, the engine scaled correspondingly and the mission fuel evaluated.2012
@inproceedings{3547,
title = {3547. Implementation of a Tool Chain for Extended Physics-Based Wing Mass Estimation in Early Design Stages},
author = {Felix Dorbath and Björn Nagel and Volker Gollnick},
url = {https://www.sawe.org/product/paper-3547},
year = {2012},
date = {2012-05-01},
booktitle = {71st Annual Conference, Bad Gögging, Germany},
pages = {21},
publisher = {Society of Allied Weight Engineers, Inc.},
address = {Bad Gögging, Germany},
abstract = {The state-of-the-art methods in preliminary wing design are using models employing physics-based methods for primary structures while using empirical correlations for secondary structures. Using those methods, detailed optimization as e.g. rear spar positions or flap size is only possible within a limited design space. Novel structural concepts such as multi-spar flap layouts or the introduction of composite materials cannot be analyzed using statistical methods and require extended higher level structural modeling. Therefore an interdisciplinary tool chain is developed for extended physics-based wing mass estimation. The tool chain consists of the following components: one central model generator, a structural finite element model, a structural sizing algorithm and loads models for aerodynamic, fuel, landing gear and engine loads. The structural finite element wing model consists of the following main parts: wing box, fixed trailing edge devices, movable trailing edge devices, spoilers, landing gears and engine pylons. The model generator is able to create several different kinds of track kinematics, covering most of the track types used in state-of-the-art aircrafts. To make the complexity of the model generation process feasible for one aircraft designer, a knowledge based approach is chosen. Therefore the central model generator requires a minimum set of easy-to- understand input parameters. This enables the aircraft designer to focus on the design and not on calculating input parameters. To include the tool chain in a wider multidisciplinary aircraft design environment, the aircraft parameterization CPACS (Common Parametric Aircraft Configuration Scheme) is used as central data model for input and output. The developed tool chain is implemented as flexible as possible to enable the designer to analyze also novel structural concepts or wing configurations. On wing configurational level, the tool chain can handle most types of different wing concepts, such as e.g. blended wing bodies, strut-braced wings and box wings. On the structural concepts side, the tool chain is able to handle various different rib and spar layouts and different materials (incl. composites).},
note = {Mike Hackney Best Paper Award},
keywords = {10. Weight Engineering - Aircraft Design, 23. Weight Engineering - Structural Estimation, Mike Hackney Best Paper Award},
pubstate = {published},
tppubtype = {inproceedings}
}
@inproceedings{3564,
title = {3564. Multi-Fidelity Wing Mass Estimations Based On A Central Model Approach},
author = {Daniel Böhnke and Felix Dorbath and Björn Nagel and Volker Gollnick},
url = {https://www.sawe.org/product/paper-3564},
year = {2012},
date = {2012-05-01},
booktitle = {71st Annual Conference, Bad Gögging, Germany},
pages = {18},
publisher = {Society of Allied Weight Engineers, Inc.},
address = {Bad Gögging, Germany},
abstract = {Although computational power is constantly increasing and Moore's Law is still not falsified, computational cost remains an essential barrier in aircraft design especially when a high number of design evaluations is necessary. This is especially true at the conceptual design stage of aircraft. While determining the characteristics of a new configuration the number of iterations and the low level of detail in the available data limit the analyses to simple empiric methods.
Nevertheless, at a later point in the design it is necessary to determine parameters like the wing mass with higher-fidelity analysis modules. Especially when assessing configurations that lie outside of the well-known design space of conceptual design, empiric methods become unreliable. Examples to name include high aspect ratio and forward-swept wings.
In this study a combination of an empiric method, a beam model and vortex lattice model for aerodynamic loads is introduced. While multi-fidelity approaches are already well known, this study focuses on the fact that all analysis modules derive their data from the same data model. Working on a central data model decreases the number of required interfaces and guarantees that all models relate to the same input data, i.e. a compliant geometry definition.
This paper includes a design chain starting from the conceptual design tool VAMPzero as initiator for the more advanced models PESTwing and TRIMvl. Using the PESTwing tool a large design space will be explored. An equation for determination of the wing mass based on a physical model is then derived and compared to existing methods in conceptual design.},
keywords = {11. Weight Engineering - Aircraft Estimation, 23. Weight Engineering - Structural Estimation},
pubstate = {published},
tppubtype = {inproceedings}
}
Nevertheless, at a later point in the design it is necessary to determine parameters like the wing mass with higher-fidelity analysis modules. Especially when assessing configurations that lie outside of the well-known design space of conceptual design, empiric methods become unreliable. Examples to name include high aspect ratio and forward-swept wings.
In this study a combination of an empiric method, a beam model and vortex lattice model for aerodynamic loads is introduced. While multi-fidelity approaches are already well known, this study focuses on the fact that all analysis modules derive their data from the same data model. Working on a central data model decreases the number of required interfaces and guarantees that all models relate to the same input data, i.e. a compliant geometry definition.
This paper includes a design chain starting from the conceptual design tool VAMPzero as initiator for the more advanced models PESTwing and TRIMvl. Using the PESTwing tool a large design space will be explored. An equation for determination of the wing mass based on a physical model is then derived and compared to existing methods in conceptual design.2007
@inproceedings{3405,
title = {3405. A Methodology of Weight Prediction for Joints in Aircraft Design},
author = {Laura Beilstein},
url = {https://www.sawe.org/product/paper-3405},
year = {2007},
date = {2007-05-01},
booktitle = {66th Annual Conference, Madrid, Spain},
pages = {9},
publisher = {Society of Allied Weight Engineers},
address = {Madrid, Spain},
organization = {Society of Allied Weight Engineers},
abstract = {For lightweight construction purposes the ideal structure of an aircraft would be a single unit. Due to various constraints (manufacturing, functionality, profitability, etc.), it is composed of thousands of parts via joints. The additional weight of joints is a major part of the non-optimum weight, which implies effects resulting from the practical design. Since it can reach values of 20 to 80 per cent of the assembly component weight, the importance of developing a methodology of weight prediction for joints is obvious. Research activities are focused on two main issues. The first one concentrates on the generalization of existing design rules from literature. These common rules are mostly given for plain geometries and simple load cases and must be adapted to the much more complex joints in aircraft design. The outcome of this step is a determination of the minimum possible weight for a joining technique (e.g., riveting, welding, adhesive bonding) and is presented for a typical longitudinal fuselage lap joint. The second focus is on the numerous constraints that often make aircraft designers deviate from the minimum possible weight solution. These constraints are due to technical, regulative, or other considerations. They may include such different issues as accessibility of the interfaces, availability of production resources, company experience, manufacturing costs, maintenance requirements, etc. To investigate the influence in a structured manner, a method called ?Analytic Hierarchy Process? (AHP) has been applied. The result of this method is a prediction of the joining technology a designer will probably choose for a given problem. The approach of the AHP is demonstrated for the example of a lap joint using joining technologies like riveting, welding, and adhesive bonding. The alternatives are assessed regarding weight, assembling, maintenance, and costs at top level. The result of both focuses is combined whereas the weight information for the AHP is supplied by the analytic or rather semi-empiric approach of the weight calculation of the different joining technologies.},
keywords = {23. Weight Engineering - Structural Estimation},
pubstate = {published},
tppubtype = {inproceedings}
}
@inproceedings{3409,
title = {3409. Landing Gear Mass Prediction. A Combined Analytic and Parametric Approach},
author = {Adrian Harrison and Sidney Smith and Edward Kay and Evangelos Vekris},
url = {https://www.sawe.org/product/paper-3409},
year = {2007},
date = {2007-05-01},
booktitle = {66th Annual Conference, Madrid, Spain},
pages = {20},
publisher = {Society of Allied Weight Engineers},
address = {Madrid, Spain},
organization = {Society of Allied Weight Engineers},
abstract = {Current parametric methods for landing gear mass prediction are based on relationships derived from existing aircraft and landing gear mass data. They can provide good results using minimal input and effort, although the resulting mass predictions are inherently linked to the design assumptions of legacy aircraft. Also, the methods cannot be used to perform trade studies that would be useful at early stages of the aircraft design process (e.g., landing gear mass vs. shock-absorber stroke, or vs. material choice). Analytic methods attempt to approximate the landing gear design process by calculating loads to size initial structural concepts. They require more detailed data than parametric methods and simplified structures are assumed that can exclude some important details. Also, it is difficult to predict robust values of overall gear weight from an idealized structural weight synthesized by this process. However, analytic methods can be used to perform early trade studies. This paper reviews the progress towards a combined analytic and parametric method that employs the benefits of both approaches. The analysis process starts from a set of data that would typically be available at early stages of the design process and uses an iterative sequence that aims to provide reliable predictions of landing gear mass. The method attempts to simulate the landing gear design process in enough detail to provide an early concept phase mass prediction.},
keywords = {22. Weight Engineering - Structural Design, 23. Weight Engineering - Structural Estimation},
pubstate = {published},
tppubtype = {inproceedings}
}
@inproceedings{3410,
title = {3410. Initial Sizing Optimization of Anisotropic Composite Panels with T-Shape Stiffeners},
author = {J. Enrique Herencia and Paul Weaver and Michael Friswell},
url = {https://www.sawe.org/product/paper-3410},
year = {2007},
date = {2007-05-01},
booktitle = {66th Annual Conference, Madrid, Spain},
pages = {31},
publisher = {Society of Allied Weight Engineers},
address = {Madrid, Spain},
organization = {Society of Allied Weight Engineers},
abstract = {This paper provides an approach to perform initial sizing optimization of anisotropic composite panels with T-shape stiffeners. The method divides the optimization problem into two levels. At the first level, composite optimization is performed using Mathematical Programming (MP), where the skin and the stiffeners are modeled using lamination parameters accounting for their anisotropy. Skin and stiffener laminates are assumed to be symmetric, or mid-plane symmetric laminates with 0, 90, 45, or -45 degree ply angles. The stiffened panel is subjected to a combined loading under strength, buckling, and practical design constraints. Buckling constraints are computed using Closed Form (CF) solutions and energy methods (Rayleigh-Ritz). Conservatism is partially removed in the buckling analysis considering the skin-stiffener flange interaction and decreasing the effective width of the skin. Furthermore, the design and manufacture of the stiffener is embedded within the design variables. At the second level, the actual skin and stiffener lay-ups are obtained using Genetic Algorithms (GAs), accounting for manufacturability and design practices. This two level approach permits the separation of the analysis (strength, buckling, etc), which is performed at the first level, from the laminate stacking sequence combinatorial problem, which is dealt efficiently with GAs at the second level.},
keywords = {10. Weight Engineering - Aircraft Design, 23. Weight Engineering - Structural Estimation},
pubstate = {published},
tppubtype = {inproceedings}
}
2003
@inproceedings{3303,
title = {3303. Evolutionary Feature Based Weight Prediction},
author = {Anna Baker and Douglas Smith},
url = {https://www.sawe.org/product/paper-3303},
year = {2003},
date = {2003-05-01},
booktitle = {62nd Annual Conference, New Haven, Connecticut},
pages = {23},
publisher = {Society of Allied Weight Engineers, Inc.},
address = {New Haven, Connecticut},
abstract = {Many weight prediction methods operate ?analytically,? deriving an ideal structural weight, and then accounting for non-optimum structural penalties using a factoring approach.
This paper presents an alternative weight prediction philosophy that combines elements of traditional mass accounting with estimated sizing data to produce detailed and accurate weights; the component weight is calculated from a set of detailed parameters using a simplified traditional accounting method. These detailed parameters describe the predicted design of the particular component in its entirety, identifying and sizing all features.
The large number of detailed parameters required would normally preclude the use of this method during the early project phases ? where weight prediction is most valuable. However, these detailed parameters can be obtained using their respective driving parameters. A generative design approach allows the prediction of relevant features. Using parametric relationships based upon initial load estimates enables the prediction of detailed sizing.
The result is a versatile method which can be implemented at any stage of a project to generate predicted weights. The resulting weights contain correct causality for ideal structural weight and simultaneously integrate weight resulting from manufacturing constraints and other design considerations.
Other benefits of this method include being able to identify the true weight drivers of a component and ascertain the weight impact of particular design alterations and manufacturing methods.},
keywords = {23. Weight Engineering - Structural Estimation},
pubstate = {published},
tppubtype = {inproceedings}
}
This paper presents an alternative weight prediction philosophy that combines elements of traditional mass accounting with estimated sizing data to produce detailed and accurate weights; the component weight is calculated from a set of detailed parameters using a simplified traditional accounting method. These detailed parameters describe the predicted design of the particular component in its entirety, identifying and sizing all features.
The large number of detailed parameters required would normally preclude the use of this method during the early project phases ? where weight prediction is most valuable. However, these detailed parameters can be obtained using their respective driving parameters. A generative design approach allows the prediction of relevant features. Using parametric relationships based upon initial load estimates enables the prediction of detailed sizing.
The result is a versatile method which can be implemented at any stage of a project to generate predicted weights. The resulting weights contain correct causality for ideal structural weight and simultaneously integrate weight resulting from manufacturing constraints and other design considerations.
Other benefits of this method include being able to identify the true weight drivers of a component and ascertain the weight impact of particular design alterations and manufacturing methods.2002
@inproceedings{3201,
title = {3201. Structural Weight Estimation for Launch Vehicles},
author = {Jeffrey Cerro},
url = {https://www.sawe.org/product/paper-3201},
year = {2002},
date = {2002-05-01},
booktitle = {61st Annual Conference, Virginia Beach, Virginia, May 18-22},
pages = {19},
publisher = {Society of Allied Weight Engineers, Inc.},
address = {Virginia Beach, Virginia},
abstract = {This paper describes a work in progress to develop automated structural weight estimation procedures within the Vehicle Analysis Branch (VAB) of NASA?s Langley Research Center. The VAB performs system studies at the conceptual and early preliminary design stages on launch vehicles and in-space transportation systems. Some examples of these studies for Earth to Orbit (ETO) systems include the Future Space Transportation System, Orbit On Demand Vehicle, Access to Space, and the Personnel Rescue Vehicle. Recently VAB has been asked to assist on a NASA Intercenter Systems Analysis Team (ISAT) to assess Second Generation Reusable Launch Vehicle conceptual designs. To help in this effort finite element based structural analysis tools are being automated and included in a distributed heterogeneous computing environment. This will provide some level of bottoms-up structural weight estimation such that vehicle characteristics and technology improvements effecting performance can be assessed. A challenge to the system being developed is to provide flexibility for differing vehicle configurations and differing structural arrangements of these configurations. A structural component building block approach is proposed and a sample configuration analysis is presented. This approach permits automation of basic FEA entities using utility programs for generic processes such as mass mapping and load case definition. A vehicle configuration is broken into JAVA objects organized in a Work Breakdown Structure (WBS) hierarchy. The JAVA objects work in a commercial computational framework environment to integrate data between the vehicle performance program and the structural analyses required to update that performance calculation. It is hoped that continued development of the system in terms of additional structural component building blocks, additional modeling fidelity, loads definition, and associated JAVA object control of these components will result in an Application Programming Interface (API) that is flexible enough to handle the structural weight assessment needs of a large variety of launch vehicle configurations.},
keywords = {23. Weight Engineering - Structural Estimation},
pubstate = {published},
tppubtype = {inproceedings}
}
1998
@inproceedings{2410,
title = {2410. Aircraft Structural Mass Property Prediction Using Conceptual-Level Structural Analysis},
author = {M G Sexstone},
url = {https://www.sawe.org/product/paper-2410},
year = {1998},
date = {1998-05-01},
booktitle = {57th Annual Conference, Wichita, Kansas, May 18-20},
pages = {16},
publisher = {Society of Allied Weight Engineers, Inc.},
address = {Wichita, Kansas},
abstract = {This paper describes a methodology that extends the use of the Equivalent Laminated Plate Solution (ELAPS) structural analysis code from conceptual-level aircraft structural analysis to conceptual-level aircraft mass property analysis. Mass property analysis in aircraft structures has historically depended upon parametric weight equations at the conceptual design level and Finite Element Analysis (FEA) at the detailed design level. ELAPS allows for the modeling of detailed geometry, metallic and composite materials, and non-structural mass coupled with analytical structural sizing to produce high-fidelity mass property analyses representing fully configured vehicles early in the design process. This capability is especially valuable for unusual configuration and advanced concept development where existing parametric weight equations are not applicable and FEA is too time consuming for conceptual design. This paper contrasts the use of ELAPS relative to empirical weight equations and FEA. ELAPS modeling techniques are described and the ELAPS-based mass properly analysis process is detailed. Examples of mass property stochastic calculations produced during a recent systems study are provided This study involved the analysis of three remotely piloted aircraft required to carry scientific payloads to very high altitudes at subsonic speeds. Due to the extreme nature of this high-altitude flight regime, few existing vehicle designs are available for use in performance and weight prediction. ELAPS was employed within a concurrent engineering analysis process that simultaneously produces aerodynamic, structural, and static aeroelastic results for input to aircraft performance analyses. The ELAPS models produced for each concept were also used to provide stochastic analyses of wing structural mass properties. The results of this effort indicate that ELAPS is an efficient means to conduct multi-disciplinary trade studies at the conceptual design level.},
keywords = {23. Weight Engineering - Structural Estimation},
pubstate = {published},
tppubtype = {inproceedings}
}
@inproceedings{2421,
title = {2421. Analytic Air Induction Weight Analysis},
author = {J W Burns},
url = {https://www.sawe.org/product/paper-2421},
year = {1998},
date = {1998-05-01},
booktitle = {57th Annual Conference, Wichita, Kansas, May 18-20},
pages = {23},
publisher = {Society of Allied Weight Engineers, Inc.},
address = {Wichita, Kansas},
abstract = {During the preliminary design and trade study phases, it is necessary for the Mass Properties engineers to make weight estimates for various air induction concepts and to determine the lightest material system. Analytic Air Induction methods provide a tool that is sensitive to duct shape, size, pressure, and materials. Provisions are included to evaluate metallic, composite laminate, and sandwich including conventional honeycomb and Syncore?. The method includes capability for combinations of rectangular, circular, and D-ducts. The method is a tool for weight estimation and trade study evaluation and is not intended to provide final detail sizing. These estimation methods can also be adapted to doors, panels, and fuel shelves that are primarily designed by normal pressure loads. Capability for combined normal pressure (out-of-plane) and axial (in-plane) loads can be added for other applications.},
keywords = {23. Weight Engineering - Structural Estimation},
pubstate = {published},
tppubtype = {inproceedings}
}
1997
@inproceedings{2406,
title = {2406. Advanced Fuselage Weight Estimation for the New Generation of Transport Aircraft},
author = {A Schmidt and M Lapple and R Kelm},
url = {https://www.sawe.org/product/paper-2406},
year = {1997},
date = {1997-05-01},
booktitle = {56th Annual Conference, Bellevue, Washington, May 19-21},
pages = {48},
publisher = {Society of Allied Weight Engineers, Inc.},
address = {Bellevue, Washington},
abstract = {The airlines are forced to use efficient aircraft due to the hard competition in air traffic. Changes in the airline network, the limited number of slots and the growing rates of passenger and freight require aircraft with high transport performance. This leads to aircraft configurations with high passenger and freight capacities. The fuselage geometry for these types of aircraft can diverge from the conventional design. Also the ongoing studies for the second generation of supersonic aircraft show fuselage designs and physical effects of a new quality. Weight estimations for the resulting new fuselage shapes (e.g. double deck or area ruled configurations) are still a challenging task. Accurate weight prognosis without powerful software tools is becoming an almost hopeless goal. A precise and reliable fuselage weight estimation tool is basis for the assessment of the viability of a new aircraft and has therefore a direct influence on the project. Since the knowledge about the design in the pre-development phase is very limited the software has to include multidisciplinary interactions between loads, structure, and materials. This paper details the process of the fuselage weight estimation method used in the weights prognosis department at Daimler-Benz Aerospace Airbus. Based on simple input data the software creates a numeric 3-D model of the exposed fuselage surface. The position and size of cutouts can be defined by the program user. In the loads module the introduction of external forces and the calculation of internal loads (due to mass distributions of pay-load, systems and structure) are considered. Certification rules, manufacturing procedures, material/structural fatigue and flight/mission envelopes are taken into account. The structure weight calculation is based on classical theories for strength and stability. For the inclusion of the elastic behavior of the fuselage the structural deformation is calculated by the software. The software tool FAME-F (Fast and Advanced Mass Estimation of Fuselage) is described with emphasis on the multidisciplinary character of the computer approach. This approach allows for fast parametric studies and determination of sensitivities. The development of the software tool FAME-F shows how weight engineering can contribute to the essential reduction of aircraft developing time and costs.},
note = {L. R. 'Mike' Hackney Award},
keywords = {23. Weight Engineering - Structural Estimation, Mike Hackney Best Paper Award},
pubstate = {published},
tppubtype = {inproceedings}
}
@inproceedings{2407,
title = {2407. Aeroelastic Effects on the Weight of an Aircraft in the Pre-Design Phase},
author = {R Kelm and M Grabietz},
url = {https://www.sawe.org/product/paper-2407},
year = {1997},
date = {1997-05-01},
booktitle = {56th Annual Conference, Bellevue, Washington, May 19-21},
pages = {20},
publisher = {Society of Allied Weight Engineers, Inc.},
address = {Bellevue, Washington},
abstract = {In the pre-development phase of a new aircraft naturally the knowledge about the design is very limited. The inclusion of aeroelastic effects is therefore an ambitious task since specific data (e. g. stiffness or mass distributions) must be available. This paper describes the method and process for the calculation of aeroelastic effects on the weight of an aircraft. Here not only the primary influence on the structural weight is important. It has to be recognized also that aeroelastic effects on the aerodynamic efficiency influence the fuel consumption. This leads to a change of the maximum take off weight (MTOW) of the aircraft and has therefore a snowball effect on the structural weight since a change of the MTOW influences the dimensioning loads. A method appropriate for the inclusion of aeroelastic effects at the very beginning of a new aircraft project is presented. Even if only a simple three-sided view with a proper definition of the wing geometry is available first calculations can be performed. The software-tool FAME-W which is used in the future projects office at Daimler-Benz Aerospace AIRBUS in Hamburg is detailed with emphasis on the multidisciplinary character of the computational approach. The results show the effects of aeroelasticity particularly on the wing and tailplane weight. A procedure for the calculation of the stiffness and mass distribution is presented. Here the influence of geometric parameters like sweep angle or aspect ratio is identified. The effectiveness of a maneuver load control system including all relevant flexibility effects for a trimmed aircraft is shown. The redistribution of the lift and pitching moment and the effect on the lift to drag (L/D) ratio during a flight mission is pointed out. A precise calculation of the L/D ratio of a new aircraft is the basis for the assessment of its viability. Together with these results the paper demonstrates the strong influence of aeroelasticity in the pre-design phase beginning with minimum information and finishing with detailed knowledge about the new aircraft. The combination of classical weight estimation approaches with numerical aerodynamics and structural mechanics into one software-tool shows that weight engineering is more important than ever and still a challenging endeavor.},
keywords = {23. Weight Engineering - Structural Estimation},
pubstate = {published},
tppubtype = {inproceedings}
}
1995
@inproceedings{2283,
title = {2283. Wing Primary Structure Weight Estimation of Transport Aircrafts in the Pre-Development Phase},
author = {R Kelm and M Lapple and M Grabietz},
url = {https://www.sawe.org/product/paper-2283},
year = {1995},
date = {1995-05-01},
booktitle = {54th Annual Conference, Huntsville, Alabama, May 22-24},
pages = {29},
publisher = {Society of Allied Weight Engineers, Inc.},
address = {Huntsville, Alabama},
abstract = {Accurate weight prognosis without powerful software tools is becoming an almost hopeless task. In the pre-development phase of modern transport aircraft the geometry is not fixed and many parameter studies have to be performed. The wing of the plane has to be optimized to minimize the operating costs. The wing weight is directly influenced by geometrical changes and the materials used. A precise and reliable wing weight prognosis method is the basis for the assessment of the viability of a plane. This paper details the process of the wing weight estimation method used in the weights prognosis department at Daimler-Benz Aerospace Airbus. The software tool FAME-W (Fast and Advanced Mass Estimation of Wings) is described with emphasis on the multidisciplinary character of the computer approach. In the pre-development phase of an aircraft only limited knowledge of the design is available. For a qualified wing weight estimation the dimensioning loadcases, the structural layout, and other essential information must be quantified. In order to establish a precise loads calculation the mass and stiffness distribution of the wing is necessary. The most promising way for a time and cost effective solution of this iterative problem is an integration of all relevant technical disciplines in one software-tool requiring only minimum data for input. During its mission a plane is exposed to changing flight conditions. For example, due to fuel consumption the weight of the plane is not constant, in the climb, cruise, and the descent phase of one flight different gust loads must be considered at each altitude. To consider the resulting large number of independent load cases in an acceptable time an analytical/numerical algorithm based on the the classical theory of multicellular shells, beam and structural instability theory extended by the calculation of special effects like differential bending was chosen. The aerodynamics are taken into account by an integrated software module. A module for the calculation of the structural deformation allows the dimensioning of the elastic structure including the re-calculation of the aerodynamic loads. This paper describes the method and process for wing primary structure weight estimation of transport aircraft in the pre-development phase.},
note = {L. R. 'Mike' Hackney Award},
keywords = {23. Weight Engineering - Structural Estimation, Mike Hackney Best Paper Award},
pubstate = {published},
tppubtype = {inproceedings}
}
@inproceedings{2287,
title = {2287. Application of Mass Cruciforms to Finite Element Models for Inertial Representation},
author = {P M Mitchell},
url = {https://www.sawe.org/product/paper-2287},
year = {1995},
date = {1995-05-01},
booktitle = {54th Annual Conference, Huntsville, Alabama, May 22-24},
pages = {11},
publisher = {Society of Allied Weight Engineers, Inc.},
address = {Huntsville, Alabama},
abstract = {A method for generating mass cruciforms for use in finite element structural models is introduced. A review of the mathematics necessary to create mass cruciforms is given. A discussion of the potential applicability of mass cruciforms is given which emphasizes its use to model propulsion systems. This is demonstrated by the use of mass cruciforms on the Boeing High Speed Civil Transport finite element model. The decision to use mass cruciforms to represent inertial properties of a structural component is influenced by several factors. These include availability of mass and inertia data during the initial preliminary design stage. Additionally, they include desired finite element model discretization and software requirements and limitations. These topics as well as those relating to dynamic loads and flutter analyses will be discussed.},
keywords = {23. Weight Engineering - Structural Estimation},
pubstate = {published},
tppubtype = {inproceedings}
}
1993
@inproceedings{2169,
title = {2169. Advanced Finite Element Weight Estimation Process on the High Speed Civil Transport},
author = {P M Mitchell},
url = {https://www.sawe.org/product/paper-2169},
year = {1993},
date = {1993-05-01},
booktitle = {52nd Annual Conference, Biloxi, Mississippi, May 24-26},
pages = {32},
publisher = {Society of Allied Weight Engineers, Inc.},
address = {Biloxi, Mississippi},
abstract = {Finite element analysis is a useful tool for airplane preliminary design and configuration analysis. Analyzing a finite element model which represents a complete aircraft configuration requires the participation of many engineering disciplines. Among these are aerodynamics, stress, design, configurations, loads, flutter, and weights. The Boeing weight engineering organization has developed a set of advanced tools for analysis of finite element mass properties. A process which integrated these tools into a multi-disciplinary finite element analysis environment was created and is being used on the High Speed Civil Transport (HSCT). This paper details the process used and briefly describes the computing tools and environment used in the finite element weight analysis. Emphasis is placed on one portion of the process, specifically, the weight estimation of primary structure which is undergoing optimization with finite element analysis. The Algorithmic Mass Factoring Method (AM-FM) is an advanced software tool which allows weight estimation of primary structure which is based on design requirements, material allowables, and manufacturing practices. Furthermore, this tool provides visibility for weight changes to the finite element model as a result of structural optimization cycling. The modeling and analysis process used on the HSCT was based on strong inter-disciplinary cooperation. The process required the weights group to be active in virtually every aspect of the team effort, from model definition to trade study completion. The tools and processes detailed in this paper represent the state of the art for finite element mass properties analysis for weight engineering at Boeing.},
keywords = {23. Weight Engineering - Structural Estimation},
pubstate = {published},
tppubtype = {inproceedings}
}
@inproceedings{2172,
title = {2172. Introduction to Stealth Technology and Stealth Aircraft Weight Penalties},
author = {J W Burns},
url = {https://www.sawe.org/product/paper-2172},
year = {1993},
date = {1993-05-01},
booktitle = {52nd Annual Conference, Biloxi, Mississippi, May 24-26},
pages = {36},
publisher = {Society of Allied Weight Engineers, Inc.},
address = {Biloxi, Mississippi},
abstract = {During the preliminary design and proposal phases for some of the modern military aircraft and missile programs, it is desirable, and often necessary, for the mass properties engineer to make preliminary weight estimates for low observable materials and penalties. The purpose of this paper is to present a brief history of the origins of low observables, an introduction to radar technology, Radar Cross Section (RCS), low observable materials, RCS reduction techniques, and weight estimation methodology for some of the stealth enhancing treatments that will aid mass properties engineers inexperienced with stealth technology. Infrared (IR) signature, acoustical, and exhaust emission signature reduction techniques are beyond the scope of this paper.},
note = {L. R. 'Mike' Hackney Award},
keywords = {23. Weight Engineering - Structural Estimation, Mike Hackney Best Paper Award},
pubstate = {published},
tppubtype = {inproceedings}
}
1992
@inproceedings{2089,
title = {2089. Finite Element Model Weight Estimation},
author = {M Droegkamp},
url = {https://www.sawe.org/product/paper-2089},
year = {1992},
date = {1992-05-01},
booktitle = {51st Annual Conference, Hartford, Connecticut, May 18-20},
pages = {14},
publisher = {Society of Allied Weight Engineers, Inc.},
address = {Hartford, Connnecticut},
abstract = {Weight is a primary criterion of aircraft performance and is frequently used as the basis for estimating aircraft cost. Weight and cost of future aircraft will be influenced by changes in design requirements and by new technologies incorporated to meet the goals set by our customers. To control and optimize the weight of aircraft structure and reduce cost, estimation procedures must be developed to reflect the weight effects of new materials and innovative configurations. This requires that weight estimation be performed at greater levels of detail than conventional weight estimation methods. The finite element model (FEM) is well suited for such detailed studies. This paper presents the technology MCAIR is developing to estimate weight from the structural FEM and distribute both structural and non-structural weight back into the FEM. Ibis technology is providing the capability to estimate and control the weight of detail parts such as individual spars, ribs, and skins. FEM weight estimates also reflect the weight impact of configuration details included in the model such as spar spacing, material properties, and construction techniques. The weight estimate can be distributed back into the FEM so that inertial loads, mode shapes, natural frequencies, flutter, and divergence speed can be calculated more accurately.},
keywords = {23. Weight Engineering - Structural Estimation},
pubstate = {published},
tppubtype = {inproceedings}
}
@inproceedings{2090,
title = {2090. Advanced Composites Sizing Guide for Preliminary Weight Estimates},
author = {J W Burns},
url = {https://www.sawe.org/product/paper-2090},
year = {1992},
date = {1992-05-01},
booktitle = {51st Annual Conference, Hartford, Connecticut, May 18-20},
pages = {37},
publisher = {Society of Allied Weight Engineers, Inc.},
address = {Hartford, Connnecticut},
abstract = {During the preliminary design and proposal phases, it is necessary for the mass properties engineer to make weight estimates that require preliminary rough estimates to improve or verify Level I and Level II estimates and to support trade studies for various types of construction, materials substitution, wing t/c, and design criteria changes. The purpose of this paper is to provide a simple and easy to understand, preliminary sizing guide and present some numeric examples that will aid the mass properties engineer that is inexperienced with advanced composites analysis.},
note = {L. R. 'Mike' Hackney Award},
keywords = {23. Weight Engineering - Structural Estimation, Mike Hackney Best Paper Award},
pubstate = {published},
tppubtype = {inproceedings}
}