SAWE Technical Papers
Technical Library
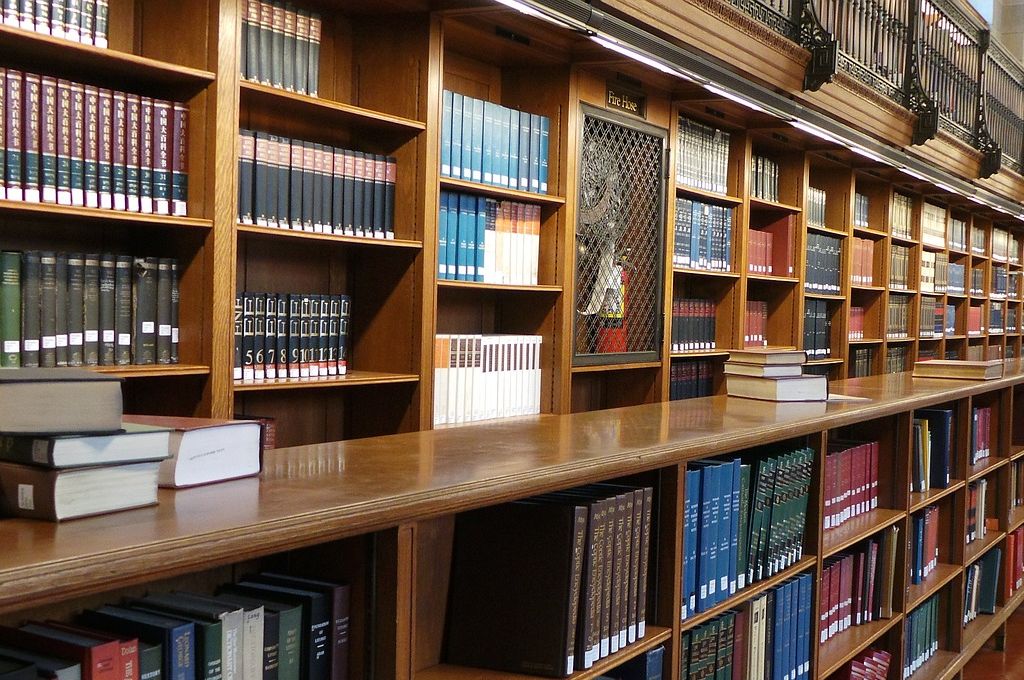
SAWE Paper Database
The SAWE Technical Library contains nearly 4000 technical papers available here for purchase and download. Use the search options below to find what you need.
3760. Design for Positive Static Margin for a Radio-Controlled Box-Wing Aircraft Bellerjeau, Charlotte In: 2020 SAWE Tech Fair, pp. 12, Society of Allied Weight Engineers, Inc., Virtual Conference, 2020. Abstract | Buy/Download | BibTeX | Tags: 10. Weight Engineering - Aircraft Design, 34. Advanced Design, Student Papers 3735. Weight and Balance Challenges for Hybrid Electric Propulsion System Paula, Vera; Vogel, Dr. Florian In: 2020 SAWE Tech Fair, pp. 16, Society of Allied Weight Engineers, Inc., Virtual Conference, 2020. Abstract | Buy/Download | BibTeX | Tags: 11. Weight Engineering - Aircraft Estimation, 34. Advanced Design 3736. Hydrogen Fuel Cell Power System Weight Challenges in VTOL Aircraft Ray, Greg; Rainville, Joseph D. In: 2020 SAWE Tech Fair, pp. 16, Society of Allied Weight Engineers, Inc., Virtual Conference, 2020. Abstract | Buy/Download | BibTeX | Tags: 11. Weight Engineering - Aircraft Estimation, 34. Advanced Design 3726. Toolchain Integration For Space Habitat Design DeVoe, Maxwell; Tokarz, Ariel; Park, Samuel In: 78th Annual Conference, Norfolk, VA, pp. 11, Society of Allied Weight Engineers, Inc., Norfolk, Virginia, 2019. Abstract | Buy/Download | BibTeX | Tags: 12. Weight Engineering - Computer Applications, 34. Advanced Design Klim, Graeme; Hashemi, Dr. Seyed M. In: 76th Annual Conference, Montreal, Canada, pp. 25, Society of Allied Weight Engineers, Inc., Montreal, Canada, 2017. Abstract | Buy/Download | BibTeX | Tags: 22. Weight Engineering - Structural Design, 34. Advanced Design, Student Papers 3692. Aircraft Systems Physics-Based Weight Estimation Methods for Conceptual Design Tfaily, Ali; Liscouët-Hanke, Dr. Susan In: 76th Annual Conference, Montreal, Canada, pp. 12, Society of Allied Weight Engineers, Inc., Montreal, Canada, 2017. Abstract | Buy/Download | BibTeX | Tags: 11. Weight Engineering - Aircraft Estimation, 25. Weight Engineering - System Estimation, 34. Advanced Design 3655. Weight and Structural Optimization in Aircraft Design Alves, William; Silva, Juliana In: 75th Annual Conference, Denver, Colorado, pp. 30, Society of Allied Weight Engineers, Inc., Denver, Colorado, 2016. Abstract | Buy/Download | BibTeX | Tags: 10. Weight Engineering - Aircraft Design, 22. Weight Engineering - Structural Design, 28. Weight Reduction - Processes, 34. Advanced Design 3670. Soil Moisture Active Passive Mission Mass Properties Optimization and Analysis IV, Morgan Hendry; Slimko, Erich In: 75th Annual Conference, Denver, Colorado, pp. 22, Society of Allied Weight Engineers, Inc., Denver, Colorado, 2016. Abstract | Buy/Download | BibTeX | Tags: 18. Weight Engineering - Spacecraft Design, 34. Advanced Design Reinartz, Roland In: 66th Annual Conference, Madrid, Spain, pp. 14, Society of Allied Weight Engineers Society of Allied Weight Engineers, Madrid, Spain, 2007. Abstract | Buy/Download | BibTeX | Tags: 24. Weight Engineering - System Design, 34. Advanced Design 3422. Weight Prediction of UAV Structures and Subsystems Using Parametric Design Methods Zimmerman, Mario In: 66th Annual Conference, Madrid, Spain, pp. 25, Society of Allied Weight Engineers Society of Allied Weight Engineers, Madrid, Spain, 2007. Abstract | Buy/Download | BibTeX | Tags: 33. Unmanned Vehicles, 34. Advanced Design2020
@inproceedings{3760,
title = {3760. Design for Positive Static Margin for a Radio-Controlled Box-Wing Aircraft},
author = {Charlotte Bellerjeau},
url = {https://www.sawe.org/product/paper-3760},
year = {2020},
date = {2020-07-01},
booktitle = {2020 SAWE Tech Fair},
pages = {12},
publisher = {Society of Allied Weight Engineers, Inc.},
address = {Virtual Conference},
abstract = {This paper will detail the aerodynamic design of a small unmanned box-wing aircraft to facilitate the study of turbulence by Dr. Brian Argrow at the CU Boulder. A design with no fuselage was necessary for the data collection, which presented a longitudinal stability challenge. The key to eventually achieving a stable design was weight placement for positive static margin. This paper will include the design process used to confront these issues. The initial choices of stagger, gap, decalage, and relative sweep are made using a simple model leveraging previous box-wing research. These, as well as the airfoil selection, are then investigated further using Athena Vortex Lattice (AVL) to analyze lift, drag, and stability. The final airframe design has a gap and stagger of 1 chord length, decalage of 5 degrees, and relative sweep of 30 degrees. A cambered NACA 6412 airfoil on the top wing and a reflexed NACA23112 airfoil on the bottom wing are selected, which combine to induce a positive pitching moment and aid in longitudinal stability. The resulting box-wing aircraft was flight tested successfully and will serve as an ideal platform for research at CU Boulder.},
keywords = {10. Weight Engineering - Aircraft Design, 34. Advanced Design, Student Papers},
pubstate = {published},
tppubtype = {inproceedings}
}
@inproceedings{3735,
title = {3735. Weight and Balance Challenges for Hybrid Electric Propulsion System},
author = {Vera Paula and Dr. Florian Vogel},
url = {https://www.sawe.org/product/paper-3735},
year = {2020},
date = {2020-07-01},
urldate = {2020-07-01},
booktitle = {2020 SAWE Tech Fair},
pages = {16},
publisher = {Society of Allied Weight Engineers, Inc.},
address = {Virtual Conference},
abstract = {In the last years electric propulsion systems became increasingly interesting and thanks to many of the technological breakthroughs from automotive companies this technological change is now entering the aviation industry and raises questions about the feasibility, advantages and challenges of the new technologies. In this context, the HEPS weight receives a special attention. The HEPS takes advantage of both electric motor and internal combustion engine and enables the system to be switched on the electrical component of the propulsion for specific flight phases (takeoff and landing).This proposed system has not only the benefit in fuel saving but also a reduction in takeoff noise, emission levels and cost. It also enables to open spaces and can contribute for safety increase, depending on application. This potential benefits are explored by manufacturers for future aircrafts, helicopters, drones and Urban Air Mobility vehicles.In that way, the main objective of this paper is to discuss and analyze HEPS architectures, considering the electric propulsion unit (e-motor and inverter), electric transmission (electrical protections and harness), electric energy source (battery/ fuel cell system and genset power generation) and thermal management (cooling system) from a weight and balance perspective. The aim is basically to answer the questions: which are the main relevant subsystems and components contributing for the weight of the HEPS and which are the challenges associated to it? In order to reach this goal a synthesis of bibliographic review is presented and a description research is proposed for a system with an aircraft application. The outcome of this work is a weight and balance perspective assessment of HEPS subsystem, which contributes to the understanding of this new technology and learning objectives for future aircraft design.},
keywords = {11. Weight Engineering - Aircraft Estimation, 34. Advanced Design},
pubstate = {published},
tppubtype = {inproceedings}
}
@inproceedings{3736,
title = {3736. Hydrogen Fuel Cell Power System Weight Challenges in VTOL Aircraft},
author = {Greg Ray and Joseph D. Rainville},
url = {https://www.sawe.org/product/paper-3736},
year = {2020},
date = {2020-07-01},
booktitle = {2020 SAWE Tech Fair},
pages = {16},
publisher = {Society of Allied Weight Engineers, Inc.},
address = {Virtual Conference},
abstract = {The 'More Electric Aircraft' movement is maturing past actuation, flight controls and backup power solutions. Starting with Unmanned Aerial Vehicles (UAV) and now growing into the passenger vehicle market, vertical lift aircraft engineers are developing electric driven propulsion systems.One of major limitations with electrification is endurance or range. Batteries only offer so much energy capacity before mass becomes a limiting factor. Hydrogen fuel cells offer another solution for on board electrical generation but present many of their own technical challenges.In cases of typical passenger vertical lift aircraft, electrification supplants traditional gas turbines and liquid fuel tanks with electric motors, power electronics, and either batteries or hydrogen fuel cells for an energy source. For Class I UAVs (55 lbs. total weight) or Class II UAVs (up to 300 lbs. total weight), batteries could be replaced by smaller, simplified fuel cells, electronics and hydrogen storage.The electric powertrain evolution will have a strong impact on several aspects of aircraft technology development, especially mass properties and center of gravity as the emerging technology is not limited to time honored positions and locations of legacy components. This paper researches some of the risks and opportunities with electrifying the propulsion systems of vertical lift aircraft.},
keywords = {11. Weight Engineering - Aircraft Estimation, 34. Advanced Design},
pubstate = {published},
tppubtype = {inproceedings}
}
2019
@inproceedings{3726,
title = {3726. Toolchain Integration For Space Habitat Design},
author = {Maxwell DeVoe and Ariel Tokarz and Samuel Park},
url = {https://www.sawe.org/product/paper-3726},
year = {2019},
date = {2019-05-01},
booktitle = {78th Annual Conference, Norfolk, VA},
pages = {11},
publisher = {Society of Allied Weight Engineers, Inc.},
address = {Norfolk, Virginia},
abstract = {Space habitat design is an iterative process that requires multiple revisions before a final product can be ascertained. Completing a project can prove cumbersome and time consuming, thus straining an organization's resources. To counteract this issue, there was a desire to automate steps within the design process to improve the efficacy of the iterative aspect while also decreasing time spent developing designs. This paper will detail the main processes that were automated within the NASA LaRC Vehicle Analysis Branch environment. Examine is a custom Microsoft Excel-based spreadsheet that was used to consolidate parameter calculations within an encapsulated environment. IDEA is a model based systems engineering software that enables fast and efficient modifications to a CAD model, allowing for greater flexibility in the design process. To improve efficiency, the two design tools were linked to ensure fast and user-friendly data flow between them. The tools are controlled within a SysML application, consolidating the linkage into one interface for the user. This paper will detail the process of linking the tools together as well as the processes being executed within the individual tools themselves.},
keywords = {12. Weight Engineering - Computer Applications, 34. Advanced Design},
pubstate = {published},
tppubtype = {inproceedings}
}
2017
@inproceedings{3680,
title = {3680. Designing Mass-Optimized Parts Using Solidthinking Inspire with Application to the Hyperloop Deployable Wheel System},
author = {Graeme Klim and Dr. Seyed M. Hashemi},
url = {https://www.sawe.org/product/paper-3680},
year = {2017},
date = {2017-05-01},
booktitle = {76th Annual Conference, Montreal, Canada},
pages = {25},
publisher = {Society of Allied Weight Engineers, Inc.},
address = {Montreal, Canada},
abstract = {Today's automotive and aerospace engineers are often faced with conflicting design goals; design for low cost or low weight. While advancements in aerospace materials, such as carbon fiber composites, have allowed engineers to design lighter parts, the cost to manufacture these parts is still very high. Similarly, recent advancements in additive manufacturing demonstrate an ability to produce lightweight, stiff structures, with a promise of future economic benefits including fuel savings, a result of optimized production part design. To realize additive manufacturing's benefits as they pertain to weight savings, design engineers must re-examine their approach to part and product design. This well-known challenge to improve the state of current design methods is being addressed through a 'design for additive manufacturing' movement that remains an ongoing subject of interest in the additive manufacturing and design communities. The present paper demonstrates the use of the industrial software tool, solidThinking Inspire, as a preliminary study and detail design weight reduction tool for additive manufacturing. To illustrate the software's usefulness, a primary structural component of the Hyperloop Deployable Wheel System, developed at Ryerson University, was selected for optimization, and designed for additive metal manufacturing production. The significant weight savings and material savings realized are presented while the potential for fast design, development and production of the part are highlighted in a step-by-step process.},
keywords = {22. Weight Engineering - Structural Design, 34. Advanced Design, Student Papers},
pubstate = {published},
tppubtype = {inproceedings}
}
@inproceedings{3692,
title = {3692. Aircraft Systems Physics-Based Weight Estimation Methods for Conceptual Design},
author = {Ali Tfaily and Dr. Susan Liscouët-Hanke},
url = {https://www.sawe.org/product/paper-3692},
year = {2017},
date = {2017-05-01},
booktitle = {76th Annual Conference, Montreal, Canada},
pages = {12},
publisher = {Society of Allied Weight Engineers, Inc.},
address = {Montreal, Canada},
abstract = {During the conceptual design phase of an aircraft, details regarding aircraft systems such as the detailed architecture and parts lists are not available. However, weight estimates for aircraft systems are needed very early for aircraft design and performance calculation. Several methods exist to predict system weights and most of these methods are empirical models correlated to top level aircraft parameters such as take- off weight, wingspan, etc. Even if the empirical methods have been sufficiently accurate in the past, they are not suitable for a more sophisticated multidisciplinary design optimization (MDO) approach implemented today in Bombardier's Advanced Design group. In addition, the empirical methods are not valid to predict the effect of new technologies. So called 'physics-based methods' are proposed, leading to a better understanding of technology and system architecture choice impact on the aircraft weight.The new weight estimation methods are implemented as integral part of a conceptual aircraft systems sizing framework. This framework enables the development of more mature aircraft concepts without comprising the calculation runtime. The proposed physics based models showed minimal errors when compared to actual data while capturing additional sensitivities that did not exist in previous methodologies. This paper illustrates the methodology for the example of the hydraulic power system.},
keywords = {11. Weight Engineering - Aircraft Estimation, 25. Weight Engineering - System Estimation, 34. Advanced Design},
pubstate = {published},
tppubtype = {inproceedings}
}
2016
@inproceedings{3655,
title = {3655. Weight and Structural Optimization in Aircraft Design},
author = {William Alves and Juliana Silva},
url = {https://www.sawe.org/product/paper-3655},
year = {2016},
date = {2016-05-01},
booktitle = {75th Annual Conference, Denver, Colorado},
pages = {30},
publisher = {Society of Allied Weight Engineers, Inc.},
address = {Denver, Colorado},
abstract = {Given the competitiveness of the current market, there is a growing movement in the sense of increase the efficiency of aeronautical product in an appropriate life cycle for airliners needs.
In the context of aeronautical structures, the challenge is to increase structural efficiency within the number of cycles required for life in service, meeting reliability requirements and loads, without losing sight of the dynamic performance of structural components.
This article is intended to present the main structural optimization techniques and estimating the gains made at various stages of development of the aircraft design.},
keywords = {10. Weight Engineering - Aircraft Design, 22. Weight Engineering - Structural Design, 28. Weight Reduction - Processes, 34. Advanced Design},
pubstate = {published},
tppubtype = {inproceedings}
}
In the context of aeronautical structures, the challenge is to increase structural efficiency within the number of cycles required for life in service, meeting reliability requirements and loads, without losing sight of the dynamic performance of structural components.
This article is intended to present the main structural optimization techniques and estimating the gains made at various stages of development of the aircraft design.@inproceedings{3670,
title = {3670. Soil Moisture Active Passive Mission Mass Properties Optimization and Analysis},
author = {Morgan Hendry IV and Erich Slimko},
url = {https://www.sawe.org/product/paper-3670},
year = {2016},
date = {2016-05-01},
booktitle = {75th Annual Conference, Denver, Colorado},
pages = {22},
publisher = {Society of Allied Weight Engineers, Inc.},
address = {Denver, Colorado},
abstract = {The Soil Moisture Active Passive (SMAP) mission creates global soil moisture measurements every 2-3 days by spinning a lightweight, ~6 meter diameter deployable mesh reflector. This represents the largest spinning antenna ever to be used on a NASA satellite. The paper discusses the mass properties challenges that were overcome in implementing the mission, including the definition of a combined imbalance term called the Effective Product of Inertia, the selection of an optimum Spun Instrument focal length and edge offset that fostered a reduced mass properties sensitivity, the inclusion of late game Spun Instrument configuration flexibility, the use of balance mass locations that leveraged the large moment arm provided by the reflector, and a subassembly measurement campaign that reduced mass properties uncertainties on testable components.},
keywords = {18. Weight Engineering - Spacecraft Design, 34. Advanced Design},
pubstate = {published},
tppubtype = {inproceedings}
}
2007
@inproceedings{3419,
title = {3419. Effect of Unstable Modern Fighter Aircraft Design on Mass Control (An example of the Eurofighter aircraft)},
author = {Roland Reinartz},
url = {https://www.sawe.org/product/paper-3419},
year = {2007},
date = {2007-05-01},
booktitle = {66th Annual Conference, Madrid, Spain},
pages = {14},
publisher = {Society of Allied Weight Engineers},
address = {Madrid, Spain},
organization = {Society of Allied Weight Engineers},
abstract = {The Mass Property Engineer's role in the classical aircraft design process is to provide reliable mass property information to the engineering organization in order to enable the optimization of the aircraft layout and performance. In the course of the design process, the role of Mass Properties Engineers is normally focused on weight control, reducing the weight growth occurring during product realization. Unstable modern fighter aircraft require mass data for their computerized flight control system. As a consequence of this requirement, the mass engineer's field of activity is extended to monitor the aircraft mass also during the in-service operation. This paper will describe what data is required by the flight control system, how these data are generated, and the implications of this on the weights engineers' community using the example of the aerodynamically highly unstable Eurofighter. It will also identify the parameters, which ultimately determine the accuracy of the required data. It is concluded that the resulting mass data generation process is a compromise between the requirements of aircraft performance, in-service operation, and the associated costs.},
keywords = {24. Weight Engineering - System Design, 34. Advanced Design},
pubstate = {published},
tppubtype = {inproceedings}
}
@inproceedings{3422,
title = {3422. Weight Prediction of UAV Structures and Subsystems Using Parametric Design Methods},
author = {Mario Zimmerman},
url = {https://www.sawe.org/product/paper-3422},
year = {2007},
date = {2007-05-01},
booktitle = {66th Annual Conference, Madrid, Spain},
pages = {25},
publisher = {Society of Allied Weight Engineers},
address = {Madrid, Spain},
organization = {Society of Allied Weight Engineers},
abstract = {For larger UAVs with more than 500 kg MTOM, technologies and assembly methods similar to man-carrying systems are used. These allow the use of known preliminary design methods according to Raymer, Roskam, or Stinton. In the case of smaller vehicles, the use of empiric equations made for man-carrying systems, most of the time, cause significant errors due to unscale-effects. Among other effects, this is based on a smaller decrease in size of connecting elements when decreasing overall part dimensions. Bonds of ribs with the outer skin can make up to 50% of the mass at small sizes. At reduced dimensions, breakouts for mass reduction cannot be made, which causes an unproportional mass increase of small parts. Since these problems appear in a similar way in nearly all parts of a UAV structure, a calculation using equations based on statistics for larger structures is no longer applicable. In order to accomplish a reasonable preliminary design of small UAV systems, the possibility of a preliminary design method by using a complete parameterization will be presented. Parameterization, in this case, means the computation and respective sizing of all system components with some key values and a number of model-changing parameters. Numerous structural elements as well as a large number of subsystems (e.g., starter and alternator-systems, reduction gear, retractable undercarriage, recovery system, etc.) were built as parametric models. The level of detail is set to a very high value, in fact down to the smallest shim, in order to take into account all unscale effects. These complex models were analyzed by a systematic variation of different parameters to get simplified mass-estimation equations which are now available for the mass prediction of small UAVs, including the effect of integrating different subsystems.},
keywords = {33. Unmanned Vehicles, 34. Advanced Design},
pubstate = {published},
tppubtype = {inproceedings}
}