SAWE Technical Papers
Technical Library
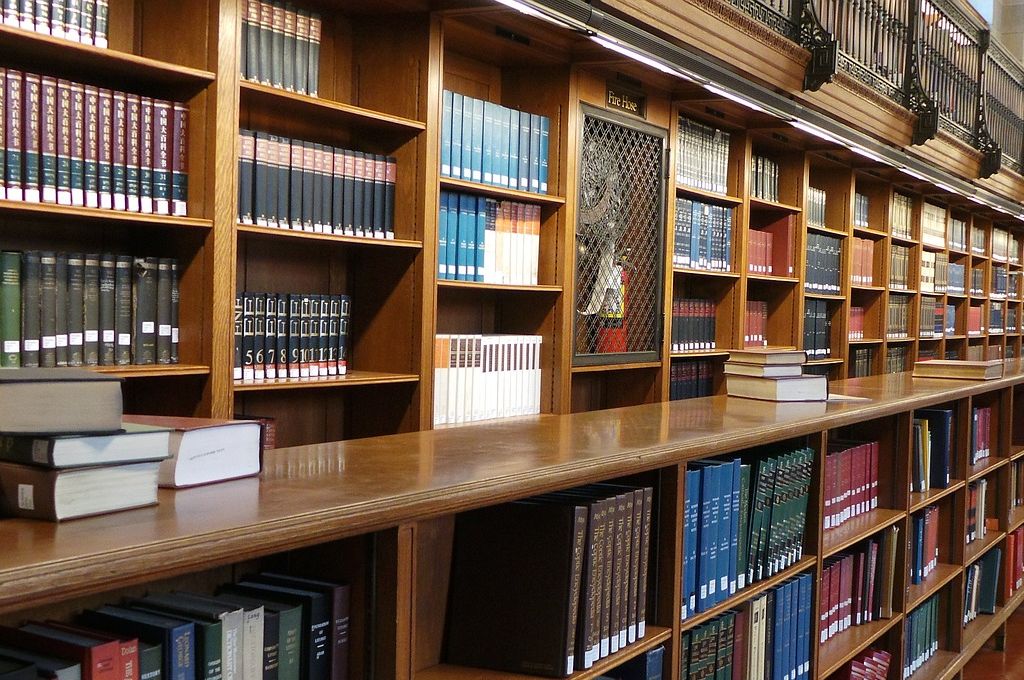
SAWE Paper Database
The SAWE Technical Library contains nearly 4000 technical papers available here for purchase and download. Use the search options below to find what you need.
3758. Strategies for the Grid Stiffened Composite Panel Topology Optimization for Minimum Weight Talele, Mohit; Elham, Ali In: 2020 SAWE Tech Fair, pp. 25, Society of Allied Weight Engineers, Inc., Virtual Conference, 2020. Abstract | Buy/Download | BibTeX | Tags: 22. Weight Engineering - Structural Design, 27. Weight Reduction - Materials, Student Papers 3664. Advanced Lightweight 3D Structures (AL3DS) Manufacturing Design Concept Feldman, Max; Sobol, Jonathan; Gerren, Dr. Donna In: 75th Annual Conference, Denver, Colorado, pp. 14, Society of Allied Weight Engineers, Inc., Denver, Colorado, 2016. Abstract | Buy/Download | BibTeX | Tags: 27. Weight Reduction - Materials, Student Papers 3565. Weight Aspects Of Glare Fiber Metal Laminates Hengel, Cees G. In: 72nd Annual Conference, St. Louis, Missouri, pp. 24, Society of Allied Weight Engineers, Inc., Saint Louis, Missouri, 2013. Abstract | Buy/Download | BibTeX | Tags: 27. Weight Reduction - Materials 3492. Explosion Welding and Bimetal Transitions for Weight Management Blakely, Michael In: 69th Annual Conference, Virginia Beach, Virginia, pp. 11, Society of Allied Weight Engineers, Inc., Virginia Beach, Virginia, 2010. Abstract | Buy/Download | BibTeX | Tags: 27. Weight Reduction - Materials, 28. Weight Reduction - Processes 3464. Innovative, Robust and Reusable Acreage TPS for Space Launch, Re-Entry and Hypersonic Vehicles Luce, Thomas L. In: 68th Annual Conference, Wichita, Kansas, pp. 21, Wichita, Kansas, 2009. Abstract | Buy/Download | BibTeX | Tags: 27. Weight Reduction - Materials Luce, Thomas In: 65th Annual Conference, Valencia, California, pp. 20, Society of Allied Weight Engineers Society of Allied Weight Engineers, Valencia, California, 2006. Abstract | Buy/Download | BibTeX | Tags: 27. Weight Reduction - Materials 3309. Aluminum Beryllium Metal Matrix Composites for Weight Reduction Haws,; Pokross,; Parsonage, In: 62nd Annual Conference, New Haven, Connecticut, pp. 14, Society of Allied Weight Engineers, Inc., New Haven, Connecticut, 2003. Abstract | Buy/Download | BibTeX | Tags: 27. Weight Reduction - Materials 3316. New High Strength Glass Bubbles Survive Injection Molding Conditions Isrealson, Ron In: 62nd Annual Conference, New Haven, Connecticut, pp. 9, Society of Allied Weight Engineers, Inc., New Haven, Connecticut, 2003. Abstract | Buy/Download | BibTeX | Tags: 27. Weight Reduction - Materials 3111. A Proven Waterborne Coating Oxenford, Andrew In: 60th Annual Conference, Arlington, Texas, May 19-23, pp. 22, Society of Allied Weight Engineers, Inc., Arlington, Texas, 2001. Abstract | Buy/Download | BibTeX | Tags: 27. Weight Reduction - Materials 3113. Composite Ejector Door Design Concept Evaluation for the HSCT Engine Nozzle Russell,; Foreman,; Pauletti,; Sauer,; Courtney, In: 60th Annual Conference, Arlington, Texas, May 19-23, pp. 12, Society of Allied Weight Engineers, Inc., Arlington, Texas, 2001. Abstract | Buy/Download | BibTeX | Tags: 27. Weight Reduction - Materials 3116. Utilizing High Thermal Conductivity Graphite Foam to Improve Heat Exchanger Performance Wiechmann,; Vrable,; Klett, In: 60th Annual Conference, Arlington, Texas, May 19-23, pp. 10, Society of Allied Weight Engineers, Inc., Arlington, Texas, 2001. Abstract | Buy/Download | BibTeX | Tags: 27. Weight Reduction - Materials Zaidi, Anwer Arif Dr. In: 60th Annual Conference, Arlington, Texas, May 19-23, pp. 26, Society of Allied Weight Engineers, Inc., Arlington, Texas, 2001. Abstract | Buy/Download | BibTeX | Tags: 27. Weight Reduction - Materials 3016. Advances in Titanium Matrix Material Usage Rowe, Charles; Hanuiak, William In: 59th Annual Conference, St. Louis, Missouri, June 5-7, pp. 10, Society of Allied Weight Engineers, Inc., St. Louis, Missouri, 2000. Abstract | Buy/Download | BibTeX | Tags: 27. Weight Reduction - Materials 3026. Electron Beam Welding of F-22 Aft Fuselage Primary Structures Zenas, Robert In: 59th Annual Conference, St. Louis, Missouri, June 5-7, pp. 21, Society of Allied Weight Engineers, Inc., St. Louis, Missouri, 2000. Abstract | Buy/Download | BibTeX | Tags: 27. Weight Reduction - Materials 2452. AlBeMet and AlBeCast: Lightweight High Performance Alloys for Weight-Critical Applications Grensing, F Dr. In: 58th Annual Conference, San Jose, California, May 24-26, pp. 17, Society of Allied Weight Engineers, Inc., San Jose, California, 1999. Abstract | Buy/Download | BibTeX | Tags: 27. Weight Reduction - Materials 2469. Introduction of Beryllium Aluminum Castings in the RAH-66 Comanche EOSS Program Hinshaw, C; Raftery, K R; Tetz, D P; Seinberg, J P In: 58th Annual Conference, San Jose, California, May 24-26, pp. 18, Society of Allied Weight Engineers, Inc., San Jose, California, 1999. Abstract | Buy/Download | BibTeX | Tags: 27. Weight Reduction - Materials Vergoz, J In: 58th Annual Conference, San Jose, California, May 24-26, pp. 64, Society of Allied Weight Engineers, Inc., San Jose, California, 1999. Abstract | Buy/Download | BibTeX | Tags: 27. Weight Reduction - Materials 2290. New and Emerging Aluminum Products for Cost-Effective Airframe and Space Structure Staley, J T In: 54th Annual Conference, Huntsville, Alabama, May 22-24, pp. 21, Society of Allied Weight Engineers, Inc., Huntsville, Alabama, 1995. Abstract | Buy/Download | BibTeX | Tags: 27. Weight Reduction - Materials 2180. Application of Arall 3 to the C-17A Cargo Door Pettit, R G; Scott, P W In: 52nd Annual Conference, Biloxi, Mississippi, May 24-26, pp. 14, Society of Allied Weight Engineers, Inc., Biloxi, Mississippi, 1993. Abstract | Buy/Download | BibTeX | Tags: 27. Weight Reduction - Materials Johnson, J L; Kantz, M R In: 52nd Annual Conference, Biloxi, Mississippi, May 24-26, pp. 20, Society of Allied Weight Engineers, Inc., Biloxi, Mississippi, 1993. Abstract | Buy/Download | BibTeX | Tags: 27. Weight Reduction - Materials2020
@inproceedings{3758,
title = {3758. Strategies for the Grid Stiffened Composite Panel Topology Optimization for Minimum Weight},
author = {Mohit Talele and Ali Elham},
url = {https://www.sawe.org/product/paper-3758},
year = {2020},
date = {2020-07-01},
booktitle = {2020 SAWE Tech Fair},
pages = {25},
publisher = {Society of Allied Weight Engineers, Inc.},
address = {Virtual Conference},
abstract = {In this paper, a topology optimization methodology for the minimum weight of the composite stiffened panel with the constraint on the criticial buckling load is presented. An existing finite element solver [1] for the analysis of the stiff- ened tow steered composite panels is extended to perform the topology optimiza- tion for the minimum weight. The panel and the stiffeners are modelled using 3 node traingular Classical Laminate Plate elements (CLPT) and 2 node timoshenko beam elements, respectively. To achieve the independent meshing of the plate and stringers, the Lagrange multiplier based on a weak formulation of the continuity requirements between the plate elements and the beam elements is used. For a specific critical buckling load, the optimum topology of the stiffeners in the stiff- ened composite panel depends not only on the stiffeners but also on the fiber patten of the composite panel. Therefore, design variables corrosponding to both fiber pattern in the skin and stiffeners needs to be considered. Manufacturing mesh ap- proach presented in [1], is used to define the design variables corrosponding to the fiber pattern. The ground structure method is implemented to optimize stringers topology. The cross-sectional area of the stringers in the ground structure are de- fined as the design variables corrosponding to the stiffeners. To perform the robust the optimization, the analytical gradients of the buckling load and the weight of the stiffened panel with respect to design variables are implemented and verified using finite difference. The optimization for the minimum weight is performed for the varied complexities of the ground structures with the constraints on the critical buckling load.},
keywords = {22. Weight Engineering - Structural Design, 27. Weight Reduction - Materials, Student Papers},
pubstate = {published},
tppubtype = {inproceedings}
}
2016
@inproceedings{3664,
title = {3664. Advanced Lightweight 3D Structures (AL3DS) Manufacturing Design Concept},
author = {Max Feldman and Jonathan Sobol and Dr. Donna Gerren},
url = {https://www.sawe.org/product/paper-3664},
year = {2016},
date = {2016-05-01},
booktitle = {75th Annual Conference, Denver, Colorado},
pages = {14},
publisher = {Society of Allied Weight Engineers, Inc.},
address = {Denver, Colorado},
abstract = {Weight is one of the factors with the greatest influence on aircraft performance. The Advanced Lightweight 3D Structures design concept proposes to reduce structural frame we ight through the use of novel manufacturing techniques. The primary objective of this paper is to analytically demonstrate the feasibility of using a 'node and rod' design for an aircraft wing box section. Preliminary analysis shows that weight reduction is possible by employing carbon-fiber rods connected with aluminum 3D printed 'nodes' in place of traditionally manufactured ribs and spars. The 'nodes' can be specifically designed in complex shapes while still allowing for mass - production by using CAD and 3D printing technology. This flexibility in rapid-prototyping allows the engineer to vary the geometry of connectivity in order to optimize for a specific design. The 'node and rod' technique would enable the design and development of increased complexity structural designs in a simple and repeatable way. Analytical software is developed to model the aerodynamic loads acting on a wing box, as well as to analyze the structural properties of a 3D wing box structure. The computational tools are validated using commercial finite element modeling programs such as ANSYS and SOLIDWORKS. These models are compared for different flight loading conditions imposed by varying angle of attack and flight Mach number. Furthermore, the models are compared for different materials,such as aluminum vs carbon-fiber rods.If successful, the node and rod concept can be implemented across multiple engineering disciplines to reduce weight in a wide range of structural design paradigms. The concept would fit well within existing engineering infrastructure as well: the structures team may design the nodes based on the desired geometry and loading cases, while the manufacturing team is able to rapidly prototype and iterate to a final node design, and of course the rods may be sub contracted out. The applications for lightweight, strong structures are endless - cars, robots, architecture, and so on. However, any possible weight reduction would drastically improve aircraft performance in fuel efficiency, range, cruise speed, and available payload. The Advanced Lightweight 3D Structures design concept would allow for a new and improved method for designing and building aircraft.},
keywords = {27. Weight Reduction - Materials, Student Papers},
pubstate = {published},
tppubtype = {inproceedings}
}
2013
@inproceedings{3565,
title = {3565. Weight Aspects Of Glare Fiber Metal Laminates},
author = {Cees G. Hengel},
url = {https://www.sawe.org/product/paper-3565},
year = {2013},
date = {2013-05-01},
booktitle = {72nd Annual Conference, St. Louis, Missouri},
pages = {24},
publisher = {Society of Allied Weight Engineers, Inc.},
address = {Saint Louis, Missouri},
abstract = {Fiber Metal Laminates (FML's) are a class of hybrid materials consisting of thin metal layers, bonded together by layers of adhesive reinforced with high-strength fibers. FML's have a metal-like appearance and several metal-like properties including plasticity Today, after its selection as skin material on the fuselage of the A380 in 2000, Glare FML is well underway to become an established technology in the aerospace industry, combining low weight with high durability and damage tolerance at competitive costs.
This paper presents a basic introduction to GLARE FML's and the associated technology. It identifies four application categories where Glare FML's can be beneficially applied: stiffened panels as part of the primary load carrying structure, local reinforcements, secondary structures, and special structures with integrated functionalities (or 'smart structures'). These categories are illustrated with specific products. The reasons why Glare was selected for these products is illustrated by showing the potential of the Glare technology for each of the three product defining disciplines of materials, manufacturing and design.
Weight aspects of Glare FML's are discussed in the context of the design process as they could present themselves to weight engineers, and some cost aspects are discussed. Weight savings of 10% to over 30% are shown, depending on the specifics of the situation.
Based on the foregoing, it is concluded that Glare FML is a mature technology that enables the creation of light weight aircraft structures with high durability and high damage tolerance, at reasonable cost and low risk.
Based on current design and production experience, and considering the broad development potential, it seems reasonable to expect that Glare FML's will be strong candidates for future aircraft structures.},
keywords = {27. Weight Reduction - Materials},
pubstate = {published},
tppubtype = {inproceedings}
}
This paper presents a basic introduction to GLARE FML's and the associated technology. It identifies four application categories where Glare FML's can be beneficially applied: stiffened panels as part of the primary load carrying structure, local reinforcements, secondary structures, and special structures with integrated functionalities (or 'smart structures'). These categories are illustrated with specific products. The reasons why Glare was selected for these products is illustrated by showing the potential of the Glare technology for each of the three product defining disciplines of materials, manufacturing and design.
Weight aspects of Glare FML's are discussed in the context of the design process as they could present themselves to weight engineers, and some cost aspects are discussed. Weight savings of 10% to over 30% are shown, depending on the specifics of the situation.
Based on the foregoing, it is concluded that Glare FML is a mature technology that enables the creation of light weight aircraft structures with high durability and high damage tolerance, at reasonable cost and low risk.
Based on current design and production experience, and considering the broad development potential, it seems reasonable to expect that Glare FML's will be strong candidates for future aircraft structures.2010
@inproceedings{3492,
title = {3492. Explosion Welding and Bimetal Transitions for Weight Management},
author = {Michael Blakely},
url = {https://www.sawe.org/product/paper-3492},
year = {2010},
date = {2010-05-01},
booktitle = {69th Annual Conference, Virginia Beach, Virginia},
pages = {11},
publisher = {Society of Allied Weight Engineers, Inc.},
address = {Virginia Beach, Virginia},
abstract = {The ability to deploy a wide range of materials in a single comprehensive design gives engineers the freedom to be creative in solving weight related challenges. Dissimilar metal transition joints, made through the explosion welding process, are one of the material options all weight engineers should have in their 'toolbox'. Explosion welding has a long history of welding similar and dissimilar metals into one integrated material. Amongst the many uses of the product are structural transitions between highly dissimilar metals. Explosion welding can facilitate the design and fabrication of structures made from a wide range of metallic materials. It can also assist in improving current designs or preexisting joints made through other methods. The most common application may be the welding of aluminum to steel, but many other possible material combinations exist. This paper introduces the explosion welding process. It also covers some specific examples of dissimilar metal welding for light weighting and weight management in land, aerospace, and ocean based environments.},
keywords = {27. Weight Reduction - Materials, 28. Weight Reduction - Processes},
pubstate = {published},
tppubtype = {inproceedings}
}
2009
@inproceedings{3464,
title = {3464. Innovative, Robust and Reusable Acreage TPS for Space Launch, Re-Entry and Hypersonic Vehicles},
author = {Thomas L. Luce},
url = {https://www.sawe.org/product/paper-3464},
year = {2009},
date = {2009-05-01},
booktitle = {68th Annual Conference, Wichita, Kansas},
pages = {21},
address = {Wichita, Kansas},
abstract = {A new generation of orbital launch, re-entry and hypersonic air vehicles will likely
demand significantly more robust reusable thermal protection systems (TPS)
than earlier and existing vehicles. Not only will these newer TPS need to perform
under the extreme external skin heating conditions inherent to very high speed
air travel, but they will have to do so while being significantly less difficult and
costly to operate than existing systems. Whether one intends to fly at supersonic
(i.e., ~ Mach 1-5), hypersonic (i.e., ~ Mach 5+), or re-entry speeds (e.g., ~ Mach
7 for boosters and ~ Mach 25+ for atmospheric re-entry vehicles), intermittently
or continuously, at elevated altitudes or low, vehicle outer moldlines (OML)
experience significant external aerodynamic and aerothermodynamic heating.
Myriad issues such as reusability, flight profile, mission requirements and
maintenance needs all play important roles in determining the types of TPS
materials and designs desired for particular vehicles. These factors all have
direct and significant implications regarding the weight, cost, and performance of
the overall vehicle design. An array of new launch & re-entry as well as
hypersonic vehicle concepts and related technologies is being developed with
cooperation among and competition between various industry (e.g., Northrop
Grumman Corporation) military (e.g., U.S. Air Force) and civilian (e.g., NASA)
players. Even within the already-weight-sensitive aerospace industry (where
higher marginal vehicle mass usually translates to lower payload weight and
reduced mission capability) developers of new launch, re-entry and hypersonic
vehicles are especially interested in weight issues. Of particular interest in this
paper is some of the continuing work aimed at improving upon space-shuttle-era
TPS technologies, that mitigate shuttle-like TPS durability and maintenance
shortcomings while retaining similar weight and thermal characteristics. In order
to provide some context and perspective for this discussion, this paper presents
selected background information regarding where severe vehicle requirements
come from as well as relevant insights provided by several relatively familiar
historical systems including the Apollo return capsule, Space Shuttle, and X-33.},
keywords = {27. Weight Reduction - Materials},
pubstate = {published},
tppubtype = {inproceedings}
}
demand significantly more robust reusable thermal protection systems (TPS)
than earlier and existing vehicles. Not only will these newer TPS need to perform
under the extreme external skin heating conditions inherent to very high speed
air travel, but they will have to do so while being significantly less difficult and
costly to operate than existing systems. Whether one intends to fly at supersonic
(i.e., ~ Mach 1-5), hypersonic (i.e., ~ Mach 5+), or re-entry speeds (e.g., ~ Mach
7 for boosters and ~ Mach 25+ for atmospheric re-entry vehicles), intermittently
or continuously, at elevated altitudes or low, vehicle outer moldlines (OML)
experience significant external aerodynamic and aerothermodynamic heating.
Myriad issues such as reusability, flight profile, mission requirements and
maintenance needs all play important roles in determining the types of TPS
materials and designs desired for particular vehicles. These factors all have
direct and significant implications regarding the weight, cost, and performance of
the overall vehicle design. An array of new launch & re-entry as well as
hypersonic vehicle concepts and related technologies is being developed with
cooperation among and competition between various industry (e.g., Northrop
Grumman Corporation) military (e.g., U.S. Air Force) and civilian (e.g., NASA)
players. Even within the already-weight-sensitive aerospace industry (where
higher marginal vehicle mass usually translates to lower payload weight and
reduced mission capability) developers of new launch, re-entry and hypersonic
vehicles are especially interested in weight issues. Of particular interest in this
paper is some of the continuing work aimed at improving upon space-shuttle-era
TPS technologies, that mitigate shuttle-like TPS durability and maintenance
shortcomings while retaining similar weight and thermal characteristics. In order
to provide some context and perspective for this discussion, this paper presents
selected background information regarding where severe vehicle requirements
come from as well as relevant insights provided by several relatively familiar
historical systems including the Apollo return capsule, Space Shuttle, and X-33.2006
@inproceedings{3388,
title = {3388. Incorporating Weight-Saving Thermally Insulated Multifunctional Structures (TIMS) into Future Fast Air Vehicle Designs},
author = {Thomas Luce},
url = {https://www.sawe.org/product/paper-3388},
year = {2006},
date = {2006-05-01},
booktitle = {65th Annual Conference, Valencia, California},
pages = {20},
publisher = {Society of Allied Weight Engineers},
address = {Valencia, California},
organization = {Society of Allied Weight Engineers},
abstract = {For some proposed flight vehicles experiencing significant external heating, the use of lower conductivity structural assemblies will translate into lighter structures. In certain cases, such lower conductivity structures are not just preferred, they actually represent enabling technology. In these cases, traditional structural solutions are likely to either be too heavy or simply unable to manage the heat loading effectively. Or both. Whether one intends to fly at supersonic (i.e., Mach 2-5), hypersonic (i.e., Mach 5+), or re-entry (e.g., Mach 7 boosters and Mach 25+ atmospheric re-entry vehicles) speeds, intermittently or continuously, at elevated altitudes or low, vehicle outer moldlines (OML) will experience significant external aerodynamic and aerothermodynamic heating. This fact has direct and significant implications for vehicle design, weight, cost, and performance. Short of inventing specific new materials that effectively and simultaneously perform all required structural and thermal functions (not likely any time soon), innovative multi-functional structures will be required. Successful such multifunctional structures will effectively combine non-structural, low- conductivity materials with relatively high conductivity durable and damage tolerant structural materials that best satisfy a host of system requirements. For many future DoD (Department of Defense) and NASA (National Aeronautics and Space Administration) vehicles, one critical discriminator among competing designs will certainly be system weight. As such, the development of improved thermally insulated multifunctional structures will certainly play a vital role.},
keywords = {27. Weight Reduction - Materials},
pubstate = {published},
tppubtype = {inproceedings}
}
2003
@inproceedings{3309,
title = {3309. Aluminum Beryllium Metal Matrix Composites for Weight Reduction},
author = {Haws and Pokross and Parsonage},
url = {https://www.sawe.org/product/paper-3309},
year = {2003},
date = {2003-05-01},
booktitle = {62nd Annual Conference, New Haven, Connecticut},
pages = {14},
publisher = {Society of Allied Weight Engineers, Inc.},
address = {New Haven, Connecticut},
abstract = {This paper will focus on the development of aluminum beryllium materials, AlBeMet? 162 and AlBeMet? 140, for applications requiring improved weight reduction, higher thermal performance, improved stiffness, and improved damping over aluminum and other materials.
The paper will also discuss the development of AlBeMet? 140 thin gauge sheet, 0.010? (0.254 mm) thickness, as a skin material for honeycomb panel applications, as a replacement for standard aluminum and composite materials. The paper will also discuss some technology efforts under way on extrusion and forging developments with this new grade of AlBeMet?.},
keywords = {27. Weight Reduction - Materials},
pubstate = {published},
tppubtype = {inproceedings}
}
The paper will also discuss the development of AlBeMet? 140 thin gauge sheet, 0.010? (0.254 mm) thickness, as a skin material for honeycomb panel applications, as a replacement for standard aluminum and composite materials. The paper will also discuss some technology efforts under way on extrusion and forging developments with this new grade of AlBeMet?.@inproceedings{3316,
title = {3316. New High Strength Glass Bubbles Survive Injection Molding Conditions},
author = {Ron Isrealson},
url = {https://www.sawe.org/product/paper-3316},
year = {2003},
date = {2003-05-01},
booktitle = {62nd Annual Conference, New Haven, Connecticut},
pages = {9},
publisher = {Society of Allied Weight Engineers, Inc.},
address = {New Haven, Connecticut},
abstract = {Glass bubble microspheres have been successfully used as fillers/additives for various kinds of polymeric compounds since the mid-1960s. Their ability to reduce the weight of finished parts, reduce resin demand, and provide other useful properties has helped end-users meet strict weight targets and reduce waste of a variety of products. Until recently, however, glass bubbles were not often considered for injection-molded parts, due to the belief that the pressures involved would break the bubbles. This concern is no longer an issue. As a result of new technical developments at 3M, a breakthrough in glass bubble manufacturing technology has led to the introduction of a new high strength glass bubble that has demonstrated its ability to withstand plastics compounding and injection molding. 3M markets this new glass bubble and all former glass bubbles under the trade name, 3M? brand Scotchlite? brand Glass Bubbles.},
keywords = {27. Weight Reduction - Materials},
pubstate = {published},
tppubtype = {inproceedings}
}
2001
@inproceedings{3111,
title = {3111. A Proven Waterborne Coating},
author = {Andrew Oxenford},
url = {https://www.sawe.org/product/paper-3111},
year = {2001},
date = {2001-05-01},
booktitle = {60th Annual Conference, Arlington, Texas, May 19-23},
pages = {22},
publisher = {Society of Allied Weight Engineers, Inc.},
address = {Arlington, Texas},
abstract = {Kimetsan Aerospace Coatings have developed a range of proven high performance low VOC waterborne coatings with a number of important features. As part of our research we sought to resolve outstanding coating issues and address those of the future, while the fashionable move to high solid paint (HSP) has created additional problems to those that already existed.
Coating manufacturers argue that the aerospace market is too small to justify the development of environmentally friendly coatings. Instead they 'demonstrate unreasonable economic hardship' to the Environmental Protection Agency (EPA). Unreasonably, these economic hardships have been passed on to the aircraft manufacturer and their customers. High capital investment in environmental programs, lost revenue, and worker safety is the price being paid. Where Volatile Organic Compounds (VOCs) have been reduced, considerable increases in the weight and drying times have been substituted. It behooves responsible manufacturers to provide a viable alternative.
We have reduced the VOCs of pigmented coatings to a Californian low when admired of 198 grams/liter. The dry film weight is up to 80% lighter than HSP and the drying times are measured in minutes. They are not carcinogenic and do not contain strontium chromate, isocyanurates, or fluorocarbons. Despite the aerospace industries fatalistic views on aircraft fires, these coatings provide a high degree of fire hardening. The exceptional anti-static properties enhance safety and operational economies. They are odorless when applied and easy to clean without toxic detergents and solvents.
Testimony to their durability is over four years of successful trials on fast jets and cargo aircraft. We have included reports from trials carried out in other sectors of industry including the surface transport and marine sectors. They were invaluable in designing the only proven waterborne coatings available to the aerospace industry today. The coatings have been developed to provide the customer with a degree of performance, economy, physical and environmental safety hitherto unavailable.},
keywords = {27. Weight Reduction - Materials},
pubstate = {published},
tppubtype = {inproceedings}
}
Coating manufacturers argue that the aerospace market is too small to justify the development of environmentally friendly coatings. Instead they 'demonstrate unreasonable economic hardship' to the Environmental Protection Agency (EPA). Unreasonably, these economic hardships have been passed on to the aircraft manufacturer and their customers. High capital investment in environmental programs, lost revenue, and worker safety is the price being paid. Where Volatile Organic Compounds (VOCs) have been reduced, considerable increases in the weight and drying times have been substituted. It behooves responsible manufacturers to provide a viable alternative.
We have reduced the VOCs of pigmented coatings to a Californian low when admired of 198 grams/liter. The dry film weight is up to 80% lighter than HSP and the drying times are measured in minutes. They are not carcinogenic and do not contain strontium chromate, isocyanurates, or fluorocarbons. Despite the aerospace industries fatalistic views on aircraft fires, these coatings provide a high degree of fire hardening. The exceptional anti-static properties enhance safety and operational economies. They are odorless when applied and easy to clean without toxic detergents and solvents.
Testimony to their durability is over four years of successful trials on fast jets and cargo aircraft. We have included reports from trials carried out in other sectors of industry including the surface transport and marine sectors. They were invaluable in designing the only proven waterborne coatings available to the aerospace industry today. The coatings have been developed to provide the customer with a degree of performance, economy, physical and environmental safety hitherto unavailable.@inproceedings{3113,
title = {3113. Composite Ejector Door Design Concept Evaluation for the HSCT Engine Nozzle},
author = {Russell and Foreman and Pauletti and Sauer and Courtney},
url = {https://www.sawe.org/product/paper-3113},
year = {2001},
date = {2001-05-01},
booktitle = {60th Annual Conference, Arlington, Texas, May 19-23},
pages = {12},
publisher = {Society of Allied Weight Engineers, Inc.},
address = {Arlington, Texas},
abstract = {Weight savings requirements for the High Speed Civil Transport (HSCT) engine nozzle have motivated development of polymer matrix composite (PMC) and ceramic matrix composite (CMC) structural concepts for the nozzle secondary air ejector door. Initial trade studies of these concepts resulted in synthesis of a PMC sandwich door concept with CMC thermal protection system (TPS) as a promising candidate for further development. Thermal and structural analyses of this concept have been performed to permit a weight comparison with a baseline metallic door concept. A manufacturing plan has been developed to highlight producibility issues and support parametric cost estimating efforts. The final results show that the composite door concept has a modest weight advantage and a distinct cost disadvantage relative to the metallic concept. Risk mitigation and design recommendations have been developed to make the composite concept more attractive for future HSCT engine nozzle development efforts.},
keywords = {27. Weight Reduction - Materials},
pubstate = {published},
tppubtype = {inproceedings}
}
@inproceedings{3116,
title = {3116. Utilizing High Thermal Conductivity Graphite Foam to Improve Heat Exchanger Performance},
author = {Wiechmann and Vrable and Klett},
url = {https://www.sawe.org/product/paper-3116},
year = {2001},
date = {2001-05-01},
booktitle = {60th Annual Conference, Arlington, Texas, May 19-23},
pages = {10},
publisher = {Society of Allied Weight Engineers, Inc.},
address = {Arlington, Texas},
abstract = {Contemporary thermal management has centered on aluminum and copper heat sinks and substrates. This is due to the very high thermal conductivity (180 W/m K for aluminum 6061 and 400 W/m K for copper). However, when weight is taken into account, the specific thermal conductivity (thermal conductivity divided by specific gravity) is only ~54 and 45 W/m K respectively. Therefore, in many applications, where weight is a significant concern, it is imperative that a lighter thermal management material is found.
New materials under development offer the potential to fabricate heat exchangers that are more efficient. The higher efficiency translates to smaller units and lower weight. The new materials are based on graphite, either a fiber or a new manifestation, graphitic foam.
A new process for fabricating graphitic foam has been developed at Oak Ridge National Laboratory (ORNL). Poco Graphite, Inc., of Decatur, Texas has licensed the process and is commercializing the product. Initially these foams possess a thermal conductivity of 120-150 W/m K at a relatively low density of 0.54 g/cm3. Potentially, the process will lead to a significant reduction in the cost of graphitic-based thermal management materials (i.e., foam- reinforced composites and foam core sandwich structures).
This paper reviews the recent work to understand the graphite foam material and also discusses the work being done to prove its utility in actual aircraft heat exchanger designs.},
keywords = {27. Weight Reduction - Materials},
pubstate = {published},
tppubtype = {inproceedings}
}
New materials under development offer the potential to fabricate heat exchangers that are more efficient. The higher efficiency translates to smaller units and lower weight. The new materials are based on graphite, either a fiber or a new manifestation, graphitic foam.
A new process for fabricating graphitic foam has been developed at Oak Ridge National Laboratory (ORNL). Poco Graphite, Inc., of Decatur, Texas has licensed the process and is commercializing the product. Initially these foams possess a thermal conductivity of 120-150 W/m K at a relatively low density of 0.54 g/cm3. Potentially, the process will lead to a significant reduction in the cost of graphitic-based thermal management materials (i.e., foam- reinforced composites and foam core sandwich structures).
This paper reviews the recent work to understand the graphite foam material and also discusses the work being done to prove its utility in actual aircraft heat exchanger designs.@inproceedings{3142,
title = {3142. Transitioin From Aluminum 2219 External Tank to 2195 Al-Li Super-Lite Weight External Tank Design for the Space Shuttle La},
author = {Anwer Arif Dr. Zaidi},
url = {https://www.sawe.org/product/paper-3142},
year = {2001},
date = {2001-05-01},
booktitle = {60th Annual Conference, Arlington, Texas, May 19-23},
pages = {26},
publisher = {Society of Allied Weight Engineers, Inc.},
address = {Arlington, Texas},
abstract = {2195 Al-Li alloy was developed to form the basis of the next generations of Super Light Weight External Tank (SLWET) design for space shuttle launch system. The first generation of external tanks was fabricated from 2219 aluminum alloy. The motivation for the replacement lies in weight savings of approximately 23% (7500 Lbs.) due to the lower density and higher stiffness to weight ratio of 2195 Al-Li alloy as compared to its predecessor.
Variable polarity plasma arc welding is the primary means of fabrication of SLWET. During the development work on SLWET, at MSFC, NASA, a peculiar nature of cracking tendency in the 2195 Al-Li welds was observed. A lighthearted historical account of the experimental research, conducted to understand the mechanism and nature of2195 Al-Li welds cracking problem is described. It was observed that some of the cracks in 2195 Al-Li alloy, were quite different in morphology from what generally was known about the weld cracks in aluminum alloys. The segment of work described in this paper has been picked from a large volume of research work, the ultimate objective of which was to characterize 2195 Al-Li welds for the fabrication of SLWET. The space limitation do not permit covering more than one aspect of the problem, which is described here to highlight the work that went into the grand goal of achieving weight savings.
The initial part describes the role of the external tank and some of its interesting features, which is necessary to put things in perspective. Certain initial phases of the research are highlighted, those that are included are the results from destructive and non-destructive analysis, and analysis tools like TGA, DTA, and SEM work with some relevant results are explored. It should be kept in mind at all times that these cracking problems had to solved, only then transition to the new lightweight alloy could be accomplished, and weight saving materialized.},
keywords = {27. Weight Reduction - Materials},
pubstate = {published},
tppubtype = {inproceedings}
}
Variable polarity plasma arc welding is the primary means of fabrication of SLWET. During the development work on SLWET, at MSFC, NASA, a peculiar nature of cracking tendency in the 2195 Al-Li welds was observed. A lighthearted historical account of the experimental research, conducted to understand the mechanism and nature of2195 Al-Li welds cracking problem is described. It was observed that some of the cracks in 2195 Al-Li alloy, were quite different in morphology from what generally was known about the weld cracks in aluminum alloys. The segment of work described in this paper has been picked from a large volume of research work, the ultimate objective of which was to characterize 2195 Al-Li welds for the fabrication of SLWET. The space limitation do not permit covering more than one aspect of the problem, which is described here to highlight the work that went into the grand goal of achieving weight savings.
The initial part describes the role of the external tank and some of its interesting features, which is necessary to put things in perspective. Certain initial phases of the research are highlighted, those that are included are the results from destructive and non-destructive analysis, and analysis tools like TGA, DTA, and SEM work with some relevant results are explored. It should be kept in mind at all times that these cracking problems had to solved, only then transition to the new lightweight alloy could be accomplished, and weight saving materialized.2000
@inproceedings{3016,
title = {3016. Advances in Titanium Matrix Material Usage},
author = {Charles Rowe and William Hanuiak},
url = {https://www.sawe.org/product/paper-3016},
year = {2000},
date = {2000-06-01},
booktitle = {59th Annual Conference, St. Louis, Missouri, June 5-7},
pages = {10},
publisher = {Society of Allied Weight Engineers, Inc.},
address = {St. Louis, Missouri},
abstract = {Atlantic Research Corporation A manufacturing company with deep technology roots producing technically advanced tactical rocket motors, satellite thrusters,advanced materials aircraftcomponents, and automotive air bag inflators at 18,000 units per day.},
keywords = {27. Weight Reduction - Materials},
pubstate = {published},
tppubtype = {inproceedings}
}
@inproceedings{3026,
title = {3026. Electron Beam Welding of F-22 Aft Fuselage Primary Structures},
author = {Robert Zenas},
url = {https://www.sawe.org/product/paper-3026},
year = {2000},
date = {2000-06-01},
booktitle = {59th Annual Conference, St. Louis, Missouri, June 5-7},
pages = {21},
publisher = {Society of Allied Weight Engineers, Inc.},
address = {St. Louis, Missouri},
abstract = {Two major components of the rear fuselage of the F-22 Raptor fighter, the forward and aft boom assemblies, were designed and fabricated as monolithic weldments in order to achieve a significant weight savings. This was a challenging task, as these components are fracture/durability critical, load bearing structures that attach the wings and vertical stabilizers to the fuselage and support the horizontal stabilizers. They also form part of the engine bay compartment, have aerodynamic surfaces/contours, and provide internal fuel storage. These highly efficient structures are made from over 90 separate pieces of 6Al-4V titanium alloy. Over 3,600 inches of full penetration electron beam welding are required to fabricate the four assemblies for each ship set.},
keywords = {27. Weight Reduction - Materials},
pubstate = {published},
tppubtype = {inproceedings}
}
1999
@inproceedings{2452,
title = {2452. AlBeMet and AlBeCast: Lightweight High Performance Alloys for Weight-Critical Applications},
author = {F Dr. Grensing},
url = {https://www.sawe.org/product/paper-2452},
year = {1999},
date = {1999-05-01},
booktitle = {58th Annual Conference, San Jose, California, May 24-26},
pages = {17},
publisher = {Society of Allied Weight Engineers, Inc.},
address = {San Jose, California},
abstract = {AlBeMet? materials are a family of aluminum-beryllium alloys containing 30 to 65 weight percent beryllium. The alloys offer substantial weight reductions and modulus increases when compared with other aerospace alloys. The mechanical properties of AlBeMet? materials are well suited for most weight critical applications. The strength performance of the materials equals or exceeds most traditional aluminum alloys, and the alloy's specific property performance offers an even greater benefit. AlBeMet? is produced using several techniques and is produced as extruded bar, rolled sheet, hot isostatically pressed (MIP) block. and investment castings. AlBeMet? alloys are powder metal products produced by the hot consolidation of inert gas atomized powder, while AlBeCast? IC910 is an investment casting alloy. AlBeMet? and AlBeCast? alloys can be fabricated into components using many standard aluminum industry processes and equipment. Machining, joining, and coating operations have been developed for the alloys and these deviate little from aluminum industry practice. The principle difference between working with aluminum and aluminum-beryllium materials is the need control, collect, and remove any beryllium- containing particles generated during the operation. The use of the materials has greatly expanded and the alloys are now used in a number of avionics, aerospace, robotics, automotive, commercial, and data storage applications. A direct substitution for aluminum results in a 270% increase in stiffness: a constant stiffness design using aluminum-beryllium alloys can reduce weight by 45 to 55%.},
keywords = {27. Weight Reduction - Materials},
pubstate = {published},
tppubtype = {inproceedings}
}
@inproceedings{2469,
title = {2469. Introduction of Beryllium Aluminum Castings in the RAH-66 Comanche EOSS Program},
author = {C Hinshaw and K R Raftery and D P Tetz and J P Seinberg},
url = {https://www.sawe.org/product/paper-2469},
year = {1999},
date = {1999-05-01},
booktitle = {58th Annual Conference, San Jose, California, May 24-26},
pages = {18},
publisher = {Society of Allied Weight Engineers, Inc.},
address = {San Jose, California},
abstract = {Beryllium aluminum alloys, containing greater than 60 weight percent beryllium, are very attractive materials for lightweight and high-stiffness applications. However, due to the inherent problems associated with casting these alloys, processing of beryllium aluminum has generally been restricted to rolling and extrusion of pre-alloyed powder metal compacts. Starmet Corporation (formally Nuclear Metals, Inc.), with technical and financial support from the Lockheed Martin Electronics and Missiles (LMEM) RAH-66 Comanche Electro-Optical Sensor System (EOSS) program, has developed a family of castable beryllium aluminum alloys suited for production using state-of-the-technology investment casting processes. These new alloys, identified as Beralcast?, yield a fine grain homogenous microstructure with attractive mechanical, physical and thermal properties. The problems associated with producing beryllium aluminum castings, including molten metal reactivity and a wide solidification range, have been resolved. As a result of the efforts to date, over fifty different Comanche EOSS components of various sizes and complexities are being produced using Beralcast? alloys. In certain cases, where designs are being modified to take full advantage of the Beralcast? properties, component weight savings of up to 50% over conventional materials can be achieved. Current focus is on the optimization of castings and cost reduction. Developmental program goals, over the past few years, have been and are being addressed in a series of programs funded by Starmet Corporation, LMEM, and the Army Aviation Research and Development Center. As a result of these efforts, Beralcast? investment castings have been available in time to support the RAH-66 Comanche EOSS demonstration/validation (Dem/Val) night hardware program.},
keywords = {27. Weight Reduction - Materials},
pubstate = {published},
tppubtype = {inproceedings}
}
@inproceedings{2470,
title = {2470. Ideas for Vehicle Weight Savings Exterior Automotive Body Panels and Structural Automotive Applications},
author = {J Vergoz},
url = {https://www.sawe.org/product/paper-2470},
year = {1999},
date = {1999-05-01},
booktitle = {58th Annual Conference, San Jose, California, May 24-26},
pages = {64},
publisher = {Society of Allied Weight Engineers, Inc.},
address = {San Jose, California},
abstract = {A number of automobile component applications using Advanced Steel, Aluminum, and sheet molded composites (SMC) plastics are presented along with the weight and cost impact of materials selected. The investigation looked into the economic tradeoff of annual component volume, material, and finished component costs. For all applications, aluminum is shown to be the lightest (~50% weight savings) yet most expensive with a cost increase of over 50% at all volumes compared to mild steel. Sheet molded composites are being used in several applications with a weight savings of 20% compared to mild steel and a cost reduction at vehicle volumes below 150,000-200,000 per year. Low density SMC in the development stage should be available within five years with a weight savings of 50% approaching aluminum at a cost of mild steel in volumes below 120,000 per year.},
keywords = {27. Weight Reduction - Materials},
pubstate = {published},
tppubtype = {inproceedings}
}
1995
@inproceedings{2290,
title = {2290. New and Emerging Aluminum Products for Cost-Effective Airframe and Space Structure},
author = {J T Staley},
url = {https://www.sawe.org/product/paper-2290},
year = {1995},
date = {1995-05-01},
booktitle = {54th Annual Conference, Huntsville, Alabama, May 22-24},
pages = {21},
publisher = {Society of Allied Weight Engineers, Inc.},
address = {Huntsville, Alabama},
abstract = {There are many drivers and parameters involved in the development and selection of materials for aircraft. They include, but are not limited to: low structural weight, safety factors, cost, availability, manufacturability, reliability, and maintainability. The drivers for materials selection and alloy development for aircraft have changed considerably during this century. Some of the same drivers and parameters exist for materials for space, but the relative importance is usually different. For example, long-term maintainability is a primary concern in designing airframes, but is hardly a concern for consumable rocket cryotankage or for structures which will spend their life in space. In addition, the value of a unit of weight saved by using a new material may be tens or even hundreds of times higher for space applications. This paper first describes the high strength aluminum alloy materials available to the designer and gives examples of their applications. The materials are presented in the approximate order of their development. Each section is introduced by a brief discussion which includes the drivers which lead to their development. The paper also gives a glimpse at materials which are still in the embryonic stage and discusses the factors driving their development.},
keywords = {27. Weight Reduction - Materials},
pubstate = {published},
tppubtype = {inproceedings}
}
1993
@inproceedings{2180,
title = {2180. Application of Arall 3 to the C-17A Cargo Door},
author = {R G Pettit and P W Scott},
url = {https://www.sawe.org/product/paper-2180},
year = {1993},
date = {1993-05-01},
booktitle = {52nd Annual Conference, Biloxi, Mississippi, May 24-26},
pages = {14},
publisher = {Society of Allied Weight Engineers, Inc.},
address = {Biloxi, Mississippi},
abstract = {Since 1985, McDonnell Douglas Aerospace has been developing ARALL laminate technology for new military and commercial aircraft. In 1988 effort was focused on identifying and evaluating various applications for the United States Air Force C-17 aircraft. Late that year, the cargo door skin application was authorized for production. This paper presents the reasons for selecting the cargo door for an ARALL laminate application over other candidates and reviews various design and manufacturing issues. A weight-strength analysis of the cargo door is also presented. Finally, a few remarks are dated at the future of the technology.},
keywords = {27. Weight Reduction - Materials},
pubstate = {published},
tppubtype = {inproceedings}
}
@inproceedings{2181,
title = {2181. Design and Fabrication of a Lightweight, High Strength Sandwich Panel for Aircraft Grade Flooring},
author = {J L Johnson and M R Kantz},
url = {https://www.sawe.org/product/paper-2181},
year = {1993},
date = {1993-05-01},
booktitle = {52nd Annual Conference, Biloxi, Mississippi, May 24-26},
pages = {20},
publisher = {Society of Allied Weight Engineers, Inc.},
address = {Biloxi, Mississippi},
abstract = {This presentation describes the development, construction, and performance of a state-of-the-art aircraft grade flooring panel. Several supported beam calculations are presented to illustrate how performance objectives and material selection issues were reconciled to give a sandwich panel offering 20 percent weight reduction and low flame, smoke, and toxicity (FST) properties without compromising stiffness and strength properties.},
keywords = {27. Weight Reduction - Materials},
pubstate = {published},
tppubtype = {inproceedings}
}