SAWE Technical Papers
Technical Library
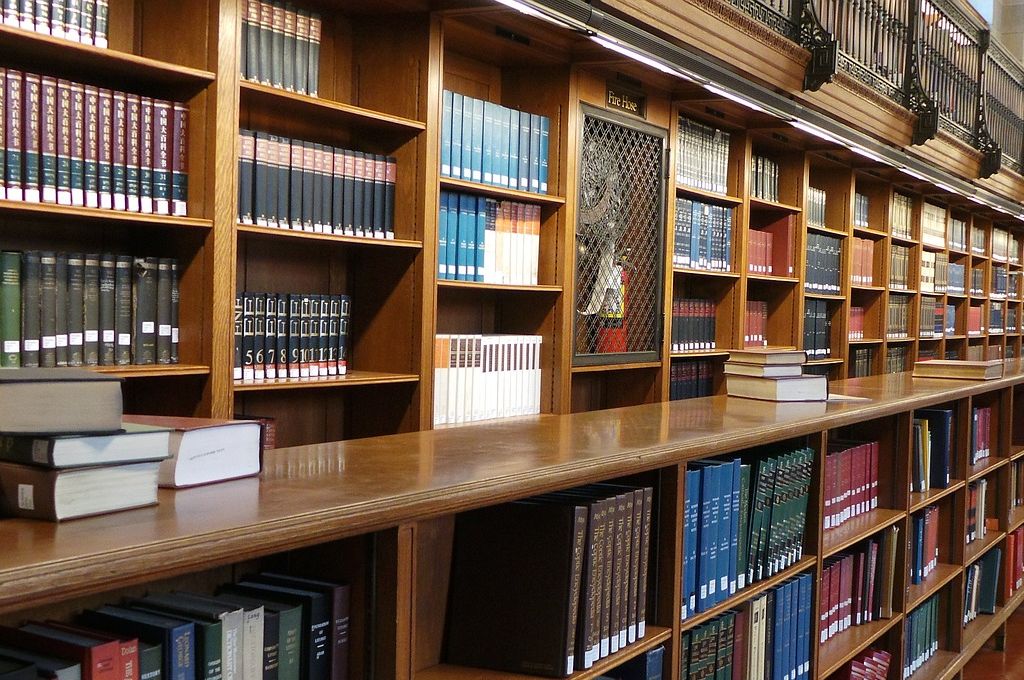
SAWE Paper Database
The SAWE Technical Library contains nearly 4000 technical papers available here for purchase and download. Use the search options below to find what you need.
3758. Strategies for the Grid Stiffened Composite Panel Topology Optimization for Minimum Weight Talele, Mohit; Elham, Ali In: 2020 SAWE Tech Fair, pp. 25, Society of Allied Weight Engineers, Inc., Virtual Conference, 2020. Abstract | Buy/Download | BibTeX | Tags: 22. Weight Engineering - Structural Design, 27. Weight Reduction - Materials, Student Papers 3679. Design and Optimization of an Aluminum Structure Assembled by Elastic Fastening Laverne, Clément; Desrochers, Alain; Maslouhi, Ahmed In: 76th Annual Conference, Montreal, Canada, pp. 26, Society of Allied Weight Engineers, Inc., Montreal, Canada, 2017. Abstract | Buy/Download | BibTeX | Tags: 22. Weight Engineering - Structural Design, Student Papers Klim, Graeme; Hashemi, Dr. Seyed M. In: 76th Annual Conference, Montreal, Canada, pp. 25, Society of Allied Weight Engineers, Inc., Montreal, Canada, 2017. Abstract | Buy/Download | BibTeX | Tags: 22. Weight Engineering - Structural Design, 34. Advanced Design, Student Papers 3655. Weight and Structural Optimization in Aircraft Design Alves, William; Silva, Juliana In: 75th Annual Conference, Denver, Colorado, pp. 30, Society of Allied Weight Engineers, Inc., Denver, Colorado, 2016. Abstract | Buy/Download | BibTeX | Tags: 10. Weight Engineering - Aircraft Design, 22. Weight Engineering - Structural Design, 28. Weight Reduction - Processes, 34. Advanced Design 3616. Methodology For Lightweight Design Of Stiffened Skin In Advanced Aerospace Structures Noevere, August In: 73rd Annual Conference, Long Beach, California, pp. 18, Society of Allied Weight Engineers, Inc., Long Beach, California, 2014. Abstract | Buy/Download | BibTeX | Tags: 22. Weight Engineering - Structural Design 3535. Innovative Design with Bi-Level Topology Optimization Remouchamps, Alain; Bruyneel, Michael; Grihon, Stephane; Fleury, Glaude In: 70th Annual Conference, Houstion, Texas, pp. 10, Society of Allied Weight Engineers, Inc., Houston, Texas, 2011. Abstract | Buy/Download | BibTeX | Tags: 22. Weight Engineering - Structural Design Higgins, Chuck In: 68th Annual Conference, Wichita, Kansas, pp. 13, Wichita, Kansas, 2009. Abstract | Buy/Download | BibTeX | Tags: 10. Weight Engineering - Aircraft Design, 18. Weight Engineering - Spacecraft Design, 22. Weight Engineering - Structural Design 3409. Landing Gear Mass Prediction. A Combined Analytic and Parametric Approach Harrison, Adrian; Smith, Sidney; Kay, Edward; Vekris, Evangelos In: 66th Annual Conference, Madrid, Spain, pp. 20, Society of Allied Weight Engineers Society of Allied Weight Engineers, Madrid, Spain, 2007. Abstract | Buy/Download | BibTeX | Tags: 22. Weight Engineering - Structural Design, 23. Weight Engineering - Structural Estimation 3389. Managing Common Data Across Multiple Platforms Tolman, Kathleen; Kniesel, Peter In: 65th Annual Conference, Valencia, California, pp. 24, Society of Allied Weight Engineers Society of Allied Weight Engineers, Valencia, California, 2006. Abstract | Buy/Download | BibTeX | Tags: 12. Weight Engineering - Computer Applications, 22. Weight Engineering - Structural Design 3392. Weight Considerations in the Design of a Low Cost Interceptor Austin, Robert; Brown, Andrew; Carreau, Kiel; Garbeff, Ted; Kearney, Chris; Lutke, Keven; Quinliven, Teresa; Stavros, Kristi In: 65th Annual Conference, Valencia, California, pp. -1, Society of Allied Weight Engineers Society of Allied Weight Engineers, Valencia, California, 2006, (Student Team "Vortex Pirates" from California Polytechnic State University, San Luis Obispo
Paper Missing). Abstract | BibTeX | Tags: 22. Weight Engineering - Structural Design 3393. Avari: Structure and Weight Considerations for the Design of a Homeland Defense Interceptor Perata, Julie; Greiner, Brian; Jensen, Bradley; Mailen, Kit; Miracle, Brian; Nichols, Zach; Pace, Seth; Tucker, Sarah In: 65th Annual Conference, Valencia, California, pp. 30, Society of Allied Weight Engineers Society of Allied Weight Engineers, Valencia, California, 2006, (Student Team Ävari" from California Polytechnic State University, San Luis Obispo). Abstract | Buy/Download | BibTeX | Tags: 22. Weight Engineering - Structural Design 3394. Structural Weight Considerations of a Low Cost High Speed Interceptor Bickley, Benjamin; Bunker, Laura; Dahl, Kelly; Gotzler, Joe; Hueftle, Dave; Huthmacher, Ryan; Richardson, Dan In: 65th Annual Conference, Valencia, California, pp. 33, Society of Allied Weight Engineers Society of Allied Weight Engineers, Valencia, California, 2006, (Student Team "Mothra" from California Polytechnic State University, San Luis Obispo). Abstract | Buy/Download | BibTeX | Tags: 22. Weight Engineering - Structural Design 3395. Revenant: A Weight And Structural Approach To The Design Of A Homeland Defense Interceptor Lemm, Jessica; Marino, Chris; Mendez, Laura; Miknus, Scott; Piper, Ben; Ross, Brian; Tamayo, William In: 65th Annual Conference, Valencia, California, pp. 36, Society of Allied Weight Engineers Society of Allied Weight Engineers, Valencia, California, 2006, (Student Team "Sentinel Solutions" from California Polytechnic State University, San Luis Obispo). Abstract | Buy/Download | BibTeX | Tags: 22. Weight Engineering - Structural Design 3359. Weight and Balance Considerations for Unmanned Combat Aerial Vehicles University, California Polytechnic State In: 64th Annual Conference, Annapolis, Maryland, pp. 23, Society of Allied Weight Engineers, Inc., Annapolis, Maryland, 2005. Abstract | Buy/Download | BibTeX | Tags: 22. Weight Engineering - Structural Design, 33. Unmanned Vehicles, Student Papers 3361. Developments of Composite Manufacturing Technologies at NLR Thuis, Bert In: 64th Annual Conference, Annapolis, Maryland, pp. 36, Society of Allied Weight Engineers, Inc., Annapolis, Maryland, 2005. Abstract | Buy/Download | BibTeX | Tags: 22. Weight Engineering - Structural Design Godines,; Abdi, Frank In: 63rd Annual Conference, Newport, California, pp. 22, Society of Allied Weight Engineers, Inc., Newport, California, 2004. Abstract | Buy/Download | BibTeX | Tags: 22. Weight Engineering - Structural Design 3333. The Development of Composite Landing Gear Components for Aerospace Applications Thuis, Bert G. S. J In: 63rd Annual Conference, Newport, California, pp. 21, Society of Allied Weight Engineers, Inc., Newport, California, 2004. Abstract | Buy/Download | BibTeX | Tags: 22. Weight Engineering - Structural Design 3336. Composite Materials for Structural Landing Gear Components On CD-R Sijpkes,; Vergouwen, In: 63rd Annual Conference, Newport, California, pp. 7, Society of Allied Weight Engineers, Inc., Newport, California, 2004. Abstract | Buy/Download | BibTeX | Tags: 22. Weight Engineering - Structural Design 3339. Topology Optimization for Weight Reduction During Preliminary Design Thomas, Harold In: 63rd Annual Conference, Newport, California, pp. 11, Society of Allied Weight Engineers, Inc., Newport, California, 2004. Abstract | Buy/Download | BibTeX | Tags: 22. Weight Engineering - Structural Design University, California Polytechnic State In: 63rd Annual Conference, Newport, California, pp. 20, Society of Allied Weight Engineers, Inc., Newport, California, 2004. Abstract | Buy/Download | BibTeX | Tags: 22. Weight Engineering - Structural Design, Student Papers2020
@inproceedings{3758,
title = {3758. Strategies for the Grid Stiffened Composite Panel Topology Optimization for Minimum Weight},
author = {Mohit Talele and Ali Elham},
url = {https://www.sawe.org/product/paper-3758},
year = {2020},
date = {2020-07-01},
booktitle = {2020 SAWE Tech Fair},
pages = {25},
publisher = {Society of Allied Weight Engineers, Inc.},
address = {Virtual Conference},
abstract = {In this paper, a topology optimization methodology for the minimum weight of the composite stiffened panel with the constraint on the criticial buckling load is presented. An existing finite element solver [1] for the analysis of the stiff- ened tow steered composite panels is extended to perform the topology optimiza- tion for the minimum weight. The panel and the stiffeners are modelled using 3 node traingular Classical Laminate Plate elements (CLPT) and 2 node timoshenko beam elements, respectively. To achieve the independent meshing of the plate and stringers, the Lagrange multiplier based on a weak formulation of the continuity requirements between the plate elements and the beam elements is used. For a specific critical buckling load, the optimum topology of the stiffeners in the stiff- ened composite panel depends not only on the stiffeners but also on the fiber patten of the composite panel. Therefore, design variables corrosponding to both fiber pattern in the skin and stiffeners needs to be considered. Manufacturing mesh ap- proach presented in [1], is used to define the design variables corrosponding to the fiber pattern. The ground structure method is implemented to optimize stringers topology. The cross-sectional area of the stringers in the ground structure are de- fined as the design variables corrosponding to the stiffeners. To perform the robust the optimization, the analytical gradients of the buckling load and the weight of the stiffened panel with respect to design variables are implemented and verified using finite difference. The optimization for the minimum weight is performed for the varied complexities of the ground structures with the constraints on the critical buckling load.},
keywords = {22. Weight Engineering - Structural Design, 27. Weight Reduction - Materials, Student Papers},
pubstate = {published},
tppubtype = {inproceedings}
}
2017
@inproceedings{3679,
title = {3679. Design and Optimization of an Aluminum Structure Assembled by Elastic Fastening},
author = {Clément Laverne and Alain Desrochers and Ahmed Maslouhi},
url = {https://www.sawe.org/product/paper-3679},
year = {2017},
date = {2017-05-01},
booktitle = {76th Annual Conference, Montreal, Canada},
pages = {26},
publisher = {Society of Allied Weight Engineers, Inc.},
address = {Montreal, Canada},
abstract = {Actual research tends to replace some steel structures by aluminum ones, leading to a better resistance to corrosion and mass reduction, for example in automobile frames, bridge decks, in the navy and in aeronautical fields. These structural decks are often welded, which need tools and labor, hence the idea of an assembly based on a fastening.This technology consists in an elastic deformation of the male part of the structure to fit into the female part by a springback of the material. This kind of assembly has the advantage to be quickly set up, with little labor and without any intermediate component. However, the elastic fastening introduces a mechanical weakness of the structure insofar as this technology is based on an important elastic deformation of an area of the part to enable the insertion.That is why the main issue of this project is to design and dimension an extruded aluminum structure assembled by an elastic fastening in order to withstand loads defined by the specifications of a bus floor while minimizing mass.Firstly, the general geometry of the deck has been chosen among several patterns usually used in aluminum structures thanks to a finite element study of their mechanical behavior exposed to loads defined by the specifications. The chosen pattern is composed of tilted stiffeners between two plates. Then, the Gauss- Newton method of optimization has been realized to calculate the optimal set of geometric parameters of the stiffeners. The four parameters to optimize were the gaps between the stiffeners, their angle and their length while the functions to minimize were the stresses and strains of typical loading conditions and the standards found in buses specifications. After that, the thicknesses have been dimensioned by a loop based on the dichotomy principle to respect the specifications. These operations were realized with an interface between Matlab and Ansys. Finally, the thickness of the deformable part of the fastening has been calculated with a simple analytical model to enable the insertion.An experimental approach with a prototype was included to validate the results of the optimization and the dimensioning by a measurement of stresses and deflections on critical points and to compare the welding, the bounding and the elastic fastening.},
keywords = {22. Weight Engineering - Structural Design, Student Papers},
pubstate = {published},
tppubtype = {inproceedings}
}
@inproceedings{3680,
title = {3680. Designing Mass-Optimized Parts Using Solidthinking Inspire with Application to the Hyperloop Deployable Wheel System},
author = {Graeme Klim and Dr. Seyed M. Hashemi},
url = {https://www.sawe.org/product/paper-3680},
year = {2017},
date = {2017-05-01},
booktitle = {76th Annual Conference, Montreal, Canada},
pages = {25},
publisher = {Society of Allied Weight Engineers, Inc.},
address = {Montreal, Canada},
abstract = {Today's automotive and aerospace engineers are often faced with conflicting design goals; design for low cost or low weight. While advancements in aerospace materials, such as carbon fiber composites, have allowed engineers to design lighter parts, the cost to manufacture these parts is still very high. Similarly, recent advancements in additive manufacturing demonstrate an ability to produce lightweight, stiff structures, with a promise of future economic benefits including fuel savings, a result of optimized production part design. To realize additive manufacturing's benefits as they pertain to weight savings, design engineers must re-examine their approach to part and product design. This well-known challenge to improve the state of current design methods is being addressed through a 'design for additive manufacturing' movement that remains an ongoing subject of interest in the additive manufacturing and design communities. The present paper demonstrates the use of the industrial software tool, solidThinking Inspire, as a preliminary study and detail design weight reduction tool for additive manufacturing. To illustrate the software's usefulness, a primary structural component of the Hyperloop Deployable Wheel System, developed at Ryerson University, was selected for optimization, and designed for additive metal manufacturing production. The significant weight savings and material savings realized are presented while the potential for fast design, development and production of the part are highlighted in a step-by-step process.},
keywords = {22. Weight Engineering - Structural Design, 34. Advanced Design, Student Papers},
pubstate = {published},
tppubtype = {inproceedings}
}
2016
@inproceedings{3655,
title = {3655. Weight and Structural Optimization in Aircraft Design},
author = {William Alves and Juliana Silva},
url = {https://www.sawe.org/product/paper-3655},
year = {2016},
date = {2016-05-01},
booktitle = {75th Annual Conference, Denver, Colorado},
pages = {30},
publisher = {Society of Allied Weight Engineers, Inc.},
address = {Denver, Colorado},
abstract = {Given the competitiveness of the current market, there is a growing movement in the sense of increase the efficiency of aeronautical product in an appropriate life cycle for airliners needs.
In the context of aeronautical structures, the challenge is to increase structural efficiency within the number of cycles required for life in service, meeting reliability requirements and loads, without losing sight of the dynamic performance of structural components.
This article is intended to present the main structural optimization techniques and estimating the gains made at various stages of development of the aircraft design.},
keywords = {10. Weight Engineering - Aircraft Design, 22. Weight Engineering - Structural Design, 28. Weight Reduction - Processes, 34. Advanced Design},
pubstate = {published},
tppubtype = {inproceedings}
}
In the context of aeronautical structures, the challenge is to increase structural efficiency within the number of cycles required for life in service, meeting reliability requirements and loads, without losing sight of the dynamic performance of structural components.
This article is intended to present the main structural optimization techniques and estimating the gains made at various stages of development of the aircraft design.2014
@inproceedings{3616,
title = {3616. Methodology For Lightweight Design Of Stiffened Skin In Advanced Aerospace Structures},
author = {August Noevere},
url = {https://www.sawe.org/product/paper-3616},
year = {2014},
date = {2014-05-01},
booktitle = {73rd Annual Conference, Long Beach, California},
pages = {18},
publisher = {Society of Allied Weight Engineers, Inc.},
address = {Long Beach, California},
abstract = {With increased interest in paradigm-shifting aerospace vehicles, such as those with a blended wing-body configuration or mostly composite structures, it is necessary to develop structural design methods that will help these concepts reach their full potential. Many traditional design methods are only suited for traditional aerospace structures. With the introduction of advanced vehicle geometry and materials, the dimensionality of design problems for advanced structures becomes quite cumbersome. The presented methodology uses a reformulation of the typical mass minimization problem to limit the number of design variables in the design of a stiffened skin panel. Typically, the mass minimization problem definition for structural design is a function of the physical dimensions of the stiffened panels. In the new minimization problem discussed here, the equivalent smeared stiffness terms of the panels become the design variables. For a finite element model with a fixed number of elements, this reformulation provides a consistent number of design variables regardless of the stiffened panel concept used in the design exploration. The reduction in design variables is made possible by the introduction of response surface methodology to map from the stiffness terms to the mass and margins of safety for the stiffened panel. To generate the response surface equations that represent mass and margin of safety, a precursory design of experiments is run to collect the necessary data. The presented methodology creates a design environment which is suited to the large-scale design exploration needed for considerations such as the placement of internal structural members or the tailoring of composites for aeroelasticity challenges.},
keywords = {22. Weight Engineering - Structural Design},
pubstate = {published},
tppubtype = {inproceedings}
}
2011
@inproceedings{3535,
title = {3535. Innovative Design with Bi-Level Topology Optimization},
author = {Alain Remouchamps and Michael Bruyneel and Stephane Grihon and Glaude Fleury},
url = {https://www.sawe.org/product/paper-3535},
year = {2011},
date = {2011-05-01},
booktitle = {70th Annual Conference, Houstion, Texas},
pages = {10},
publisher = {Society of Allied Weight Engineers, Inc.},
address = {Houston, Texas},
abstract = {Starting from results obtained in the topology optimization of two Airbus pylons, this paper proposes an innovative bi-level optimization scheme used to solve multidisciplinary optimization problems including aerodynamics (drag) and structure (mass, stiffness) requirements. The drag related to the pylon fairing depends on some global geometric design variables. For a given geometry, the minimal mass is obtained by solving a topology optimization problem with stiffness (displacement) restrictions. Mass and drag feed a cost function which is minimized with a surrogate-based optimization approach. The developed methodology is demonstrated for the multidisciplinary optimization of the Airbus pylon.},
keywords = {22. Weight Engineering - Structural Design},
pubstate = {published},
tppubtype = {inproceedings}
}
2009
@inproceedings{3467,
title = {3467. Weight Analytics},
author = {Chuck Higgins},
url = {https://www.sawe.org/product/paper-3467},
year = {2009},
date = {2009-05-01},
booktitle = {68th Annual Conference, Wichita, Kansas},
pages = {13},
address = {Wichita, Kansas},
abstract = {Weight Analytics addresses the gathering, analyzing, reporting and sharing of critical weight data and opening new horizons for the use of this knowledge within the design process. In this paper we will show the use of a cubical data base, allowing the user to look at an infinite number of dimensions of data quickly, easily and intuitively. Automation of the collection, storage, analysis and reporting on this disparate data has until now been challenging at the least. With the flexibility of the Rubix Cube, data is quickly and easily sliced and diced along any number of
relationships thus 'elevating data to knowledge.'},
keywords = {10. Weight Engineering - Aircraft Design, 18. Weight Engineering - Spacecraft Design, 22. Weight Engineering - Structural Design},
pubstate = {published},
tppubtype = {inproceedings}
}
relationships thus 'elevating data to knowledge.'2007
@inproceedings{3409,
title = {3409. Landing Gear Mass Prediction. A Combined Analytic and Parametric Approach},
author = {Adrian Harrison and Sidney Smith and Edward Kay and Evangelos Vekris},
url = {https://www.sawe.org/product/paper-3409},
year = {2007},
date = {2007-05-01},
booktitle = {66th Annual Conference, Madrid, Spain},
pages = {20},
publisher = {Society of Allied Weight Engineers},
address = {Madrid, Spain},
organization = {Society of Allied Weight Engineers},
abstract = {Current parametric methods for landing gear mass prediction are based on relationships derived from existing aircraft and landing gear mass data. They can provide good results using minimal input and effort, although the resulting mass predictions are inherently linked to the design assumptions of legacy aircraft. Also, the methods cannot be used to perform trade studies that would be useful at early stages of the aircraft design process (e.g., landing gear mass vs. shock-absorber stroke, or vs. material choice). Analytic methods attempt to approximate the landing gear design process by calculating loads to size initial structural concepts. They require more detailed data than parametric methods and simplified structures are assumed that can exclude some important details. Also, it is difficult to predict robust values of overall gear weight from an idealized structural weight synthesized by this process. However, analytic methods can be used to perform early trade studies. This paper reviews the progress towards a combined analytic and parametric method that employs the benefits of both approaches. The analysis process starts from a set of data that would typically be available at early stages of the design process and uses an iterative sequence that aims to provide reliable predictions of landing gear mass. The method attempts to simulate the landing gear design process in enough detail to provide an early concept phase mass prediction.},
keywords = {22. Weight Engineering - Structural Design, 23. Weight Engineering - Structural Estimation},
pubstate = {published},
tppubtype = {inproceedings}
}
2006
@inproceedings{3389,
title = {3389. Managing Common Data Across Multiple Platforms},
author = {Kathleen Tolman and Peter Kniesel},
url = {https://www.sawe.org/product/paper-3389},
year = {2006},
date = {2006-05-01},
booktitle = {65th Annual Conference, Valencia, California},
pages = {24},
publisher = {Society of Allied Weight Engineers},
address = {Valencia, California},
organization = {Society of Allied Weight Engineers},
abstract = {The Size, Weight, Power and Cooling (SWaP-C) attributes of common equipment in the Future Combat System (FCS) Program must be standardized in content and availability throughout all the platform Integrated Product Teams (IPTs). Under a traditional program-management approach, SWaP-C data would be informally managed and tracked by each vehicle platform IPT individually. But in the case of FCS–a highly decentralized program where development is proceeding at multiple geographic sites– such an approach posed potential risks. The results of employing a traditional approach to SWaP management, especially over several years of performance, could have included confusion about reporting responsibility, inconsistent use of the latest available estimates, and an environment in which IPTs would not maximize opportunities to share data and avoid duplication of tasks. To avoid such problems, a multi step approach has been instituted for FCS. Control of the data was assigned to a single, non-vehicle affiliated IPT (System of Systems Engineering and Integration (SSEI)), using a standard dataflow process and a dedicated, central, database. This approach provided a single source for all program SWaP-C Data with program wide visibility and unanimous IPT buy-in. The solution proved to be stable and effective, reducing confusion and inconsistent reporting practices. The processes described in this paper are uniquely applicable to System of Systems integration problems where complex, multi-product programs share common elements that need to be tracked in a central, visible manner by a Lead System Integrator.},
keywords = {12. Weight Engineering - Computer Applications, 22. Weight Engineering - Structural Design},
pubstate = {published},
tppubtype = {inproceedings}
}
@inproceedings{3392,
title = {3392. Weight Considerations in the Design of a Low Cost Interceptor},
author = {Robert Austin and Andrew Brown and Kiel Carreau and Ted Garbeff and Chris Kearney and Keven Lutke and Teresa Quinliven and Kristi Stavros},
year = {2006},
date = {2006-05-01},
booktitle = {65th Annual Conference, Valencia, California},
pages = {-1},
publisher = {Society of Allied Weight Engineers},
address = {Valencia, California},
organization = {Society of Allied Weight Engineers},
abstract = {The Vortex Pirates aircraft design team has chronicled the weight considerations in the preliminary design of a low cost interceptor. The process began with the derivation of an initial sizing relationship based on weights of similar aircraft adjusted for payload, and continued through the structural design and weight validation. The potential benefits and limitations of active c.g. management were investigated for a small aircraft with cranked arrow wing that caused large movements in the aerodynamic center. Validated weights were then used to investigate the effects of weight on cost and performance, resulting in the establishment of linear relationships. These relationships should be confirmed with varying configurations and more detailed mass properties; however, they are believed to be of sufficient accuracy for conceptual design. While this study focused on high performance fighters in the less than 30,000 pound (13,636 kg) clean takeoff weight class, it should serve as a roadmap for weights engineers new to the conceptual design process.},
note = {Student Team "Vortex Pirates" from California Polytechnic State University, San Luis Obispo
Paper Missing},
keywords = {22. Weight Engineering - Structural Design},
pubstate = {published},
tppubtype = {inproceedings}
}
@inproceedings{3393,
title = {3393. Avari: Structure and Weight Considerations for the Design of a Homeland Defense Interceptor},
author = {Julie Perata and Brian Greiner and Bradley Jensen and Kit Mailen and Brian Miracle and Zach Nichols and Seth Pace and Sarah Tucker},
url = {https://www.sawe.org/product/paper-3393},
year = {2006},
date = {2006-05-01},
booktitle = {65th Annual Conference, Valencia, California},
pages = {30},
publisher = {Society of Allied Weight Engineers},
address = {Valencia, California},
organization = {Society of Allied Weight Engineers},
abstract = {Avari is a Homeland Defense Interceptor designed to meet the 2005-2006 AIAA Undergraduate Team Aircraft Design Competition RFP. Avari uses the maximum amount of existing technologies possible to minimize the overall cost. As the cost is repeatedly highlighted by the RFP, this became a major design driver. To meet this cost, the selections of low-cost and easily manufactured materials was a high priority along with minimizing the overall aircraft weight, as most aircraft are ?bought by the pound.? The large loiter section of the Combat-Air Patrol mission created a large fuel requirement, which created a large empty weight. Notable requirements that are met include takeoff and landing distances less than 8,000 feet, a loiter time greater than 4 hours, a dash speed greater than 2.2, and a flyaway cost of under $15 million. Materials, maintenance, manufacturing, and cost are kept minimal by using existing technology and low part counts.},
note = {Student Team Ävari" from California Polytechnic State University, San Luis Obispo},
keywords = {22. Weight Engineering - Structural Design},
pubstate = {published},
tppubtype = {inproceedings}
}
@inproceedings{3394,
title = {3394. Structural Weight Considerations of a Low Cost High Speed Interceptor},
author = {Benjamin Bickley and Laura Bunker and Kelly Dahl and Joe Gotzler and Dave Hueftle and Ryan Huthmacher and Dan Richardson},
url = {https://www.sawe.org/product/paper-3394},
year = {2006},
date = {2006-05-01},
booktitle = {65th Annual Conference, Valencia, California},
pages = {33},
publisher = {Society of Allied Weight Engineers},
address = {Valencia, California},
organization = {Society of Allied Weight Engineers},
abstract = {In response to the 2005 AIAA Undergraduate RFP for a Homeland Defense Interceptor, Team Mothra presents Black Mamba. Black Mamba is a low cost, high speed aircraft capable of intercepting any airborne threat above domestic United States airspace. Black Mamba is capable of Mach 2.2 while being extremely cheap and reliable in the field. While supersonic capable, it also has the ability to loiter for up to 4 hours on internal fuel and then dash to a target, intercept, and cruise back while not undergoing aerial refueling. With such requirements, weight control is especially important. Black Mamba is approximately 29,000 pounds gross takeoff weight with 43% of that being fuel. A center-of-gravity control system is used to distribute the fuel in order to achieve the most suitable center-of-gravity location for control purposes. Black Mamba also includes advanced materials in its construction. Composite material accounts for approximately 35% of the structural weight. Despite the large non-recurring costs of using composites, the advantages of unitization, reduced part count, larger buy- to-fly ratio, and larger maintenance intervals ensure a cheaper and more reliable structure in the long term than a conventional aluminum aircraft. With the advanced technology already available today, Black Mamba is designed to last well into this century in defending U.S. airspace.},
note = {Student Team "Mothra" from California Polytechnic State University, San Luis Obispo},
keywords = {22. Weight Engineering - Structural Design},
pubstate = {published},
tppubtype = {inproceedings}
}
@inproceedings{3395,
title = {3395. Revenant: A Weight And Structural Approach To The Design Of A Homeland Defense Interceptor},
author = {Jessica Lemm and Chris Marino and Laura Mendez and Scott Miknus and Ben Piper and Brian Ross and William Tamayo},
url = {https://www.sawe.org/product/paper-3395},
year = {2006},
date = {2006-05-01},
booktitle = {65th Annual Conference, Valencia, California},
pages = {36},
publisher = {Society of Allied Weight Engineers},
address = {Valencia, California},
organization = {Society of Allied Weight Engineers},
abstract = {The goal of this report is to present team Sentinel Solutions? direction to the American Institute of Aeronautics and Astronautics request for proposal for the 2005- 2006 Undergraduate Team Aircraft Design Competition. The challenge was to design a Homeland Defense Interceptor capable of a Mach 2.2 dash, 4 hour combat air patrol endurance, and meet a flyaway cost for 1,000 aircraft of $15 million each. The Revenant, a team designed interceptor, has several notable and special qualities that make it a winning candidate for the competition. These include a 45},
note = {Student Team "Sentinel Solutions" from California Polytechnic State University, San Luis Obispo},
keywords = {22. Weight Engineering - Structural Design},
pubstate = {published},
tppubtype = {inproceedings}
}
2005
@inproceedings{3359,
title = {3359. Weight and Balance Considerations for Unmanned Combat Aerial Vehicles},
author = {California Polytechnic State University},
url = {https://www.sawe.org/product/paper-3359},
year = {2005},
date = {2005-05-01},
booktitle = {64th Annual Conference, Annapolis, Maryland},
pages = {23},
publisher = {Society of Allied Weight Engineers, Inc.},
address = {Annapolis, Maryland},
abstract = {Sentinel Aerospace presents Cavalier, a ship-based morphing unmanned combat aerial vehicle (UCAV), in response to the 2004 ? 2005 American Institute of Aeronautics and Astronautics (AIAA) Graduate Team Aircraft Design Competition. Cavalier uses a combination of speed, stealth, and maneuverability to perform the suppression of enemy air defenses (SEAD) mission. The profile includes a 200 nautical mile cruise segment and a four hour loiter followed by a 0.757 Mach dash to the target area where four AGM-88 HARM missiles are to be expended, and a 5 g maneuver to egress the threat area. The alternate mission, which is also required, involves the same mission profile, but without engaging the enemy target. Cavalier effectively uses several forms of morphing on the wing. As the plane is to takeoff and land on LHA ships, a span limitation of 48 feet exists. Therefore, Cavalier uses shape memory alloy-actuated folding wingtips that extend after takeoff, and provide an additional 8.2 feet of span on each wing. Pivoting leading edge strakes are used to adjust planform area, mean sweep and thickness-to-chord for the different flight conditions. Hinge-less ailerons, based on the Smart Wing Program, will be employed to provide roll control while improving the radar cross-section. During the course of this investigation, it was realized that substantial savings could be achieved if morphing was applied to the propulsion system as well. The use of technology derived from the Smart Aircraft and Marine ProjectS demonstratiON (SAMPSON) was found to reduce the installation losses, in turn improving specific fuel consumption and net thrust. Additional morphing system concepts will be discussed that could yield a significant increase in performance. However, research and technology projects are still being conducted to determine a reasonable figure for benefits and penalties from these systems. As such, credit for these concepts has not been applied to the current configuration.},
keywords = {22. Weight Engineering - Structural Design, 33. Unmanned Vehicles, Student Papers},
pubstate = {published},
tppubtype = {inproceedings}
}
@inproceedings{3361,
title = {3361. Developments of Composite Manufacturing Technologies at NLR},
author = {Bert Thuis},
url = {https://www.sawe.org/product/paper-3361},
year = {2005},
date = {2005-05-01},
booktitle = {64th Annual Conference, Annapolis, Maryland},
pages = {36},
publisher = {Society of Allied Weight Engineers, Inc.},
address = {Annapolis, Maryland},
abstract = {Over the last two decades the use of fiber reinforced composites in secondary and primary aircraft structures has increased tremendously. The weight savings that were realized by applying composites in stead of metals used to be one of the main drivers to apply these materials. However, nowadays a reduction in fabrication and maintenance costs is becoming more and more important.
The objective therefore is to combine cost effective fabrication methods with lightweight structural concepts in order bring the exploitation of composite materials to a higher level. The autoclave process used to be the standard fabrication technique to produce composite components for the aerospace industry. Recent developments show the evolution of new cost efficient fabrication techniques and of composite materials for these new techniques. One of these (for the aerospace) relatively new fabrication methods is pressurized Resin Transfer Moulding (RTM). The RTM fabrication concept is based on the injection of resin into a mould cavity containing dry fibers (preform). During the injection process, air in the mould is being replaced by resin and the fibers are impregnated. For pressurized RTM normally matched die concepts are being used. Although these matched die tools can be complex and expensive, RTM has several major advantages compared to autoclave processing:
? Components can be made within very tight dimensional tolerances. This means that during assembly of the components no or a very limited amount of shimming is required.
? Components can be made (nearly) net shaped. This means that the amount of trimming and milling activities after curing of the component can be reduced.
? Components can be made with a high level of part integration. This means the cost savings can be realized during assembly.
? Thick complex shaped components can be made. This means that components can be designed in composite that would be impossible or very cumbersome to make by autoclave processing (e.g. landing gear components).
Over the last decade the National Aerospace Laboratory NLR in the Netherlands has contributed to the development of pressurized RTM technology by participating to a wide variety of application driven research projects. These programs were carried out in close collaboration with the industry in order to make sure that innovations made, keep lined-up with the requirement specifications of the structural components te be developed.
The present paper presents an overview of a number of composite RTM prototypes that were developed by NLR over the last ten years. These are:
? Bracket for the Ariane V launcher
In this project, techniques for preform manufacturing like stitching and bindering were evaluated. Also, design rules for concentrated load introduction were developed
? Composite cargo door for an Airbus A320 type of aircraft
In this project combining the pre-preg technology with resin injection principles developed a novel manufacturing technique. A manufacturing process was developed in which a cargo door including doorstops, pin locks and hinges was manufactured in one single production cycle
? Integrated beam concepts
In this project, the integration of brackets as well as net shaped fabrication issues were Addressed
? NH-90 composite trailing arm
In this project injection strategies were developed, braiding was evaluated, exothermal peaks were dealt with and new RTM tooling concepts were generated.
? Composite fuselage frames for an A320 sized aircraft
In this project, in which a large series of fuselage frames were manufactured, the issue of high production rates was addressed.},
keywords = {22. Weight Engineering - Structural Design},
pubstate = {published},
tppubtype = {inproceedings}
}
The objective therefore is to combine cost effective fabrication methods with lightweight structural concepts in order bring the exploitation of composite materials to a higher level. The autoclave process used to be the standard fabrication technique to produce composite components for the aerospace industry. Recent developments show the evolution of new cost efficient fabrication techniques and of composite materials for these new techniques. One of these (for the aerospace) relatively new fabrication methods is pressurized Resin Transfer Moulding (RTM). The RTM fabrication concept is based on the injection of resin into a mould cavity containing dry fibers (preform). During the injection process, air in the mould is being replaced by resin and the fibers are impregnated. For pressurized RTM normally matched die concepts are being used. Although these matched die tools can be complex and expensive, RTM has several major advantages compared to autoclave processing:
? Components can be made within very tight dimensional tolerances. This means that during assembly of the components no or a very limited amount of shimming is required.
? Components can be made (nearly) net shaped. This means that the amount of trimming and milling activities after curing of the component can be reduced.
? Components can be made with a high level of part integration. This means the cost savings can be realized during assembly.
? Thick complex shaped components can be made. This means that components can be designed in composite that would be impossible or very cumbersome to make by autoclave processing (e.g. landing gear components).
Over the last decade the National Aerospace Laboratory NLR in the Netherlands has contributed to the development of pressurized RTM technology by participating to a wide variety of application driven research projects. These programs were carried out in close collaboration with the industry in order to make sure that innovations made, keep lined-up with the requirement specifications of the structural components te be developed.
The present paper presents an overview of a number of composite RTM prototypes that were developed by NLR over the last ten years. These are:
? Bracket for the Ariane V launcher
In this project, techniques for preform manufacturing like stitching and bindering were evaluated. Also, design rules for concentrated load introduction were developed
? Composite cargo door for an Airbus A320 type of aircraft
In this project combining the pre-preg technology with resin injection principles developed a novel manufacturing technique. A manufacturing process was developed in which a cargo door including doorstops, pin locks and hinges was manufactured in one single production cycle
? Integrated beam concepts
In this project, the integration of brackets as well as net shaped fabrication issues were Addressed
? NH-90 composite trailing arm
In this project injection strategies were developed, braiding was evaluated, exothermal peaks were dealt with and new RTM tooling concepts were generated.
? Composite fuselage frames for an A320 sized aircraft
In this project, in which a large series of fuselage frames were manufactured, the issue of high production rates was addressed.2004
@inproceedings{3331,
title = {3331. Prediction of Fracture Damage in and Reliability Based Design Optimization of Composite Structures},
author = {Godines and Frank Abdi},
url = {https://www.sawe.org/product/paper-3331},
year = {2004},
date = {2004-05-01},
urldate = {2004-05-01},
booktitle = {63rd Annual Conference, Newport, California},
pages = {22},
publisher = {Society of Allied Weight Engineers, Inc.},
address = {Newport, California},
abstract = {A simplified composite analytical life prediction procedure (SAPGEN) is developed for naval joint design that will perform: material constituent analysis (MCA), material uncertainty analysis (MUA), fracture damage, and the percent contribution of each material constituent to failure mechanisms. SAPGEN has the ability to predict: 1) constituent/ply mechanical properties, 2) property degradation, 3) damage modes and mechanisms, 4) failure modes and mechanisms, 5) percent damages due to fourteen specified failure criteria and, 6) the durability/reliability of a composite joint/structure. The progressive failure analysis (PFA) methodology imbedded within SAPGEN utilizes finite element analyses (FEA) and iteratively updates material properties due to the existing loading conditions. The applied load (force, temperature, pressure, etc.) or time is iteratively increased, permitting damage tracking throughout the structure for many loading scenarios. SAPGEN predicts failure mechanisms relevant to composite structures, such as delamination, with simplified finite element models. As a demonstration, SAPGEN was used to determine damage modes within a typical naval joint and compared to test results and current detailed analytical methods.},
keywords = {22. Weight Engineering - Structural Design},
pubstate = {published},
tppubtype = {inproceedings}
}
@inproceedings{3333,
title = {3333. The Development of Composite Landing Gear Components for Aerospace Applications},
author = {Bert G. S. J Thuis},
url = {https://www.sawe.org/product/paper-3333},
year = {2004},
date = {2004-05-01},
booktitle = {63rd Annual Conference, Newport, California},
pages = {21},
publisher = {Society of Allied Weight Engineers, Inc.},
address = {Newport, California},
abstract = {Composites are being used increasingly for structural components for aircraft and space applications because of their superior specific strength and stiffness properties in comparison to aluminum and steel. The weight savings that were realized by applying composites used to be one of the main drivers to apply these materials. However, nowadays a reduction in fabrication cost is becoming important as well. The objective, therefore, is to combine new cost effective fabrication methods with lightweight structural concepts in order bring the exploitation of composite materials to a higher level.
Up to now, the autoclave process is the standard fabrication technique to produce composite components for the aerospace industry. Recent developments show the evolution of new cost efficient fabrication techniques and of composite materials for these new techniques. One of these (for the aerospace) new fabrication methods is Resin Transfer Moulding (RTM). The RTM fabrication concept is based on the injection of resin into a mould cavity containing dry fibers (preform). During the injection process, air in the mould is being replaced by resin and the fibers are impregnated. Although RTM tooling can be complex and expensive, RTM has several advantages compared to autoclave processing. One of these advantages is that thick complex shaped components can be made that would be very cumbersome or even impossible to make by autoclave processing. This means that designers now can design composite components as replacements for components made with metal forging.
In the framework of several technology programs the Structures Technology Department as part of the Aerospace Vehicles division of NLR developed several composite landing gear components for a large military helicopter and a fighter aircraft. These programs were carried out in close collaboration with the landing gear manufacturer, SP aerospace and vehicle systems. The targets of the programs were to achieve not only weight reductions of 20% but also to reduce the manufacturing costs by 15% and to achieve a reduction in lead-time.
Several different landing gear components were fabricated successfully by RTM and tested. All tested landing gear components failed beyond their required failure load levels. All program targets were met.
This paper will present an overview of the design concepts of these composite landing gear components. The RTM tooling concepts and the RTM manufacturing set-ups will be described and a brief overview of the test results will be given.
Based on the results achieved, composite landing gear components are now considered to be feasible for application in next generation civil and military aircraft.},
keywords = {22. Weight Engineering - Structural Design},
pubstate = {published},
tppubtype = {inproceedings}
}
Up to now, the autoclave process is the standard fabrication technique to produce composite components for the aerospace industry. Recent developments show the evolution of new cost efficient fabrication techniques and of composite materials for these new techniques. One of these (for the aerospace) new fabrication methods is Resin Transfer Moulding (RTM). The RTM fabrication concept is based on the injection of resin into a mould cavity containing dry fibers (preform). During the injection process, air in the mould is being replaced by resin and the fibers are impregnated. Although RTM tooling can be complex and expensive, RTM has several advantages compared to autoclave processing. One of these advantages is that thick complex shaped components can be made that would be very cumbersome or even impossible to make by autoclave processing. This means that designers now can design composite components as replacements for components made with metal forging.
In the framework of several technology programs the Structures Technology Department as part of the Aerospace Vehicles division of NLR developed several composite landing gear components for a large military helicopter and a fighter aircraft. These programs were carried out in close collaboration with the landing gear manufacturer, SP aerospace and vehicle systems. The targets of the programs were to achieve not only weight reductions of 20% but also to reduce the manufacturing costs by 15% and to achieve a reduction in lead-time.
Several different landing gear components were fabricated successfully by RTM and tested. All tested landing gear components failed beyond their required failure load levels. All program targets were met.
This paper will present an overview of the design concepts of these composite landing gear components. The RTM tooling concepts and the RTM manufacturing set-ups will be described and a brief overview of the test results will be given.
Based on the results achieved, composite landing gear components are now considered to be feasible for application in next generation civil and military aircraft.@inproceedings{3336,
title = {3336. Composite Materials for Structural Landing Gear Components On CD-R},
author = {Sijpkes and Vergouwen},
url = {https://www.sawe.org/product/paper-3336},
year = {2004},
date = {2004-05-01},
booktitle = {63rd Annual Conference, Newport, California},
pages = {7},
publisher = {Society of Allied Weight Engineers, Inc.},
address = {Newport, California},
abstract = {Although the use of fiber reinforced composite materials in landing gear applications has been under investigation for several years, until now this technology had not reached the maturity status of clearance for flight in primary structural application in landing gears. Due to the ever increasing demands on low weight and low life cycle cost, SP aerospace identified composite technology for use in landing gears as very promising in the medium to long term. Therefore a technology development program was started to show the feasibility of composite materials in this application. This program was partly funded by the Dutch government. To assure maturation of this technology up to its final stages, the decision was made to continue development up to full flight clearance qualification, validated by actual flight testing.
SP aerospace has established a Technology Roadmap to guide the technology development process. One of the appointed key elements is 'Affordable Light Weight Components.' Within this technology area, SP aerospace has been active in developing material applications for landing gears both in Polymer Matrix Composite (PMC) and in Titanium Matrix Composite (TiMMC). To be able to compare the performance of both the PMC and TiMMC applications, the lower drag brace of the F-16 main landing gear was used as a reference component. This structural landing gear component is manufactured in ultra high strength steel (for the heavy-weight version of the F-16). The PMC technology development program resulted January 2001 in the world?s first flight of a structural PMC component in a landing gear. In June of 2003 the world?s first flight for a TiMMC component was accomplished.},
keywords = {22. Weight Engineering - Structural Design},
pubstate = {published},
tppubtype = {inproceedings}
}
SP aerospace has established a Technology Roadmap to guide the technology development process. One of the appointed key elements is 'Affordable Light Weight Components.' Within this technology area, SP aerospace has been active in developing material applications for landing gears both in Polymer Matrix Composite (PMC) and in Titanium Matrix Composite (TiMMC). To be able to compare the performance of both the PMC and TiMMC applications, the lower drag brace of the F-16 main landing gear was used as a reference component. This structural landing gear component is manufactured in ultra high strength steel (for the heavy-weight version of the F-16). The PMC technology development program resulted January 2001 in the world?s first flight of a structural PMC component in a landing gear. In June of 2003 the world?s first flight for a TiMMC component was accomplished.@inproceedings{3339,
title = {3339. Topology Optimization for Weight Reduction During Preliminary Design},
author = {Harold Thomas},
url = {https://www.sawe.org/product/paper-3339},
year = {2004},
date = {2004-05-01},
booktitle = {63rd Annual Conference, Newport, California},
pages = {11},
publisher = {Society of Allied Weight Engineers, Inc.},
address = {Newport, California},
abstract = {Weight reduction of current designs can be achieved through sizing optimization by reducing thicknesses with constraints on strength, stiffness, and frequency. Unfortunately, the weight reduction is usually just a few percent. A more effective approach to weight reduction is to define an optimum topology (layout) during the preliminary design stage. For example, three small diagonal reinforcement ribs may be more effective than two large horizontal ribs if the load path is diagonal. Another example is the number, size, and location of lightening holes. If the number and location of these holes is predetermined, weight reduction can only be achieved through changing the size of the holes. Much greater weight reduction can be achieved if the correct number of holes in the correct locations and of the correct sizes is used. In this paper a finite element based structural topology optimization software program, Altair OptiStruct?, is used to determine optimum layouts for aerospace, automotive, and consumer goods structures. This software program determines optimum topologies of components subject to weight, stiffness, and frequency limits. Examples will be shown and the weight reduction and cost benefits discussed. The impact of manufacturing constraints, such as stamping die and casting mold removal, will be discussed. In addition, the optimal design of stamped ribs in sheet metal structures (topography optimization) will be introduced. By using mathematical optimization techniques in conjunction with finite element based structural analysis, the optimal topology and topography of designs can be achieved. By using this approach during the preliminary design phase, significant weight and cost reductions can be achieved.},
keywords = {22. Weight Engineering - Structural Design},
pubstate = {published},
tppubtype = {inproceedings}
}
@inproceedings{3344,
title = {3344. Stormcrow: Considerations of Weight and Structure in the Design of an Advanced Tactical Tanker/Transport},
author = {California Polytechnic State University},
url = {https://www.sawe.org/product/paper-3344},
year = {2004},
date = {2004-05-01},
booktitle = {63rd Annual Conference, Newport, California},
pages = {20},
publisher = {Society of Allied Weight Engineers, Inc.},
address = {Newport, California},
abstract = {In response to Boeing?s request for proposal (RFP) for a tactical tanker/transport aircraft, Ninja Aerospace presents Stormcrow. This aircraft is capable of fulfilling the dual mission requirements set forth in the RFP and takes into account the call for increased survivability. The cargo bay of Stormcrow can accommodate all interim combat brigade vehicles as well as other oversized cargo loadings, with a 70,000 lb cargo capacity. A dual probe/drogue refueling boom, and the ability to fly from 100 knots to above 0.8 Mach allows Stormcrow to refuel any aircraft in the U.S. inventory. Through use of externally blown flaps and robust landing gear, Stormcrow can land at austere airfields with less than 2,000 feet of runway. By employing cascade style thrust reversers, Stormcrow boasts ground maneuverability exceeding that of the C-17 Globemaster III. With a wingspan comparable to that of a C-130, Stormcrow can deliver more payload to smaller airfields for greatly increased throughput. The cargo bay is can be configured for vehicles, personnel or aero-medical uses, to make this a truly versatile aircraft. Through creative shaping and configuration choices, the Stormcrow tactical transport has an average radar return of currently operational non low-observable fighters, greatly reducing the amount of electronic countermeasures needed to mask its presence when in harm?s way. Use of a saw-edged wing, canted H-tail, and fuselage chine, contribute to lower radar cross-section (RCS). Radar absorbing materials (RAM) have been used sparingly to reduce cost, weight, and avoid the high maintenance of such material. Cost and maintenance were foremost throughout the design process. The end result is Stormcrow, a highly versatile aircraft that can be developed and deployed at a reasonable cost to fulfill the military needs for advanced tanker/transports.},
keywords = {22. Weight Engineering - Structural Design, Student Papers},
pubstate = {published},
tppubtype = {inproceedings}
}