SAWE Technical Papers
Technical Library
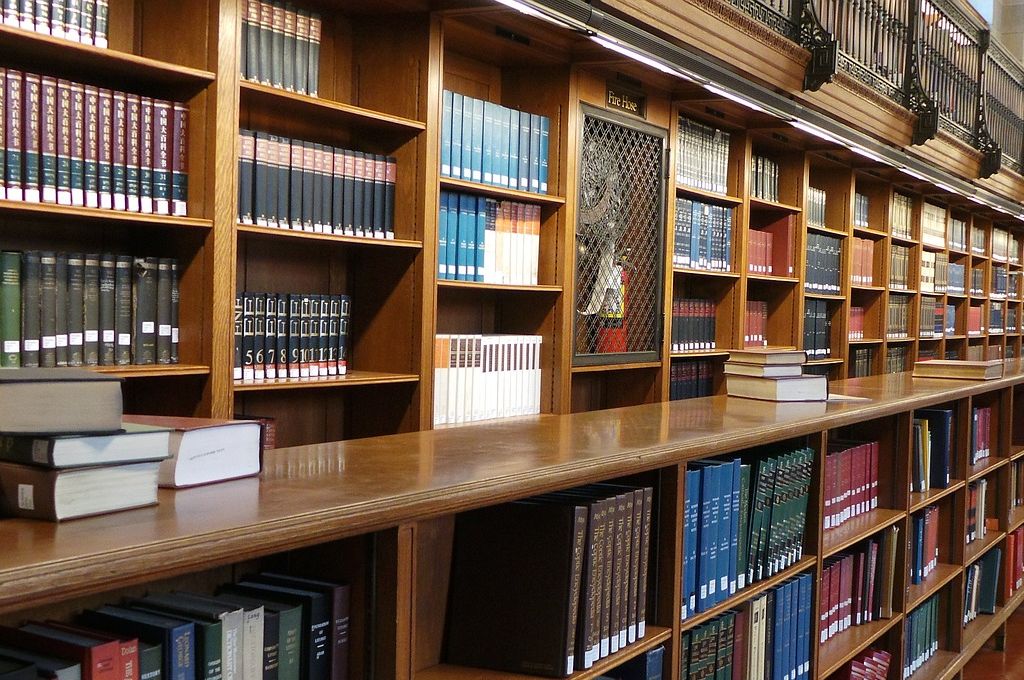
SAWE Paper Database
The SAWE Technical Library contains nearly 4000 technical papers available here for purchase and download. Use the search options below to find what you need.
Previati, Giorgio; Mastinu, Gianpiero; Gobbi, Massimiliano In: 2020 SAWE Tech Fair, pp. 14, Society of Allied Weight Engineers, Inc., Virtual Conference, 2020. Abstract | Buy/Download | BibTeX | Tags: 06. Inertia Measurements, 09. Weighing Equipment 3727. Trifilar Pendulum: Non-small Oscillations and Calibration Previati, Giorgio In: 78th Annual Conference, Norfolk, VA, pp. 16, Society of Allied Weight Engineers, Inc., Norfolk, Virginia, 2019. Abstract | Buy/Download | BibTeX | Tags: 06. Inertia Measurements 3728. Investigation on the Mass Properties of Cars Previati, Giorgio In: 78th Annual Conference, Norfolk, VA, pp. 14, Society of Allied Weight Engineers, Inc., Norfolk, Virginia, 2019. Abstract | Buy/Download | BibTeX | Tags: 05. Inertia Calculations, 06. Inertia Measurements Johnston, Brittany In: 78th Annual Conference, Norfolk, VA, pp. 6, Society of Allied Weight Engineers, Inc., Norfolk, Virginia, 2019. Abstract | Buy/Download | BibTeX | Tags: 06. Inertia Measurements Otlowski, Daniel In: 77th Annual Conference, Irving, Texas, pp. 64, Society of Allied Weight Engineers, Inc., Irving, Texas, 2018. Abstract | Buy/Download | BibTeX | Tags: 06. Inertia Measurements 3691. Methods to Evaluate the Mass Properties of a Scale Model Aircraft Kohtanen, Eetu; Davis, R. Benjamin In: 76th Annual Conference, Montreal, Canada, pp. 12, Society of Allied Weight Engineers, Inc., Montreal, Canada, 2017. Abstract | Buy/Download | BibTeX | Tags: 06. Inertia Measurements, 08. Weighing, 11. Weight Engineering - Aircraft Estimation, Student Papers 3610. Inertia Uncertainity of a Moored FPSO Chandrasekaran, Santhosh Kumar; Schuster, Andreas In: 73rd Annual Conference, Long Beach, California, pp. 13, Society of Allied Weight Engineers, Inc., Long Beach, California, 2014. Abstract | Buy/Download | BibTeX | Tags: 06. Inertia Measurements, 35. Weight Engineering - Offshore, Marine 3612. Measurement of the Inertia Tensor - A Review Previati, Giorgio; Gobbi, M.; Mastinu, G. In: 73rd Annual Conference, Long Beach, California, pp. 23, Society of Allied Weight Engineers, Inc., Long Beach, California, 2014. Abstract | Buy/Download | BibTeX | Tags: 05. Inertia Calculations, 06. Inertia Measurements, 32. Product of Inertia Measurement 3624. A Unique Method of Measuring Road Vehicle Moments of Inertia and Centre of Gravity Watson, Jim In: 73rd Annual Conference, Long Beach California, pp. 16, Society of Allied Weight Engineers, Inc., Long Beach, California, 2014. Abstract | Buy/Download | BibTeX | Tags: 06. Inertia Measurements 3625. Methods For Representing Conditions On A Weight Database Bjòrhovde, Stein In: 73rd Annual Conference, Long Beach California, pp. 17, Society of Allied Weight Engineers, Inc., Long Beach, California, 2014. Abstract | Buy/Download | BibTeX | Tags: 06. Inertia Measurements 3603. Mass Property Measurements Of The Mars Science Laboratory Rover Fields, Keith In: 72nd Annual Conference, St. Louis, Missouri, pp. 16, Society of Allied Weight Engineers, Inc., Saint Louis, Missouri, 2013. Abstract | Buy/Download | BibTeX | Tags: 06. Inertia Measurements, 07. Section Properties 3500. Technical Feasibility Study for the Measurement of the Inertia Properties of an Aircraft Previati, Giorgio; Mastinu, G.; Gobbi, M. In: 69th Annual Conference, Virginia Beach, Virginia, pp. 21, Society of Allied Weight Engineers, Inc., Virginia Beach, Virginia, 2010. Abstract | Buy/Download | BibTeX | Tags: 03. Center Of Gravity, 06. Inertia Measurements, 32. Product of Inertia Measurement 3507. A Practical Method to Improve Moment of Inertia Measurement Accuracy for Formosat-3 Satellites HUNG, HENG-CHUAN In: 69th Annual Conference, Virginia Beach, Virginia, pp. 10, Society of Allied Weight Engineers, Inc., Virginia Beach, Virginia, 2010. Abstract | Buy/Download | BibTeX | Tags: 06. Inertia Measurements 3457. How Mass Properties Affect Satellite Attitude Control Boynton, Richard In: 67th Annual Conference, Seattle, Washington, pp. 21, Seattle, Washington, 2008. Abstract | Buy/Download | BibTeX | Tags: 06. Inertia Measurements, 18. Weight Engineering - Spacecraft Design 3460. Using a Two-Plane Spin Balance Instrument to Balance a Satellite Rotor About Its Own Bearings Kennedy, Paul; Otlowski, Daniel; Rathbun, Brandon; Wiener, Kurt In: 67th Annual Conference, Seattle, Washington, pp. 21, Seattle, Washington, 2008, (Mike Hackney Best Paper Award). Abstract | Buy/Download | BibTeX | Tags: 06. Inertia Measurements, 18. Weight Engineering - Spacecraft Design, Mike Hackney Best Paper Award Pennati, M.; Mastinu, G.; Gobbi, M. In: 66th Annual Conference, Madrid, Spain, pp. 22, Society of Allied Weight Engineers Society of Allied Weight Engineers, Madrid, Spain, 2007. Abstract | Buy/Download | BibTeX | Tags: 06. Inertia Measurements 3396. Improve Your Sensor Image with Balance Otlowski, Daniel; Wiener, Kurt In: 65th Annual Conference, Valencia, California, pp. 53, Society of Allied Weight Engineers Society of Allied Weight Engineers, Valencia, California, 2006. Abstract | Buy/Download | BibTeX | Tags: 06. Inertia Measurements 3354. The Role of Mass Properties Measurement In The Space Mission Wiener, Kurt In: 64th Annual Conference, Annapolis, Maryland, pp. 14, Society of Allied Weight Engineers, Inc., Annapolis, Maryland, 2005. Abstract | Buy/Download | BibTeX | Tags: 06. Inertia Measurements 3325. Mass Properties Measurement in the X-38 Project Peterson, Wayne L. In: 63rd Annual Conference, Newport, California, pp. 26, Society of Allied Weight Engineers, Inc., Newport, California, 2004, (L. R. 'Mike' Hackney Award). Abstract | Buy/Download | BibTeX | Tags: 06. Inertia Measurements, Mike Hackney Best Paper Award 3340. Design of an Engine Inertia Measuring Device McGarry,; Guenther,; Andreatta,; Heydinger, In: 63rd Annual Conference, Newport, California, pp. 10, Society of Allied Weight Engineers, Inc., Newport, California, 2004. Abstract | Buy/Download | BibTeX | Tags: 06. Inertia Measurements2020
@inproceedings{3753,
title = {3753. Theoretical and Experimental Evaluation of the Flexibility of the Test Rig on Inertia Property Measurement},
author = {Giorgio Previati and Gianpiero Mastinu and Massimiliano Gobbi},
url = {https://www.sawe.org/product/paper-3753},
year = {2020},
date = {2020-07-01},
booktitle = {2020 SAWE Tech Fair},
pages = {14},
publisher = {Society of Allied Weight Engineers, Inc.},
address = {Virtual Conference},
abstract = {In the measurement of inertia properties (mass, centre of gravity and inertia tensor), both the body under investigation and the test rig are commonly considered as rigid bodies. However, in case of heavy or large bodies, these assumptions may not be satisfied. The present paper deals with the consequences of the test rig structure deformations on the measured inertia parameters. In fact, if the forces exchanged by the structure of the test rig and the body are large, the structure may deform changing its geometry and dynamic behavior. These effects, in turn, affect the measured kinematic and dynamic quantities needed for the measurement of the inertia properties.In the paper, by considering the InTenso+ Measuring System of the Politecnico di Milano, a special type of multi-filar pendulum, the effects of the deformation of the test rig on the measurement of the inertia properties is investigated both numerically and experimentally. A flexible multibody model is employed to understand the dynamic effects of the deformations on the mass properties measurement. Several bodies are measured to validate such analyses. A proper mathematical procedure is then derived to measure the inertia properties of bodies when the realization of a sufficiently stiff structure is impractical.},
keywords = {06. Inertia Measurements, 09. Weighing Equipment},
pubstate = {published},
tppubtype = {inproceedings}
}
2019
@inproceedings{3727,
title = {3727. Trifilar Pendulum: Non-small Oscillations and Calibration},
author = {Giorgio Previati},
url = {https://www.sawe.org/product/paper-3727},
year = {2019},
date = {2019-05-01},
booktitle = {78th Annual Conference, Norfolk, VA},
pages = {16},
publisher = {Society of Allied Weight Engineers, Inc.},
address = {Norfolk, Virginia},
abstract = {The trifilar pendulum is a well-known and established technique for the measurement of the moment of inertia of rigid bodies. For such application, the motion off the pendulum, which is inherently nonlinear, is considered linear. As consequences, only small oscillations and pendula with long cables with respect to their distance should be employed for the measurement. However, in some application either to use non- small oscillation angles or to use pendulum with relative short cables have to be employed. In these cases, the motion cannot be considered linear and some error in the measurement could arise.This paper aims to analyze the nonlinear motion off the pendulum. A formula is analytically derived for the calibration of the pendulum for non-small rotation angles. A sensitivity analysis is proposed to highlight the advantages of the proposed approach to the measurement of the moment of inertia of relatively smalll and compact bodies, such as tires and engines, and to full scale vehicles and airplanes.},
keywords = {06. Inertia Measurements},
pubstate = {published},
tppubtype = {inproceedings}
}
@inproceedings{3728,
title = {3728. Investigation on the Mass Properties of Cars},
author = {Giorgio Previati},
url = {https://www.sawe.org/product/paper-3728},
year = {2019},
date = {2019-05-01},
booktitle = {78th Annual Conference, Norfolk, VA},
pages = {14},
publisher = {Society of Allied Weight Engineers, Inc.},
address = {Norfolk, Virginia},
abstract = {The knowledge of the mass properties (center off gravity location and inertia tensor) of cars is crucial for the analysis of their dynamic performances. The measurement of such properties is not always performed and their value is estimated by 3D models off some empirical formula. In this paper, the mass properties off cars are investigated by analyzing the measurements performed at tthe Politecnico di Milano. The measurements have been realized by the InTenso+ test rig off the Politecnico di Milano in the period from 2000 to 2018. The test rig is basically a multi-bar pendulum carrying the body under investigation and oscillating from well-known initial conditions. By means of a proper mathematical procedure, the mass properties of the body are accurately measured in a very short testing time.The obtained measures are statistically analyzed and correlations are found with easily accessible vehicle data. On the basis of such correlations, formulae are proposed to have a quick and reasonable estimation of the most relevant mass parameters (center of gravity, heights and diagonal terms of the inertia tensor) of any vehicle.},
keywords = {05. Inertia Calculations, 06. Inertia Measurements},
pubstate = {published},
tppubtype = {inproceedings}
}
@inproceedings{3730,
title = {3730. Path to be an Engineer},
author = {Brittany Johnston},
url = {https://www.sawe.org/product/paper-3730},
year = {2019},
date = {2019-05-01},
booktitle = {78th Annual Conference, Norfolk, VA},
pages = {6},
publisher = {Society of Allied Weight Engineers, Inc.},
address = {Norfolk, Virginia},
abstract = {This is an unconventional Society of Allied Weight Engineers (SAWE) student conference paper that gives insight of how a person can have the will power to navigate on a journey of obtaining a new career. Becoming an engineer is far from easy, but it is possible to obtain. I take that possibility with positivity that enables me to make the great strides that I must complete. This paper gives insight to who I am and why I must make this change.},
keywords = {06. Inertia Measurements},
pubstate = {published},
tppubtype = {inproceedings}
}
2018
@inproceedings{3700,
title = {3700. On Techniques for Correcting Entrained Air Errors during MOI Measurement of Aircraft Control Surfaces},
author = {Daniel Otlowski},
url = {https://www.sawe.org/product/paper-3700},
year = {2018},
date = {2018-05-01},
booktitle = {77th Annual Conference, Irving, Texas},
pages = {64},
publisher = {Society of Allied Weight Engineers, Inc.},
address = {Irving, Texas},
abstract = {Knowing the true mass properties of aircraft control surfaces is critical to preventing aerodynamic flutter, a condition that can result in the loss of flight control or outright airframe failure. As the aircraft industry turns to a greater use of composites in airframe construction, layup variations in material density and manufacturing techniques result in as-built deviations from the mass distribution calculated in the CAD model. These moment of inertia (MOI) deviations can be up to 10%, thereby increasing the need to verify MOI of control surfaces through physical measurement.Control surface MOI measurements are subject to errors when the measurements are conducted in air. Errors in air measurements are principally caused by entrained air. This virtually-attached air adds apparent mass to the control surface and anomalously increases the control surface's measured MOI. Typical MOI errors range from 5% to 25% of the control surface's MOI.Concentrating on entrained air errors, this paper examines viable methods of error correction. Further refined by test article requirements, the methods are evaluated both experimentally and analytically. Application strategies are then developed, and expected outcomes are predicted. Lastly, a new gravity driven horizontal axis instrument, complete with its own novel error compensation, is introduced and compared to a variety of measurement and correction techniques.},
keywords = {06. Inertia Measurements},
pubstate = {published},
tppubtype = {inproceedings}
}
2017
@inproceedings{3691,
title = {3691. Methods to Evaluate the Mass Properties of a Scale Model Aircraft},
author = {Eetu Kohtanen and R. Benjamin Davis},
url = {https://www.sawe.org/product/paper-3691},
year = {2017},
date = {2017-05-01},
booktitle = {76th Annual Conference, Montreal, Canada},
pages = {12},
publisher = {Society of Allied Weight Engineers, Inc.},
address = {Montreal, Canada},
abstract = {Scale model ditching tests are sometimes conducted to study the loads and dynamic behavior associated with an aircraft during water impact. To ensure scalability of the results, the model's mass properties including weight, center of gravity, and pitch moment of inertia in particular must proportionally reflect the characteristics of the full-scale aircraft. This paper presents the experimental methods used to evaluate these mass characteristics for a 1/20th scale Gulfstream G550 model prior to ditching tests conducted at the University of Georgia. These methods can be used for any similarly sized model.To determine the center of gravity the aircraft model is placed on a v-block assembly resting on three force transducers arranged in an isosceles triangle formation. The model's center of gravity along longitudinal and lateral axes is found by summing moments about a known reference axes system using the static forces measured at each transducer. To find the vertical center of gravity, the model is rotated about its longitudinal axis in a v-block fixture, and the force readings along the projection of the rotated plane are then manipulated.For pitch inertia, a compound pendulum is used to measure the aircraft's period of oscillation which is related to the inertia about the axis of oscillation through an analytical method [1]. The inertia of the pendulum apparatus by itself is then subtracted from the total experimental inertia, and the parallel axis theorem is used to determine the model's pitch inertia about its center of gravity. To evaluate the accuracy of the pendulum method, aluminum and steel brackets with known mass properties are attached to the model's tail, and the pitch inertia is measured again for each bracket. The increase in inertia is then compared against the theoretical increase.},
keywords = {06. Inertia Measurements, 08. Weighing, 11. Weight Engineering - Aircraft Estimation, Student Papers},
pubstate = {published},
tppubtype = {inproceedings}
}
2014
@inproceedings{3610,
title = {3610. Inertia Uncertainity of a Moored FPSO},
author = {Santhosh Kumar Chandrasekaran and Andreas Schuster},
url = {https://www.sawe.org/product/paper-3610},
year = {2014},
date = {2014-05-01},
booktitle = {73rd Annual Conference, Long Beach, California},
pages = {13},
publisher = {Society of Allied Weight Engineers, Inc.},
address = {Long Beach, California},
abstract = {This paper will address weight requirements t o ensure the delivered mass inertia properties match the initial estimates used for model testing and hydrodynamic performance assessment. It has been assumed that the large dead weight of an FPSO makes the design insensitive to variances in mass inertia over the design cycle. As hydrodynamic engineers improve their mooring design performance and reduce margins, minor changes in mass inertia can have dramatic impact on system response. This paper will compare the mass inertia estimating, uncertainty and detailed calculation with mooring performance to determine optimum thresholds for weight control to mitigate the risk of changes in inertia.},
keywords = {06. Inertia Measurements, 35. Weight Engineering - Offshore, Marine},
pubstate = {published},
tppubtype = {inproceedings}
}
@inproceedings{3612,
title = {3612. Measurement of the Inertia Tensor - A Review},
author = {Giorgio Previati and M. Gobbi and G. Mastinu},
url = {https://www.sawe.org/product/paper-3612},
year = {2014},
date = {2014-05-01},
booktitle = {73rd Annual Conference, Long Beach, California},
pages = {23},
publisher = {Society of Allied Weight Engineers, Inc.},
address = {Long Beach, California},
abstract = {This paper is focused on the measurement of the full inertia tensor of a rigid body. In the literature, many papers can be found addressing this problem. Basically, two different measurement approaches are used.
In the first approach, different moments of inertia around different axes are measured and then the inertia tensor is reconstructed from these measurements. In this case, the measurement of the moment of inertia around a given axis can be performed with very high accuracy. In the reconstruction of the inertia tensor is, however, some uncertainty is introduced due to the positioning of the rotation axes with respect to the body.
The second measurement approach involves the realization of a test rig able to apply a complex motion to the body under investigation. By a proper measurement of the motion and a suitable mathematical procedure, is possible to derive all the components components of the inertia tensor from a single experiment. Sometimes, the motion is reduced to a vibration of small amplitude and the inertia tensor is derived from a modal analysis.
The experimental techniques referring to such two strategies are presented and the underlying theoretical and mathematical aspects involved are discussed.},
keywords = {05. Inertia Calculations, 06. Inertia Measurements, 32. Product of Inertia Measurement},
pubstate = {published},
tppubtype = {inproceedings}
}
In the first approach, different moments of inertia around different axes are measured and then the inertia tensor is reconstructed from these measurements. In this case, the measurement of the moment of inertia around a given axis can be performed with very high accuracy. In the reconstruction of the inertia tensor is, however, some uncertainty is introduced due to the positioning of the rotation axes with respect to the body.
The second measurement approach involves the realization of a test rig able to apply a complex motion to the body under investigation. By a proper measurement of the motion and a suitable mathematical procedure, is possible to derive all the components components of the inertia tensor from a single experiment. Sometimes, the motion is reduced to a vibration of small amplitude and the inertia tensor is derived from a modal analysis.
The experimental techniques referring to such two strategies are presented and the underlying theoretical and mathematical aspects involved are discussed.@inproceedings{3624,
title = {3624. A Unique Method of Measuring Road Vehicle Moments of Inertia and Centre of Gravity},
author = {Jim Watson},
url = {https://www.sawe.org/product/paper-3624},
year = {2014},
date = {2014-05-01},
booktitle = {73rd Annual Conference, Long Beach California},
pages = {16},
publisher = {Society of Allied Weight Engineers, Inc.},
address = {Long Beach, California},
abstract = {In order for vehicle manufacturers to design their vehicles with accurate test data a technique has been developed and used extensibly to measure the moments of inertia (MOI) and centre of gravity (CoG) for a wide range of vehicles. The rig which was designed and built at Cranfield University uses a reverse pendulum methodology. This is in contrast to other methods of measuring inertia which supports the vehicle or object from the ceiling.
Essentially, a vehicle is supported by its chassis and allowed to float on an air bearing and rotate, in a frictionless manner, in three degrees of freedom. The motion of the vehicle is configured to move in one axis of rotation, pitch, roll or yaw. A pair of linear springs is then introduced and simple harmonic motion of the vehicle is obtained by applying small amplitudes. The vehicle oscillates against the springs and the time interval is recorded. From the time period of one oscillation, the inertia for the vehicle and rig with any supporting structures can be calculated. To determine the inertia of the vehicle only, the rig and supporting structure inertia are subtracted.
The inertia is defined about the centre of gravity of the vehicle which is obtained by performing a different test. The vehicle is tilted to small angles up-to 2 degrees and the force required to maintain the vehicle at equilibrium with the angle of rotation is measured at various degrees of tilt. This test is performed in pitch and roll to provide verification of results.
This paper describes the background to the equations derived for calculations, features of the rig which have arisen from over 25 years of testing with this unique methodology and details of the software used.},
keywords = {06. Inertia Measurements},
pubstate = {published},
tppubtype = {inproceedings}
}
Essentially, a vehicle is supported by its chassis and allowed to float on an air bearing and rotate, in a frictionless manner, in three degrees of freedom. The motion of the vehicle is configured to move in one axis of rotation, pitch, roll or yaw. A pair of linear springs is then introduced and simple harmonic motion of the vehicle is obtained by applying small amplitudes. The vehicle oscillates against the springs and the time interval is recorded. From the time period of one oscillation, the inertia for the vehicle and rig with any supporting structures can be calculated. To determine the inertia of the vehicle only, the rig and supporting structure inertia are subtracted.
The inertia is defined about the centre of gravity of the vehicle which is obtained by performing a different test. The vehicle is tilted to small angles up-to 2 degrees and the force required to maintain the vehicle at equilibrium with the angle of rotation is measured at various degrees of tilt. This test is performed in pitch and roll to provide verification of results.
This paper describes the background to the equations derived for calculations, features of the rig which have arisen from over 25 years of testing with this unique methodology and details of the software used.@inproceedings{3625,
title = {3625. Methods For Representing Conditions On A Weight Database},
author = {Stein Bjòrhovde},
url = {https://www.sawe.org/product/paper-3625},
year = {2014},
date = {2014-05-01},
booktitle = {73rd Annual Conference, Long Beach California},
pages = {17},
publisher = {Society of Allied Weight Engineers, Inc.},
address = {Long Beach, California},
abstract = {This paper will look into several conditions that can appear in a weight control project and where all of them need calculation of weight and center of gravity as a variant of the standard lightweight calculation at point of completion. Requirements and wishes for a weight control system to handle these conditions will be discussed and addressed against methods and solutions.},
keywords = {06. Inertia Measurements},
pubstate = {published},
tppubtype = {inproceedings}
}
2013
@inproceedings{3603,
title = {3603. Mass Property Measurements Of The Mars Science Laboratory Rover},
author = {Keith Fields},
url = {https://www.sawe.org/product/paper-3603},
year = {2013},
date = {2013-05-01},
booktitle = {72nd Annual Conference, St. Louis, Missouri},
pages = {16},
publisher = {Society of Allied Weight Engineers, Inc.},
address = {Saint Louis, Missouri},
abstract = {The NASA/JPL Mars Science Laboratory (MSL) spacecraft mass properties were measured on a spin balance table prior to launch. This paper discusses the requirements and issues encountered with the setup, qualification, and testing using the spin balance table, and the idiosyncrasies encountered with the test system. The final mass measurements were made in the Payload Hazardous Servicing Facility (PHSF) at Kennedy Space Center on the fully assembled and fueled spacecraft. This set of environmental tests required that the control system for the spin balance machine be at a remote location, which posed additional challenges to the operation of the machine.},
keywords = {06. Inertia Measurements, 07. Section Properties},
pubstate = {published},
tppubtype = {inproceedings}
}
2010
@inproceedings{3500,
title = {3500. Technical Feasibility Study for the Measurement of the Inertia Properties of an Aircraft},
author = {Giorgio Previati and G. Mastinu and M. Gobbi},
url = {https://www.sawe.org/product/paper-3500},
year = {2010},
date = {2010-05-01},
booktitle = {69th Annual Conference, Virginia Beach, Virginia},
pages = {21},
publisher = {Society of Allied Weight Engineers, Inc.},
address = {Virginia Beach, Virginia},
abstract = {A feasibility study for the measurement of the inertia properties of a full-scale aircraft is presented. The employment of the InTenso+ system developed at Politecnico di Milano is discussed referring to the measurement of the inertia properties of a fighter aircraft. Preliminarily, the InTenso+ system is introduced to highlight its basic features. Then, referring to the addressed non standard aeronautic application, the accuracy of the measurement method is investigated. Both analytical and numerical analyses are presented to estimate the uncertainties of the measurement method. The measurement of the inertia properties of a full scale aircraft is technically feasible within the accuracy quantified in this report. Economic and financial issues are not critical, being the InTenso+ system very simple and consequently inexpensive (the implementation costs are not given in this paper as they depend on the customization of the system). The main result of this paper is that, maybe for the first time since the beginning of aeronautical engineering, the measurement of the full inertia tensor and of the location of the centre of gravity of aircrafts appears feasible in a simple way. Such a measurement can be performed by using the InTenso+ system.},
keywords = {03. Center Of Gravity, 06. Inertia Measurements, 32. Product of Inertia Measurement},
pubstate = {published},
tppubtype = {inproceedings}
}
@inproceedings{3507,
title = {3507. A Practical Method to Improve Moment of Inertia Measurement Accuracy for Formosat-3 Satellites},
author = {HENG-CHUAN HUNG},
url = {https://www.sawe.org/product/paper-3507},
year = {2010},
date = {2010-05-01},
booktitle = {69th Annual Conference, Virginia Beach, Virginia},
pages = {10},
publisher = {Society of Allied Weight Engineers, Inc.},
address = {Virginia Beach, Virginia},
abstract = {The 'FORMOSAT-3 Program' is an international collaboration project between Taiwan and the US with
joint efforts of Taiwan's National SPace Organization (NSPO) and University Corporation for
Atmospheric Research (UCAR) of the US. The primary FORMOSAT-3 mission is to launch a
constellation of six micro-satellites into Low-Earth Orbit (LEO) in altitude range 700 ~ 800 Km to
collect atmospheric data for weather prediction, atmospheric studies, space weather monitoring and
geodetic research. The satellites integration and test were completed at NSPO I&T Facility located in
Hsinchu, Taiwan.
The objective of this paper is to present the method developed at NSPO to improve Moment Of Inertia
(MOI) measurement accuracy for FORMOSAT-3 satellites. The Mass Properties Measurement Facility
(MPMF) at NSPO is designed for three axes mass properties measurement of satellite up to 1500 Kg.
The MPMF includes a 980 Kg weight L-Fixture for horizontal axes measurement. This 'huge'
L-Fixture greatly reduces the sensitivity of the MOI measurement for FORMOSAT-3 micro-satellites
each weighs only about 62 Kg. Redesign of a smaller L-Fixture is inevitable. However, the L-Fixture
is designed so that the test objective is well aligned with the MPMF, to manufacture a new one would be
too costly and too time consuming. Decision was made to design a smaller fixture without looking for
the alignment problem. The alignment problem is solved later when performing the measurement.
The Alignment Measurement Equipment is used to accurately identify the misalignment when the
satellite is installed in position for measurement. The misalignment data is then used to correct the
MOI data. Although the satellite installed with smaller fixture is not well aligned to the MPMF, the
misalignment is well measured. The MOI data can be accurately corrected with the alignment data.
The final results show that accuracy has been dramatically improved with this method.},
keywords = {06. Inertia Measurements},
pubstate = {published},
tppubtype = {inproceedings}
}
joint efforts of Taiwan's National SPace Organization (NSPO) and University Corporation for
Atmospheric Research (UCAR) of the US. The primary FORMOSAT-3 mission is to launch a
constellation of six micro-satellites into Low-Earth Orbit (LEO) in altitude range 700 ~ 800 Km to
collect atmospheric data for weather prediction, atmospheric studies, space weather monitoring and
geodetic research. The satellites integration and test were completed at NSPO I&T Facility located in
Hsinchu, Taiwan.
The objective of this paper is to present the method developed at NSPO to improve Moment Of Inertia
(MOI) measurement accuracy for FORMOSAT-3 satellites. The Mass Properties Measurement Facility
(MPMF) at NSPO is designed for three axes mass properties measurement of satellite up to 1500 Kg.
The MPMF includes a 980 Kg weight L-Fixture for horizontal axes measurement. This 'huge'
L-Fixture greatly reduces the sensitivity of the MOI measurement for FORMOSAT-3 micro-satellites
each weighs only about 62 Kg. Redesign of a smaller L-Fixture is inevitable. However, the L-Fixture
is designed so that the test objective is well aligned with the MPMF, to manufacture a new one would be
too costly and too time consuming. Decision was made to design a smaller fixture without looking for
the alignment problem. The alignment problem is solved later when performing the measurement.
The Alignment Measurement Equipment is used to accurately identify the misalignment when the
satellite is installed in position for measurement. The misalignment data is then used to correct the
MOI data. Although the satellite installed with smaller fixture is not well aligned to the MPMF, the
misalignment is well measured. The MOI data can be accurately corrected with the alignment data.
The final results show that accuracy has been dramatically improved with this method.2008
@inproceedings{3457,
title = {3457. How Mass Properties Affect Satellite Attitude Control},
author = {Richard Boynton},
url = {https://www.sawe.org/product/paper-3457},
year = {2008},
date = {2008-05-01},
booktitle = {67th Annual Conference, Seattle, Washington},
pages = {21},
address = {Seattle, Washington},
abstract = {The success of a satellite mission is highly dependent on the accuracy of the measurement of its mass properties before flight and the proper ballasting of the satellite to bring the mass properties within tight limits. Failure to properly control mass properties can result in the satellite tumbling end over end after launch, or quickly using up its thruster capacity in an attempt to point in the correct direction. Solar panels must continue to point toward the sun as the satellite orbits the earth. Telescopes must point earthward. Satellite attitude control systems generally consist of a closed loop of measurement and correction of the spacecraft's attitude such that it is constantly driven into its desired nominal orientation, effectively rejecting any disturbances imposed on the satellite, such as variations in the earth's magnetic field, nonspherical shape of the Earth, lunar and solar perturbations, drag of the residual atmosphere on the solar array, and solar radiation pressure, or by movement of mechanical parts within the satellite. This paper discusses the different means of attitude control: thrusters, momentum wheel, spin stabilization, gravity gradient stabilization, and magnetic field control, with emphasis on the relationship of mass properties to these control methods.},
keywords = {06. Inertia Measurements, 18. Weight Engineering - Spacecraft Design},
pubstate = {published},
tppubtype = {inproceedings}
}
@inproceedings{3460,
title = {3460. Using a Two-Plane Spin Balance Instrument to Balance a Satellite Rotor About Its Own Bearings},
author = {Paul Kennedy and Daniel Otlowski and Brandon Rathbun and Kurt Wiener},
url = {https://www.sawe.org/product/paper-3460},
year = {2008},
date = {2008-05-01},
booktitle = {67th Annual Conference, Seattle, Washington},
pages = {21},
address = {Seattle, Washington},
abstract = {This paper addresses the problem of statically and dynamically balancing a satellite, mounted antenna rotor supported on its own bearings, and driven by a motor in the satellite body. The satellite body is considered a stationary platform, (stator) for this procedure and is not part of the balancing problem. The antenna rotor is isolated and balanced independently while spinning on its own bearings. In order to measure the unbalance, a method is developed to utilize a two-plane vertical axis spin balance machine. Rather than using the gas bearing rotor of the measuring instrument and spinning the entire satellite, the satellite body (stator) is attached to the balancing machine table, which is held stationary, and the satellite 'rotor' is spun on its own bearings. Forces due to the unbalance are measured by the Spin Balance Machine force transducers. The method is compared to a similar procedure using a single plane spin balancer and to methods using 'work reversal' methods to balance the rotor by spinning the entire satellite. The accuracy of this procedure is compared to the basic balance capability of the spin balance instrument when used in the conventional manner.},
note = {Mike Hackney Best Paper Award},
keywords = {06. Inertia Measurements, 18. Weight Engineering - Spacecraft Design, Mike Hackney Best Paper Award},
pubstate = {published},
tppubtype = {inproceedings}
}
2007
@inproceedings{3414,
title = {3414. A Reconfigurable Body for Assessing the Uncertainties Related to the Measurement of Inertia Properties},
author = {M. Pennati and G. Mastinu and M. Gobbi},
url = {https://www.sawe.org/product/paper-3414},
year = {2007},
date = {2007-05-01},
booktitle = {66th Annual Conference, Madrid, Spain},
pages = {22},
publisher = {Society of Allied Weight Engineers},
address = {Madrid, Spain},
organization = {Society of Allied Weight Engineers},
abstract = {The paper presents the design of a reconfigurable body to be taken as the reference body for assessing the uncertainties related to the measurement of inertia properties of rigid bodies. The presented reconfigurable body can be used for the calibration of any rig for measuring the inertia properties of rigid bodies, particularly for the InTenso system of the Politecnico di Milano. The body is composed of a plate, three columns, and a set of masses (disks) that can be arranged in several ways. By changing the position of the columns and the number and the position of the disks along the columns, the mass, the center of gravity (C.G.) location, and the inertia tensor of the body can be modified in whichever fashion. The simple shape of the body components and the construction accuracy allow the difference between the actual inertia properties of the assembled body and the corresponding computed nominal values to be maintained within 0.10 %. The reconfigurable body mass can span from 120 to 500 kg and the diagonal components of the inertia tensor may vary between 9 and 100 kgm2.},
keywords = {06. Inertia Measurements},
pubstate = {published},
tppubtype = {inproceedings}
}
2006
@inproceedings{3396,
title = {3396. Improve Your Sensor Image with Balance},
author = {Daniel Otlowski and Kurt Wiener},
url = {https://www.sawe.org/product/paper-3396},
year = {2006},
date = {2006-05-01},
booktitle = {65th Annual Conference, Valencia, California},
pages = {53},
publisher = {Society of Allied Weight Engineers},
address = {Valencia, California},
organization = {Society of Allied Weight Engineers},
abstract = {This paper reviews the properties which inherently limit the image quality of a gimbal mounted optical imaging system. It further describes how image quality is degraded by external influences, particularly vibration, in the supporting vehicle. The primary emphasis is to quantify, through physical principals, and verify, through experimental demonstration, the degree of static balance required to minimize the detrimental effects of external vibration to an acceptable level. The effects of dynamic balancing will also be discussed. The principles developed for visible light optical systems carried by an Unmanned Air Vehicle (UAV) will be expanded, in a general way, to describe how these principles apply to infra red, ultra violet, and radar systems as well as variations to the requirements as a function of the vehicle on which they are mounted. This discussion will include manned aircraft, missiles, land vehicles and watercraft.},
keywords = {06. Inertia Measurements},
pubstate = {published},
tppubtype = {inproceedings}
}
2005
@inproceedings{3354,
title = {3354. The Role of Mass Properties Measurement In The Space Mission},
author = {Kurt Wiener},
url = {https://www.sawe.org/product/paper-3354},
year = {2005},
date = {2005-05-01},
booktitle = {64th Annual Conference, Annapolis, Maryland},
pages = {14},
publisher = {Society of Allied Weight Engineers, Inc.},
address = {Annapolis, Maryland},
abstract = {This paper outlines the requirements for a successful mass properties (MP) measurement program for space missions. It emphasizes the need for cooperation and coordination between the various mission groups in establishing the MP measurement requirements, tolerances equipment, & procedures necessary to meet mission objectives. The typical responsibilities of each group are outlined.
The paper also describes the capabilities and limitations of various specific state of the are MP instruments and methods available to measure the weight, center of gravity location (CG), moments of inertia (MOI), and products of inertia (POI) of spacecraft and subassemblies. These MP measuring instruments are compared with regard to the basic principals of measurement, accuracy, cost, and other characteristics. It will also provide guidelines for incorporating design features in the spacecraft to optimize the accuracy of MP measurements and ballasting to meet the design specifications.
Examples and design guidelines for locating fixtures are given along with methods and examples used to optimize the accuracy of MP measurements.},
keywords = {06. Inertia Measurements},
pubstate = {published},
tppubtype = {inproceedings}
}
The paper also describes the capabilities and limitations of various specific state of the are MP instruments and methods available to measure the weight, center of gravity location (CG), moments of inertia (MOI), and products of inertia (POI) of spacecraft and subassemblies. These MP measuring instruments are compared with regard to the basic principals of measurement, accuracy, cost, and other characteristics. It will also provide guidelines for incorporating design features in the spacecraft to optimize the accuracy of MP measurements and ballasting to meet the design specifications.
Examples and design guidelines for locating fixtures are given along with methods and examples used to optimize the accuracy of MP measurements.2004
@inproceedings{3325,
title = {3325. Mass Properties Measurement in the X-38 Project},
author = {Wayne L. Peterson},
url = {https://www.sawe.org/product/paper-3325},
year = {2004},
date = {2004-05-01},
booktitle = {63rd Annual Conference, Newport, California},
pages = {26},
publisher = {Society of Allied Weight Engineers, Inc.},
address = {Newport, California},
abstract = {This paper details the techniques used in measuring the mass properties for the X-38 family of test vehicles. The X-38 Project was a NASA internal venture in which a series of test vehicles were built in order to develop a Crew Return Vehicle (CRV) for the International Space Station. Three atmospheric test vehicles and one spaceflight vehicle were built to develop the technologies required for a CRV. The three atmospheric test vehicles have undergone flight-testing by a combined team from the NASA Johnson Space Center and the NASA Dryden Flight Research Center. The flight-testing was performed at Edwards Air Force Base in California. The X-38 test vehicles are based on the X-24A, which flew in the ?60s and ?70s. Scaled Composites, Inc. of Mojave, California, built the airframes and the vehicles were outfitted at the NASA Johnson Space Center in Houston, Texas. Mass properties measurements on the atmospheric test vehicles included weight and balance by the three-point suspension method, four-point suspension method, three load cells on jackstands, and on three in-ground platform scales. Inertia measurements were performed as well in which Ixx, Iyy, Izz, and Ixz were obtained. This paper describes each technique and the relative merits of each. The proposed measurement methods for an X-38 spaceflight test vehicle will also be discussed. This vehicle had different measurement challenges, but integrated vehicle measurements were never conducted. The spaceflight test vehicle was also developed by NASA and was scheduled to fly on the Space Shuttle before the project was cancelled.},
note = {L. R. 'Mike' Hackney Award},
keywords = {06. Inertia Measurements, Mike Hackney Best Paper Award},
pubstate = {published},
tppubtype = {inproceedings}
}
@inproceedings{3340,
title = {3340. Design of an Engine Inertia Measuring Device},
author = {McGarry and Guenther and Andreatta and Heydinger},
url = {https://www.sawe.org/product/paper-3340},
year = {2004},
date = {2004-05-01},
booktitle = {63rd Annual Conference, Newport, California},
pages = {10},
publisher = {Society of Allied Weight Engineers, Inc.},
address = {Newport, California},
abstract = {It is sometimes necessary to know the complete inertia matrix (three moments of inertia and three products of inertia) of an engine in order to tune the vibrational dynamics of the engine or the system to which it is added. Typically, one axis about which the moment of inertia is measured is the crankshaft axis, while the other two axes may be any other two mutually perpendicular axes. The device reported on here was designed to measure the components of the inertia matrix, as well as measure the center-of-gravity (CG) location. The CG location must be determined in order to measure the moments of inertia.
The device described here was designed for engines in the 200-700 lb range (100-300 kg). Other objects may also be measured, but there is a minimum size and weight below which accurate results cannot be obtained.},
keywords = {06. Inertia Measurements},
pubstate = {published},
tppubtype = {inproceedings}
}
The device described here was designed for engines in the 200-700 lb range (100-300 kg). Other objects may also be measured, but there is a minimum size and weight below which accurate results cannot be obtained.