SAWE Technical Papers
Technical Library
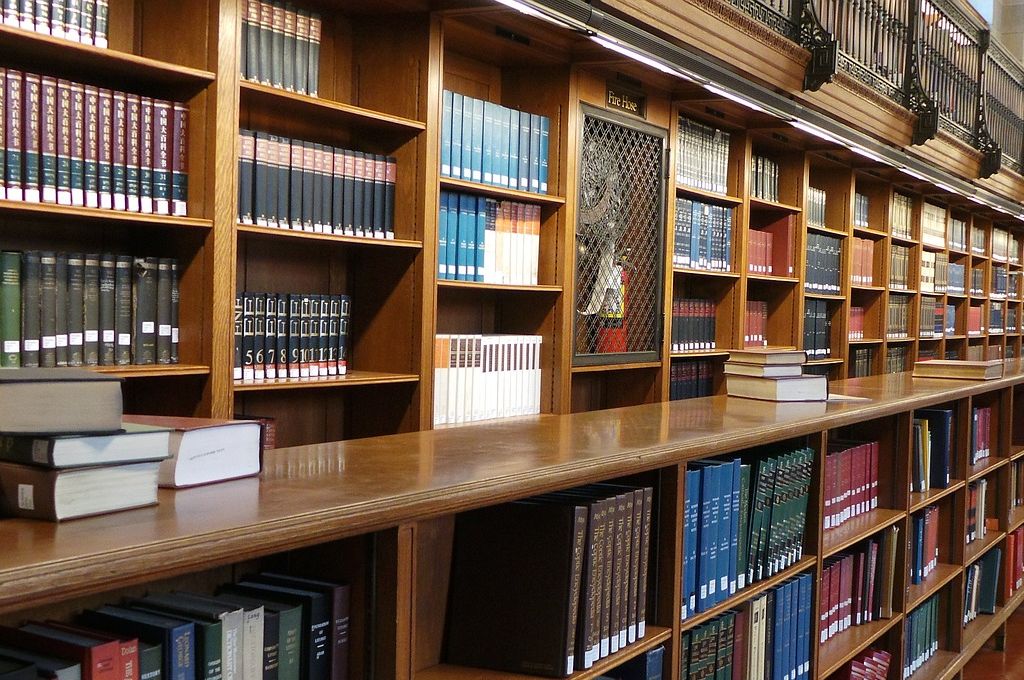
SAWE Paper Database
The SAWE Technical Library contains nearly 4000 technical papers available here for purchase and download. Use the search options below to find what you need.
3741. Finding the Balance Between Accuracy and Practicality in Deadweight Survey MacFarlane, Colin; Bucci, Manuela In: 2020 SAWE Tech Fair, pp. 24, Society of Allied Weight Engineers, Inc., Virtual Conference, 2020. Abstract | Buy/Download | BibTeX | Tags: 08. Weighing, 21. Weight Engineering - Statistical Studies, 35. Weight Engineering - Offshore, Marine 3691. Methods to Evaluate the Mass Properties of a Scale Model Aircraft Kohtanen, Eetu; Davis, R. Benjamin In: 76th Annual Conference, Montreal, Canada, pp. 12, Society of Allied Weight Engineers, Inc., Montreal, Canada, 2017. Abstract | Buy/Download | BibTeX | Tags: 06. Inertia Measurements, 08. Weighing, 11. Weight Engineering - Aircraft Estimation, Student Papers 3651. Reducing Variation during Actual Aircraft Weighing Rebhorn, Keith In: 75th Annual Conference, Denver, Colorado, pp. 15, Society of Allied Weight Engineers, Inc., Denver, Colorado, 2016. Abstract | Buy/Download | BibTeX | Tags: 08. Weighing 3631. Weighing the B-25 Classic Aircraft Johnston, J; Kleine, L; Pierson, J; Velasquez, V In: 74th Annual Conference, Alexandria, Virginia, pp. 8, Society of Allied Weight Engineers, Inc., Alexandria, Virginia, 2015. Abstract | Buy/Download | BibTeX | Tags: 08. Weighing 3638. Buoyancy Effects on Mass Properties Analysis Montgomery, J G In: 74th Annual Conference, Alexandria, Virginia, pp. 42, Society of Allied Weight Engineers, Inc., Alexandria, Virginia, 2015. Abstract | Buy/Download | BibTeX | Tags: 08. Weighing 3542. Optimization of Aircraft Weighing Results and Failure Investigation Lehnertz, Gregor In: 71st Annual Conference, Bad Gögging, Germany, pp. 14, Society of Allied Weight Engineers, Inc., Bad Gögging, Germany, 2012. Abstract | Buy/Download | BibTeX | Tags: 08. Weighing Schneider, Philipp; Thräne, Kai; Wenzl, Johann; Matthiesen, Sven In: 71st Annual Conference, Bad Gögging, Germany, pp. 31, Society of Allied Weight Engineers, Inc., Bad Gögging, Germany, 2012. Abstract | Buy/Download | BibTeX | Tags: 08. Weighing 3494. An Error Propagation Analysis of Small Engine Mass Properties Measurements Primozich, P. E. Anthony In: 69th Annual Conference, Virginia Beach, Virginia, pp. 16, Society of Allied Weight Engineers, Inc., Virginia Beach, Virginia, 2010. Abstract | Buy/Download | BibTeX | Tags: 03. Center Of Gravity, 08. Weighing, 17. Weight Engineering - Procedures 3456. Level or Not to Level: The Analysis of a Single Engine Weighing Process Kaufman, Johnathan In: 67th Annual Conference, Seattle, Washington, pp. 24, Seattle, Washington, 2008. Abstract | Buy/Download | BibTeX | Tags: 08. Weighing, 17. Weight Engineering - Procedures 3404. Weighing B747-400 Nose Up to Determine the Vertical Center of Gravity Pery, Asher In: 66th Annual Conference, Madrid, Spain, pp. 33, Society of Allied Weight Engineers Society of Allied Weight Engineers, Madrid, Spain, 2007. Abstract | Buy/Download | BibTeX | Tags: 03. Center Of Gravity, 08. Weighing 3434. Evaluation of Single Engine Weight and Center of Gravity Determination Methods Brown, Patrick In: 66th Annual Conference, Madrid, Spain, pp. 48, Society of Allied Weight Engineers Society of Allied Weight Engineers, Madrid, Spain, 2007. Abstract | Buy/Download | BibTeX | Tags: 08. Weighing 3397. Weight on Wheels: Software Development Kaufman, Johathan; Brown, Patrick In: 65th Annual Conference, Valencia, California, pp. 35, Society of Allied Weight Engineers Society of Allied Weight Engineers, Valencia, California, 2006. Abstract | Buy/Download | BibTeX | Tags: 08. Weighing 3384. Measuring Weight And Center Of Gravity Using Load Cells Hill, Brad In: 65th Annual Conference, Valencia, California, pp. 19, Society of Allied Weight Engineers Society of Allied Weight Engineers, Valencia, California, 2006, (Mike Hackney Best Paper Award). Abstract | Buy/Download | BibTeX | Tags: 08. Weighing, 09. Weighing Equipment, Mike Hackney Best Paper Award Brown, Patrick In: 64th Annual Conference, Annapolis, Maryland, pp. 23, Society of Allied Weight Engineers, Inc., Annapolis, Maryland, 2005. Abstract | Buy/Download | BibTeX | Tags: 08. Weighing 3371. Weighing a Vessel Without Hull Information and Without Placing the Vessel on Scales Martinez, Rosendo In: 64th Annual Conference, Annapolis, Maryland, pp. 15, Society of Allied Weight Engineers, Inc., Annapolis, Maryland, 2005. Abstract | Buy/Download | BibTeX | Tags: 08. Weighing 3147. Precise Measurement of Mass Boynton, Richard In: 60th Annual Conference, Arlington, Texas, May 19-23, pp. 32, Society of Allied Weight Engineers, Inc., Arlington, Texas, 2001. Abstract | Buy/Download | BibTeX | Tags: 08. Weighing 3149. Weight Verification of a Pressure Stabilized Vehicle McGill, Andrew V. In: 60th Annual Conference, Arlington, Texas, May 19-23, pp. 31, Society of Allied Weight Engineers, Inc., Arlington, Texas, 2001. Abstract | Buy/Download | BibTeX | Tags: 08. Weighing 3022. Uncertainty Analysis in Weighing Pressurized Vessels LeCong, Phung; Roy, Ricardo In: 59th Annual Conference, St. Louis, Missouri, June 5-7, pp. 10, Society of Allied Weight Engineers, Inc., St. Louis, Missouri, 2000. Abstract | Buy/Download | BibTeX | Tags: 08. Weighing 3029. Trinity Airweighs Weight and Balance System Nance, Kirk In: 59th Annual Conference, St. Louis, Missouri, June 5-7, pp. 14, Society of Allied Weight Engineers, Inc., St. Louis, Missouri, 2000. Abstract | Buy/Download | BibTeX | Tags: 08. Weighing 2455. Weighing a Beluga (A300-600ST) Nose Up to Determine the Vertical Center of Gravity Krautner, A In: 58th Annual Conference, San Jose, California, May 24-26, pp. 32, Society of Allied Weight Engineers, Inc., San Jose, California, 1999. Abstract | Buy/Download | BibTeX | Tags: 08. Weighing2020
@inproceedings{3741,
title = {3741. Finding the Balance Between Accuracy and Practicality in Deadweight Survey},
author = {Colin MacFarlane and Manuela Bucci},
url = {https://www.sawe.org/product/paper-3741},
year = {2020},
date = {2020-07-01},
booktitle = {2020 SAWE Tech Fair},
pages = {24},
publisher = {Society of Allied Weight Engineers, Inc.},
address = {Virtual Conference},
abstract = {Deadweight audits are exercises required to calculate the vessel lightweight by deduction from the actual ship weight. Depending on the size of the vessel, they can take a few hours to several days. Minimising the duration of the exercise should be prioritised since accuracy of the result is connected to avoidance of changes in the recorded vessel's configuration during the audit. This leads to a compromise between precision and the accuracy that can be achieved: estimating the weight of the deadweight based on experience is the quickest method, weighing everything with calibrated scales is the most precise. An intermediate solution is to find the deadweight partly with estimates, partly with weighing.Experience with all three of these methods showed that accuracy can be achieved even if relatively poor resolution is accepted, if some precautions are taken when recording the weights.This paper presents three study cases and the calculation of uncertainty in the deadweight that derived from the different approaches. The uncertainty and the time spent to complete the audit are used to define an efficiency estimator to rate the deadweight audit.The conclusion is a method to upgrade data recording that allows production of a more meaningful result.},
keywords = {08. Weighing, 21. Weight Engineering - Statistical Studies, 35. Weight Engineering - Offshore, Marine},
pubstate = {published},
tppubtype = {inproceedings}
}
2017
@inproceedings{3691,
title = {3691. Methods to Evaluate the Mass Properties of a Scale Model Aircraft},
author = {Eetu Kohtanen and R. Benjamin Davis},
url = {https://www.sawe.org/product/paper-3691},
year = {2017},
date = {2017-05-01},
booktitle = {76th Annual Conference, Montreal, Canada},
pages = {12},
publisher = {Society of Allied Weight Engineers, Inc.},
address = {Montreal, Canada},
abstract = {Scale model ditching tests are sometimes conducted to study the loads and dynamic behavior associated with an aircraft during water impact. To ensure scalability of the results, the model's mass properties including weight, center of gravity, and pitch moment of inertia in particular must proportionally reflect the characteristics of the full-scale aircraft. This paper presents the experimental methods used to evaluate these mass characteristics for a 1/20th scale Gulfstream G550 model prior to ditching tests conducted at the University of Georgia. These methods can be used for any similarly sized model.To determine the center of gravity the aircraft model is placed on a v-block assembly resting on three force transducers arranged in an isosceles triangle formation. The model's center of gravity along longitudinal and lateral axes is found by summing moments about a known reference axes system using the static forces measured at each transducer. To find the vertical center of gravity, the model is rotated about its longitudinal axis in a v-block fixture, and the force readings along the projection of the rotated plane are then manipulated.For pitch inertia, a compound pendulum is used to measure the aircraft's period of oscillation which is related to the inertia about the axis of oscillation through an analytical method [1]. The inertia of the pendulum apparatus by itself is then subtracted from the total experimental inertia, and the parallel axis theorem is used to determine the model's pitch inertia about its center of gravity. To evaluate the accuracy of the pendulum method, aluminum and steel brackets with known mass properties are attached to the model's tail, and the pitch inertia is measured again for each bracket. The increase in inertia is then compared against the theoretical increase.},
keywords = {06. Inertia Measurements, 08. Weighing, 11. Weight Engineering - Aircraft Estimation, Student Papers},
pubstate = {published},
tppubtype = {inproceedings}
}
2016
@inproceedings{3651,
title = {3651. Reducing Variation during Actual Aircraft Weighing},
author = {Keith Rebhorn},
url = {https://www.sawe.org/product/paper-3651},
year = {2016},
date = {2016-05-01},
booktitle = {75th Annual Conference, Denver, Colorado},
pages = {15},
publisher = {Society of Allied Weight Engineers, Inc.},
address = {Denver, Colorado},
abstract = {Aircraft weight and center of gravity are attributes that vary over the production and operational lifecycle of an aircraft. For a production aircraft, variation in weight and center of gravity (CG) can alert a Mass Properties engineer to potential issues with the aircraft, the weighing equipment, or the weighing procedure. Consistent weighing results minimize risk and associated costs, increase confidence and ensure product quality. This paper will address industry shortcomings in defining variation in aircraft weight and CG, discuss methods for reducing variation for production aircraft and explore methods to determine allowable values of variation. Furthermore variation and trend analysis will be discussed, concluding with ideas for future improvements.},
keywords = {08. Weighing},
pubstate = {published},
tppubtype = {inproceedings}
}
2015
@inproceedings{3631,
title = {3631. Weighing the B-25 Classic Aircraft},
author = {J Johnston and L Kleine and J Pierson and V Velasquez},
url = {https://www.sawe.org/product/paper-3631},
year = {2015},
date = {2015-05-01},
booktitle = {74th Annual Conference, Alexandria, Virginia},
pages = {8},
publisher = {Society of Allied Weight Engineers, Inc.},
address = {Alexandria, Virginia},
abstract = {Aircraft have been flying since December 17, 1903. Keeping older aircraft flying is a challenge. This desire to keep antique aircraft flying takes a group of individuals dedicated to preserving history. The relationship between L-3 and the Commemorative Air Force helps to keep this history alive.
Weighing aircraft built over 50 years ago was a process that required the use of bubble levels, mechanical scales, hand written paper documentation to perform the process of weighing an aircraft and the ability to perform addition, multiplication, and division without a computer. Today with the use of digital levels, Wi-Fi readouts hooked to electronic scales, digital cameras for inventory, and computers with spreadsheets, the weighing processes have become more manageable. Today's processes also help to minimize the chance of simple arithmetic errors and provide a neat professional output. Digital cameras and photography also help to provide a permanent record of inventory and the entire weighing process. This photographic record may help with reconciliation of the aircraft condition if the weighing results appear incorrect after the weighing and reconciliation have occurred.
This technical paper documents the use of advanced technology to help create accurate weighings and maintain accurate weight and balance records for antique aircraft.
Many of these early aircraft are made from fabric and held together with what is considered today to be primitive structural designs. Some aircraft require significant modifications and repairs to keep them flying and therefore require a reweighing after these modifications are performed.
This paper could also be a useful source for another B-25 owner to help with the process of maintaining weight and balance records. This paper documents the process, the experience and the satisfaction when working with classic aircraft.},
keywords = {08. Weighing},
pubstate = {published},
tppubtype = {inproceedings}
}
Weighing aircraft built over 50 years ago was a process that required the use of bubble levels, mechanical scales, hand written paper documentation to perform the process of weighing an aircraft and the ability to perform addition, multiplication, and division without a computer. Today with the use of digital levels, Wi-Fi readouts hooked to electronic scales, digital cameras for inventory, and computers with spreadsheets, the weighing processes have become more manageable. Today's processes also help to minimize the chance of simple arithmetic errors and provide a neat professional output. Digital cameras and photography also help to provide a permanent record of inventory and the entire weighing process. This photographic record may help with reconciliation of the aircraft condition if the weighing results appear incorrect after the weighing and reconciliation have occurred.
This technical paper documents the use of advanced technology to help create accurate weighings and maintain accurate weight and balance records for antique aircraft.
Many of these early aircraft are made from fabric and held together with what is considered today to be primitive structural designs. Some aircraft require significant modifications and repairs to keep them flying and therefore require a reweighing after these modifications are performed.
This paper could also be a useful source for another B-25 owner to help with the process of maintaining weight and balance records. This paper documents the process, the experience and the satisfaction when working with classic aircraft.@inproceedings{3638,
title = {3638. Buoyancy Effects on Mass Properties Analysis},
author = {J G Montgomery},
url = {https://www.sawe.org/product/paper-3638},
year = {2015},
date = {2015-05-01},
booktitle = {74th Annual Conference, Alexandria, Virginia},
pages = {42},
publisher = {Society of Allied Weight Engineers, Inc.},
address = {Alexandria, Virginia},
abstract = {This research project is designed to determine the effect of buoyancy on the weight of a specimen during final mass properties testing. The hypothesis is that the mass of the air displaced by the spacecraft is significant enough to warrant consideration during these tests. Also considered were the effects of the air displaced by the material that comprises the object being weighed, and the mass difference between a load cell standardization weight and the specimen under consideration.
To demonstrate these effects a test specimen was weighed in three different configurations. These configurations were open top, closed top and helium filled. It was demonstrated that there is a measurable difference between the first two configurations and the last configuration.
These buoyancy effects are not very relevant to objects that stay in the atmosphere. However, these effects should be considered when testing specimens that are to be used in space or very high altitudes. There will be buoyancy effects everywhere, but in the case of objects that leave the atmosphere, or go where there is a measurable pressure difference, there will be some measurable effect. These effects should be taken into account during mass properties final testing.
The results of the experiment showed a definite weight decrease when taking the buoyancy effects into account. The helium filled configuration weighed less that the open top and closed top configuration. This demonstrates a measurable effect of the displace air from inside the experimental vessel.
The goal of any final test in mass properties is to determine the mass at the highest accuracy possible. Some of the uncertainty can be reduced by taking into account that the propellant system will take up more volume than any other system due to the air displaced by the tanks. We can also reduce some of the uncertainty by factoring in the amount of air displaced by the volume of material in the spacecraft. Load cells are calibrated with this in mind, however they do not consider the material that the spacecraft is made of.},
keywords = {08. Weighing},
pubstate = {published},
tppubtype = {inproceedings}
}
To demonstrate these effects a test specimen was weighed in three different configurations. These configurations were open top, closed top and helium filled. It was demonstrated that there is a measurable difference between the first two configurations and the last configuration.
These buoyancy effects are not very relevant to objects that stay in the atmosphere. However, these effects should be considered when testing specimens that are to be used in space or very high altitudes. There will be buoyancy effects everywhere, but in the case of objects that leave the atmosphere, or go where there is a measurable pressure difference, there will be some measurable effect. These effects should be taken into account during mass properties final testing.
The results of the experiment showed a definite weight decrease when taking the buoyancy effects into account. The helium filled configuration weighed less that the open top and closed top configuration. This demonstrates a measurable effect of the displace air from inside the experimental vessel.
The goal of any final test in mass properties is to determine the mass at the highest accuracy possible. Some of the uncertainty can be reduced by taking into account that the propellant system will take up more volume than any other system due to the air displaced by the tanks. We can also reduce some of the uncertainty by factoring in the amount of air displaced by the volume of material in the spacecraft. Load cells are calibrated with this in mind, however they do not consider the material that the spacecraft is made of.2012
@inproceedings{3542,
title = {3542. Optimization of Aircraft Weighing Results and Failure Investigation},
author = {Gregor Lehnertz},
url = {https://www.sawe.org/product/paper-3542},
year = {2012},
date = {2012-05-01},
booktitle = {71st Annual Conference, Bad Gögging, Germany},
pages = {14},
publisher = {Society of Allied Weight Engineers, Inc.},
address = {Bad Gögging, Germany},
abstract = {Weighing of aircraft has been the basic control feature for mass properties since the very be- ginning of aircraft history, significantly supporting airworthiness verification purpose. With im- proving tools and methods for mass properties analysis the significance of theoretical data prognosis as well as monitoring increased, but with at the same time increasing complexity of aircraft systems and structure the weighing of aircraft together with potentially resulting mass properties data adjustment did not become less important.
In the meantime, rising flight performance requirements - especially for current fighter genera- tion - have correspondingly led to rising accuracy requirements on mass properties as one of the basic input parameters for flight control. Considering the above-mentioned role of weighing for aircraft mass properties data verification and adjustment this again applies likewise in- creased quality requirements to aircraft weighing data acquisition, which is always subjected to disturbing influences (like all kinds of measurements).
As disturbing influences can never be completely eliminated, the key task to obtain higher quality weighing results is to minimize those influences by adequate counter measures con- cerning aircraft weighing preparation as well as the weighing procedure itself. At the same time any resulting additional effort should be kept at a handable level, which can only be achieved by focusing on significant contributors only. And those significant contributors may vary be- tween different aircraft types. Hence the final result would normally lead to an aircraft type re- lated optimization, which needs to be permanently monitored and potentially improved by con- sideration of gained experience.
This paper tries to highlight and categorize disturbing weighing influences and to provide po- tential counter measures. Additionally a failure investigation system will be outlined in order to provide hands-on advice for further activities in case of significant deviations between ex- pected and obtained weighing results.},
keywords = {08. Weighing},
pubstate = {published},
tppubtype = {inproceedings}
}
In the meantime, rising flight performance requirements - especially for current fighter genera- tion - have correspondingly led to rising accuracy requirements on mass properties as one of the basic input parameters for flight control. Considering the above-mentioned role of weighing for aircraft mass properties data verification and adjustment this again applies likewise in- creased quality requirements to aircraft weighing data acquisition, which is always subjected to disturbing influences (like all kinds of measurements).
As disturbing influences can never be completely eliminated, the key task to obtain higher quality weighing results is to minimize those influences by adequate counter measures con- cerning aircraft weighing preparation as well as the weighing procedure itself. At the same time any resulting additional effort should be kept at a handable level, which can only be achieved by focusing on significant contributors only. And those significant contributors may vary be- tween different aircraft types. Hence the final result would normally lead to an aircraft type re- lated optimization, which needs to be permanently monitored and potentially improved by con- sideration of gained experience.
This paper tries to highlight and categorize disturbing weighing influences and to provide po- tential counter measures. Additionally a failure investigation system will be outlined in order to provide hands-on advice for further activities in case of significant deviations between ex- pected and obtained weighing results.@inproceedings{3573,
title = {3573. Investigation into the Feasibility of Onboard Weight and Balance Systems for Rotary Wing Aircraft with Wheeled Landing Gear},
author = {Philipp Schneider and Kai Thräne and Johann Wenzl and Sven Matthiesen},
url = {https://www.sawe.org/product/paper-3573},
year = {2012},
date = {2012-05-01},
booktitle = {71st Annual Conference, Bad Gögging, Germany},
pages = {31},
publisher = {Society of Allied Weight Engineers, Inc.},
address = {Bad Gögging, Germany},
abstract = {The gross weight and the location of the center of gravity are known to be crucial to the safe operation of aircraft. Calculation of the these values is mostly done by hand with a paper manifest or with the help of computer programs and lead to an estimate of about 99% accuracy - not accounting for human errors. To enhance the safety, onboard weight and balance systems which measure the actual gross weight and center of gravity before takeoff have been developed and used in fixed wing aircraft since 1932.
This paper aims to investigate the feasibility of such an integrated weighing system for rotary wing aircraft with wheeled landing gear. Although the experience from airplanes is beneficial to evaluate available measurement techniques and to foresee possible problems, there are several differences that do not allow direct technological transfer. This document describes the necessary measurement accuracies for rotary wing aircraft in diverse environmental conditions like ramp slope and wind. Further, available sensors and their capability to fulfill these needs are discussed. Technological risks are likewise identified and total system accuracies for different combinations of sensors are given. An analysis into customer needs in weight and balance determination and a possible human machine interface which meets these requirements is provided. Concluding, different forms of OWBS are synthesized from these conclusions and compared by their ability to fulfill miscellaneous objectives like certification strategy, operational constraints and customer acceptance.},
keywords = {08. Weighing},
pubstate = {published},
tppubtype = {inproceedings}
}
This paper aims to investigate the feasibility of such an integrated weighing system for rotary wing aircraft with wheeled landing gear. Although the experience from airplanes is beneficial to evaluate available measurement techniques and to foresee possible problems, there are several differences that do not allow direct technological transfer. This document describes the necessary measurement accuracies for rotary wing aircraft in diverse environmental conditions like ramp slope and wind. Further, available sensors and their capability to fulfill these needs are discussed. Technological risks are likewise identified and total system accuracies for different combinations of sensors are given. An analysis into customer needs in weight and balance determination and a possible human machine interface which meets these requirements is provided. Concluding, different forms of OWBS are synthesized from these conclusions and compared by their ability to fulfill miscellaneous objectives like certification strategy, operational constraints and customer acceptance.2010
@inproceedings{3494,
title = {3494. An Error Propagation Analysis of Small Engine Mass Properties Measurements},
author = {P. E. Anthony Primozich},
url = {https://www.sawe.org/product/paper-3494},
year = {2010},
date = {2010-05-01},
booktitle = {69th Annual Conference, Virginia Beach, Virginia},
pages = {16},
publisher = {Society of Allied Weight Engineers, Inc.},
address = {Virginia Beach, Virginia},
abstract = {This paper investigates the impact of measurement error propagation on the accuracy of calculated weights and centers of gravity of small turbofan engines. Three variations of the two-load-cell crane-and-cable weighing technique were explored. The potential sources of measurement error were identified and analytical expressions for calculating the total error in the weight and center of gravity calculations were derived. A generic engine example was used to conduct a sensitivity analysis to illustrate the magnitude of error that could result from various weighing configurations. Results show that incorrect mass properties values can have an effect on modern aircraft flying qualities, such as fuel burn, aircraft handling, and trim.},
keywords = {03. Center Of Gravity, 08. Weighing, 17. Weight Engineering - Procedures},
pubstate = {published},
tppubtype = {inproceedings}
}
2008
@inproceedings{3456,
title = {3456. Level or Not to Level: The Analysis of a Single Engine Weighing Process},
author = {Johnathan Kaufman},
url = {https://www.sawe.org/product/paper-3456},
year = {2008},
date = {2008-05-01},
booktitle = {67th Annual Conference, Seattle, Washington},
pages = {24},
address = {Seattle, Washington},
abstract = {With Cessna growing at a rate unprecedented in the company's history, and facilities bursting at the seams to accommodate the 18 different models of aircraft currently produced, every line is reviewed and evaluated to simplify and accelerate line flow. Cessna's Independence facility decided to evaluate the weighing process for the current production single engine aircraft (172, 182, and 206).
How can a process developed 10, 20, or even 30 years ago compare to one developed using the latest technologies? This paper discusses the analytical process used to develop a new weighing process for Cessna's single engine aircraft. This new process allows the aircraft to be weighed in unlevel conditions, translates the center-of-gravity to level conditions and decreases cycle time by more than one hour per weighing. These equations have been tested and show an improvement in repeatability, reproducibility and comparability between different units. This paper evaluates Cessna's previous single engine weighing process on safety, accuracy, reproducibility, repeatability, cycle time and cost. Anyone who has ever observed a weighing process and thought, 'there must be a better way,' will enjoy this paper.},
keywords = {08. Weighing, 17. Weight Engineering - Procedures},
pubstate = {published},
tppubtype = {inproceedings}
}
How can a process developed 10, 20, or even 30 years ago compare to one developed using the latest technologies? This paper discusses the analytical process used to develop a new weighing process for Cessna's single engine aircraft. This new process allows the aircraft to be weighed in unlevel conditions, translates the center-of-gravity to level conditions and decreases cycle time by more than one hour per weighing. These equations have been tested and show an improvement in repeatability, reproducibility and comparability between different units. This paper evaluates Cessna's previous single engine weighing process on safety, accuracy, reproducibility, repeatability, cycle time and cost. Anyone who has ever observed a weighing process and thought, 'there must be a better way,' will enjoy this paper.2007
@inproceedings{3404,
title = {3404. Weighing B747-400 Nose Up to Determine the Vertical Center of Gravity},
author = {Asher Pery},
url = {https://www.sawe.org/product/paper-3404},
year = {2007},
date = {2007-05-01},
booktitle = {66th Annual Conference, Madrid, Spain},
pages = {33},
publisher = {Society of Allied Weight Engineers},
address = {Madrid, Spain},
organization = {Society of Allied Weight Engineers},
abstract = {The report describes in detail the test carried out at Israel Aerospace Industries (IAI) in January 2006 to determine the vertical center of gravity of the Boeing 747-400 airplane. The Boeing 747-400 airplane underwent a conversion to an all cargo aircraft at IAI. IAI was therefore required to substantiate the conversion modifications for an airplane of another manufacturer. The vertical center of gravity is one of the parameters required in the analysis for the aircraft loads and dynamics, control and stability, ground loads, dynamic braking, and loadability. Essentially the method in the test was to weigh the airplane in two different airplane attitudes. The first weighing was performed with the aircraft in level attitude. Then the aircraft was lifted at the nose wheel and weighed again in the nose up position. The report includes full details of the setup (including photos), actual test results, computations, and evaluation of the tolerances. A derivation to in service cargo configuration is included. The results obtained were considered to be very satisfactory. It is our hope that this report will be of practical help to anyone who wishes to carry out a similar test on a large airplane.},
keywords = {03. Center Of Gravity, 08. Weighing},
pubstate = {published},
tppubtype = {inproceedings}
}
@inproceedings{3434,
title = {3434. Evaluation of Single Engine Weight and Center of Gravity Determination Methods},
author = {Patrick Brown},
url = {https://www.sawe.org/product/paper-3434},
year = {2007},
date = {2007-05-01},
booktitle = {66th Annual Conference, Madrid, Spain},
pages = {48},
publisher = {Society of Allied Weight Engineers},
address = {Madrid, Spain},
organization = {Society of Allied Weight Engineers},
abstract = {There is no greater task for a Weight Control Engineer than determining an aircraft?s weight and center of gravity (CG). Although the concept of balance or CG is easy to grasp, calculating or measuring it for complex objects, such as an aircraft, is very difficult. The accurate calculation of an aircraft?s CG is a primary factor in any flight operation. It directly affects aircraft safety, performance, and mission capability. This paper contains a comparative analysis of four potential methods for weight and CG measuring for single-engine aircraft. They are analytic, current, simplified weigh on wheels, and weigh on wheels, respectively. Each of the four methods is analyzed using historical data obtained from Cessna Aircraft Company. The methods are evaluated using statistical queuing and variation analysis. The queuing analysis, based on the Allen-Cunneen approximation model, assumes a normal probability distribution for both the arrival and service rates. It also considers only the known move rate of one product line. It does not consider either multiple lines or multiple move rates. However, it does consider both the capability and the productivity gains as a function of the weighing method selected. The variation analysis compares the results with the guidelines established in Advisory Circular (AC) 120-27E and its Cessna corollary, CSPS-011. These are 1.0% of the fleet weight and 0.5% of the mean aerodynamic cord. For the Cessna model considered in this investigation, these are +/-20.6 pounds (9.344 kg) and +/-0.29 inches (0.7366 cm), respectively. Probability plots contain the results obtained for each method. The plots also illustrate some interesting relationships between the measurements of weight and distance and the calculation of center of gravity (CG).},
keywords = {08. Weighing},
pubstate = {published},
tppubtype = {inproceedings}
}
2006
@inproceedings{3397,
title = {3397. Weight on Wheels: Software Development},
author = {Johathan Kaufman and Patrick Brown},
url = {https://www.sawe.org/product/paper-3397},
year = {2006},
date = {2006-05-01},
booktitle = {65th Annual Conference, Valencia, California},
pages = {35},
publisher = {Society of Allied Weight Engineers},
address = {Valencia, California},
organization = {Society of Allied Weight Engineers},
abstract = {The accurate and precise measurement of aircraft weight and center of gravity (CG) is a demanding task in the aviation industry. To that end, a group of Cessna employees was challenged by a member of its Senior Leadership Team (SLT) to improve the in-house weighing process. Through multiple initiatives, Cessna Aircraft Company has developed and patented the most accurate aircraft CG measurement system in the industry. In order for the system to work, Cessna engineers developed and copyrighted a sophisticated software package. The presentation will show how the team designed, developed, and implemented the Weight on Wheels (WoW) software package. The topics of ongoing and future software development will also be discussed.},
keywords = {08. Weighing},
pubstate = {published},
tppubtype = {inproceedings}
}
@inproceedings{3384,
title = {3384. Measuring Weight And Center Of Gravity Using Load Cells},
author = {Brad Hill},
url = {https://www.sawe.org/product/paper-3384},
year = {2006},
date = {2006-05-01},
booktitle = {65th Annual Conference, Valencia, California},
pages = {19},
publisher = {Society of Allied Weight Engineers},
address = {Valencia, California},
organization = {Society of Allied Weight Engineers},
abstract = {Today?s load cells are capable of an accuracy of +-0.05%, or better, under ideal conditions. But ideal conditions are expensive to obtain and, because ?you get what you pay for,? these high accuracies are not always possible or even required. Given sufficient time and money most anything can be weighed to a high degree of accuracy. More often we are asked to measure the weight and center of gravity of an object when the design and building of specialized fixtures and laboratory conditions is not practical or warranted. To meet the needs of a customer without exceeding his budget we are often required to be creative in how we use the equipment available while keeping in mind the accuracy and validity of the data we are gathering. Many things will affect the accuracy of the information we get from a test, especially the quality of the equipment, the physical arrangement, our procedures and the calibration uncertainty of the load cells. There are just as many areas where confidence can be built into a test. To obtain the best value for the dollar from our test we must consider things like the set-up of the test, weight and dimensional measurements, environmental factors and equipment shortcomings. For the purpose of this paper the term ?load cell? refers to stand alone canister-type cells, like those in a standard aircraft weighing kit, that are not part of a permanent fixture. This type of equipment is commonly used to measure the weight and center of gravity of large parts, assemblies, tooling, missiles and other items where a unique set-up is required for each.},
note = {Mike Hackney Best Paper Award},
keywords = {08. Weighing, 09. Weighing Equipment, Mike Hackney Best Paper Award},
pubstate = {published},
tppubtype = {inproceedings}
}
2005
@inproceedings{3369,
title = {3369. Weigh on Wheels},
author = {Patrick Brown},
url = {https://www.sawe.org/product/paper-3369},
year = {2005},
date = {2005-05-01},
booktitle = {64th Annual Conference, Annapolis, Maryland},
pages = {23},
publisher = {Society of Allied Weight Engineers, Inc.},
address = {Annapolis, Maryland},
abstract = {This paper introduces a new paradigm to the aviation industry. The new paradigm is a method for weighing and calculating the center of gravity of an aircraft without leveling the aircraft. The solution requires the measurement and input of eight variables into a complex algorithm contained within a software program. The eight variables are: 1-3) the scale reactions at each of the wheel locations, 4-6) the measurement of each of the exposed oleo lengths, 7-8) the measurement of the angle of incidence of the pitch and roll axis to earth center.
With an accelerometer installed at a tooled location, Cessna Engineers determined aircraft level repeatedly and accurately within 0.01 of a degree of earth center. The ability to measure aircraft level further enabled Cessna Engineers to improve the calculation of aircraft C.G. by 14 Sigma!
Because of moving from weighing and leveling aircraft on jacks with load cells to Weigh on Wheels, Cessna can claim a 33% reduction in labor for the first aircraft weighing. Cessna can also claim a 40% reduction in labor for the first and second successive aircraft weighings. Finally, Cessna can claim up to a 68% reduction in labor for the first and second weighings and a reweigh.
Not only can Cessna claim increased labor efficiency as a direct result of the accuracy of Weigh on Wheels, but they can also claim a reduction in the total number of weighings performed. Statistically, Cessna weighs each aircraft 2.78 times. With Weigh on Wheels, Cessna can now claim that each aircraft is weighed an average of 2.16 times. Entitlement is 2.0 weighings per aircraft.
With the reduced number of weighings per aircraft and the reduction in time required to weigh an aircraft, Cessna was able to replace 12 sets of jack scales with 3 portable sets of platform scales!
Finally, Weigh on Wheels is a much safer method of weighing aircraft. It is safer for the aircraft. It is safer for the mechanics. While no documented cases of injury exist as a direct result of weighing an aircraft, wing panels cost in the tens of thousands of dollars.},
keywords = {08. Weighing},
pubstate = {published},
tppubtype = {inproceedings}
}
With an accelerometer installed at a tooled location, Cessna Engineers determined aircraft level repeatedly and accurately within 0.01 of a degree of earth center. The ability to measure aircraft level further enabled Cessna Engineers to improve the calculation of aircraft C.G. by 14 Sigma!
Because of moving from weighing and leveling aircraft on jacks with load cells to Weigh on Wheels, Cessna can claim a 33% reduction in labor for the first aircraft weighing. Cessna can also claim a 40% reduction in labor for the first and second successive aircraft weighings. Finally, Cessna can claim up to a 68% reduction in labor for the first and second weighings and a reweigh.
Not only can Cessna claim increased labor efficiency as a direct result of the accuracy of Weigh on Wheels, but they can also claim a reduction in the total number of weighings performed. Statistically, Cessna weighs each aircraft 2.78 times. With Weigh on Wheels, Cessna can now claim that each aircraft is weighed an average of 2.16 times. Entitlement is 2.0 weighings per aircraft.
With the reduced number of weighings per aircraft and the reduction in time required to weigh an aircraft, Cessna was able to replace 12 sets of jack scales with 3 portable sets of platform scales!
Finally, Weigh on Wheels is a much safer method of weighing aircraft. It is safer for the aircraft. It is safer for the mechanics. While no documented cases of injury exist as a direct result of weighing an aircraft, wing panels cost in the tens of thousands of dollars.@inproceedings{3371,
title = {3371. Weighing a Vessel Without Hull Information and Without Placing the Vessel on Scales},
author = {Rosendo Martinez},
url = {https://www.sawe.org/product/paper-3371},
year = {2005},
date = {2005-05-01},
booktitle = {64th Annual Conference, Annapolis, Maryland},
pages = {15},
publisher = {Society of Allied Weight Engineers, Inc.},
address = {Annapolis, Maryland},
abstract = {The vessel weight is obtained during the incline experiment by observing the draft height on the side of the vessel. This method is the most practical method because it does not require taking the vessel out of the water and it is very simple to perform. This method of obtaining the weight requires calculating the volume of the shape of the hull for incremental draft heights, recording the information for future reference on a displacement curve and placing the draft gage markings on the vessel.
Obtaining the vessel weight (displacement) is accomplished by measuring the specific gravity of the water the vessel is floating on using a hydrometer to obtain the water density. The volume of water displaced is obtained by observing the draft gage on the side of the vessel and by looking at the Hydrostatic Curve of the particular vessel. The vessel weight is the multiplication of the water density times the volume of water displaced.
The weighing method presented in this paper is a method for obtaining the vessel weight when the Lines Plan, Hydrostatic Curves or hull shape information is not available, scales are not available, the vessel cannot be taken out of the water and placed on the scales or if it is necessary to verify the Hydrostatic Curves. Air, space and ground vehicle are weighed on scales to verify the calculated weight, it would be nice to verify the Hydrostatic Curves of a vessel. The accuracy of the result obtained using this method depends on the precautions taken and the equipment available.},
keywords = {08. Weighing},
pubstate = {published},
tppubtype = {inproceedings}
}
Obtaining the vessel weight (displacement) is accomplished by measuring the specific gravity of the water the vessel is floating on using a hydrometer to obtain the water density. The volume of water displaced is obtained by observing the draft gage on the side of the vessel and by looking at the Hydrostatic Curve of the particular vessel. The vessel weight is the multiplication of the water density times the volume of water displaced.
The weighing method presented in this paper is a method for obtaining the vessel weight when the Lines Plan, Hydrostatic Curves or hull shape information is not available, scales are not available, the vessel cannot be taken out of the water and placed on the scales or if it is necessary to verify the Hydrostatic Curves. Air, space and ground vehicle are weighed on scales to verify the calculated weight, it would be nice to verify the Hydrostatic Curves of a vessel. The accuracy of the result obtained using this method depends on the precautions taken and the equipment available.2001
@inproceedings{3147,
title = {3147. Precise Measurement of Mass},
author = {Richard Boynton},
url = {https://www.sawe.org/product/paper-3147},
year = {2001},
date = {2001-05-01},
booktitle = {60th Annual Conference, Arlington, Texas, May 19-23},
pages = {32},
publisher = {Society of Allied Weight Engineers, Inc.},
address = {Arlington, Texas},
abstract = {Space vehicle weight is very critical. It is particularly important to have accurate weight if the vehicle weight is near the maximum allowable. Scales with accuracies as good as 0.002% are now available from companies such as Space Electronics. However, unless precaution is taken to correct for local gravity, air buoyancy, and a number of other factors, the high accuracy of the scale is not realized. In fact, considerations which are often overlooked can result in a total error of several percent. Some of the concerns are:
1. Latitude The acceleration of gravity varies from 9.780 m/s2 at the equator to 9.832 m/s2 at the poles (a difference of 0.53%). This is in part due to the centrifugal force resulting from the rotation of the earth, which varies from zero at the north pole to a maximum value at the equator, and in part due to the bulge of the earth at the equator, resulting in a greater distance to the mass center of the earth.
2. Altitude The gravitational mass attraction to the earth at a particular location varies as the square of the distance to the mass center of the earth, resulting in a variation by as much as 0.26% over the surface of the earth.
3. Tidal effects The gravitational mass attraction to the sun and moon at a particular location may exhibit a variation as large as 0.003% of the acceleration of earth gravity at certain dates during the year when the sun and moon align (this means that the scale could indicate a larger weight in the morning than at night).
4. Gravity anomaly Variations in the density of the earth's crust in the vicinity of an object result in small variations in gravity at different locations. Nearby mountain ranges reduce the force of gravity on the object.
5. Buoyancy The object being measured displaces a volume of air, whose density can vary due to the weather. The resulting upward force is a function of object size. For large low density objects, failure to correct for buoyancy may result in errors of 0.5% or larger.
In addition, errors can be introduced by
6. Moisture condensation or absorption of moisture (evaporates in vacuum of space)
7. Electrostatic attraction to the draft shield surrounding the scale
8. Magnetic attraction to nearby objects and to the earth's magnetic north
9. Downdrafts or updrafts (due to a temperature difference between object and ambient air)
Variations in the acceleration of gravity result in a change in the weight of an object of about 0.8% over the surface of the earth, and about 0.2% over the contiguous USA!
I put the exclamation point at the end of the sentence because I frequently see specifications for a scale accuracy of 0.03% or better, yet these scales are used at latitudes that are significantly different from the latitude at which the scale was calibrated without any adjustment being made. Air buoyancy can cause a scale to read low by 0.5% or greater. Some of the other factors listed produce errors of 0.1% or more.
This paper discusses several issues:
1. How and when to correct for the acceleration of gravity when measuring mass.
2. How to correct for air buoyancy.
3. A very simple method to correct for both quantities automatically without knowing either the acceleration of gravity or the air density at a particular location.
In addition, this paper outlines the methods for determining local gravity, and summarizes the types of scales which are available and their accuracy. Finally, I have given my opinion on the subject of mass vs. weight, a topic which seems to result in endless confusion and disagreement.},
keywords = {08. Weighing},
pubstate = {published},
tppubtype = {inproceedings}
}
1. Latitude The acceleration of gravity varies from 9.780 m/s2 at the equator to 9.832 m/s2 at the poles (a difference of 0.53%). This is in part due to the centrifugal force resulting from the rotation of the earth, which varies from zero at the north pole to a maximum value at the equator, and in part due to the bulge of the earth at the equator, resulting in a greater distance to the mass center of the earth.
2. Altitude The gravitational mass attraction to the earth at a particular location varies as the square of the distance to the mass center of the earth, resulting in a variation by as much as 0.26% over the surface of the earth.
3. Tidal effects The gravitational mass attraction to the sun and moon at a particular location may exhibit a variation as large as 0.003% of the acceleration of earth gravity at certain dates during the year when the sun and moon align (this means that the scale could indicate a larger weight in the morning than at night).
4. Gravity anomaly Variations in the density of the earth's crust in the vicinity of an object result in small variations in gravity at different locations. Nearby mountain ranges reduce the force of gravity on the object.
5. Buoyancy The object being measured displaces a volume of air, whose density can vary due to the weather. The resulting upward force is a function of object size. For large low density objects, failure to correct for buoyancy may result in errors of 0.5% or larger.
In addition, errors can be introduced by
6. Moisture condensation or absorption of moisture (evaporates in vacuum of space)
7. Electrostatic attraction to the draft shield surrounding the scale
8. Magnetic attraction to nearby objects and to the earth's magnetic north
9. Downdrafts or updrafts (due to a temperature difference between object and ambient air)
Variations in the acceleration of gravity result in a change in the weight of an object of about 0.8% over the surface of the earth, and about 0.2% over the contiguous USA!
I put the exclamation point at the end of the sentence because I frequently see specifications for a scale accuracy of 0.03% or better, yet these scales are used at latitudes that are significantly different from the latitude at which the scale was calibrated without any adjustment being made. Air buoyancy can cause a scale to read low by 0.5% or greater. Some of the other factors listed produce errors of 0.1% or more.
This paper discusses several issues:
1. How and when to correct for the acceleration of gravity when measuring mass.
2. How to correct for air buoyancy.
3. A very simple method to correct for both quantities automatically without knowing either the acceleration of gravity or the air density at a particular location.
In addition, this paper outlines the methods for determining local gravity, and summarizes the types of scales which are available and their accuracy. Finally, I have given my opinion on the subject of mass vs. weight, a topic which seems to result in endless confusion and disagreement.@inproceedings{3149,
title = {3149. Weight Verification of a Pressure Stabilized Vehicle},
author = {Andrew V. McGill},
url = {https://www.sawe.org/product/paper-3149},
year = {2001},
date = {2001-05-01},
booktitle = {60th Annual Conference, Arlington, Texas, May 19-23},
pages = {31},
publisher = {Society of Allied Weight Engineers, Inc.},
address = {Arlington, Texas},
abstract = {Verify the predicted weight of a launch vehicle before flight. Weigh the vehicle to reduce the uncertainty associated with itsweight, ensure the performance requirements acquiesce, and thereby increase the probability of mission success.
Obtain a gross weight of the vehicle using the appropriate calibrated weighing equipment. Establish the as-weighed configuration. Rectify the actual weight to the flight configuration. Consider shortages and overages, such as handling fixtures and non-flight hardware that must be removed before flight. Determine the buoyancy effect of the air displaced by the vehicle and its handling fixtures. Take into account the composition and pressure of the gas in the tank. Base the ambient air density on temperature, relative humidity, and barometric pressure. Document all results.
The fundamental systems engineering process described in this paper is used on the highly successful Atlas launch vehicle program. This paper provides a method to determine an actual weight adjustment that is applicable to the predicted launch vehicle mass properties. The weight of every Centaur upper stage is verified in this manner.},
keywords = {08. Weighing},
pubstate = {published},
tppubtype = {inproceedings}
}
Obtain a gross weight of the vehicle using the appropriate calibrated weighing equipment. Establish the as-weighed configuration. Rectify the actual weight to the flight configuration. Consider shortages and overages, such as handling fixtures and non-flight hardware that must be removed before flight. Determine the buoyancy effect of the air displaced by the vehicle and its handling fixtures. Take into account the composition and pressure of the gas in the tank. Base the ambient air density on temperature, relative humidity, and barometric pressure. Document all results.
The fundamental systems engineering process described in this paper is used on the highly successful Atlas launch vehicle program. This paper provides a method to determine an actual weight adjustment that is applicable to the predicted launch vehicle mass properties. The weight of every Centaur upper stage is verified in this manner.2000
@inproceedings{3022,
title = {3022. Uncertainty Analysis in Weighing Pressurized Vessels},
author = {Phung LeCong and Ricardo Roy},
url = {https://www.sawe.org/product/paper-3022},
year = {2000},
date = {2000-06-01},
booktitle = {59th Annual Conference, St. Louis, Missouri, June 5-7},
pages = {10},
publisher = {Society of Allied Weight Engineers, Inc.},
address = {St. Louis, Missouri},
abstract = {For proper guidance, the mass of the launch vehicle must be determined with the least uncertainty. Analytical expressions are developed to calculate the uncertainty in the vehicle mass. Application of these expressions to the booster and second stage yields data that are useful in minimizing the uncertainty and in making operation decisions.},
keywords = {08. Weighing},
pubstate = {published},
tppubtype = {inproceedings}
}
@inproceedings{3029,
title = {3029. Trinity Airweighs Weight and Balance System},
author = {Kirk Nance},
url = {https://www.sawe.org/product/paper-3029},
year = {2000},
date = {2000-06-01},
booktitle = {59th Annual Conference, St. Louis, Missouri, June 5-7},
pages = {14},
publisher = {Society of Allied Weight Engineers, Inc.},
address = {St. Louis, Missouri},
abstract = {For over 50 years the aviation industry has tried to develop a reliable onboard weighing system. The results of these efforts have ranged from the Wheatstone Bridge in 1944 to Barkhausen Noise in 1999. As early as 1967, attempts have been made to use landing gear strut pressure measurements. The strut pressure attempts failed due to inaccuracies caused by aircraft landing gear strut seal friction, which distorts landing gear strut pressure, as it relates to weight supported. The Trinity Airweighs Weight & Balance System (W&BS) incorporates a new, patented technology which efficiently measures and compensates for pressure distortions caused by strut seal friction. The aircraft landing gear strut has evolved through decades of design changes to be one of the most durable components of today?s modern aircraft. What better tool to use in determining aircraft weight than converting the landing gear strut into a load cell, which is designed to take the abuse of the day-to-day rigors of an airline operation.
The Trinity Airweighs W&BS is permanently attached to the aircraft and converts aircraft landing gear struts into onboard weighing scales.
Dispatching with the Trinity Airweighs Weight & Balance System reduces the time required to measure actual aircraft take-off weight and center of gravity to about 6-8 seconds.},
keywords = {08. Weighing},
pubstate = {published},
tppubtype = {inproceedings}
}
The Trinity Airweighs W&BS is permanently attached to the aircraft and converts aircraft landing gear struts into onboard weighing scales.
Dispatching with the Trinity Airweighs Weight & Balance System reduces the time required to measure actual aircraft take-off weight and center of gravity to about 6-8 seconds.1999
@inproceedings{2455,
title = {2455. Weighing a Beluga (A300-600ST) Nose Up to Determine the Vertical Center of Gravity},
author = {A Krautner},
url = {https://www.sawe.org/product/paper-2455},
year = {1999},
date = {1999-05-01},
booktitle = {58th Annual Conference, San Jose, California, May 24-26},
pages = {32},
publisher = {Society of Allied Weight Engineers, Inc.},
address = {San Jose, California},
abstract = {Federal Aviation Administration regulations require that all civil aircraft are weighed to determine the center of gravity (CG) location and the empty weight in order to establish a basis for weight and balance computations. Normally the weighing is conducted prior to ground vibration tests, first flight or delivery of the aircraft. From the weighing results Manufacturer Weight Empty (MWE), Operational Weight Empty (OWE) and the CG of the aircraft are calculated and provided to the customer. In order to determine the weight and the longitudinal center of gravity weighing the aircraft in level attitude is sufficient and common practice. For the A300-600ST Beluga the knowledge of the longitudinal CG is not enough. The unconventional shape and the variety of payloads which are transported mostly in the main cargo compartment requires also knowledge of the vertical CG of the empty aircraft. The position of the vertical CG is necessary for airplane control and stability investigations and the determination of ground loads. Dynamic braking, for example, a load case which occurs when the take off with maximum take off weight is aborted, causes the maximum nose landing gear load and the maximum compression in the upper front fuselage sections. To determine the CG in the z-direction it is necessary to weigh the aircraft in two different attitudes. At first the weighing is performed with the aircraft in level attitude. Then the aircraft is lifted at the nose wheel and weighed again in the nose up position. Lifting the aircraft at the nose landing gear was one part of the challenge, the other was to measure precisely nose up angle and wheel-base for the final calculation. This paper describes the methodology that was developed and the weighing of aircraft number four which took place in May 1998 in Toulouse, France.},
keywords = {08. Weighing},
pubstate = {published},
tppubtype = {inproceedings}
}