SAWE Technical Papers
Technical Library
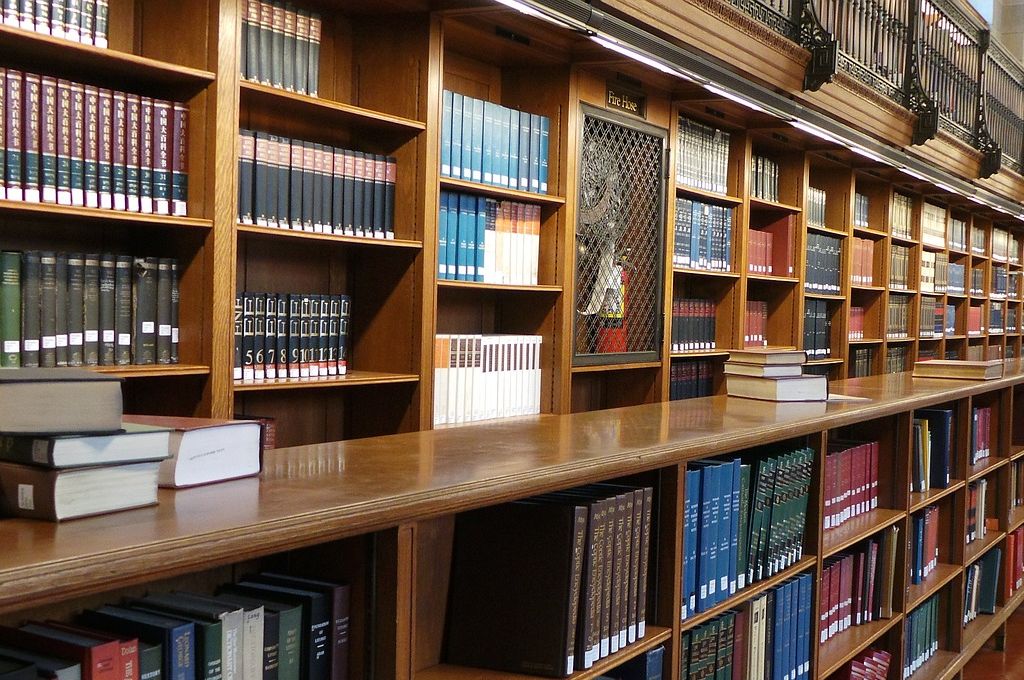
SAWE Paper Database
The SAWE Technical Library contains nearly 4000 technical papers available here for purchase and download. Use the search options below to find what you need.
3774. Weight Control For Floating Wind Installation Crowle, A. P.; Thies, P. R. In: 2021 SAWE Tech Fair, pp. 10, Society of Allied Weight Engineers, Inc., Virtual Conference, 2021. Abstract | Buy/Download | BibTeX | Tags: 24. Weight Engineering - System Design, 35. Weight Engineering - Offshore, Marine, Student Papers 3739. Rotorcraft Mass Assessment in an Integrated Design Framework Schwinn, Dominik B.; Weiand, Peter In: 2020 SAWE Tech Fair, pp. 15, Society of Allied Weight Engineers, Inc., Virtual Conference, 2020. Abstract | Buy/Download | BibTeX | Tags: 10. Weight Engineering - Aircraft Design, 21. Weight Engineering - Statistical Studies, 24. Weight Engineering - System Design 3690. Weight Optimization of Environmental Control System of Corporate Jets Mitry, Ragaa In: 76th Annual Conference, Montreal, Canada, pp. 20, Society of Allied Weight Engineers, Inc., Montreal, Canada, 2017. Abstract | Buy/Download | BibTeX | Tags: 10. Weight Engineering - Aircraft Design, 24. Weight Engineering - System Design 3671. Model Based Mass Properties Engineering at JPL IV, Morgan Hendry; Gross, Johannes In: 75th Annual Conference, Denver, Colorado, pp. 11, Society of Allied Weight Engineers, Inc., Denver, Colorado, 2016. Abstract | Buy/Download | BibTeX | Tags: 12. Weight Engineering - Computer Applications, 24. Weight Engineering - System Design 3672. Weight's Importance in Machine Design Hundl, Jacob In: 75th Annual Conference, Denver, Colorado, pp. 9, Society of Allied Weight Engineers, Inc., Denver, Colorado, 2016. Abstract | Buy/Download | BibTeX | Tags: 24. Weight Engineering - System Design, Student Papers 3635. Mass Properties - Flow of Information de Paula, V B Gomide; Abrantes, F V; de Matos, M Silveira; Meyer, S C In: 74th Annual Conference, Alexandria, Virginia, pp. 14, Society of Allied Weight Engineers, Inc., Alexandria, Virginia, 2015. Abstract | Buy/Download | BibTeX | Tags: 17. Weight Engineering - Procedures, 24. Weight Engineering - System Design Boze, William; Heaney, Elizabeth In: 69th Annual Conference, Virginia Beach, Virginia, pp. 10, Society of Allied Weight Engineers, Inc., Virginia Beach, Virginia, 2010. Abstract | Buy/Download | BibTeX | Tags: 17. Weight Engineering - Procedures, 21. Weight Engineering - Statistical Studies, 24. Weight Engineering - System Design 3508. Methods and Benefits of Detailed Wire Weight Accounting FLUEGEL, ANDREW; NASCHANSKY, NICK In: 69th Annual Conference, Virginia Beach, Virginia, pp. 12, Society of Allied Weight Engineers, Inc., Virginia Beach, Virginia, 2010. Abstract | Buy/Download | BibTeX | Tags: 20. Weight Engineering - Specifications, 24. Weight Engineering - System Design 3469. Comparison of Power Distribution Systems for Land Vehicles Al-Kahwati, Jack In: 68th Annual Conference, Wichita, Kansas, pp. 10, Wichita, Kansas, 2009. Abstract | Buy/Download | BibTeX | Tags: 24. Weight Engineering - System Design, 31. Weight Engineering - Surface Transportation 3437. Development and Implementation of a Space Systems Mass Properties Process Peterson, Jesse; Ratz, Otto G.; Trego, Dr. Angela In: 67th Annual Conference, Seattle, Washington, pp. 10, Seattle, Washington, 2008. Abstract | Buy/Download | BibTeX | Tags: 17. Weight Engineering - Procedures, 24. Weight Engineering - System Design 3448. The Role of Effective Mass Property Management in a Global Product Creation Process Heim, Claudia; Pertermann, Holger In: 67th Annual Conference, Seattle, Washington, pp. 18, Seattle, Washington, 2008. Abstract | Buy/Download | BibTeX | Tags: 16. Weight Engineering - Organization, 24. Weight Engineering - System Design 3403. Topology Optimization on the Example of an Advanced Trainer Aircraft Anton, Hansjürgen; Hörnlein, Herbert In: 66th Annual Conference, Madrid, Spain, pp. 12, Society of Allied Weight Engineers Society of Allied Weight Engineers, Madrid, Spain, 2007. Abstract | Buy/Download | BibTeX | Tags: 10. Weight Engineering - Aircraft Design, 24. Weight Engineering - System Design Reinartz, Roland In: 66th Annual Conference, Madrid, Spain, pp. 14, Society of Allied Weight Engineers Society of Allied Weight Engineers, Madrid, Spain, 2007. Abstract | Buy/Download | BibTeX | Tags: 24. Weight Engineering - System Design, 34. Advanced Design 3390. Mass Body Data Collection System Cooper, John; Sinor, Buddy In: 65th Annual Conference, Valencia, California, pp. 13, Society of Allied Weight Engineers Society of Allied Weight Engineers, Valencia, California, 2006. Abstract | Buy/Download | BibTeX | Tags: 24. Weight Engineering - System Design 3364. Conceptual Level Mass Properties of an All-Mach Aerospace Plane MacConochie, Ian O. In: 64th Annual Conference, Annapolis, Maryland, pp. 13, Society of Allied Weight Engineers, Inc., Annapolis, Maryland, 2005. Abstract | Buy/Download | BibTeX | Tags: 24. Weight Engineering - System Design 3008. The Systems Engineering Role in Mass Properties Morgan, Jonathan In: 59th Annual Conference, St. Louis, Missouri, June 5-7, pp. 7, Society of Allied Weight Engineers, Inc., St. Louis, Missouri, 2000. Abstract | Buy/Download | BibTeX | Tags: 24. Weight Engineering - System Design Lucas, S In: 57th Annual Conference, Wichita, Kansas, May 18-20, pp. 10, Society of Allied Weight Engineers, Inc., Wichita, Kansas, 1998. Abstract | Buy/Download | BibTeX | Tags: 24. Weight Engineering - System Design 2429. Integrated Thermal Energy Management System Carter, N In: 57th Annual Conference, Wichita, Kansas, May 18-20, pp. 25, Society of Allied Weight Engineers, Inc., Wichita, Kansas, 1998. Abstract | Buy/Download | BibTeX | Tags: 24. Weight Engineering - System Design 1818. Weight Savings in Aerospace Vehicles Through Propellant Scavenging Schneider, S J Dr. In: 47th Annual Conference, Plymouth, Michigan, May 23-25, pp. 41, Society of Allied Weight Engineers, Inc., Plymouth, Michigan, 1988. Abstract | Buy/Download | BibTeX | Tags: 24. Weight Engineering - System Design 1743. Fifteen Years of Flight Control Evolution on European Airbus Aircraft Weight Impact Hammen, M In: 45th Annual Conference, Williamsburg, Virginia, May 12-14, pp. 25, Society of Allied Weight Engineers, Inc., Williamsburg, Virginia, 1986. Abstract | Buy/Download | BibTeX | Tags: 24. Weight Engineering - System Design2021
@inproceedings{3774,
title = {3774. Weight Control For Floating Wind Installation},
author = {A. P. Crowle and P. R. Thies},
url = {https://www.sawe.org/product/paper-3774},
year = {2021},
date = {2021-11-01},
urldate = {2021-11-01},
booktitle = {2021 SAWE Tech Fair},
pages = {10},
publisher = {Society of Allied Weight Engineers, Inc.},
address = {Virtual Conference},
abstract = {Floating offshore wind is a growing market within the renewable energy sector. The floating offshore wind turbines give access to deeper water sites, with minimal visual impact from land. The paper includes the weight control requirements for Spars, barges, semi submersibles and Tension Leg Platforms (TLPs) as floating wind platforms.
There are weight control challenges for the various substructure types during the temporary phases of construction and offshore installation. An accurate assessment of the buoyancy of the floating wind turbine for different drafts and trims is required. Allowances need to be included in the weight calculation for temporary buoyancy, sea-fastenings and grillage.
Weight control for installation has an influence on the weather window for the floating substructures during transportation to the offshore site and mooring and electrical connection. The paper will cover weight calculation methods during early design, detailed design, construction, installation, operation and demolition.
The installation process for a floating wind turbine varies with substructure type and this paper will give an overview of the weight control requirements for loadout, ocean transport and mooring connection. The floating offshore wind turbine weight and centre of gravity has a direct bearing on draft, intact stability and motions. As part of the weight control process the centre of gravity and radii of gyration need to be accurately determined for each stage of the installation.},
keywords = {24. Weight Engineering - System Design, 35. Weight Engineering - Offshore, Marine, Student Papers},
pubstate = {published},
tppubtype = {inproceedings}
}
There are weight control challenges for the various substructure types during the temporary phases of construction and offshore installation. An accurate assessment of the buoyancy of the floating wind turbine for different drafts and trims is required. Allowances need to be included in the weight calculation for temporary buoyancy, sea-fastenings and grillage.
Weight control for installation has an influence on the weather window for the floating substructures during transportation to the offshore site and mooring and electrical connection. The paper will cover weight calculation methods during early design, detailed design, construction, installation, operation and demolition.
The installation process for a floating wind turbine varies with substructure type and this paper will give an overview of the weight control requirements for loadout, ocean transport and mooring connection. The floating offshore wind turbine weight and centre of gravity has a direct bearing on draft, intact stability and motions. As part of the weight control process the centre of gravity and radii of gyration need to be accurately determined for each stage of the installation.2020
@inproceedings{3739,
title = {3739. Rotorcraft Mass Assessment in an Integrated Design Framework},
author = {Dominik B. Schwinn and Peter Weiand},
url = {https://www.sawe.org/product/paper-3739},
year = {2020},
date = {2020-07-01},
booktitle = {2020 SAWE Tech Fair},
pages = {15},
publisher = {Society of Allied Weight Engineers, Inc.},
address = {Virtual Conference},
abstract = {Mass estimation is an essential discipline in the design process of aeronautical vehicles. The maximum take-off mass determines most other design parameters and should therefore be estimated sufficiently precise from the beginning. In the conceptual design phase fast analyses are required in order to allow trade-off studies. In general, this phase is dominated by the use of analytical and statistical methods. At the end of this design stage, a basic external layout has been elaborated and basic design parameters have been determined.During the subsequent preliminary design stage, physics based higher fidelity methods are applied to further elaborate the design and to establish an internal configuration. The constantly increasing computational power allows comparably fast analyses in this design stage that may alter the configuration established in the conceptual design stage.Particular challenges in this design approach arise with unconventional configurations, such as compound rotorcraft, or with different propulsion systems to be integrated, for instance electric or hybrid systems, because of a lack of sufficient statistical data.The German Aerospace Center (DLR) has established the integrated design environment IRIS (Integrated Rotorcraft Initial Sizing) to allow an assessment of virtual rotorcraft configurations. It covers the conceptual and parts of the preliminary design stage and uses the data model CPACS (Common Parametric Aircraft Configuration Schema) for the parametric rotorcraft description.Component masses in IRIS are estimated using various statistical methods during the conceptual design stage. Finite Element (FE) methods are applied in the preliminary design phase to allow a more precise estimation of the structural mass which may influence the maximum take-off mass and therefore the performance characteristics calculated in the conceptual design stage.This paper introduces the design environment IRIS, and in particular the PANDORA framework (Parametric Numerical Design and Optimization Routines for Aircraft) which is used for the statistical estimation of the rotorcraft component masses and the structural sizing process to determine the fuselage mass.},
keywords = {10. Weight Engineering - Aircraft Design, 21. Weight Engineering - Statistical Studies, 24. Weight Engineering - System Design},
pubstate = {published},
tppubtype = {inproceedings}
}
2017
@inproceedings{3690,
title = {3690. Weight Optimization of Environmental Control System of Corporate Jets},
author = {Ragaa Mitry},
url = {https://www.sawe.org/product/paper-3690},
year = {2017},
date = {2017-05-01},
booktitle = {76th Annual Conference, Montreal, Canada},
pages = {20},
publisher = {Society of Allied Weight Engineers, Inc.},
address = {Montreal, Canada},
abstract = {The environmental control system (ECS) is an essential system in the aircraft; it provides air supply, thermal, humidity, ventilation, and cabin pressurization for the crew and passengers. It is also used for engine anti-ice, main door sealing, avionic cooling, and smoke detection.ECS is sized to meet the aircraft mission. It is the highest power-consuming system on the aircraft.The basic designs of the ECS used on most aircraft, in both corporate jets and commercial airliners, are remarkably similar. In simplified terms, air is first compressed to high pressure and temperature in the engine compressors, cooled in a precooler before entering the fuselage then conditioned by an air cycle machine (ACM) where excess moisture is removed and the temperature necessary for heating or cooling the airplane is established. The conditioned air is then delivered to the cabin and cockpit through the duct distribution system to maintain a comfortable environment.To optimize the system from the weight point of view, a complete analysis of each component must be considered and evaluated. The weight of the ECS is driven by the bleed air pressure and temperature which determines the size of the precooler (Reference SAWE Paper $#$ 3648; Engine Integration to Aircraft of Corporate Jets).The thermal heating and cooling load will determine the extracted bleed airflow quantity, which in turn, will impact the ACM size and weight.Most of the ECS components are designed and provided by suppliers but the air distribution ducts are laid out by the airframers and that deserves more attention. The adverse effect of paying little attention to duct optimization is a weight penalty and cost increase. The ducts' layout, size, and shape can lead to increased cabin's noise which is usually treated by additional sound attenuation materials on the account of weight, cost, and maintainability. The duct noise can also lead to other problems such as vibration and passenger's discomfort.This paper will focus on addressing the air distribution duct design and layout as related to weight optimization.},
keywords = {10. Weight Engineering - Aircraft Design, 24. Weight Engineering - System Design},
pubstate = {published},
tppubtype = {inproceedings}
}
2016
@inproceedings{3671,
title = {3671. Model Based Mass Properties Engineering at JPL},
author = {Morgan Hendry IV and Johannes Gross},
url = {https://www.sawe.org/product/paper-3671},
year = {2016},
date = {2016-05-01},
booktitle = {75th Annual Conference, Denver, Colorado},
pages = {11},
publisher = {Society of Allied Weight Engineers, Inc.},
address = {Denver, Colorado},
abstract = {The Soil Moisture Active Passive (SMAP) mission creates global soil moisture measurements every 2-3 days by spinning a lightweight, ~6 meter diameter deployable mesh reflector. This represents the largest spinning antenna ever to be used on a NASA satellite. The paper discusses the mass properties challenges that were overcome in implementing the mission, including the definition of a combined imbalance term called the Effective Product of Inertia, the selection of an optimum Spun Instrument focal length and edge offset that fostered a reduced mass properties sensitivity, the inclusion of late game Spun Instrument configuration flexibility, the use of balance mass locations that leveraged the large moment arm provided by the reflector, and a subassembly measurement campaign that reduced mass properties uncertainties on testable components.},
keywords = {12. Weight Engineering - Computer Applications, 24. Weight Engineering - System Design},
pubstate = {published},
tppubtype = {inproceedings}
}
@inproceedings{3672,
title = {3672. Weight's Importance in Machine Design},
author = {Jacob Hundl},
url = {https://www.sawe.org/product/paper-3672},
year = {2016},
date = {2016-05-01},
booktitle = {75th Annual Conference, Denver, Colorado},
pages = {9},
publisher = {Society of Allied Weight Engineers, Inc.},
address = {Denver, Colorado},
abstract = {This report will describe the prototyping, design, fabrication and testing of a device that was designed to propel golf and ping-pong balls a distance of at least three feet into separate containers. After a five second delay, the device was required to deposit the first ball into its container. At least five of each type of ball had to be deposited within twenty seconds of the release time. The device had to begin operation with a release or a flick of a switch. The device also had to cost less than $100 dollars and weigh less than ten pounds at testing. Finally, the device was required to be constructed out of raw materials. Any type of pre-fab system in the device would lead to the device's elimination. The device was graded more favorably if it was powered by gravity as opposed to electricity or a spring force. The simplicity of our device's design and its reliance on gravity as the driving force for the motion of the balls led us to believe that our design was very reliable. However, the observed difference in final and initial testing produced unexpected results.},
keywords = {24. Weight Engineering - System Design, Student Papers},
pubstate = {published},
tppubtype = {inproceedings}
}
2015
@inproceedings{3635,
title = {3635. Mass Properties - Flow of Information},
author = {V B Gomide de Paula and F V Abrantes and M Silveira de Matos and S C Meyer},
url = {https://www.sawe.org/product/paper-3635},
year = {2015},
date = {2015-05-01},
booktitle = {74th Annual Conference, Alexandria, Virginia},
pages = {14},
publisher = {Society of Allied Weight Engineers, Inc.},
address = {Alexandria, Virginia},
abstract = {Product development is a challenging process for any product, because aircraft are highly complex, interconnected, and should take into account a multiplicity of requirements, their design represents a challenge of the highest order. Hence, among the various requirements to be met by a new aircraft there are: cost, performance and sustainability requirements. The mass properties of the aircraft are intrinsically related to the fulfillment of these three requirements, consequently it is crucial that realistic estimates of aircraft mass properties be used during early conceptual design, and that it be strictly controlled during later stages of design.
The mass properties management has different characteristics depending on the product development phase; it has to be adjusted as the maturity of the aircraft increases and also depends on the technical integration status of the development. The main objective of this paper is to analyze how the mass properties flow of information should be between specialized groups and managers, in order to guarantee that the information on the lowest level of the system will be able to answer on the aircraft level. The integration has to give accurate and timely mass properties data for making design optimization decisions. The primary result of this work is the development of an integrated and user- friendly tool to track the achievement of the local target weight and impact on the global weight.
Keywords: mass properties, flow of information, requirements},
keywords = {17. Weight Engineering - Procedures, 24. Weight Engineering - System Design},
pubstate = {published},
tppubtype = {inproceedings}
}
The mass properties management has different characteristics depending on the product development phase; it has to be adjusted as the maturity of the aircraft increases and also depends on the technical integration status of the development. The main objective of this paper is to analyze how the mass properties flow of information should be between specialized groups and managers, in order to guarantee that the information on the lowest level of the system will be able to answer on the aircraft level. The integration has to give accurate and timely mass properties data for making design optimization decisions. The primary result of this work is the development of an integrated and user- friendly tool to track the achievement of the local target weight and impact on the global weight.
Keywords: mass properties, flow of information, requirements2010
@inproceedings{3493,
title = {3493. An Expanded Study of SAWE Paper 3468 - Quantifying Uncertainty and Risk in Vehicle Mass Properties Throughout the Design Development Phase},
author = {William Boze and Elizabeth Heaney},
url = {https://www.sawe.org/product/paper-3493},
year = {2010},
date = {2010-05-01},
booktitle = {69th Annual Conference, Virginia Beach, Virginia},
pages = {10},
publisher = {Society of Allied Weight Engineers, Inc.},
address = {Virginia Beach, Virginia},
abstract = {SAWE Paper No. 3468 (Boze & Hester, 2009) demonstrated
that uncertainty and risk can be quantified by coupling a
Monte Carlo simulation using Microsoft Excel, mass
properties data, a work breakdown structure, uncertainty
categories, and derived probability distributions. The risk can
be assessed by evaluating the probability of occurrence, the
standard deviation, and the coefficient of variation resulting
from randomly varying the mass properties variable within an
uncertainty category's probability distribution.
The original paper demonstrated this approach using data
collected over an 18 month period on an existing ship
acquisition program. The purpose of this paper is to broaden
the range of mass properties data used in the same simulation
model to a five year design acquisition life cycle in order to
gain increased insight into the use of this method. New
observations will be drawn as to the required number of
simulation runs, the various measures of risk, affects on risk of
physical platform changes to satisfy performance requirement
changes, as well as disclosing improved graphic methods for
displaying some risk data.},
keywords = {17. Weight Engineering - Procedures, 21. Weight Engineering - Statistical Studies, 24. Weight Engineering - System Design},
pubstate = {published},
tppubtype = {inproceedings}
}
that uncertainty and risk can be quantified by coupling a
Monte Carlo simulation using Microsoft Excel, mass
properties data, a work breakdown structure, uncertainty
categories, and derived probability distributions. The risk can
be assessed by evaluating the probability of occurrence, the
standard deviation, and the coefficient of variation resulting
from randomly varying the mass properties variable within an
uncertainty category's probability distribution.
The original paper demonstrated this approach using data
collected over an 18 month period on an existing ship
acquisition program. The purpose of this paper is to broaden
the range of mass properties data used in the same simulation
model to a five year design acquisition life cycle in order to
gain increased insight into the use of this method. New
observations will be drawn as to the required number of
simulation runs, the various measures of risk, affects on risk of
physical platform changes to satisfy performance requirement
changes, as well as disclosing improved graphic methods for
displaying some risk data.@inproceedings{3508,
title = {3508. Methods and Benefits of Detailed Wire Weight Accounting},
author = {ANDREW FLUEGEL and NICK NASCHANSKY},
url = {https://www.sawe.org/product/paper-3508},
year = {2010},
date = {2010-05-01},
booktitle = {69th Annual Conference, Virginia Beach, Virginia},
pages = {12},
publisher = {Society of Allied Weight Engineers, Inc.},
address = {Virginia Beach, Virginia},
abstract = {A method of projecting, tracking, measuring and reporting wire weights used, by the
Gulfstream Aerospace Mass Properties Department, for an aircraft development program
will be presented and discussed. Program wire weight accounting and control goals were
to accurately track and project the total weight of the electrical system by harness, while
measuring weight maturity against system allocated weights. The paper will present our
approach from the beginning of the project, where goals and reporting requirements were
defined, through to the end where measured harness weights were used to verify
methods.
A detailed wire weight accounting approach was used. This involved tracking all wire
harness weights by the system assigned to individual wires and connectors, then
comparing those weights to the system weight allocation. System allocations were used
to determine RP8 groupings for reporting. After iterative accounting automations that
facilitated processing and management of weight data the detailed method proved to be
both manageable and beneficial for both the program aircraft as it matures, and future
programs.},
keywords = {20. Weight Engineering - Specifications, 24. Weight Engineering - System Design},
pubstate = {published},
tppubtype = {inproceedings}
}
Gulfstream Aerospace Mass Properties Department, for an aircraft development program
will be presented and discussed. Program wire weight accounting and control goals were
to accurately track and project the total weight of the electrical system by harness, while
measuring weight maturity against system allocated weights. The paper will present our
approach from the beginning of the project, where goals and reporting requirements were
defined, through to the end where measured harness weights were used to verify
methods.
A detailed wire weight accounting approach was used. This involved tracking all wire
harness weights by the system assigned to individual wires and connectors, then
comparing those weights to the system weight allocation. System allocations were used
to determine RP8 groupings for reporting. After iterative accounting automations that
facilitated processing and management of weight data the detailed method proved to be
both manageable and beneficial for both the program aircraft as it matures, and future
programs.2009
@inproceedings{3469,
title = {3469. Comparison of Power Distribution Systems for Land Vehicles},
author = {Jack Al-Kahwati},
url = {https://www.sawe.org/product/paper-3469},
year = {2009},
date = {2009-05-01},
booktitle = {68th Annual Conference, Wichita, Kansas},
pages = {10},
address = {Wichita, Kansas},
abstract = {For combat vehicles, power distribution systems face a
multitude of challenges caused by shrinking space availability,
demanding thermal environments, reliability constraints, and the
need to reduce system weight. This paper investigates the trade
between two different design methodologies: cable conductors and
bus bar concepts. The design approach and thermal assessments are
investigated to achieve a weight optimized solution for high
powered applications.
In this study, a 2D Computation Fluid Dynamic (CFD) model is
created to simulate the natural convection and conduction cooling
of the cable conductor and a laminated bus structure.},
keywords = {24. Weight Engineering - System Design, 31. Weight Engineering - Surface Transportation},
pubstate = {published},
tppubtype = {inproceedings}
}
multitude of challenges caused by shrinking space availability,
demanding thermal environments, reliability constraints, and the
need to reduce system weight. This paper investigates the trade
between two different design methodologies: cable conductors and
bus bar concepts. The design approach and thermal assessments are
investigated to achieve a weight optimized solution for high
powered applications.
In this study, a 2D Computation Fluid Dynamic (CFD) model is
created to simulate the natural convection and conduction cooling
of the cable conductor and a laminated bus structure.2008
@inproceedings{3437,
title = {3437. Development and Implementation of a Space Systems Mass Properties Process},
author = {Jesse Peterson and Otto G. Ratz and Dr. Angela Trego},
url = {https://www.sawe.org/product/paper-3437},
year = {2008},
date = {2008-05-01},
booktitle = {67th Annual Conference, Seattle, Washington},
pages = {10},
address = {Seattle, Washington},
abstract = {ATK Launch Systems is the world leader in solid rocket motor design and manufacturing. The Systems Engineering and Integration (SE&I) team within the Advanced Programs group was tasked with developing a mass properties process for very large and complex systems. This process was to include a definition of what mass properties information needed to be tracked, how the information was going to be calculated and tracked, and where the information would be stored. The SE&I team chose to use the AIAA S-120-2006 [1] standard as a basis for the new process. This standard provided suggestions for what information should be tracked, and what the mass growth allowance (MGA) and mass margin (MM) depletion schedule should look like for a space system, including mass assessment Technical Performance Measure (TPM) guidelines. With the AIAA guidelines [1] in mind, the SE&I team developed a new mass properties control plan. This control plan included the process for calculating MGA and MM depletion schedules, and mass assessment roll ups, including TPMs, for assemblies with components in various design stages. The traditional roll up as outlined in the AIAA standard [1] suggests components within assemblies follow the same schedule with different percentages based on maturity. ATK chose to develop an approach to allow different schedules for each component / assembly based on the component / assembly specific development schedule and maturity. The mass properties process also included the method for tracking detail part changes real time, and calculating and reporting TPMs for mass assessment, the number of component mass changes, and the time sequenced mass properties. All of the knowledge contained within the control plan was then captured within a MATLAB application which calculated the time sequenced mass properties, the mass depletion schedule of the system, and output the required TPMs programmatically. The MATLAB application also created a formatted mass properties report, and a data file containing all of the time sequenced mass properties information for use by other groups. This process and application can be used on any large system, and it is ideal for systems which implement the AIAA approach [1] to mass properties control. With little time and effort on the part of the mass properties engineer, a great deal of data can be created programmatically.},
keywords = {17. Weight Engineering - Procedures, 24. Weight Engineering - System Design},
pubstate = {published},
tppubtype = {inproceedings}
}
@inproceedings{3448,
title = {3448. The Role of Effective Mass Property Management in a Global Product Creation Process},
author = {Claudia Heim and Holger Pertermann},
url = {https://www.sawe.org/product/paper-3448},
year = {2008},
date = {2008-05-01},
booktitle = {67th Annual Conference, Seattle, Washington},
pages = {18},
address = {Seattle, Washington},
abstract = {Mass property Management is an integral part of the overall system design. Therefore the information should be managed like other requirement and design data in a centralized location. This could be either a specific database application, which is closely linked to other product data in a PLM system, or it is embedded into the enterprise PLM system.
This paper outlines specific requirements to a PLM system, which has been implemented at a large tier1 automotive supplier for advanced product data management with integrated mass property handling. The first discussed challenge for complex system design is the huge variety of different configurations - which can easily lead to millions of combinations. The handling of mass properties in combination with different configurations is one of the most complex tasks. The introduction of a conceptual product structure is a very powerful vehicle to meet this requirement. In general the end product of each aerospace and automotive supplier has always a similar body structure, whatever it is - a plane or a car. A plane has in general engines and wings; each car has wheels and a roof. Therefore the manufacturer has lots of information, which he can re-use from his past projects. The discussed Conceptual Product Structure describes the data model, which supports advanced tasks in product data management with all the different aspects of aggregating information like mass properties.
The next discussion point is a methodology of how to create target views (Parallel Structures) for different departments (mass, regulations, materials/environmental, supplier). This is a quite interesting methodology, if mass management is treated as part of the overall organization, contributing to one end product.
The last topic which will be discussed is the role of configuration management throughout the product lifecycle and its impact on the mass properties. Bringing different information sets for mass properties of different design stages together and keep track of all the changes, requires also in the mass property department clean processes for an efficient configuration management. As long as mass property information is part of the global information set, this shouldn't be an issue in theory. In this paper it will be discussed, what processes are affected if mass property management is done outside the enterprise system.
The paper will close with the discussion of how efficient mass property management systems will address the need for globalization. Especially, the role of Service Oriented Architectures (SOA) will address the increasing business process complexity in global organizations.},
keywords = {16. Weight Engineering - Organization, 24. Weight Engineering - System Design},
pubstate = {published},
tppubtype = {inproceedings}
}
This paper outlines specific requirements to a PLM system, which has been implemented at a large tier1 automotive supplier for advanced product data management with integrated mass property handling. The first discussed challenge for complex system design is the huge variety of different configurations - which can easily lead to millions of combinations. The handling of mass properties in combination with different configurations is one of the most complex tasks. The introduction of a conceptual product structure is a very powerful vehicle to meet this requirement. In general the end product of each aerospace and automotive supplier has always a similar body structure, whatever it is - a plane or a car. A plane has in general engines and wings; each car has wheels and a roof. Therefore the manufacturer has lots of information, which he can re-use from his past projects. The discussed Conceptual Product Structure describes the data model, which supports advanced tasks in product data management with all the different aspects of aggregating information like mass properties.
The next discussion point is a methodology of how to create target views (Parallel Structures) for different departments (mass, regulations, materials/environmental, supplier). This is a quite interesting methodology, if mass management is treated as part of the overall organization, contributing to one end product.
The last topic which will be discussed is the role of configuration management throughout the product lifecycle and its impact on the mass properties. Bringing different information sets for mass properties of different design stages together and keep track of all the changes, requires also in the mass property department clean processes for an efficient configuration management. As long as mass property information is part of the global information set, this shouldn't be an issue in theory. In this paper it will be discussed, what processes are affected if mass property management is done outside the enterprise system.
The paper will close with the discussion of how efficient mass property management systems will address the need for globalization. Especially, the role of Service Oriented Architectures (SOA) will address the increasing business process complexity in global organizations.2007
@inproceedings{3403,
title = {3403. Topology Optimization on the Example of an Advanced Trainer Aircraft},
author = {Hansjürgen Anton and Herbert Hörnlein},
url = {https://www.sawe.org/product/paper-3403},
year = {2007},
date = {2007-05-01},
booktitle = {66th Annual Conference, Madrid, Spain},
pages = {12},
publisher = {Society of Allied Weight Engineers},
address = {Madrid, Spain},
organization = {Society of Allied Weight Engineers},
abstract = {During the concept and definition phase of an aircraft, it is essential to define a structural concept, which provides the required strength and stiffness constraints of the airframe, subjected to a minimum of weight. The most efficient way of load transfer is a straight and undisturbed load path. However, the design space of the airframe is restricted by the outboard profile, which is defined by aerodynamics and flight mechanics and is also determined by the inboard profile, which is driven by systems installations. Howeve,r there are situations where a major load path cannot be continued, as is ideal. This presentation shows an example of how topology optimization can give one an idea to find an alternative load path. The example is given by a main wing attachment frame, which has the task of carrying the wing bending moment from one wing to the other. However, the air intake duct disturbs the assumed load path. There were some doubts by experienced airframe designers whether this air vehicle concept would work in an acceptable way in terms of mass and strength. The results of the topology optimization unveiled an alternative load path, which is subsequently interpretable by airframe engineers. This presentation also shows how the process goes from a given design to data for manufacturing.},
keywords = {10. Weight Engineering - Aircraft Design, 24. Weight Engineering - System Design},
pubstate = {published},
tppubtype = {inproceedings}
}
@inproceedings{3419,
title = {3419. Effect of Unstable Modern Fighter Aircraft Design on Mass Control (An example of the Eurofighter aircraft)},
author = {Roland Reinartz},
url = {https://www.sawe.org/product/paper-3419},
year = {2007},
date = {2007-05-01},
booktitle = {66th Annual Conference, Madrid, Spain},
pages = {14},
publisher = {Society of Allied Weight Engineers},
address = {Madrid, Spain},
organization = {Society of Allied Weight Engineers},
abstract = {The Mass Property Engineer's role in the classical aircraft design process is to provide reliable mass property information to the engineering organization in order to enable the optimization of the aircraft layout and performance. In the course of the design process, the role of Mass Properties Engineers is normally focused on weight control, reducing the weight growth occurring during product realization. Unstable modern fighter aircraft require mass data for their computerized flight control system. As a consequence of this requirement, the mass engineer's field of activity is extended to monitor the aircraft mass also during the in-service operation. This paper will describe what data is required by the flight control system, how these data are generated, and the implications of this on the weights engineers' community using the example of the aerodynamically highly unstable Eurofighter. It will also identify the parameters, which ultimately determine the accuracy of the required data. It is concluded that the resulting mass data generation process is a compromise between the requirements of aircraft performance, in-service operation, and the associated costs.},
keywords = {24. Weight Engineering - System Design, 34. Advanced Design},
pubstate = {published},
tppubtype = {inproceedings}
}
2006
@inproceedings{3390,
title = {3390. Mass Body Data Collection System},
author = {John Cooper and Buddy Sinor},
url = {https://www.sawe.org/product/paper-3390},
year = {2006},
date = {2006-05-01},
booktitle = {65th Annual Conference, Valencia, California},
pages = {13},
publisher = {Society of Allied Weight Engineers},
address = {Valencia, California},
organization = {Society of Allied Weight Engineers},
abstract = {In designing a new system for a modern fighter aircraft, our team was tasked with characterizing the vibration environment in the nose of the fighter. This system would have to be small, light, and have as little interaction with the aircraft as possible. Time constraints necessitated using a collection of Commercial Off The Shelf (COTS) systems that but still had to operate in a fighter aircraft environment.},
keywords = {24. Weight Engineering - System Design},
pubstate = {published},
tppubtype = {inproceedings}
}
2005
@inproceedings{3364,
title = {3364. Conceptual Level Mass Properties of an All-Mach Aerospace Plane},
author = {Ian O. MacConochie},
url = {https://www.sawe.org/product/paper-3364},
year = {2005},
date = {2005-05-01},
booktitle = {64th Annual Conference, Annapolis, Maryland},
pages = {13},
publisher = {Society of Allied Weight Engineers, Inc.},
address = {Annapolis, Maryland},
abstract = {The mass properties are identified for a plane that is an 'aerospace' plane in the literal sense in that it can take off at sea level and fly on a ballistic trajectory above the atmosphere. The vehicle is tactical in nature, as opposed to logistical, having a crew of two and a payload limited to under-wing missiles. The configuration is dominated by the engine duct which makes up the main body airframe.
The propulsion system is made up of a traditional jet engine mounted in the forward end of the duct and a JP rocket engine mounted aft. Annulus space around the two engines serves as area cross-section for ramjet operation. Structure and thermal protection are modeled after the X-15 rocket plane that flew on a ballistic trajectory to Mach 6.7 and an altitude of 150,000 ft.},
keywords = {24. Weight Engineering - System Design},
pubstate = {published},
tppubtype = {inproceedings}
}
The propulsion system is made up of a traditional jet engine mounted in the forward end of the duct and a JP rocket engine mounted aft. Annulus space around the two engines serves as area cross-section for ramjet operation. Structure and thermal protection are modeled after the X-15 rocket plane that flew on a ballistic trajectory to Mach 6.7 and an altitude of 150,000 ft.2000
@inproceedings{3008,
title = {3008. The Systems Engineering Role in Mass Properties},
author = {Jonathan Morgan},
url = {https://www.sawe.org/product/paper-3008},
year = {2000},
date = {2000-06-01},
booktitle = {59th Annual Conference, St. Louis, Missouri, June 5-7},
pages = {7},
publisher = {Society of Allied Weight Engineers, Inc.},
address = {St. Louis, Missouri},
abstract = {For missile Engineering Manufacturing and Development (EMD) programs, mass properties is defined as the weight, center of gravity, moment of inertia, and roll unbalance of the missile. Mechanical and Systems Engineering departments continually debate over control of mass properties. Systems Engineering has the advantage of knowing the top level requirements, requirements flowdown, and the ability to allocate budgets accordingly, including mass properties. Program decisions are all made at the systems level and require a systems engineer to flow into lower level requirements. The Mechanical group has close contact with the hardware and an intimate knowledge of the buildup of the missile. Unfortunately, they do not have close contact with all the design and simulation teams requiring mass properties, or understand some of the program level requirements that influence mass properties. Mass properties are used by many organizations and have special needs that the Systems Engineering Team is best able to meet and the Systems Engineering approach to mass properties will be addressed in the paper. Regardless of which department claims the Mass Properties Engineer, the information provided will help give any engineer a better understanding of the importance and correct use of mass properties.},
keywords = {24. Weight Engineering - System Design},
pubstate = {published},
tppubtype = {inproceedings}
}
1998
@inproceedings{2423,
title = {2423. What is Design to Cost?},
author = {S Lucas},
url = {https://www.sawe.org/product/paper-2423},
year = {1998},
date = {1998-05-01},
booktitle = {57th Annual Conference, Wichita, Kansas, May 18-20},
pages = {10},
publisher = {Society of Allied Weight Engineers, Inc.},
address = {Wichita, Kansas},
abstract = {With the cost of competing designs becoming an integral part of any analysis, design trade studies are increasingly relevant. By the end of the concept definition phase of a program, about 80 percent of system life cycle costs (LCC) me committed, and by the time drawings are signed off by the engineer approximately 95 percent of life cycle costs are already determined. One method to ensure that competitive cost goals are achieved is to apply Design to Cost (DTC)) principles to all projects. Mandated by government regulations for acquisition or modification programs with design efforts, DTC is extremely important. DTC is not value engineering or bottoms up estimating from detailed parts lists, although these activities may take place during DTC within certain program phases. DTC is the design and development of an item to meet a cost target or cost range. That is, in order to be DTC activity, there must be both design activity and a cost target. This paper addresses DTC from a global perspective.},
keywords = {24. Weight Engineering - System Design},
pubstate = {published},
tppubtype = {inproceedings}
}
@inproceedings{2429,
title = {2429. Integrated Thermal Energy Management System},
author = {N Carter},
url = {https://www.sawe.org/product/paper-2429},
year = {1998},
date = {1998-05-01},
booktitle = {57th Annual Conference, Wichita, Kansas, May 18-20},
pages = {25},
publisher = {Society of Allied Weight Engineers, Inc.},
address = {Wichita, Kansas},
abstract = {(None)},
keywords = {24. Weight Engineering - System Design},
pubstate = {published},
tppubtype = {inproceedings}
}
1988
@inproceedings{1818,
title = {1818. Weight Savings in Aerospace Vehicles Through Propellant Scavenging},
author = {S J Dr. Schneider},
url = {https://www.sawe.org/product/paper-1818},
year = {1988},
date = {1988-05-01},
booktitle = {47th Annual Conference, Plymouth, Michigan, May 23-25},
pages = {41},
publisher = {Society of Allied Weight Engineers, Inc.},
address = {Plymouth, Michigan},
abstract = {This paper addresses the vehicle payload benefits of scavenging hydrogen and oxygen propellants from the launch propulsion system reserves and residuals for utilization in the auxiliary propulsion system. The Shuttle II vehicle on a Space Station rendezvous mission is chosen for study. The propellant scavenging system scavenges propellants from the launch propulsion tankage during orbital maneuvers and stores them in well insulated liquid accumulators for use in a cryogenic auxiliary propulsion system. The fraction of auxiliary propulsion propellant which may be scavenged for propulsive purposes is estimated to be 45.1%. The auxiliary propulsion subsystem dry mass, including the proposed scavenging system, an additional 20% for secondary structure, an additional 5% for electrical service, a 10% weight growth margin, and 15.4% propellant reserves and residuals is estimated to be 6331 kg (13958 lbm).},
keywords = {24. Weight Engineering - System Design},
pubstate = {published},
tppubtype = {inproceedings}
}
1986
@inproceedings{1743,
title = {1743. Fifteen Years of Flight Control Evolution on European Airbus Aircraft Weight Impact},
author = {M Hammen},
url = {https://www.sawe.org/product/paper-1743},
year = {1986},
date = {1986-05-01},
booktitle = {45th Annual Conference, Williamsburg, Virginia, May 12-14},
pages = {25},
publisher = {Society of Allied Weight Engineers, Inc.},
address = {Williamsburg, Virginia},
abstract = {Most civil transport aircraft flying today have moving surfaces that are controlled mechanically by hydraulic servomotors. In order to improve aircraft performance these controls have become more and more complicated and have now become a nightmare of complexity from the design and maintenance points of view. Within Airbus Industrie Aerospatiale is responsible for flight control and has developed a new concept: ''Fly-by-wire''. This paper will present the technological evolution of flight controls since the A300-B4 aircraft with mechanical controls, the A310 and A300-bUO with some electrical secondary flight controls, up to the A320 with electric primary pitch and roll controls and the introduction of the side-stick controller. The fifteen years of evolution introduce a direct weight saving of about 30 ~ of the total flight control weight; this weight impact will be examined, dissociating the different functions and mechanical and electrical parts. Other indirect weight benefits appear on the wing structure thanks to load alleviation, or flight deck layout by removal of the conventional control columns. What is important above all is for this weight saving to be accompanied by other benefits of a different nature, such as: improved control surface efficiency, improved safety thanks to protection systems in electronic computers for flight envelope limits, and reduced crew work load. After an initial application on the Concorde supersonic aircraft, fly-by-wire controls have been developed and improved on the Airbus A320, mainly thanks to the progress made in the field of electronic and airborne computers. The future promises considerable evolutions as a result of research on electrical power servo-actuators and fully electric flight controls.},
keywords = {24. Weight Engineering - System Design},
pubstate = {published},
tppubtype = {inproceedings}
}