SAWE Technical Papers
Technical Library
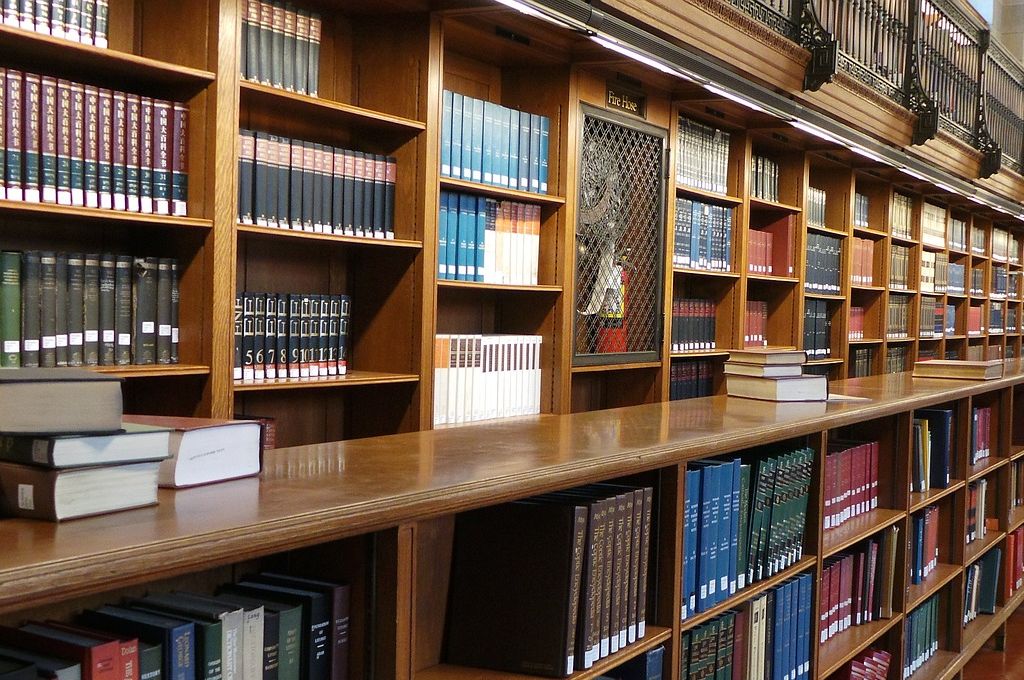
SAWE Paper Database
The SAWE Technical Library contains nearly 4000 technical papers available here for purchase and download. Use the search options below to find what you need.
3768. Mass Properties Reporting Ma, Yiyuan; Yan, Jin; Elham, Ali In: 2021 SAWE Tech Fair, pp. 28, Society of Allied Weight Engineers, Inc., Virtual Conference, 2021. Abstract | Buy/Download | BibTeX | Tags: 10. Weight Engineering - Aircraft Design, 11. Weight Engineering - Aircraft Estimation, Student Papers Konersmann, M.; Schmidt, M.; Neveling, S.; Scholjegerdes, M.; Diekmann, F.; Moxter, T.; Nuño, Miguel In: 2020 SAWE Tech Fair, pp. 16, Society of Allied Weight Engineers, Inc., Virtual Conference, 2020. Abstract | Buy/Download | BibTeX | Tags: 11. Weight Engineering - Aircraft Estimation, 21. Weight Engineering - Statistical Studies, Student Papers 3749. One Fits All? A Comparison of Weight Estimation Methods for Preliminary Aircraft Design Kluender, Arthur; Gobbin, Andreas In: 2020 SAWE Tech Fair, pp. 17, Society of Allied Weight Engineers, Inc., Virtual Conference, 2020. Abstract | Buy/Download | BibTeX | Tags: 11. Weight Engineering - Aircraft Estimation, 21. Weight Engineering - Statistical Studies, Student Papers 3709. A Wing Weight Estimation Method Based on Wing-box Beam Design Bai, Lu; Deng, Zhi; Zhang, Xintan; Xia, Ming; Wang, Jianli In: 2020 SAWE Tech Fair, pp. 12, Society of Allied Weight Engineers, Inc., Virtual Conference, 2020. Abstract | Buy/Download | BibTeX | Tags: 11. Weight Engineering - Aircraft Estimation, 23. Weight Engineering - Structural Estimation 3732. Class II & 1/2 Mass Estimation of Light Aircraft Composite Wings Nuño, Miguel; Schröder, K. U. In: 2020 SAWE Tech Fair, pp. 12, Society of Allied Weight Engineers, Inc., Virtual Conference, 2020. Abstract | Buy/Download | BibTeX | Tags: 11. Weight Engineering - Aircraft Estimation, 23. Weight Engineering - Structural Estimation 3735. Weight and Balance Challenges for Hybrid Electric Propulsion System Paula, Vera; Vogel, Dr. Florian In: 2020 SAWE Tech Fair, pp. 16, Society of Allied Weight Engineers, Inc., Virtual Conference, 2020. Abstract | Buy/Download | BibTeX | Tags: 11. Weight Engineering - Aircraft Estimation, 34. Advanced Design 3736. Hydrogen Fuel Cell Power System Weight Challenges in VTOL Aircraft Ray, Greg; Rainville, Joseph D. In: 2020 SAWE Tech Fair, pp. 16, Society of Allied Weight Engineers, Inc., Virtual Conference, 2020. Abstract | Buy/Download | BibTeX | Tags: 11. Weight Engineering - Aircraft Estimation, 34. Advanced Design 3729. Application of SAWE Course 'Developing Basic Parametric Methods' to Nacelle Weight Estimating Fisher, Doug In: 78th Annual Conference, Norfolk, VA, pp. 17, Society of Allied Weight Engineers, Inc., Norfolk, Virginia, 2019. Abstract | Buy/Download | BibTeX | Tags: 10. Weight Engineering - Aircraft Design, 11. Weight Engineering - Aircraft Estimation, 21. Weight Engineering - Statistical Studies 3685. Design of an internal aerodynamic load cell for static for oscillating airfoils Miloud, Kamal Ben; Fellouah, Hachimi In: 76th Annual Conference, Montreal, Canada, pp. 7, Society of Allied Weight Engineers, Inc., Montreal, Canada, 2017. Abstract | Buy/Download | BibTeX | Tags: 11. Weight Engineering - Aircraft Estimation, Student Papers 3691. Methods to Evaluate the Mass Properties of a Scale Model Aircraft Kohtanen, Eetu; Davis, R. Benjamin In: 76th Annual Conference, Montreal, Canada, pp. 12, Society of Allied Weight Engineers, Inc., Montreal, Canada, 2017. Abstract | Buy/Download | BibTeX | Tags: 06. Inertia Measurements, 08. Weighing, 11. Weight Engineering - Aircraft Estimation, Student Papers 3692. Aircraft Systems Physics-Based Weight Estimation Methods for Conceptual Design Tfaily, Ali; Liscouët-Hanke, Dr. Susan In: 76th Annual Conference, Montreal, Canada, pp. 12, Society of Allied Weight Engineers, Inc., Montreal, Canada, 2017. Abstract | Buy/Download | BibTeX | Tags: 11. Weight Engineering - Aircraft Estimation, 25. Weight Engineering - System Estimation, 34. Advanced Design 3660. Development of a Conceptual Flight Vehicle Design Weight Estimation Method Library Walker, Andy In: 75th Annual Conference, Denver, Colorado, pp. 171, Society of Allied Weight Engineers, Inc., Denver, Colorado, 2016, (Mike HackneyBest Paper Award - 2016). Abstract | Buy/Download | BibTeX | Tags: 10. Weight Engineering - Aircraft Design, 11. Weight Engineering - Aircraft Estimation, Mike Hackney Best Paper Award 3627. Multifidelity Overall AC Mass Model: Fit for Purpose Mass Models for Overall Aircraft Design Reina, A. Rodriguez; Ferran, S. Lanzàn In: 73rd Annual Conference, Long Beach California, pp. 13, Society of Allied Weight Engineers, Inc., Long Beach, California, 2014. Abstract | Buy/Download | BibTeX | Tags: 11. Weight Engineering - Aircraft Estimation 3629. The Mysterious Art of Weight Estimation of Large Civil Aircraft Cheeseman, Judi In: 73rd Annual Conference, Long Beach California, pp. 10, Society of Allied Weight Engineers, Inc., Long Beach, California, 2014. Abstract | Buy/Download | BibTeX | Tags: 11. Weight Engineering - Aircraft Estimation 3597. Aircraft Weight Estimation In Interactive Design Process Al-Shamma, Omran; Ali, Dr. Rashid In: 72nd Annual Conference, St. Louis, Missouri, pp. 11, Society of Allied Weight Engineers, Inc., Saint Louis, Missouri, 2013. Abstract | Buy/Download | BibTeX | Tags: 11. Weight Engineering - Aircraft Estimation Moghadasi, Seyyedeh Maryam; Elham, Ali; Voskuijl, Mark In: 72nd Annual Conference, St. Louis, Missouri, pp. 18, Society of Allied Weight Engineers, Inc., Saint Louis, Missouri, 2013. Abstract | Buy/Download | BibTeX | Tags: 11. Weight Engineering - Aircraft Estimation Eberle, Albrecht In: 71st Annual Conference, Bad Gögging, Germany, pp. 17, Society of Allied Weight Engineers, Inc., Bad Gögging, Germany, 2012. Abstract | Buy/Download | BibTeX | Tags: 11. Weight Engineering - Aircraft Estimation 3559. Fuel Mass Properties Calculation with CATIA V5 Funk, Ralf In: 71st Annual Conference, Bad Gögging, Germany, pp. 21, Society of Allied Weight Engineers, Inc., Bad Gögging, Germany, 2012. Abstract | Buy/Download | BibTeX | Tags: 11. Weight Engineering - Aircraft Estimation, 12. Weight Engineering - Computer Applications 3564. Multi-Fidelity Wing Mass Estimations Based On A Central Model Approach Böhnke, Daniel; Dorbath, Felix; Nagel, Björn; Gollnick, Volker In: 71st Annual Conference, Bad Gögging, Germany, pp. 18, Society of Allied Weight Engineers, Inc., Bad Gögging, Germany, 2012. Abstract | Buy/Download | BibTeX | Tags: 11. Weight Engineering - Aircraft Estimation, 23. Weight Engineering - Structural Estimation Schweiger, Johannes; Büsing, Moritz; Feger, Jens In: 71st Annual Conference, Bad Gögging, Germany, pp. 19, Society of Allied Weight Engineers, Inc., Bad Gögging, Germany, 2012. Abstract | Buy/Download | BibTeX | Tags: 11. Weight Engineering - Aircraft Estimation2021
@inproceedings{3768,
title = {3768. Mass Properties Reporting},
author = {Yiyuan Ma and Jin Yan and Ali Elham},
url = {https://www.sawe.org/product/paper-3768},
year = {2021},
date = {2021-11-01},
urldate = {2021-11-01},
booktitle = {2021 SAWE Tech Fair},
pages = {28},
publisher = {Society of Allied Weight Engineers, Inc.},
address = {Virtual Conference},
abstract = {The Ultra-High Aspect Ratio Wing (UHARW) concept can improve the aircraft's aerodynamic efficiency and reduce fuel consumption. The Twin-Fuselage (TF) configuration is one of the most promising concepts for the UHARW design to reduce the wing bending moments and shear forces. This paper presents the development of a semi-empirical method for the weight estimation of TF aircraft in the initial sizing stage. A physics-based wing weight estimation method is improved for higher aerodynamic analysis fidelity and composite materials, which is used in the design of experiments and the results are applied for regression analysis to establish a semi-empirical method. Eventually, the established semi- empirical weight estimation method is integrated into a TF aircraft conceptual design and performance analysis framework, and a mid-range TF aircraft and a long-range TF aircraft are designed and sized to illustrate its application and efficiency in rapidly estimating the TF aircraft weight breakdown.},
keywords = {10. Weight Engineering - Aircraft Design, 11. Weight Engineering - Aircraft Estimation, Student Papers},
pubstate = {published},
tppubtype = {inproceedings}
}
2020
@inproceedings{3743,
title = {3743. FVA30: Application of Probabilistic Mass Estimation Methods to the Design of a Touring Motor Glider},
author = {M. Konersmann and M. Schmidt and S. Neveling and M. Scholjegerdes and F. Diekmann and T. Moxter and Miguel Nuño},
url = {https://www.sawe.org/product/paper-3743},
year = {2020},
date = {2020-07-01},
booktitle = {2020 SAWE Tech Fair},
pages = {16},
publisher = {Society of Allied Weight Engineers, Inc.},
address = {Virtual Conference},
abstract = {In early design phases the mass and position of many aircraft components is uncertain. So, it is not possible to accurately calculate key aircraft parameters such as the total mass and center of gravity. A possible approach to deal with these uncertainties is using pessimistic and optimistic estimations for every component. This approach considers only the boundary values and can therefore lead to very conservative decisions. To reduce the uncertainty of the calculations and get a better estimation of the expected mass properties probabilistic mass estimation methods can be used.The FVA 30 is a hybrid electric motorglider being developed by students at the Flugwissenschaftliche Vereinigung Aachen (FVA). The configuration of the prototype features two electric engines in the V-tail unit and is therefore especially sensitive to mass changes. In this paper the usage of probabilistic mass estimation and propagation methods to design the FVA 30 is presented. Several methods to estimate probability distributions of different components are described. The propagation of uncertainties is calculated using Monte Carlo simulations with random sampling. At last, the probabilistic calculation results are discussed and compared with the ones using a deterministic method.},
keywords = {11. Weight Engineering - Aircraft Estimation, 21. Weight Engineering - Statistical Studies, Student Papers},
pubstate = {published},
tppubtype = {inproceedings}
}
@inproceedings{3749,
title = {3749. One Fits All? A Comparison of Weight Estimation Methods for Preliminary Aircraft Design},
author = {Arthur Kluender and Andreas Gobbin},
url = {https://www.sawe.org/product/paper-3749},
year = {2020},
date = {2020-07-01},
booktitle = {2020 SAWE Tech Fair},
pages = {17},
publisher = {Society of Allied Weight Engineers, Inc.},
address = {Virtual Conference},
abstract = {Is there any compelling way to precisely determine the major masses of an aircraft in preliminary design stages? If so, do the results match the real airplane weight properties, when it is built? This paper presents a comprehensive overview of commonly used approaches, highlighting their individual (dis)advantages and eligibility for typical transport missions. The study evaluates widely used, of-the-book-methods for weight estimation and searches for the most accurate approach among them. Each method is applied to determine the masses of four different aircraft, each of them representing a typical aircraft category. The results are put in relation to the real masses, extracted from the corresponding manufacturers manual. In addition, an extended and modified method, already existing and being used at the Department for Aircraft Design and Lightweight Structures at the Technical University of Berlin, is included in the study and tested for its reliability. The overall objective of this paper is to evaluate, whether there is a method that precisely calculates all relevant masses or else, which one delivers the most accurate results for various aircraft types. In order to differentiate even further, the set of required input parameters is considered. In early design phases, typically only a few of those are known. Hence, a method that leads to accurate results with minimal input is favorable for preliminary design. The study indicates that none of the methods covers all the aircraft types. However, tendencies show that some approaches suit certain aircraft types better than others. Most of them provide satisfactory results for an average, jet-engine propelled, single aisle, medium range aircraft in conventional twinjet configuration. Regarding more unusual configurations, for example with turboprop engines, the outcome differs noticeably. Also, for long range aircraft, only a few methods produce realistic numbers. According to this exploration, guidelines on when to use which method are provided. This is followed by an outlook, giving recommendations on the development of new methods. Ultimately, a suggestion on how to consider new technologies and implement them into existing methods of weight estimation is given.},
keywords = {11. Weight Engineering - Aircraft Estimation, 21. Weight Engineering - Statistical Studies, Student Papers},
pubstate = {published},
tppubtype = {inproceedings}
}
@inproceedings{3709,
title = {3709. A Wing Weight Estimation Method Based on Wing-box Beam Design},
author = {Lu Bai and Zhi Deng and Xintan Zhang and Ming Xia and Jianli Wang},
url = {https://www.sawe.org/product/paper-3709},
year = {2020},
date = {2020-07-01},
urldate = {2020-07-01},
booktitle = {2020 SAWE Tech Fair},
pages = {12},
publisher = {Society of Allied Weight Engineers, Inc.},
address = {Virtual Conference},
abstract = {In this paper, a wing weight estimation method for transport aircraft is presented. By establishing related computational framework, a wing-box model is developed based on wing-box beam design, from where a wing weight estimation method is derived. The key steps of this work include parametric modeling based on structural model simplification, aerodynamic study, finite element method, and aeroelastic analysis. The influence of the mounted pylon has been considered for the wing-box sizing. This method has been validated using data of two different transport aircrafts, which shows that this method is robust and efficient. Outcome of this paper could be rapidly integrated in the conceptual design phase.},
keywords = {11. Weight Engineering - Aircraft Estimation, 23. Weight Engineering - Structural Estimation},
pubstate = {published},
tppubtype = {inproceedings}
}
@inproceedings{3732,
title = {3732. Class II & 1/2 Mass Estimation of Light Aircraft Composite Wings},
author = {Miguel Nuño and K. U. Schröder},
url = {https://www.sawe.org/product/paper-3732},
year = {2020},
date = {2020-07-01},
urldate = {2020-07-01},
booktitle = {2020 SAWE Tech Fair},
pages = {12},
publisher = {Society of Allied Weight Engineers, Inc.},
address = {Virtual Conference},
abstract = {An accurate mass estimation is key to better evaluate aircraft concepts during conceptual and preliminary design. The influence of composite materials on the structural mass estimation of large commercial aircraft has been reviewed on several studies. For light aircraft however, few methods besides applying a fudge factor to scale down masses of an equivalent metallic wing are available. On aircraft concepts deviating from a classical con- figuration statistical methods can not be reliably used for the mass estimation. Therefore Class II & 1/2 and Class III methods, which account for the loading of the structure, are expected to provide a better estimation.In this paper we develop a Class II & 1/2 method to estimate structural masses of composite light aircraft wings. For this, the primary structure of several wings is dimensioned according to static strength criteria. The structure is modeled using a stick beam model. Static aerodynamic loads are calculated using a vortex lattice method. The masses of the dimensioned structures are then compared to the published masses of the considered wings. The comparison is used to calibrate the estimation method and account for sec- ondary structures and miscellaneous items. At last, the deviations between the real masses and the estimated ones using different methods are compared to evaluate the suitability of the developed method.},
keywords = {11. Weight Engineering - Aircraft Estimation, 23. Weight Engineering - Structural Estimation},
pubstate = {published},
tppubtype = {inproceedings}
}
@inproceedings{3735,
title = {3735. Weight and Balance Challenges for Hybrid Electric Propulsion System},
author = {Vera Paula and Dr. Florian Vogel},
url = {https://www.sawe.org/product/paper-3735},
year = {2020},
date = {2020-07-01},
urldate = {2020-07-01},
booktitle = {2020 SAWE Tech Fair},
pages = {16},
publisher = {Society of Allied Weight Engineers, Inc.},
address = {Virtual Conference},
abstract = {In the last years electric propulsion systems became increasingly interesting and thanks to many of the technological breakthroughs from automotive companies this technological change is now entering the aviation industry and raises questions about the feasibility, advantages and challenges of the new technologies. In this context, the HEPS weight receives a special attention. The HEPS takes advantage of both electric motor and internal combustion engine and enables the system to be switched on the electrical component of the propulsion for specific flight phases (takeoff and landing).This proposed system has not only the benefit in fuel saving but also a reduction in takeoff noise, emission levels and cost. It also enables to open spaces and can contribute for safety increase, depending on application. This potential benefits are explored by manufacturers for future aircrafts, helicopters, drones and Urban Air Mobility vehicles.In that way, the main objective of this paper is to discuss and analyze HEPS architectures, considering the electric propulsion unit (e-motor and inverter), electric transmission (electrical protections and harness), electric energy source (battery/ fuel cell system and genset power generation) and thermal management (cooling system) from a weight and balance perspective. The aim is basically to answer the questions: which are the main relevant subsystems and components contributing for the weight of the HEPS and which are the challenges associated to it? In order to reach this goal a synthesis of bibliographic review is presented and a description research is proposed for a system with an aircraft application. The outcome of this work is a weight and balance perspective assessment of HEPS subsystem, which contributes to the understanding of this new technology and learning objectives for future aircraft design.},
keywords = {11. Weight Engineering - Aircraft Estimation, 34. Advanced Design},
pubstate = {published},
tppubtype = {inproceedings}
}
@inproceedings{3736,
title = {3736. Hydrogen Fuel Cell Power System Weight Challenges in VTOL Aircraft},
author = {Greg Ray and Joseph D. Rainville},
url = {https://www.sawe.org/product/paper-3736},
year = {2020},
date = {2020-07-01},
booktitle = {2020 SAWE Tech Fair},
pages = {16},
publisher = {Society of Allied Weight Engineers, Inc.},
address = {Virtual Conference},
abstract = {The 'More Electric Aircraft' movement is maturing past actuation, flight controls and backup power solutions. Starting with Unmanned Aerial Vehicles (UAV) and now growing into the passenger vehicle market, vertical lift aircraft engineers are developing electric driven propulsion systems.One of major limitations with electrification is endurance or range. Batteries only offer so much energy capacity before mass becomes a limiting factor. Hydrogen fuel cells offer another solution for on board electrical generation but present many of their own technical challenges.In cases of typical passenger vertical lift aircraft, electrification supplants traditional gas turbines and liquid fuel tanks with electric motors, power electronics, and either batteries or hydrogen fuel cells for an energy source. For Class I UAVs (55 lbs. total weight) or Class II UAVs (up to 300 lbs. total weight), batteries could be replaced by smaller, simplified fuel cells, electronics and hydrogen storage.The electric powertrain evolution will have a strong impact on several aspects of aircraft technology development, especially mass properties and center of gravity as the emerging technology is not limited to time honored positions and locations of legacy components. This paper researches some of the risks and opportunities with electrifying the propulsion systems of vertical lift aircraft.},
keywords = {11. Weight Engineering - Aircraft Estimation, 34. Advanced Design},
pubstate = {published},
tppubtype = {inproceedings}
}
2019
@inproceedings{3729,
title = {3729. Application of SAWE Course 'Developing Basic Parametric Methods' to Nacelle Weight Estimating},
author = {Doug Fisher},
url = {https://www.sawe.org/product/paper-3729},
year = {2019},
date = {2019-05-01},
booktitle = {78th Annual Conference, Norfolk, VA},
pages = {17},
publisher = {Society of Allied Weight Engineers, Inc.},
address = {Norfolk, Virginia},
abstract = {This paper details how the learning contained in SAWE course 'Developing Basic Parametric Methods' was applied at Collins Aerospace for estimating nacelle weights of new commercial and business jet aircraft. Collins has decades of experience developing nacelles and a large database of historical weight data, but has not effectively leveraged that data into better weight estimating tools. Learning from this course was applied to develop improved methods of estimating the weight of nacelles for new product proposals. This has allowed us to not only provide better weight estimates but also better understand the limits of our data and estimating methods.},
keywords = {10. Weight Engineering - Aircraft Design, 11. Weight Engineering - Aircraft Estimation, 21. Weight Engineering - Statistical Studies},
pubstate = {published},
tppubtype = {inproceedings}
}
2017
@inproceedings{3685,
title = {3685. Design of an internal aerodynamic load cell for static for oscillating airfoils},
author = {Kamal Ben Miloud and Hachimi Fellouah},
url = {https://www.sawe.org/product/paper-3685},
year = {2017},
date = {2017-05-01},
booktitle = {76th Annual Conference, Montreal, Canada},
pages = {7},
publisher = {Society of Allied Weight Engineers, Inc.},
address = {Montreal, Canada},
abstract = {This project concerns the design of a three components internal aerodynamic load cell. This load cell will be used to measure the lift, drag and pitching moment in static or oscillating airfoils enduring air loads. The end objective is to study the complex unsteady 3 dimensional (3D) air flows interaction with airfoils. This interaction is often characterized by flow recirculation and massive flow separations that lead to reduction of both aerodynamic performance and structure fatigue.The Computer-aided design (CAD) of the internal load cell will be presented. Finite element analysis (FEA), through ANSYS software, is used to assess the design before its construction. The result shows the good response of the balance to simulated air loads.},
keywords = {11. Weight Engineering - Aircraft Estimation, Student Papers},
pubstate = {published},
tppubtype = {inproceedings}
}
@inproceedings{3691,
title = {3691. Methods to Evaluate the Mass Properties of a Scale Model Aircraft},
author = {Eetu Kohtanen and R. Benjamin Davis},
url = {https://www.sawe.org/product/paper-3691},
year = {2017},
date = {2017-05-01},
booktitle = {76th Annual Conference, Montreal, Canada},
pages = {12},
publisher = {Society of Allied Weight Engineers, Inc.},
address = {Montreal, Canada},
abstract = {Scale model ditching tests are sometimes conducted to study the loads and dynamic behavior associated with an aircraft during water impact. To ensure scalability of the results, the model's mass properties including weight, center of gravity, and pitch moment of inertia in particular must proportionally reflect the characteristics of the full-scale aircraft. This paper presents the experimental methods used to evaluate these mass characteristics for a 1/20th scale Gulfstream G550 model prior to ditching tests conducted at the University of Georgia. These methods can be used for any similarly sized model.To determine the center of gravity the aircraft model is placed on a v-block assembly resting on three force transducers arranged in an isosceles triangle formation. The model's center of gravity along longitudinal and lateral axes is found by summing moments about a known reference axes system using the static forces measured at each transducer. To find the vertical center of gravity, the model is rotated about its longitudinal axis in a v-block fixture, and the force readings along the projection of the rotated plane are then manipulated.For pitch inertia, a compound pendulum is used to measure the aircraft's period of oscillation which is related to the inertia about the axis of oscillation through an analytical method [1]. The inertia of the pendulum apparatus by itself is then subtracted from the total experimental inertia, and the parallel axis theorem is used to determine the model's pitch inertia about its center of gravity. To evaluate the accuracy of the pendulum method, aluminum and steel brackets with known mass properties are attached to the model's tail, and the pitch inertia is measured again for each bracket. The increase in inertia is then compared against the theoretical increase.},
keywords = {06. Inertia Measurements, 08. Weighing, 11. Weight Engineering - Aircraft Estimation, Student Papers},
pubstate = {published},
tppubtype = {inproceedings}
}
@inproceedings{3692,
title = {3692. Aircraft Systems Physics-Based Weight Estimation Methods for Conceptual Design},
author = {Ali Tfaily and Dr. Susan Liscouët-Hanke},
url = {https://www.sawe.org/product/paper-3692},
year = {2017},
date = {2017-05-01},
booktitle = {76th Annual Conference, Montreal, Canada},
pages = {12},
publisher = {Society of Allied Weight Engineers, Inc.},
address = {Montreal, Canada},
abstract = {During the conceptual design phase of an aircraft, details regarding aircraft systems such as the detailed architecture and parts lists are not available. However, weight estimates for aircraft systems are needed very early for aircraft design and performance calculation. Several methods exist to predict system weights and most of these methods are empirical models correlated to top level aircraft parameters such as take- off weight, wingspan, etc. Even if the empirical methods have been sufficiently accurate in the past, they are not suitable for a more sophisticated multidisciplinary design optimization (MDO) approach implemented today in Bombardier's Advanced Design group. In addition, the empirical methods are not valid to predict the effect of new technologies. So called 'physics-based methods' are proposed, leading to a better understanding of technology and system architecture choice impact on the aircraft weight.The new weight estimation methods are implemented as integral part of a conceptual aircraft systems sizing framework. This framework enables the development of more mature aircraft concepts without comprising the calculation runtime. The proposed physics based models showed minimal errors when compared to actual data while capturing additional sensitivities that did not exist in previous methodologies. This paper illustrates the methodology for the example of the hydraulic power system.},
keywords = {11. Weight Engineering - Aircraft Estimation, 25. Weight Engineering - System Estimation, 34. Advanced Design},
pubstate = {published},
tppubtype = {inproceedings}
}
2016
@inproceedings{3660,
title = {3660. Development of a Conceptual Flight Vehicle Design Weight Estimation Method Library},
author = {Andy Walker},
url = {https://www.sawe.org/product/paper-3660},
year = {2016},
date = {2016-05-01},
booktitle = {75th Annual Conference, Denver, Colorado},
pages = {171},
publisher = {Society of Allied Weight Engineers, Inc.},
address = {Denver, Colorado},
abstract = {The state of the art in estimating the volumetric size and mass of flight vehicles is held today by an elite group of engineers in the Aerospace Conceptual Design Industry. This is not a skill readily accessible or taught in academia. To estimate flight vehicle mass properties, many aerospace engineering students are encouraged to read the latest design textbooks, learn how to use a few basic statistical equations, and plunge into the details of parametric mass properties analysis. Specifications for and a prototype of a standardized engineering 'tool-box' of conceptual and preliminary design weight estimation methods were developed to manage the growing and ever-changing body of weight estimation knowledge. This also bridges the gap in Mass Properties education for aerospace engineering students. The Weight Method Library will also be used as a living document for use by future aerospace students. This 'tool-box' consists of a weight estimation method bibliography containing unclassified, open -source literature for conceptual and preliminary flight vehicle design phases. Transport aircraft validation cases have been applied to each entry in the AVD Weight Method Library in order to provide a sense of context and applicability to each method. The weight methodology validation results indicate consensus and agreement of the individual methods. This generic specification of a method library will be applicable for use by other disciplines within the AVD Lab, Post- Graduate design labs, or engineering design professionals.},
note = {Mike HackneyBest Paper Award - 2016},
keywords = {10. Weight Engineering - Aircraft Design, 11. Weight Engineering - Aircraft Estimation, Mike Hackney Best Paper Award},
pubstate = {published},
tppubtype = {inproceedings}
}
2014
@inproceedings{3627,
title = {3627. Multifidelity Overall AC Mass Model: Fit for Purpose Mass Models for Overall Aircraft Design},
author = {A. Rodriguez Reina and S. Lanzàn Ferran},
url = {https://www.sawe.org/product/paper-3627},
year = {2014},
date = {2014-05-01},
booktitle = {73rd Annual Conference, Long Beach California},
pages = {13},
publisher = {Society of Allied Weight Engineers, Inc.},
address = {Long Beach, California},
abstract = {To allow an integrated multidisciplinary aircraft design, consistent models which can be used in all disciplines representing the same physical properties are needed.
This paper studies the possibility to generate an overall Mass Model, which can be used for all applications, adapting its fidelity to each target application. From a simple stick model, up to a fine cloud of points, the aim is to study and define the most appropriate model which adapts itself to the application needed.
The investigation performed is proving that it's possible to generate unique fit for purpose mass models which have multifidelity depending on the needed application, thus maintaining the consistency and traceability to a reference model. This reduces the number of different models to be generated depending on the application, streamlining the process and increasing the overall efficiency.},
keywords = {11. Weight Engineering - Aircraft Estimation},
pubstate = {published},
tppubtype = {inproceedings}
}
This paper studies the possibility to generate an overall Mass Model, which can be used for all applications, adapting its fidelity to each target application. From a simple stick model, up to a fine cloud of points, the aim is to study and define the most appropriate model which adapts itself to the application needed.
The investigation performed is proving that it's possible to generate unique fit for purpose mass models which have multifidelity depending on the needed application, thus maintaining the consistency and traceability to a reference model. This reduces the number of different models to be generated depending on the application, streamlining the process and increasing the overall efficiency.@inproceedings{3629,
title = {3629. The Mysterious Art of Weight Estimation of Large Civil Aircraft},
author = {Judi Cheeseman},
url = {https://www.sawe.org/product/paper-3629},
year = {2014},
date = {2014-05-01},
booktitle = {73rd Annual Conference, Long Beach California},
pages = {10},
publisher = {Society of Allied Weight Engineers, Inc.},
address = {Long Beach, California},
abstract = {The weight estimation of large civil aircraft has been a challenge much explored by aircraft manufacturers and academics. The difficulties to achieve the required accuracy and sensitivities to design changes during the development cycle of an aircraft are well known by those involved in the mass properties discipline.
Weight figures are required from the very early stages of the product definition right the way through to the end of life of an aircraft and each stage of the development process presents a range of problems for the mass properties engineer to solve.
To the uninitiated it may appear to be an impossible task to provide accurate weights when considering the complexity of today's large civil aircraft, how interdependent are the numerous disciplines involved & how much of the aircraft final design is unknown in the early phases where weight estimation plays a critical role in ensuring a successful product for both manufacturer & customer.
This paper explores some of those challenges and describes some solutions employed today in the Aircraft industry in support of the aircraft design and development process.},
keywords = {11. Weight Engineering - Aircraft Estimation},
pubstate = {published},
tppubtype = {inproceedings}
}
Weight figures are required from the very early stages of the product definition right the way through to the end of life of an aircraft and each stage of the development process presents a range of problems for the mass properties engineer to solve.
To the uninitiated it may appear to be an impossible task to provide accurate weights when considering the complexity of today's large civil aircraft, how interdependent are the numerous disciplines involved & how much of the aircraft final design is unknown in the early phases where weight estimation plays a critical role in ensuring a successful product for both manufacturer & customer.
This paper explores some of those challenges and describes some solutions employed today in the Aircraft industry in support of the aircraft design and development process.2013
@inproceedings{3597,
title = {3597. Aircraft Weight Estimation In Interactive Design Process},
author = {Omran Al-Shamma and Dr. Rashid Ali},
url = {https://www.sawe.org/product/paper-3597},
year = {2013},
date = {2013-05-01},
booktitle = {72nd Annual Conference, St. Louis, Missouri},
pages = {11},
publisher = {Society of Allied Weight Engineers, Inc.},
address = {Saint Louis, Missouri},
abstract = {Amongst all the design variables employed in aircraft design process, weight is the most significant one. Aircraft performance is dependent on a suitable weight in order for it to carry out its intended mission. In the interactive design process, the weight design engineers usually follow one particular published methodology such as that proposed by Roskam or Torenbeek or etc.
The main drawback of these methodologies is their limited accuracy, especially when applied to the vast variation of civilian aircraft. Furthermore, the non-availability of component- weight data, which may be used in evaluating maximum take-off weight, makes the design process difficult.
A new weight estimation method has been developed and has been applied to interactive design process. In this method many equations of different methodologies are applied to each aircraft component instead of applying one analyst's methodology. Simultaneously, any formula that has secondary variables, which may not be available in the early stages of aircraft design, is rejected. The equation that gives the lowest average value is selected. The results from the new method shows that the accuracy of the estimated operating empty weight and the maximum take-off weight is better than 5% can be obtained.},
keywords = {11. Weight Engineering - Aircraft Estimation},
pubstate = {published},
tppubtype = {inproceedings}
}
The main drawback of these methodologies is their limited accuracy, especially when applied to the vast variation of civilian aircraft. Furthermore, the non-availability of component- weight data, which may be used in evaluating maximum take-off weight, makes the design process difficult.
A new weight estimation method has been developed and has been applied to interactive design process. In this method many equations of different methodologies are applied to each aircraft component instead of applying one analyst's methodology. Simultaneously, any formula that has secondary variables, which may not be available in the early stages of aircraft design, is rejected. The equation that gives the lowest average value is selected. The results from the new method shows that the accuracy of the estimated operating empty weight and the maximum take-off weight is better than 5% can be obtained.@inproceedings{3598,
title = {3598. Improving Structural Weight Estimation of Novel Aircraft Configurations to Enhance Flying Quality Analysis},
author = {Seyyedeh Maryam Moghadasi and Ali Elham and Mark Voskuijl},
url = {https://www.sawe.org/product/paper-3598},
year = {2013},
date = {2013-05-01},
booktitle = {72nd Annual Conference, St. Louis, Missouri},
pages = {18},
publisher = {Society of Allied Weight Engineers, Inc.},
address = {Saint Louis, Missouri},
abstract = {Structural weight estimation of novel aircraft configurations, such as a box-wing aircraft, in the conceptual and preliminary design phase is a challenge due to a lack of statistical data. Most of the aircraft performance and handling qualities parameters are strongly influenced by the aircraft weight and inertia. Therefore an accurate weight estimation method is required. The application of existing (statistical) weight estimation methods provides a rather inaccurate and weak estimation for this novel configuration. An alternative is the use of higher fidelity weight estimation methods, which use more physics based calculations and less statistical estimations.
A novel design framework with various disciplines is developed. In this framework, a parametric aircraft model, a weight estimation method, aerodynamic analysis and flight mechanics analysis are coupled to perform a fully automated design process. The various modules of this design framework create a decision making system so that the aerodynamic and weight estimations for handling quality measurements can take place with high fidelity for different aircraft category during the preliminary and conceptual design process.
It is demonstrated that the design parameters of the PrP300 are closely coupled and a delicate balance has to be found between the design parameters in order to have adequate handling qualities throughout the flight envelope. Such a trade- off is most likely very difficult, if not impossible to conduct by hand.
The proposed framework is therefore a powerful tool to support the aircraft design activities and to investigate the handling qualities of an (unconventional) aircraft already in the early design stages. This can lead to a less error design and consequently decrease the cost due to additional design work and extra wind tunnel and flight testing.},
keywords = {11. Weight Engineering - Aircraft Estimation},
pubstate = {published},
tppubtype = {inproceedings}
}
A novel design framework with various disciplines is developed. In this framework, a parametric aircraft model, a weight estimation method, aerodynamic analysis and flight mechanics analysis are coupled to perform a fully automated design process. The various modules of this design framework create a decision making system so that the aerodynamic and weight estimations for handling quality measurements can take place with high fidelity for different aircraft category during the preliminary and conceptual design process.
It is demonstrated that the design parameters of the PrP300 are closely coupled and a delicate balance has to be found between the design parameters in order to have adequate handling qualities throughout the flight envelope. Such a trade- off is most likely very difficult, if not impossible to conduct by hand.
The proposed framework is therefore a powerful tool to support the aircraft design activities and to investigate the handling qualities of an (unconventional) aircraft already in the early design stages. This can lead to a less error design and consequently decrease the cost due to additional design work and extra wind tunnel and flight testing.2012
@inproceedings{3555,
title = {3555. A Fast Method For Estimating Airloads On Parts Of Aircraft At Arbitrary Flight Conditions To Support Early Mass Estimations},
author = {Albrecht Eberle},
url = {https://www.sawe.org/product/paper-3555},
year = {2012},
date = {2012-05-01},
booktitle = {71st Annual Conference, Bad Gögging, Germany},
pages = {17},
publisher = {Society of Allied Weight Engineers, Inc.},
address = {Bad Gögging, Germany},
abstract = {This paper presents a new CFD (Computational Fluid Dynamics) approach for nodal force evaluations at flight Mach numbers from low subsonic up to hypersonics. Airloads are an important input variable for flight mechanics which take into account the mass properties of aircraft. The simplest example is the aerodynamic vertical force necessary for lifting an aircraft at desired speed. With CFD, neutral point positions may be obtained for the Mach number range of the aircraft (three-axis static stability assessment). Mass properties do enter in unsteady phenomenons such as flutter, aero-structure-mass dynamics etc. Recent CFD developments aim at the analysis of flow details to perfection and thus require significant computer resources. In contrast to this approach the present work provides airload predictions by using fast computational methods with acceptable accuracy at less cost. The method is based on an integrated unstructured mesh generator equipped with an Euler- or optionally a Navier-Stokes solver. The mesh contains only bricks. It is body aligned with sublayers attached to the body surface for enhanced accuracy. The aircraft skin is user defined by scattered point coordinates. A newly developed 3D multilinear level set function is iteratively generated on a 3D cartesian mesh. This function produces cartesian cells having positive baricentric function values outside of the aircraft and negative values inside. In this way the discretized surface consists of quadrilaterals serving as boundary for the field mesh generator. An algorithm similar to the plate equation makes the aircraft surface smoothly pass through the input points. The solution of the Euler/Navier-Stokes equations is accelerated by a defect correction scheme invented by the author. Elementary numerical geometry is applied for distributing the forces on user defined structural nodes. Non-overlapping frames allow for partial conservative integration of the pressure distribution. The present CFD is suited for laptop usage.},
keywords = {11. Weight Engineering - Aircraft Estimation},
pubstate = {published},
tppubtype = {inproceedings}
}
@inproceedings{3559,
title = {3559. Fuel Mass Properties Calculation with CATIA V5},
author = {Ralf Funk},
url = {https://www.sawe.org/product/paper-3559},
year = {2012},
date = {2012-05-01},
booktitle = {71st Annual Conference, Bad Gögging, Germany},
pages = {21},
publisher = {Society of Allied Weight Engineers, Inc.},
address = {Bad Gögging, Germany},
abstract = {Complex aircraft tank geometries due to challenging requirements are designed nowadays using CAD allowing analysis in a concise and cheap way. For fuel mass properties calculation inside CATIA V5 a corresponding feature has to be provided via fuel macro.
This programme can be used in the various design and development phases of an aircraft. Hence this tool is qualified for analysis of simple cuboids in the Pre-Draft as well as positioned and optimised tank geometries with integrated pumps or pipes in the Pre-Design-Phase, Product-Design-Phase or In-Service-Phase.
Fuel mass properties are essential for aircraft moments of inertia (MOI) determination, flight performance (Flight Control System) and mission performance evaluation.
Processing with CATIA V5 is possible for CAD-solids, which are designed in the CATIA V4/ V5 environment or having a compatible file format. Before starting the analysis it is necessary to install the basic settings and to prepare the files with a powercopy providing the CAD-model with various parameters and geometry, thus the user of this programme requires a basic knowledge of CATIA V5.
This paper gives an overview to run the fuel macro for individual tanks or tank groups for various configured fuel rundown sequences. The simplification of internal tank geometry is compensated by a feature of the tool which provides fuel density variation. Further input parameters are the flight attitude with individual air space and unusable fuel.
The Log-File contains apart from fuel mass properties of tank geometries the input parameters and more detailed information for interpretation of results.},
keywords = {11. Weight Engineering - Aircraft Estimation, 12. Weight Engineering - Computer Applications},
pubstate = {published},
tppubtype = {inproceedings}
}
This programme can be used in the various design and development phases of an aircraft. Hence this tool is qualified for analysis of simple cuboids in the Pre-Draft as well as positioned and optimised tank geometries with integrated pumps or pipes in the Pre-Design-Phase, Product-Design-Phase or In-Service-Phase.
Fuel mass properties are essential for aircraft moments of inertia (MOI) determination, flight performance (Flight Control System) and mission performance evaluation.
Processing with CATIA V5 is possible for CAD-solids, which are designed in the CATIA V4/ V5 environment or having a compatible file format. Before starting the analysis it is necessary to install the basic settings and to prepare the files with a powercopy providing the CAD-model with various parameters and geometry, thus the user of this programme requires a basic knowledge of CATIA V5.
This paper gives an overview to run the fuel macro for individual tanks or tank groups for various configured fuel rundown sequences. The simplification of internal tank geometry is compensated by a feature of the tool which provides fuel density variation. Further input parameters are the flight attitude with individual air space and unusable fuel.
The Log-File contains apart from fuel mass properties of tank geometries the input parameters and more detailed information for interpretation of results.@inproceedings{3564,
title = {3564. Multi-Fidelity Wing Mass Estimations Based On A Central Model Approach},
author = {Daniel Böhnke and Felix Dorbath and Björn Nagel and Volker Gollnick},
url = {https://www.sawe.org/product/paper-3564},
year = {2012},
date = {2012-05-01},
booktitle = {71st Annual Conference, Bad Gögging, Germany},
pages = {18},
publisher = {Society of Allied Weight Engineers, Inc.},
address = {Bad Gögging, Germany},
abstract = {Although computational power is constantly increasing and Moore's Law is still not falsified, computational cost remains an essential barrier in aircraft design especially when a high number of design evaluations is necessary. This is especially true at the conceptual design stage of aircraft. While determining the characteristics of a new configuration the number of iterations and the low level of detail in the available data limit the analyses to simple empiric methods.
Nevertheless, at a later point in the design it is necessary to determine parameters like the wing mass with higher-fidelity analysis modules. Especially when assessing configurations that lie outside of the well-known design space of conceptual design, empiric methods become unreliable. Examples to name include high aspect ratio and forward-swept wings.
In this study a combination of an empiric method, a beam model and vortex lattice model for aerodynamic loads is introduced. While multi-fidelity approaches are already well known, this study focuses on the fact that all analysis modules derive their data from the same data model. Working on a central data model decreases the number of required interfaces and guarantees that all models relate to the same input data, i.e. a compliant geometry definition.
This paper includes a design chain starting from the conceptual design tool VAMPzero as initiator for the more advanced models PESTwing and TRIMvl. Using the PESTwing tool a large design space will be explored. An equation for determination of the wing mass based on a physical model is then derived and compared to existing methods in conceptual design.},
keywords = {11. Weight Engineering - Aircraft Estimation, 23. Weight Engineering - Structural Estimation},
pubstate = {published},
tppubtype = {inproceedings}
}
Nevertheless, at a later point in the design it is necessary to determine parameters like the wing mass with higher-fidelity analysis modules. Especially when assessing configurations that lie outside of the well-known design space of conceptual design, empiric methods become unreliable. Examples to name include high aspect ratio and forward-swept wings.
In this study a combination of an empiric method, a beam model and vortex lattice model for aerodynamic loads is introduced. While multi-fidelity approaches are already well known, this study focuses on the fact that all analysis modules derive their data from the same data model. Working on a central data model decreases the number of required interfaces and guarantees that all models relate to the same input data, i.e. a compliant geometry definition.
This paper includes a design chain starting from the conceptual design tool VAMPzero as initiator for the more advanced models PESTwing and TRIMvl. Using the PESTwing tool a large design space will be explored. An equation for determination of the wing mass based on a physical model is then derived and compared to existing methods in conceptual design.@inproceedings{3566,
title = {3566. Multidisciplinary Analysis and Optimization in the Conceptual Aircraft Design Phase to Support Early Mass Predictions},
author = {Johannes Schweiger and Moritz Büsing and Jens Feger},
url = {https://www.sawe.org/product/paper-3566},
year = {2012},
date = {2012-05-01},
booktitle = {71st Annual Conference, Bad Gögging, Germany},
pages = {19},
publisher = {Society of Allied Weight Engineers, Inc.},
address = {Bad Gögging, Germany},
abstract = {A new approach in conceptual aircraft design at Cassidian is presented which supports the initial assessment of mass data for a new configuration. It is based on the fast creation of a multidisciplinary analytical model for the description of the complete vehicle and the application of mathematical optimization methods to determine the mass of its structural components, sub- ject to external loading conditions and requirements for the structural stiffness to meet the es- sential performance constraints.
In the first place, this process serves as a tool that helps to find the optimum overall design for the top level requirements like range and payload by a direct coupling of the structural lay out with the vehicle's conceptual design topology and sizing process.
Mass data from this process help to confirm and adjust the classic mass estimation process which is based on statistic and semi-empirical data for the individual components of the vehicle but also for the global mass properties like center of gravity location and mass moments of in- ertia, which are also important during the initial sizing process.
In addition, the method help to find optimum solutions for the integration of heavy equipment by directly including the impacts from the attachment loads of these equipment items to the structure, as well as the related interactions with the vehicle's flutter stability.
The basic analysis and optimization tool for this process is the Cassidian in-house program LAGRANGE. Its development started 30 years ago, based on the needs to assess and include all relevant design requirements for the stiffness and strength of an aircraft structure into the design process from the very beginning, and at the same time explore and exploit the new pos- sibilities of 'tailoring' the strength and stiffness properties of carbon composites.
Whereas initial structural analysis and optimization application started by setting up rather sim- ple structural analysis models from 'scratch', recent years showed a trend towards first creat- ing computer aided design models and then derive the analysis models from these already rather complex designs. The approach which is described in this paper is different from similar efforts because it starts with the creation of the analytical models by simple input data only. Its results can then be used to create or update the design model. The time to set up the complete model for a new configuration is less than one day, and it takes only minutes or few hours to modify the model for a different geometry, different requirements, or different options for the optimization process.
Especially for new configurations, where no or only very limited statistical data exist from com- parable projects, this new approach is very useful to support the generation and tracking of mass data, and it helps to minimize these masses by using analytical sensitivities for the es- sential design variables as functions from a set of complex design requirements from different disciplines.
An example is presented for a generic medium-altitude-long endurance (MALE) UAV.},
keywords = {11. Weight Engineering - Aircraft Estimation},
pubstate = {published},
tppubtype = {inproceedings}
}
In the first place, this process serves as a tool that helps to find the optimum overall design for the top level requirements like range and payload by a direct coupling of the structural lay out with the vehicle's conceptual design topology and sizing process.
Mass data from this process help to confirm and adjust the classic mass estimation process which is based on statistic and semi-empirical data for the individual components of the vehicle but also for the global mass properties like center of gravity location and mass moments of in- ertia, which are also important during the initial sizing process.
In addition, the method help to find optimum solutions for the integration of heavy equipment by directly including the impacts from the attachment loads of these equipment items to the structure, as well as the related interactions with the vehicle's flutter stability.
The basic analysis and optimization tool for this process is the Cassidian in-house program LAGRANGE. Its development started 30 years ago, based on the needs to assess and include all relevant design requirements for the stiffness and strength of an aircraft structure into the design process from the very beginning, and at the same time explore and exploit the new pos- sibilities of 'tailoring' the strength and stiffness properties of carbon composites.
Whereas initial structural analysis and optimization application started by setting up rather sim- ple structural analysis models from 'scratch', recent years showed a trend towards first creat- ing computer aided design models and then derive the analysis models from these already rather complex designs. The approach which is described in this paper is different from similar efforts because it starts with the creation of the analytical models by simple input data only. Its results can then be used to create or update the design model. The time to set up the complete model for a new configuration is less than one day, and it takes only minutes or few hours to modify the model for a different geometry, different requirements, or different options for the optimization process.
Especially for new configurations, where no or only very limited statistical data exist from com- parable projects, this new approach is very useful to support the generation and tracking of mass data, and it helps to minimize these masses by using analytical sensitivities for the es- sential design variables as functions from a set of complex design requirements from different disciplines.
An example is presented for a generic medium-altitude-long endurance (MALE) UAV.