SAWE Technical Papers
Technical Library
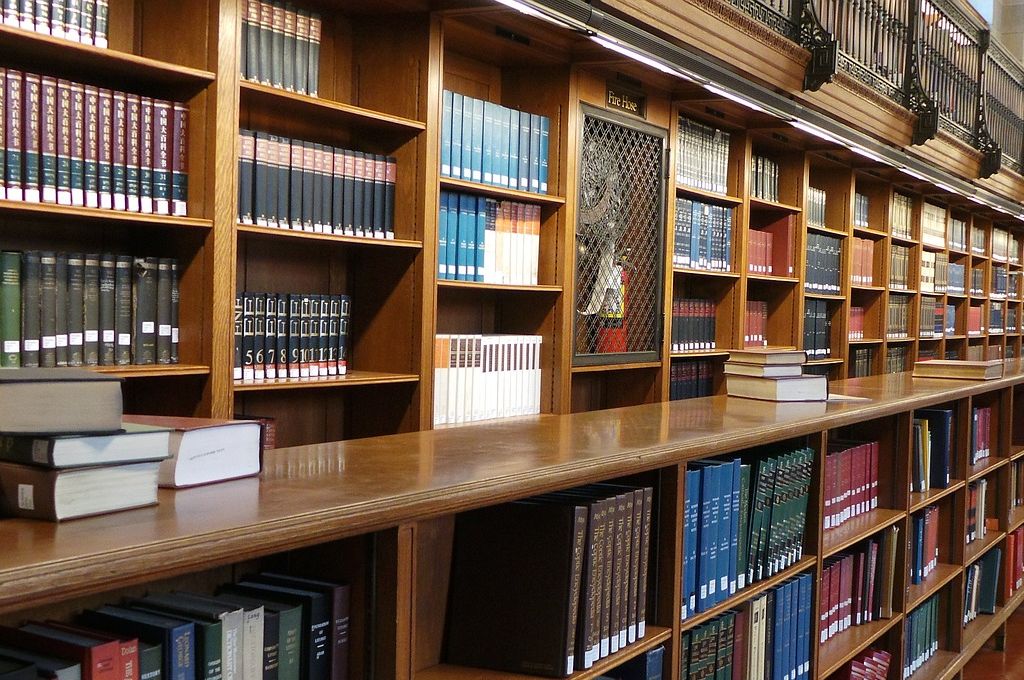
SAWE Paper Database
The SAWE Technical Library contains nearly 4000 technical papers available here for purchase and download. Use the search options below to find what you need.
3763. MauSPAF: Design of an Open-Source Mass Properties Management Framework Nuño, M.; Schröder, K. In: 81st Annual Conference, Savannah, Georgia, pp. 18, Society of Allied Weight Engineers, Inc., Savannah, Georgia, 2022. Abstract | Buy/Download | BibTeX | Tags: 12. Weight Engineering - Computer Applications, Student Papers 3762. Artificial Intelligence Techniques for Ship Weight Estimation and Calculation Malla, Upendra In: 2021 SAWE Tech Fair, pp. 9, Society of Allied Weight Engineers, Inc., Virtual Conference, 2021. Abstract | Buy/Download | BibTeX | Tags: 12. Weight Engineering - Computer Applications 3726. Toolchain Integration For Space Habitat Design DeVoe, Maxwell; Tokarz, Ariel; Park, Samuel In: 78th Annual Conference, Norfolk, VA, pp. 11, Society of Allied Weight Engineers, Inc., Norfolk, Virginia, 2019. Abstract | Buy/Download | BibTeX | Tags: 12. Weight Engineering - Computer Applications, 34. Advanced Design 3694. Using Knowledge Analytics to Search and Characterize Mass Properties Aerospace Data Cerro, Jeffrey; Sidehamer, Theodore; Notarnicola, Dorthy In: 77th Annual Conference, Irving, Texas, pp. 25, Society of Allied Weight Engineers, Inc., Irving, Texas, 2018. Abstract | Buy/Download | BibTeX | Tags: 12. Weight Engineering - Computer Applications 3671. Model Based Mass Properties Engineering at JPL IV, Morgan Hendry; Gross, Johannes In: 75th Annual Conference, Denver, Colorado, pp. 11, Society of Allied Weight Engineers, Inc., Denver, Colorado, 2016. Abstract | Buy/Download | BibTeX | Tags: 12. Weight Engineering - Computer Applications, 24. Weight Engineering - System Design 3630. Design Patterns in Object Oriented Programming Rosal, Sal In: 73rd Annual Conference, Long Beach California, pp. 10, Society of Allied Weight Engineers, Inc., Long Beach, California, 2014. Abstract | Buy/Download | BibTeX | Tags: 12. Weight Engineering - Computer Applications 3595. Calculating Mass Properties from a Triangulated Solid Sinclair, Dr. Paul In: 72nd Annual Conference, St. Louis, Missouri, pp. 10, Society of Allied Weight Engineers, Inc., Saint Louis, Missouri, 2013. Abstract | Buy/Download | BibTeX | Tags: 12. Weight Engineering - Computer Applications 3600. Autonomous Mass Properties Tracking Database Attributes Burt, Edd In: 72nd Annual Conference, St. Louis, Missouri, pp. 30, Society of Allied Weight Engineers, Inc., Saint Louis, Missouri, 2013. Abstract | Buy/Download | BibTeX | Tags: 12. Weight Engineering - Computer Applications 3556. Composite Tank Structure Dynamics Modeling Based On Finite Particles Baeten, André In: 71st Annual Conference, Bad Gögging, Germany, pp. 23, Society of Allied Weight Engineers, Inc., Bad Gögging, Germany, 2012. Abstract | Buy/Download | BibTeX | Tags: 12. Weight Engineering - Computer Applications 3559. Fuel Mass Properties Calculation with CATIA V5 Funk, Ralf In: 71st Annual Conference, Bad Gögging, Germany, pp. 21, Society of Allied Weight Engineers, Inc., Bad Gögging, Germany, 2012. Abstract | Buy/Download | BibTeX | Tags: 11. Weight Engineering - Aircraft Estimation, 12. Weight Engineering - Computer Applications 3560. Dummy Optimization Regarding Mass Properties for Shaker Test and Flight Test Clermont, Jürgen In: 71st Annual Conference, Bad Gögging, Germany, pp. 45, Society of Allied Weight Engineers, Inc., Bad Gögging, Germany, 2012. Abstract | Buy/Download | BibTeX | Tags: 12. Weight Engineering - Computer Applications, 30. Miscellaneous 3574. Updated SumMassProps A Comprehensive Excel-Based Mass Properties Solution Zimmerman, Robert L. In: 71st Annual Conference, Bad Gögging, Germany, pp. 13, Society of Allied Weight Engineers, Inc., Bad Gögging, Germany, 2012. Abstract | Buy/Download | BibTeX | Tags: 12. Weight Engineering - Computer Applications 3576. Automation Methods Of Aircraft Weight Activities Isikdogan, O; Kiper, T; Unay, E; Gurak, D. In: 71st Annual Conference, Bad Gögging, Germany, pp. 12, Society of Allied Weight Engineers, Inc., Bad Gögging, Germany, 2012. Abstract | Buy/Download | BibTeX | Tags: 12. Weight Engineering - Computer Applications 3590. Optimized Mass Matrices Business Process Zawadzki, Radoslaw; Hiersig, Michael In: 71st Annual Conference, Bad Gögging, Germany, pp. 17, Society of Allied Weight Engineers, Inc., Bad Gögging, Germany, 2012. Abstract | Buy/Download | BibTeX | Tags: 12. Weight Engineering - Computer Applications 3530. Confidence Of Mass Properties (COMP) Tool Smith, James In: 70th Annual Conference, Houstion, Texas, pp. 14, Society of Allied Weight Engineers, Inc., Houston, Texas, 2011. Abstract | Buy/Download | BibTeX | Tags: 07. Section Properties, 12. Weight Engineering - Computer Applications 3531. Weight Data Management for Completion of Corporate Jets Mitry, Ragaa In: 70th Annual Conference, Houstion, Texas, pp. 18, Society of Allied Weight Engineers, Inc., Houston, Texas, 2011. Abstract | Buy/Download | BibTeX | Tags: 11. Weight Engineering - Aircraft Estimation, 12. Weight Engineering - Computer Applications 3534. Mass Properties Requirements For Marine Design Software Titcomb, Alan; Carter, Keith; Moore, Ronnie In: 70th Annual Conference, Houstion, Texas, pp. 18, Society of Allied Weight Engineers, Inc., Houston, Texas, 2011. Abstract | Buy/Download | BibTeX | Tags: 12. Weight Engineering - Computer Applications, Marine 3495. Using PHP/MySQL to Manage Potential Mass Impacts Hager, I. Benjamin In: 69th Annual Conference, Virginia Beach, Virginia, pp. 20, Society of Allied Weight Engineers, Inc., Virginia Beach, Virginia, 2010. Abstract | Buy/Download | BibTeX | Tags: 12. Weight Engineering - Computer Applications, 26. Weight Growth 3498. Introduction of Mass Management Software - Our experiences Rosenberger, Claudia In: 69th Annual Conference, Virginia Beach, Virginia, pp. 16, Society of Allied Weight Engineers, Inc., Virginia Beach, Virginia, 2010. Abstract | Buy/Download | BibTeX | Tags: 12. Weight Engineering - Computer Applications 3475. Mass Distribution, Weight, and Center of Gravity application using CATIA V5 Edmounson, Scott; Papanastasiou, Angelo In: 68th Annual Conference, Wichita, Kansas, pp. 9, Wichita, Kansas, 2009. Abstract | Buy/Download | BibTeX | Tags: 07. Section Properties, 12. Weight Engineering - Computer Applications2022
@inproceedings{3763,
title = {3763. MauSPAF: Design of an Open-Source Mass Properties Management Framework},
author = {M. Nuño and K. Schröder},
url = {https://www.sawe.org/product/paper-3763},
year = {2022},
date = {2022-05-21},
urldate = {2022-05-21},
booktitle = {81st Annual Conference, Savannah, Georgia},
pages = {18},
publisher = {Society of Allied Weight Engineers, Inc.},
address = {Savannah, Georgia},
abstract = {In this paper, an open-source mass properties calculation and management created using Python 3 is presented. The program implements uncertainty calculations using Monte Carlo simulations, mass properties calculations and basic tree structures. It also includes a library with aircraft mass estimation and calculation functions for simple geometrical shapes. To argument the design decisions, a thorough review of available literature about mass calculation tools is performed.},
keywords = {12. Weight Engineering - Computer Applications, Student Papers},
pubstate = {published},
tppubtype = {inproceedings}
}
2021
@inproceedings{3762,
title = {3762. Artificial Intelligence Techniques for Ship Weight Estimation and Calculation},
author = {Upendra Malla},
url = {https://www.sawe.org/product/paper-3762},
year = {2021},
date = {2021-11-01},
urldate = {2021-11-01},
booktitle = {2021 SAWE Tech Fair},
pages = {9},
publisher = {Society of Allied Weight Engineers, Inc.},
address = {Virtual Conference},
abstract = {The advancement of computing and data analysis tools gave rise to the development of Artificial Intelligence (AI) tools. The ship weight estimation and calculation are a simple and tedious process which requires a qualitative weight budgets and quantitative calculations. The evolution of ship weight estimation and calculation using Artificial Intelligence techniques is discussed in the paper and compared with the existing techniques used in the shipping industry. Currently there are several in-house tools and software’s which are utilized by design firms and shipyards for the mass properties estimation / calculation, but these tools are not built with any intelligence to make the weight estimate accurate and effective. The implementation of Artificial Intelligence algorithms for the ship weight estimation by considering the constraints like class rules, standards, guidelines etc.
In this paper at the end, it shows the cost and time savings involved by the implementation of Artificial Intelligence techniques in the ship weight estimate program by means of an example AI tool.},
keywords = {12. Weight Engineering - Computer Applications},
pubstate = {published},
tppubtype = {inproceedings}
}
In this paper at the end, it shows the cost and time savings involved by the implementation of Artificial Intelligence techniques in the ship weight estimate program by means of an example AI tool.2019
@inproceedings{3726,
title = {3726. Toolchain Integration For Space Habitat Design},
author = {Maxwell DeVoe and Ariel Tokarz and Samuel Park},
url = {https://www.sawe.org/product/paper-3726},
year = {2019},
date = {2019-05-01},
booktitle = {78th Annual Conference, Norfolk, VA},
pages = {11},
publisher = {Society of Allied Weight Engineers, Inc.},
address = {Norfolk, Virginia},
abstract = {Space habitat design is an iterative process that requires multiple revisions before a final product can be ascertained. Completing a project can prove cumbersome and time consuming, thus straining an organization's resources. To counteract this issue, there was a desire to automate steps within the design process to improve the efficacy of the iterative aspect while also decreasing time spent developing designs. This paper will detail the main processes that were automated within the NASA LaRC Vehicle Analysis Branch environment. Examine is a custom Microsoft Excel-based spreadsheet that was used to consolidate parameter calculations within an encapsulated environment. IDEA is a model based systems engineering software that enables fast and efficient modifications to a CAD model, allowing for greater flexibility in the design process. To improve efficiency, the two design tools were linked to ensure fast and user-friendly data flow between them. The tools are controlled within a SysML application, consolidating the linkage into one interface for the user. This paper will detail the process of linking the tools together as well as the processes being executed within the individual tools themselves.},
keywords = {12. Weight Engineering - Computer Applications, 34. Advanced Design},
pubstate = {published},
tppubtype = {inproceedings}
}
2018
@inproceedings{3694,
title = {3694. Using Knowledge Analytics to Search and Characterize Mass Properties Aerospace Data},
author = {Jeffrey Cerro and Theodore Sidehamer and Dorthy Notarnicola},
url = {https://www.sawe.org/product/paper-3694},
year = {2018},
date = {2018-05-01},
booktitle = {77th Annual Conference, Irving, Texas},
pages = {25},
publisher = {Society of Allied Weight Engineers, Inc.},
address = {Irving, Texas},
abstract = {There is growing capability in the field of 'Big Data' and 'Data Analytics' which Mass Properties Engineers might like to take advantage of. This paper utilizes an implementation of the IBM Knowledge Analytics and Watson search capabilities to explore a corpus of material developed primarily with the interests of Mass Properties Engineers and vehicle concept developers at its forefront. The full collection of SAWE Technical Papers from 1939 thru 2015 is a major portion of the knowledge content. Additional aerospace vehicle design information includes metadata from AIAA (American Institute for Aeronautics and Astronautics), and INCOSE (International Council on Systems Engineering) as well as author provided personal search material. This data is processed with respect to certain expected content, data taxonomies and key words to become the core data in NASA Langley Research Center's 'Vehicle Analysis Analytics', IBM Watson Content. Processed data becomes the corpus of information which is interrogated to provide examples of finding data for mass regression analysis, technology impacts on MPE, mass properties control, standards, and other aspects of interest.},
keywords = {12. Weight Engineering - Computer Applications},
pubstate = {published},
tppubtype = {inproceedings}
}
2016
@inproceedings{3671,
title = {3671. Model Based Mass Properties Engineering at JPL},
author = {Morgan Hendry IV and Johannes Gross},
url = {https://www.sawe.org/product/paper-3671},
year = {2016},
date = {2016-05-01},
booktitle = {75th Annual Conference, Denver, Colorado},
pages = {11},
publisher = {Society of Allied Weight Engineers, Inc.},
address = {Denver, Colorado},
abstract = {The Soil Moisture Active Passive (SMAP) mission creates global soil moisture measurements every 2-3 days by spinning a lightweight, ~6 meter diameter deployable mesh reflector. This represents the largest spinning antenna ever to be used on a NASA satellite. The paper discusses the mass properties challenges that were overcome in implementing the mission, including the definition of a combined imbalance term called the Effective Product of Inertia, the selection of an optimum Spun Instrument focal length and edge offset that fostered a reduced mass properties sensitivity, the inclusion of late game Spun Instrument configuration flexibility, the use of balance mass locations that leveraged the large moment arm provided by the reflector, and a subassembly measurement campaign that reduced mass properties uncertainties on testable components.},
keywords = {12. Weight Engineering - Computer Applications, 24. Weight Engineering - System Design},
pubstate = {published},
tppubtype = {inproceedings}
}
2014
@inproceedings{3630,
title = {3630. Design Patterns in Object Oriented Programming},
author = {Sal Rosal},
url = {https://www.sawe.org/product/paper-3630},
year = {2014},
date = {2014-05-01},
booktitle = {73rd Annual Conference, Long Beach California},
pages = {10},
publisher = {Society of Allied Weight Engineers, Inc.},
address = {Long Beach, California},
abstract = {Designing and implementing custom software solutions to meet program reporting and calculation requirements is nothing new to Mass Properties Engineering. This paper aims to address basic software development best practices and their application in a Mass Properties Engineering environment. These software concepts in conjunction with an understanding of mass properties engineering provided the basis for the development of the mass properties software program, Mass Properties Data, Configuration Analysis Tool (MADCAT).},
keywords = {12. Weight Engineering - Computer Applications},
pubstate = {published},
tppubtype = {inproceedings}
}
2013
@inproceedings{3595,
title = {3595. Calculating Mass Properties from a Triangulated Solid},
author = {Dr. Paul Sinclair},
url = {https://www.sawe.org/product/paper-3595},
year = {2013},
date = {2013-05-01},
booktitle = {72nd Annual Conference, St. Louis, Missouri},
pages = {10},
publisher = {Society of Allied Weight Engineers, Inc.},
address = {Saint Louis, Missouri},
abstract = {The introduction of solid modelling in Computer—Aided Design (CAD) tools has proven to be a tremendous boon to weight engineering. Analysis of the solid models provides weight, center of gravity, and inertia data with an ease and precision undreamt of by earlier generations. However, CAD packages such as Dassault's Catia and SolidWorks are designed for a wide range of applications. As a result, the models are highly complex and even simple operations require a significant amount of resources. This can make sophisticated weights analyses slow and unwieldly, and occasionally prone to error.
Alternative means of representing solid objects
can address these problems. One of the simplest
representations of a solid is by triangulation: the
surface of the solid is approximated by adjoining
triangles. The representation is not exact, but can
be refined to any desired level of precision. By
Stoke's theorem, any quantity that can be
expressed by an integration of a well—behaved
function over the volume of a solid can also be
expressed by an integration of a related function
over the solid's surface. So, for a given mass
distribution, it is only necessary to know the surface of the solid in order to do mass properties calculations. Representations such as this are the heart of Finite Element Modelling (FEM), and various sophisticated software packages are also available to perform analysis on FE models. However, sometimes a custom application may be preferable. Since FEM is widely used, CAD packages commonly support the extraction of FE models from their solids, making the creation of these models easy to accomplish. Once created, the data for the FE model can be made available to other applications by exporting it to a text file. Although analysis packages exist that can handle triangulated solids, very little information [1][2][3] is publicly available on how the analysis is done. This article attempts to fill this hole by developing the necessary formulas and procedures.
For the author, the genesis of this article was a new routine for simulating the ditching of an aircraft in water. The routine worked by tracking the movement of water as it flowed into various parts of the aircraft. I originally attempted to craft a Catia macro, but quickly ran into problems. The routine required splitting solids by planes representing the water surface. Regularly, Catia would encounter errors in attempting the splits. I had to add special handling to work around these errors by estimating the results. When I finally produced a working program, it took over 8 hours to produce a very coarse simulation. And to my surprise, Catia had filled over 12 gigabytes of virtual memory, forcing me to reboot. It was clear that another approach would be needed to make this simulation viable. Rather than licensing and learning an existing FEM package, which might have its own computation overhead issues, I chose to program it on my own.
I would like to express my appreciation to Patrick Brown and especially to Victor Graham, who assisted me in the preparation of this paper.},
keywords = {12. Weight Engineering - Computer Applications},
pubstate = {published},
tppubtype = {inproceedings}
}
Alternative means of representing solid objects
can address these problems. One of the simplest
representations of a solid is by triangulation: the
surface of the solid is approximated by adjoining
triangles. The representation is not exact, but can
be refined to any desired level of precision. By
Stoke's theorem, any quantity that can be
expressed by an integration of a well—behaved
function over the volume of a solid can also be
expressed by an integration of a related function
over the solid's surface. So, for a given mass
distribution, it is only necessary to know the surface of the solid in order to do mass properties calculations. Representations such as this are the heart of Finite Element Modelling (FEM), and various sophisticated software packages are also available to perform analysis on FE models. However, sometimes a custom application may be preferable. Since FEM is widely used, CAD packages commonly support the extraction of FE models from their solids, making the creation of these models easy to accomplish. Once created, the data for the FE model can be made available to other applications by exporting it to a text file. Although analysis packages exist that can handle triangulated solids, very little information [1][2][3] is publicly available on how the analysis is done. This article attempts to fill this hole by developing the necessary formulas and procedures.
For the author, the genesis of this article was a new routine for simulating the ditching of an aircraft in water. The routine worked by tracking the movement of water as it flowed into various parts of the aircraft. I originally attempted to craft a Catia macro, but quickly ran into problems. The routine required splitting solids by planes representing the water surface. Regularly, Catia would encounter errors in attempting the splits. I had to add special handling to work around these errors by estimating the results. When I finally produced a working program, it took over 8 hours to produce a very coarse simulation. And to my surprise, Catia had filled over 12 gigabytes of virtual memory, forcing me to reboot. It was clear that another approach would be needed to make this simulation viable. Rather than licensing and learning an existing FEM package, which might have its own computation overhead issues, I chose to program it on my own.
I would like to express my appreciation to Patrick Brown and especially to Victor Graham, who assisted me in the preparation of this paper.@inproceedings{3600,
title = {3600. Autonomous Mass Properties Tracking Database Attributes},
author = {Edd Burt},
url = {https://www.sawe.org/product/paper-3600},
year = {2013},
date = {2013-05-01},
booktitle = {72nd Annual Conference, St. Louis, Missouri},
pages = {30},
publisher = {Society of Allied Weight Engineers, Inc.},
address = {Saint Louis, Missouri},
abstract = {Gulfstream has made some interesting discoveries while deploying our autonomous mass properties tracking database. Design attributes long used in manually updated databases are not always conducive to the design of an autonomous self-updating database. This technical paper intends to explore some of the more enlightening challenges and elegant solutions discovered while making our transition to an autonomous database.
Many obstacles to the development of an autonomous database have been cited. When does the weight of a part get verified if there is no engineer calculating the weight? Even if a part's weight is 100% perfect; that does not stop the 100% error from just one missing or extra quantity of it in the database. How do we verify the drawing tree is complete when there is no engineer inputting it? Will the computer make up drawing numbers for multiple use assemblies? How will we input delta actual weights when some program might come along behind us and mess them up? Design groups don't use the five RP$#$8 material codes; so how does an RP$#$8 report get generated from an autonomous database? Can a computer input the half-dozen other codes we also need to generate reports? Will someone have to re-write our programs every time CATIA releases a new version? We track airplanes designed long before V5 or electronic drawing release and all our airplane data, old and new, need to be viewed together. So tell me, just how is some database going to do all that for us, and make me confident in the answers?
Gulfstream has faced and overcome these and many more challenges in the pursuit of an autonomous self-updating database. The tradition of storing the weight of a part was abandoned in favor of storing the bill of materials it is calculated from. Our database sums a part weight like an assembly weight. The exception is it totals materials and finishes instead of parts and sub-assemblies. Like back in school - the database shows its work. This simple design allows the database to record how much of the real materials and finishes, found in the drawing release system, build the weight. It does not pick from a list of made-up codes. Volumes, areas and lengths come from a database where they are stored for certification purposes by design groups. This is done in the drawing review and release processes. CATIA is not touched by Mass Properties software to calculate the weight of a part; so new releases do not affect our weight calculations. Drawing release materials and finishes are built from the five RP$#$8 materials. So densities are recorded in the database and RP$#$8 reports can be run from the database. This allows a simple database design where installations, assemblies, parts, materials, finishes and RP$#$8 materials are all stored together. Those many types of components, stored in a single component table, build up to total airplanes in a single bill of materials table. This is accomplished by coupling the Quantity field with a Unit of Measure field. The Unit of Measure contains units like 'Each', 'IN^3', 'IN^2' and 'IN'. Only five components are to have the unit of measure called 'Pound' - the five RP$#$8 materials - and they are the very bottom callout in every branch of every bill of materials. It was also discovered that all the codes used to report mass properties can be derived from a matrix of just two available attributes. Gulfstream hopes you find the advances we are making as exciting to you as they are to us when you read and study this technical paper.},
keywords = {12. Weight Engineering - Computer Applications},
pubstate = {published},
tppubtype = {inproceedings}
}
Many obstacles to the development of an autonomous database have been cited. When does the weight of a part get verified if there is no engineer calculating the weight? Even if a part's weight is 100% perfect; that does not stop the 100% error from just one missing or extra quantity of it in the database. How do we verify the drawing tree is complete when there is no engineer inputting it? Will the computer make up drawing numbers for multiple use assemblies? How will we input delta actual weights when some program might come along behind us and mess them up? Design groups don't use the five RP$#$8 material codes; so how does an RP$#$8 report get generated from an autonomous database? Can a computer input the half-dozen other codes we also need to generate reports? Will someone have to re-write our programs every time CATIA releases a new version? We track airplanes designed long before V5 or electronic drawing release and all our airplane data, old and new, need to be viewed together. So tell me, just how is some database going to do all that for us, and make me confident in the answers?
Gulfstream has faced and overcome these and many more challenges in the pursuit of an autonomous self-updating database. The tradition of storing the weight of a part was abandoned in favor of storing the bill of materials it is calculated from. Our database sums a part weight like an assembly weight. The exception is it totals materials and finishes instead of parts and sub-assemblies. Like back in school - the database shows its work. This simple design allows the database to record how much of the real materials and finishes, found in the drawing release system, build the weight. It does not pick from a list of made-up codes. Volumes, areas and lengths come from a database where they are stored for certification purposes by design groups. This is done in the drawing review and release processes. CATIA is not touched by Mass Properties software to calculate the weight of a part; so new releases do not affect our weight calculations. Drawing release materials and finishes are built from the five RP$#$8 materials. So densities are recorded in the database and RP$#$8 reports can be run from the database. This allows a simple database design where installations, assemblies, parts, materials, finishes and RP$#$8 materials are all stored together. Those many types of components, stored in a single component table, build up to total airplanes in a single bill of materials table. This is accomplished by coupling the Quantity field with a Unit of Measure field. The Unit of Measure contains units like 'Each', 'IN^3', 'IN^2' and 'IN'. Only five components are to have the unit of measure called 'Pound' - the five RP$#$8 materials - and they are the very bottom callout in every branch of every bill of materials. It was also discovered that all the codes used to report mass properties can be derived from a matrix of just two available attributes. Gulfstream hopes you find the advances we are making as exciting to you as they are to us when you read and study this technical paper.2012
@inproceedings{3556,
title = {3556. Composite Tank Structure Dynamics Modeling Based On Finite Particles},
author = {André Baeten},
url = {https://www.sawe.org/product/paper-3556},
year = {2012},
date = {2012-05-01},
booktitle = {71st Annual Conference, Bad Gögging, Germany},
pages = {23},
publisher = {Society of Allied Weight Engineers, Inc.},
address = {Bad Gögging, Germany},
abstract = {This paper deals with the modeling of multi-layer airborne composite tank structures interacting with liquids. The analysis is carried out in terms of sloshing impact pressure and focuses on an innovative modeling approach of elastic tank walls.
This approach is based on finite particles, which provide similar properties as finite elements in classical structure mechanics. It is implemented into a computationally efficient numerical multi-body simulation program, which is flexible in geometry and dynamic load spectrum. It features a particle-based liquid model and provides time accurate hydrodynamic pressure results in three dimensions and 6 Degrees-of-Freedom.
Based on the results of a generic tank geometry undergoing short-time accelerations using a rigid wall model, unsteady sloshing loads are computed for elastic tank walls.
The stresses and strains are discussed to optimize the structure in terms of impact pressure loading. Thereby, the tank geometry is flexible in terms of wall friction, elasticity laws and damping coefficients.
A special focus has been set on the feasibility and production issues of an advanced lightweight tank. Based on the maximum loads obtained from the sloshing analysis for rigid and elastic walls, the coupled liquid-structure dynamics is analyzed in order to provide some recommendations for a possible structural layout.},
keywords = {12. Weight Engineering - Computer Applications},
pubstate = {published},
tppubtype = {inproceedings}
}
This approach is based on finite particles, which provide similar properties as finite elements in classical structure mechanics. It is implemented into a computationally efficient numerical multi-body simulation program, which is flexible in geometry and dynamic load spectrum. It features a particle-based liquid model and provides time accurate hydrodynamic pressure results in three dimensions and 6 Degrees-of-Freedom.
Based on the results of a generic tank geometry undergoing short-time accelerations using a rigid wall model, unsteady sloshing loads are computed for elastic tank walls.
The stresses and strains are discussed to optimize the structure in terms of impact pressure loading. Thereby, the tank geometry is flexible in terms of wall friction, elasticity laws and damping coefficients.
A special focus has been set on the feasibility and production issues of an advanced lightweight tank. Based on the maximum loads obtained from the sloshing analysis for rigid and elastic walls, the coupled liquid-structure dynamics is analyzed in order to provide some recommendations for a possible structural layout.@inproceedings{3559,
title = {3559. Fuel Mass Properties Calculation with CATIA V5},
author = {Ralf Funk},
url = {https://www.sawe.org/product/paper-3559},
year = {2012},
date = {2012-05-01},
booktitle = {71st Annual Conference, Bad Gögging, Germany},
pages = {21},
publisher = {Society of Allied Weight Engineers, Inc.},
address = {Bad Gögging, Germany},
abstract = {Complex aircraft tank geometries due to challenging requirements are designed nowadays using CAD allowing analysis in a concise and cheap way. For fuel mass properties calculation inside CATIA V5 a corresponding feature has to be provided via fuel macro.
This programme can be used in the various design and development phases of an aircraft. Hence this tool is qualified for analysis of simple cuboids in the Pre-Draft as well as positioned and optimised tank geometries with integrated pumps or pipes in the Pre-Design-Phase, Product-Design-Phase or In-Service-Phase.
Fuel mass properties are essential for aircraft moments of inertia (MOI) determination, flight performance (Flight Control System) and mission performance evaluation.
Processing with CATIA V5 is possible for CAD-solids, which are designed in the CATIA V4/ V5 environment or having a compatible file format. Before starting the analysis it is necessary to install the basic settings and to prepare the files with a powercopy providing the CAD-model with various parameters and geometry, thus the user of this programme requires a basic knowledge of CATIA V5.
This paper gives an overview to run the fuel macro for individual tanks or tank groups for various configured fuel rundown sequences. The simplification of internal tank geometry is compensated by a feature of the tool which provides fuel density variation. Further input parameters are the flight attitude with individual air space and unusable fuel.
The Log-File contains apart from fuel mass properties of tank geometries the input parameters and more detailed information for interpretation of results.},
keywords = {11. Weight Engineering - Aircraft Estimation, 12. Weight Engineering - Computer Applications},
pubstate = {published},
tppubtype = {inproceedings}
}
This programme can be used in the various design and development phases of an aircraft. Hence this tool is qualified for analysis of simple cuboids in the Pre-Draft as well as positioned and optimised tank geometries with integrated pumps or pipes in the Pre-Design-Phase, Product-Design-Phase or In-Service-Phase.
Fuel mass properties are essential for aircraft moments of inertia (MOI) determination, flight performance (Flight Control System) and mission performance evaluation.
Processing with CATIA V5 is possible for CAD-solids, which are designed in the CATIA V4/ V5 environment or having a compatible file format. Before starting the analysis it is necessary to install the basic settings and to prepare the files with a powercopy providing the CAD-model with various parameters and geometry, thus the user of this programme requires a basic knowledge of CATIA V5.
This paper gives an overview to run the fuel macro for individual tanks or tank groups for various configured fuel rundown sequences. The simplification of internal tank geometry is compensated by a feature of the tool which provides fuel density variation. Further input parameters are the flight attitude with individual air space and unusable fuel.
The Log-File contains apart from fuel mass properties of tank geometries the input parameters and more detailed information for interpretation of results.@inproceedings{3560,
title = {3560. Dummy Optimization Regarding Mass Properties for Shaker Test and Flight Test},
author = {Jürgen Clermont},
url = {https://www.sawe.org/product/paper-3560},
year = {2012},
date = {2012-05-01},
booktitle = {71st Annual Conference, Bad Gögging, Germany},
pages = {45},
publisher = {Society of Allied Weight Engineers, Inc.},
address = {Bad Gögging, Germany},
abstract = {For shaker- and flight test in aircraft development, replacement bodies with similar physical properties as the real body (like a black box) have to be created.
A body like this is called DUMMY and the meant properties are mass, center of gravity in x-, y- and z-direction, as well as inertias (in total 10 components).
These dynamic tests are essential to generate adequate mountings/bearings or to reproduce the real behaviour of an airplane or a subsystem in flight.
Dummies are used when the exact part is not (yet) available or the part is too expensive to destroy it by testing.
To produce dummies, results within 10% deviation (per component) are necessary for dynamic similarity. By trial and error it is possible to create such a body, but it is either time intensive or the precision is not very high. The higher the accuracy of all 10 components of mass properties, the better is the similarity and the better will be the results for mountings and bearings.
Based on an inertia program with shape code calculation capability, an iterative process to create a dummy was developed. By variation of at least 4 bodies it is possible to get first results in all components. Up to a variation of 8 bodies and more is possible. To get good results in acceptable time and effort, a well-thought-out code is essential.
This iteration process produces a lot of data, but with effective code and modern computing hardware it is possible to create more than 100.000 iterations per hour, where one of it is a best fit within 5% deviation or better.},
keywords = {12. Weight Engineering - Computer Applications, 30. Miscellaneous},
pubstate = {published},
tppubtype = {inproceedings}
}
A body like this is called DUMMY and the meant properties are mass, center of gravity in x-, y- and z-direction, as well as inertias (in total 10 components).
These dynamic tests are essential to generate adequate mountings/bearings or to reproduce the real behaviour of an airplane or a subsystem in flight.
Dummies are used when the exact part is not (yet) available or the part is too expensive to destroy it by testing.
To produce dummies, results within 10% deviation (per component) are necessary for dynamic similarity. By trial and error it is possible to create such a body, but it is either time intensive or the precision is not very high. The higher the accuracy of all 10 components of mass properties, the better is the similarity and the better will be the results for mountings and bearings.
Based on an inertia program with shape code calculation capability, an iterative process to create a dummy was developed. By variation of at least 4 bodies it is possible to get first results in all components. Up to a variation of 8 bodies and more is possible. To get good results in acceptable time and effort, a well-thought-out code is essential.
This iteration process produces a lot of data, but with effective code and modern computing hardware it is possible to create more than 100.000 iterations per hour, where one of it is a best fit within 5% deviation or better.@inproceedings{3574,
title = {3574. Updated SumMassProps A Comprehensive Excel-Based Mass Properties Solution},
author = {Robert L. Zimmerman},
url = {https://www.sawe.org/product/paper-3574},
year = {2012},
date = {2012-05-01},
booktitle = {71st Annual Conference, Bad Gögging, Germany},
pages = {13},
publisher = {Society of Allied Weight Engineers, Inc.},
address = {Bad Gögging, Germany},
abstract = {In May 2003 at the Society of Allied Weight Engineers International Conference on Weight Engineering in New Haven Connecticut, the author presented the original release version of SumMassProps as part of SAWE Paper 3310. SumMassProps is an Excel-based add-in that provides within Microsoft Excel a comprehensive set of mass properties functions to sum component mass properties. In the intervening years, over 100 interface improvements, bug fixes, speed enhancements, and additional functionality changes have been made to this add-in. The resulting version of SumMassProps is now a fully functional mass properties database manipulator using modern programming and error prevention techniques. Many of the improvements specifically address ease-of-use and error proofing the functionality of the add-in.
The present version of SumMassProps now creates the function prototypes for each of its menu-driven functions; performs full coordinate and inertia rotations; determines Principal Inertia Matrices and the corresponding Direction Cosine Matrix to arrive at the principal inertias; and incorporates the lessons of SAWE Paper 3360 depicting the correct derivation of mass property uncertainties. Additional functionality includes one click formula matrix filling; utilization of multiple mass properties formats; determination of ballast weights for dynamic balance; specific unit conversions; and the capability to undo any of SumMassProps' built-in functions.
SumMassProps as it currently stands is what the author envisioned this comprehensive solution to be when this odyssey began. The functionality and user interface makes Version 9 a desirable tool in the Mass Properties Engineer's arsenal.},
keywords = {12. Weight Engineering - Computer Applications},
pubstate = {published},
tppubtype = {inproceedings}
}
The present version of SumMassProps now creates the function prototypes for each of its menu-driven functions; performs full coordinate and inertia rotations; determines Principal Inertia Matrices and the corresponding Direction Cosine Matrix to arrive at the principal inertias; and incorporates the lessons of SAWE Paper 3360 depicting the correct derivation of mass property uncertainties. Additional functionality includes one click formula matrix filling; utilization of multiple mass properties formats; determination of ballast weights for dynamic balance; specific unit conversions; and the capability to undo any of SumMassProps' built-in functions.
SumMassProps as it currently stands is what the author envisioned this comprehensive solution to be when this odyssey began. The functionality and user interface makes Version 9 a desirable tool in the Mass Properties Engineer's arsenal.@inproceedings{3576,
title = {3576. Automation Methods Of Aircraft Weight Activities},
author = {O Isikdogan and T Kiper and E Unay and D. Gurak},
url = {https://www.sawe.org/product/paper-3576},
year = {2012},
date = {2012-05-01},
booktitle = {71st Annual Conference, Bad Gögging, Germany},
pages = {12},
publisher = {Society of Allied Weight Engineers, Inc.},
address = {Bad Gögging, Germany},
abstract = {This paper presents the optimization and automation efforts for aircraft weight activities in aircraft design projects. Those weight activities involve monitoring the aircraft total weight and inertia, evaluation of weight breakdown and calculation of mass and inertia distribution. The results are then submitted to project management, flight mechanics, structural analyses and design groups. The methods and tools developed for this study provide less time-consuming process and more accurate results. The mass and inertia properties of the aircraft are subject to change progressively during an aircraft design process. The challenge is to monitor those changes and report their effects instantly. An integrated system is designed to make all those weight activities to be automatically performed and controlled. The system works simultaneously with Computer Aided Design (CAD) software and provides real time monitoring of weight properties and weight breakdown of aircraft. In addition, this system helps the weight data to be more accessible and updated. Also, mass and inertia distribution of aircraft is evaluated in this integrated system as the mass model, consisting of lumped masses, required from related analysis groups. The most common method for this mass distribution calculation is slicing functions of CAD software. However, the methods developed for the weight activities help overcome the inefficiencies of solely depending on CAD software for large assemblies consisting of thousands of detailed parts, sub-assemblies, equipments, harness, systems etc. These tools are designed to be used in all phases of the aircraft design process, from conceptual to detailed design. In conclusion, the integrated system developed for the automation of weight activities is mentioned and compared to common methods used in industry. The advantages and impact of those new methods and tools to aircraft design are presented.},
keywords = {12. Weight Engineering - Computer Applications},
pubstate = {published},
tppubtype = {inproceedings}
}
@inproceedings{3590,
title = {3590. Optimized Mass Matrices Business Process},
author = {Radoslaw Zawadzki and Michael Hiersig},
url = {https://www.sawe.org/product/paper-3590},
year = {2012},
date = {2012-05-01},
booktitle = {71st Annual Conference, Bad Gögging, Germany},
pages = {17},
publisher = {Society of Allied Weight Engineers, Inc.},
address = {Bad Gögging, Germany},
abstract = {The Mass Matrices Process is part of the A/C development process in Flight Physics, creating mass model data as input for loads and aeroelastics. The methods have been developed by Airbus to increase the efficiency of weights engineer work. The modeling of mass properties is a key milestone in building aircraft dynamic and aeroelastic analyses and further more for dimensioning of primary structure. This paper discusses the optimized mass matrices business process for the MEW, OWE, payload and fuel calculation.
The earlier mass matrices process has been driven by various different tools but still with a great deal of manual work. The user needed to work on configuration files and had to manually copy data from one tool to the other. This process had a high risk of uncertainties and inconsistencies. It was extremely difficult to retain an overview of the total process and its associated data. A lot of time was used with the processing of data and few for actual calculations and innovations. Increasing requirements concerning quantity and quality indicated that the total process has to be improved. Intensive process analyses, customer needs interviews, risk and lean analyses led the definition, development and tool implementation of a new tool.
At the end this optimized business process allows to perform more loops and trade studies to be performed for the early evaluation of alternatives.},
keywords = {12. Weight Engineering - Computer Applications},
pubstate = {published},
tppubtype = {inproceedings}
}
The earlier mass matrices process has been driven by various different tools but still with a great deal of manual work. The user needed to work on configuration files and had to manually copy data from one tool to the other. This process had a high risk of uncertainties and inconsistencies. It was extremely difficult to retain an overview of the total process and its associated data. A lot of time was used with the processing of data and few for actual calculations and innovations. Increasing requirements concerning quantity and quality indicated that the total process has to be improved. Intensive process analyses, customer needs interviews, risk and lean analyses led the definition, development and tool implementation of a new tool.
At the end this optimized business process allows to perform more loops and trade studies to be performed for the early evaluation of alternatives.2011
@inproceedings{3530,
title = {3530. Confidence Of Mass Properties (COMP) Tool},
author = {James Smith},
url = {https://www.sawe.org/product/paper-3530},
year = {2011},
date = {2011-05-01},
booktitle = {70th Annual Conference, Houstion, Texas},
pages = {14},
publisher = {Society of Allied Weight Engineers, Inc.},
address = {Houston, Texas},
abstract = {This paper serves to outline and discuss the practices and methods used to check the mass distribution properties of airframe conceptual aircraft. This paper will show the type and fidelity of the information gathered, collation technique, and what pertinent information was utilized. Finally, it will show how calculations can draw conclusions to the viability and the integrity of the data proposed. In addition, it will show how basic geometric equations can be applied to ensure further that the data is within the magnitude of acceptance.},
keywords = {07. Section Properties, 12. Weight Engineering - Computer Applications},
pubstate = {published},
tppubtype = {inproceedings}
}
@inproceedings{3531,
title = {3531. Weight Data Management for Completion of Corporate Jets},
author = {Ragaa Mitry},
url = {https://www.sawe.org/product/paper-3531},
year = {2011},
date = {2011-05-01},
booktitle = {70th Annual Conference, Houstion, Texas},
pages = {18},
publisher = {Society of Allied Weight Engineers, Inc.},
address = {Houston, Texas},
abstract = {Cabin Completion Engineering is a very crucial phase of the high-end business jet aircraft design. The interior of the aircraft, including all of its customer-oriented and advanced technology, is perhaps one of the most important factors in the decision-making process of a potential corporate aircraft buyer. Indeed, range, performance and operating costs are factors, but the customer is also buying privacy and functionality. With this mindset, the Original Equipment Manufacturer is prone to hold nothing back - to 'spare no expense' - in the development of a state-of-the-art aircraft interior.
In order to protect vehicle performance, the weight and center of gravity of the completions must be maintained. Completions engineering is no different when it comes to the need to properly identify, sort, and budget weights, all while correlating Computer-Aided Design models to the proper installations. This task can be somewhat automated using contemporary design tools and appropriate software.
This paper discusses how to build a matrix to track and manage the completion development weight. The matrix is a depletion schedule that sets the limits for each installation and/or assembly. Whenever a weight exceeds the preliminary estimated weight, it will be immediately flagged red, bringing the attention of the designers to a potential problem. The estimated weight is based on historical data adjusted to the new aircraft. The depletion schedule matrix allows the quick generation of tables and charts at any given time during the program, drastically reducing the effort required to compile and create weight status reports.
The matrix calculations output graphs can be interpreted to ensure that the weight status of the detail is not only dependent on the weight recorded but its developmental maturity. Also, it is helpful in determining whether there are some areas that are sufficiently reduced in weight allowing for the reallocation of weight budget - and its CG location - to another area or if weight savings can result in improved aircraft performance.
This data can then be used by the engineer and program to quickly pinpoint weight-critical design areas.},
keywords = {11. Weight Engineering - Aircraft Estimation, 12. Weight Engineering - Computer Applications},
pubstate = {published},
tppubtype = {inproceedings}
}
In order to protect vehicle performance, the weight and center of gravity of the completions must be maintained. Completions engineering is no different when it comes to the need to properly identify, sort, and budget weights, all while correlating Computer-Aided Design models to the proper installations. This task can be somewhat automated using contemporary design tools and appropriate software.
This paper discusses how to build a matrix to track and manage the completion development weight. The matrix is a depletion schedule that sets the limits for each installation and/or assembly. Whenever a weight exceeds the preliminary estimated weight, it will be immediately flagged red, bringing the attention of the designers to a potential problem. The estimated weight is based on historical data adjusted to the new aircraft. The depletion schedule matrix allows the quick generation of tables and charts at any given time during the program, drastically reducing the effort required to compile and create weight status reports.
The matrix calculations output graphs can be interpreted to ensure that the weight status of the detail is not only dependent on the weight recorded but its developmental maturity. Also, it is helpful in determining whether there are some areas that are sufficiently reduced in weight allowing for the reallocation of weight budget - and its CG location - to another area or if weight savings can result in improved aircraft performance.
This data can then be used by the engineer and program to quickly pinpoint weight-critical design areas.@inproceedings{3534,
title = {3534. Mass Properties Requirements For Marine Design Software},
author = {Alan Titcomb and Keith Carter and Ronnie Moore},
url = {https://www.sawe.org/product/paper-3534},
year = {2011},
date = {2011-05-01},
booktitle = {70th Annual Conference, Houstion, Texas},
pages = {18},
publisher = {Society of Allied Weight Engineers, Inc.},
address = {Houston, Texas},
abstract = {Design tools have made significant progress since the days of drafting boards and T-squares. Today's advanced 3-D product modeling systems offer tremendous capability in both design and analysis. However, the same capabilities that benefit the ship designer are usually not optimized for the mass properties engineer or weight calculator who must extract data from the product model to determine weights and moments for the marine product in question. In the marine field, the identification of functionality to support the mass properties function is developed each time a new design system is deployed and often gets much less attention than the design function. Because new design tools are usually not developed specifically for the marine industry, extensive customization including mass properties functionality is generally required for each marine application. No industry standard exists for the basic functional requirements which a new design tool should satisfy. This paper will attempt to define core functional requirements needed by mass properties engineers in the marine field. It is hoped that this effort will allow the mass properties engineer faced with the advent of a new design tool to dedicate more time in the future to the unique or specialized features desired rather than the core mass properties requirements that should be met by all advanced design tools.},
keywords = {12. Weight Engineering - Computer Applications, Marine},
pubstate = {published},
tppubtype = {inproceedings}
}
2010
@inproceedings{3495,
title = {3495. Using PHP/MySQL to Manage Potential Mass Impacts},
author = {I. Benjamin Hager},
url = {https://www.sawe.org/product/paper-3495},
year = {2010},
date = {2010-05-01},
booktitle = {69th Annual Conference, Virginia Beach, Virginia},
pages = {20},
publisher = {Society of Allied Weight Engineers, Inc.},
address = {Virginia Beach, Virginia},
abstract = {This paper presents a new application using commercially available software to manage mass properties
for spaceflight vehicles. PHP/MySQL (PHP: Hypertext Preprocessor and My Structured Query
Language) are a web scripting language and a database language commonly used in concert with each
other. They open up new opportunities to develop cutting edge mass properties tools, and tools for the
management of potential mass impacts (threats and opportunities). The paper begins by providing an
overview of the functions and capabilities of PHP/MySQL. The focus of this paper is on how
PHP/MySQL are being used to develop an advanced 'web accessible' database system for identifying
and managing mass impacts on NASA's Ares I Upper Stage program, managed by the Marshall Space
Flight Center. To fully describe this application, examples of the data, search, and view pages are
provided to show, not only the function, but the security, ease of use, and simplicity of this new
application.
The premise behind this paper is that PHP/MySQL are software tools that are easy to use and readily
available for the development of cutting edge mass properties applications. These tools are capable of
providing 'real-time' searching and status of an active database, automated report generation, and other
capabilities to streamline and enhance mass properties management application. By using
PHP/MySQL, proven existing methods for managing mass properties can be adapted to present-day
information technology to accelerate mass properties data gathering, analysis, and reporting, allowing
mass property engineers, and the management they support, to keep pace with today's fast-pace design
and development processes.},
keywords = {12. Weight Engineering - Computer Applications, 26. Weight Growth},
pubstate = {published},
tppubtype = {inproceedings}
}
for spaceflight vehicles. PHP/MySQL (PHP: Hypertext Preprocessor and My Structured Query
Language) are a web scripting language and a database language commonly used in concert with each
other. They open up new opportunities to develop cutting edge mass properties tools, and tools for the
management of potential mass impacts (threats and opportunities). The paper begins by providing an
overview of the functions and capabilities of PHP/MySQL. The focus of this paper is on how
PHP/MySQL are being used to develop an advanced 'web accessible' database system for identifying
and managing mass impacts on NASA's Ares I Upper Stage program, managed by the Marshall Space
Flight Center. To fully describe this application, examples of the data, search, and view pages are
provided to show, not only the function, but the security, ease of use, and simplicity of this new
application.
The premise behind this paper is that PHP/MySQL are software tools that are easy to use and readily
available for the development of cutting edge mass properties applications. These tools are capable of
providing 'real-time' searching and status of an active database, automated report generation, and other
capabilities to streamline and enhance mass properties management application. By using
PHP/MySQL, proven existing methods for managing mass properties can be adapted to present-day
information technology to accelerate mass properties data gathering, analysis, and reporting, allowing
mass property engineers, and the management they support, to keep pace with today's fast-pace design
and development processes.@inproceedings{3498,
title = {3498. Introduction of Mass Management Software - Our experiences},
author = {Claudia Rosenberger},
url = {https://www.sawe.org/product/paper-3498},
year = {2010},
date = {2010-05-01},
booktitle = {69th Annual Conference, Virginia Beach, Virginia},
pages = {16},
publisher = {Society of Allied Weight Engineers, Inc.},
address = {Virginia Beach, Virginia},
abstract = {From the design to the in-service phase of products, managing mass properties is a running
challenge. High technology products are becoming more and more complex, so time and
resources necessary for a proper handling of mass properties are increasing considerably.
Standard software products like MS Excel are meeting the limits of its capacities facing this
request.
In August 2009, EADS Germany decided to introduce the mass management system M3 of
usb GmbH for all military projects like Tornado, Eurofighter and all future projects.
This paper is written in cooperation of usb and EADS and will report our common
experiences during the introduction of this software. The main points are:
What are the reasons for EADS to choose M3?
What are the main improvements compared to previous situation?
What are the main steps and milestones during the introduction?
These questions are answered in detail by this paper, describing the features of M3 and how
these features support EADS Mass Properties department to make its work easier and more
effective. Different projects in different production phases from early design up to in service
phase are managed by M3. The paper shows, how these different requirements and algorithms
are handled by the software.
At the moment M3 replaces former software tools and is used as a standalone system.
However, it is planned to apply its full capabilities as an open system to integrate other
applications into the mass management processes. Therefore, data exchange with CATIA and
the PLM System will be installed in the next steps. Automation of workflow avoids manual
data entry, increases productivity and ensures quality of work.},
keywords = {12. Weight Engineering - Computer Applications},
pubstate = {published},
tppubtype = {inproceedings}
}
challenge. High technology products are becoming more and more complex, so time and
resources necessary for a proper handling of mass properties are increasing considerably.
Standard software products like MS Excel are meeting the limits of its capacities facing this
request.
In August 2009, EADS Germany decided to introduce the mass management system M3 of
usb GmbH for all military projects like Tornado, Eurofighter and all future projects.
This paper is written in cooperation of usb and EADS and will report our common
experiences during the introduction of this software. The main points are:
What are the reasons for EADS to choose M3?
What are the main improvements compared to previous situation?
What are the main steps and milestones during the introduction?
These questions are answered in detail by this paper, describing the features of M3 and how
these features support EADS Mass Properties department to make its work easier and more
effective. Different projects in different production phases from early design up to in service
phase are managed by M3. The paper shows, how these different requirements and algorithms
are handled by the software.
At the moment M3 replaces former software tools and is used as a standalone system.
However, it is planned to apply its full capabilities as an open system to integrate other
applications into the mass management processes. Therefore, data exchange with CATIA and
the PLM System will be installed in the next steps. Automation of workflow avoids manual
data entry, increases productivity and ensures quality of work.2009
@inproceedings{3475,
title = {3475. Mass Distribution, Weight, and Center of Gravity application using CATIA V5},
author = {Scott Edmounson and Angelo Papanastasiou},
url = {https://www.sawe.org/product/paper-3475},
year = {2009},
date = {2009-05-01},
booktitle = {68th Annual Conference, Wichita, Kansas},
pages = {9},
address = {Wichita, Kansas},
abstract = {Inertia 360, software to automate mass distribution calculations and reporting with
CATIA V5, has been developed. The software has been used successfully on very large CATIA V5 assemblies to extract mass properties, create flexible volume sections and extract these mass properties and then output accurate weight, mass and fuel distribution reports. The software provides for more accurate reports, reduces the potential for human error and greatly reduces the time required to generate reports.},
keywords = {07. Section Properties, 12. Weight Engineering - Computer Applications},
pubstate = {published},
tppubtype = {inproceedings}
}
CATIA V5, has been developed. The software has been used successfully on very large CATIA V5 assemblies to extract mass properties, create flexible volume sections and extract these mass properties and then output accurate weight, mass and fuel distribution reports. The software provides for more accurate reports, reduces the potential for human error and greatly reduces the time required to generate reports.