SAWE Technical Papers
Technical Library
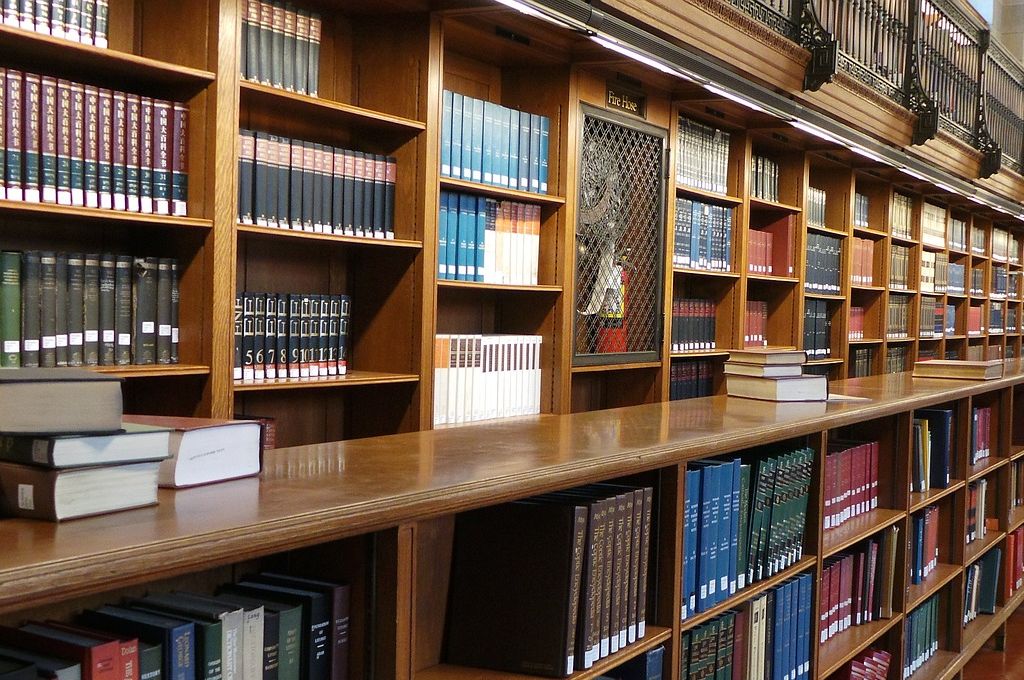
SAWE Paper Database
The SAWE Technical Library contains nearly 4000 technical papers available here for purchase and download. Use the search options below to find what you need.
3779. Determining the Center of Gravity of the Electric No Emissions Low Drag Airframe (NELDA) Haley, Christl K. In: 81st Annual Conference, Savannah, Georgia, pp. 27, Society of Allied Weight Engineers, Inc., Savannah, Georgia, 2022. Abstract | Buy/Download | BibTeX | Tags: 03. Center Of Gravity, 10. Weight Engineering - Aircraft Design, Student Papers 3768. Mass Properties Reporting Ma, Yiyuan; Yan, Jin; Elham, Ali In: 2021 SAWE Tech Fair, pp. 28, Society of Allied Weight Engineers, Inc., Virtual Conference, 2021. Abstract | Buy/Download | BibTeX | Tags: 10. Weight Engineering - Aircraft Design, 11. Weight Engineering - Aircraft Estimation, Student Papers 3739. Rotorcraft Mass Assessment in an Integrated Design Framework Schwinn, Dominik B.; Weiand, Peter In: 2020 SAWE Tech Fair, pp. 15, Society of Allied Weight Engineers, Inc., Virtual Conference, 2020. Abstract | Buy/Download | BibTeX | Tags: 10. Weight Engineering - Aircraft Design, 21. Weight Engineering - Statistical Studies, 24. Weight Engineering - System Design 3760. Design for Positive Static Margin for a Radio-Controlled Box-Wing Aircraft Bellerjeau, Charlotte In: 2020 SAWE Tech Fair, pp. 12, Society of Allied Weight Engineers, Inc., Virtual Conference, 2020. Abstract | Buy/Download | BibTeX | Tags: 10. Weight Engineering - Aircraft Design, 34. Advanced Design, Student Papers 3734. Dynamic Computer Simulation of Aircraft Buoyancy Stubbers, Peter In: 2020 SAWE Tech Fair, pp. 97, Society of Allied Weight Engineers, Inc., Virtual Conference, 2020. Abstract | Buy/Download | BibTeX | Tags: 10. Weight Engineering - Aircraft Design 3714. Weight and Design Data for World War II - Era United States Military Aircraft Cate, Dudley M In: 78th Annual Conference, Norfolk, VA, pp. 39, Society of Allied Weight Engineers, Inc., Norfolk, Virginia, 2019. Abstract | Buy/Download | BibTeX | Tags: 10. Weight Engineering - Aircraft Design, 30. Miscellaneous 3729. Application of SAWE Course 'Developing Basic Parametric Methods' to Nacelle Weight Estimating Fisher, Doug In: 78th Annual Conference, Norfolk, VA, pp. 17, Society of Allied Weight Engineers, Inc., Norfolk, Virginia, 2019. Abstract | Buy/Download | BibTeX | Tags: 10. Weight Engineering - Aircraft Design, 11. Weight Engineering - Aircraft Estimation, 21. Weight Engineering - Statistical Studies 3690. Weight Optimization of Environmental Control System of Corporate Jets Mitry, Ragaa In: 76th Annual Conference, Montreal, Canada, pp. 20, Society of Allied Weight Engineers, Inc., Montreal, Canada, 2017. Abstract | Buy/Download | BibTeX | Tags: 10. Weight Engineering - Aircraft Design, 24. Weight Engineering - System Design 3655. Weight and Structural Optimization in Aircraft Design Alves, William; Silva, Juliana In: 75th Annual Conference, Denver, Colorado, pp. 30, Society of Allied Weight Engineers, Inc., Denver, Colorado, 2016. Abstract | Buy/Download | BibTeX | Tags: 10. Weight Engineering - Aircraft Design, 22. Weight Engineering - Structural Design, 28. Weight Reduction - Processes, 34. Advanced Design 3660. Development of a Conceptual Flight Vehicle Design Weight Estimation Method Library Walker, Andy In: 75th Annual Conference, Denver, Colorado, pp. 171, Society of Allied Weight Engineers, Inc., Denver, Colorado, 2016, (Mike HackneyBest Paper Award - 2016). Abstract | Buy/Download | BibTeX | Tags: 10. Weight Engineering - Aircraft Design, 11. Weight Engineering - Aircraft Estimation, Mike Hackney Best Paper Award 3662. Minimizing Mass of a Spacecraft Structure Burkey, Larry; Cervantes, Jorge; Gillis, Lewis; Graser, Evan; Howard, Megan; Iskra, Andrei; Maurer, Taylor; Peterson, Davis; Williams, Margaret In: 75th Annual Conference, Denver, Colorado, pp. 26, Society of Allied Weight Engineers, Inc., Denver, Colorado, 2016. Abstract | Buy/Download | BibTeX | Tags: 10. Weight Engineering - Aircraft Design, Student Papers 3648. Engine Integration to Aircraft of Corporate Jets Mitry, Ragaa In: 74th Annual Conference, Alexandria, Virginia, pp. 17, Society of Allied Weight Engineers, Inc., Alexandria, Virginia, 2015. Abstract | Buy/Download | BibTeX | Tags: 10. Weight Engineering - Aircraft Design Dorbath, Felix In: 73rd Annual Conference, Long Beach, California, pp. 23, Society of Allied Weight Engineers, Inc., Long Beach, California, 2014. Abstract | Buy/Download | BibTeX | Tags: 10. Weight Engineering - Aircraft Design, 23. Weight Engineering - Structural Estimation Elham, Ali; Tooren, Michel J. L. In: 72nd Annual Conference, St. Louis, Missouri, pp. 27, Society of Allied Weight Engineers, Inc., Saint Louis, Missouri, 2013. Abstract | Buy/Download | BibTeX | Tags: 10. Weight Engineering - Aircraft Design 3606. Design Considerations Of Flight Control Systems In High Performance General Aviation Aircraft McCloud, Darrin In: 72nd Annual Conference, St. Louis, Missouri, pp. 20, Society of Allied Weight Engineers, Inc., Saint Louis, Missouri, 2013. Abstract | Buy/Download | BibTeX | Tags: 10. Weight Engineering - Aircraft Design Dorbath, Felix; Nagel, Björn; Gollnick, Volker In: 71st Annual Conference, Bad Gögging, Germany, pp. 21, Society of Allied Weight Engineers, Inc., Bad Gögging, Germany, 2012, (Mike Hackney Best Paper Award). Abstract | Buy/Download | BibTeX | Tags: 10. Weight Engineering - Aircraft Design, 23. Weight Engineering - Structural Estimation, Mike Hackney Best Paper Award 3571. An Advanced Quasi-Analytical Weight Estimation Method for Airplane Lifting Surfaces Elham, Ali; Rocca, Gianfranco La; Tooren, Michel J. L. In: 71st Annual Conference, Bad Gögging, Germany, pp. 19, Society of Allied Weight Engineers, Inc., Bad Gögging, Germany, 2012. Abstract | Buy/Download | BibTeX | Tags: 10. Weight Engineering - Aircraft Design 3509. Airframe Wingbox Preliminary Design and Weight Prediction AINSWORTH, JAMES; COLLIER, CRAIG; YARRINGTON, PHIL; LUCKING, RYAN; LOCKE, JAMES In: 69th Annual Conference, Virginia Beach, Virginia, pp. 41, Society of Allied Weight Engineers, Inc., Virginia Beach, Virginia, 2010. Abstract | Buy/Download | BibTeX | Tags: 10. Weight Engineering - Aircraft Design Higgins, Chuck In: 68th Annual Conference, Wichita, Kansas, pp. 13, Wichita, Kansas, 2009. Abstract | Buy/Download | BibTeX | Tags: 10. Weight Engineering - Aircraft Design, 18. Weight Engineering - Spacecraft Design, 22. Weight Engineering - Structural Design 3474. U.S. Fighter Aircraft Design, Weight And Performance Trends Cate, Dudley M In: 68th Annual Conference, Wichita, Kansas, pp. 95, Wichita, Kansas, 2009. Abstract | Buy/Download | BibTeX | Tags: 10. Weight Engineering - Aircraft Design, 21. Weight Engineering - Statistical Studies2022
@inproceedings{3779,
title = {3779. Determining the Center of Gravity of the Electric No Emissions Low Drag Airframe (NELDA)},
author = {Christl K. Haley},
url = {https://www.sawe.org/product/paper-3779},
year = {2022},
date = {2022-05-21},
urldate = {2022-05-21},
booktitle = {81st Annual Conference, Savannah, Georgia},
pages = {27},
publisher = {Society of Allied Weight Engineers, Inc.},
address = {Savannah, Georgia},
abstract = {Although climate change has become an impending issue for all of humanity, it has brought nations together to design and create a variety of systems that leave little to no carbon footprint. The No Emission Low Drag Airframe (NELDA) is a unique electric aircraft design which aims to join this world-wide mission. The author (the airframe design lead) and her senior design team from the University of Colorado Boulder spent the fall semester of 2021 designing this commuter aircraft. NELDA can fly 6 passengers at a cruise altitude of 12,000 ft MSL, at a cruise speed of 150 knots for 1.5 hours with a 30-minute reserve, making this a perfect aircraft for short, direct flights. The characteristics for this aircraft aim to be certified under Federal Aviation Regulation (FAR) 23 to ensure the safety of every passenger. Multiple trade studies were conducted to determine the design choices that make up this innovative aircraft. These studies resulted in an aft-mid-mounted wing, a canard, fixed tricycle landing gear, butterfly doors, and a pusher-propeller powertrain configuration. The specific energy, density, volume, and weight of the electric powertrain were estimated using a 5-year prediction for solid-state batteries. Since these batteries do not exist today, it was very challenging to accurately model and place the power system. The range and endurance of NELDA were used to determine the volume, number, and weight of the batteries. The safety of passengers, size of the batteries, and functionality of each battery were all considered while determining where and how to place the batteries among the other major components of NELDA. Additionally, it was critical to strategically place each of the components to achieve an acceptable static margin of 10%, as well as predictable dynamic and static flight characteristics. The designers of NELDA believe that their successful commuter electric airplane design will be part of the beginning of new, improved, clean aerial transportation.},
keywords = {03. Center Of Gravity, 10. Weight Engineering - Aircraft Design, Student Papers},
pubstate = {published},
tppubtype = {inproceedings}
}
2021
@inproceedings{3768,
title = {3768. Mass Properties Reporting},
author = {Yiyuan Ma and Jin Yan and Ali Elham},
url = {https://www.sawe.org/product/paper-3768},
year = {2021},
date = {2021-11-01},
urldate = {2021-11-01},
booktitle = {2021 SAWE Tech Fair},
pages = {28},
publisher = {Society of Allied Weight Engineers, Inc.},
address = {Virtual Conference},
abstract = {The Ultra-High Aspect Ratio Wing (UHARW) concept can improve the aircraft's aerodynamic efficiency and reduce fuel consumption. The Twin-Fuselage (TF) configuration is one of the most promising concepts for the UHARW design to reduce the wing bending moments and shear forces. This paper presents the development of a semi-empirical method for the weight estimation of TF aircraft in the initial sizing stage. A physics-based wing weight estimation method is improved for higher aerodynamic analysis fidelity and composite materials, which is used in the design of experiments and the results are applied for regression analysis to establish a semi-empirical method. Eventually, the established semi- empirical weight estimation method is integrated into a TF aircraft conceptual design and performance analysis framework, and a mid-range TF aircraft and a long-range TF aircraft are designed and sized to illustrate its application and efficiency in rapidly estimating the TF aircraft weight breakdown.},
keywords = {10. Weight Engineering - Aircraft Design, 11. Weight Engineering - Aircraft Estimation, Student Papers},
pubstate = {published},
tppubtype = {inproceedings}
}
2020
@inproceedings{3739,
title = {3739. Rotorcraft Mass Assessment in an Integrated Design Framework},
author = {Dominik B. Schwinn and Peter Weiand},
url = {https://www.sawe.org/product/paper-3739},
year = {2020},
date = {2020-07-01},
booktitle = {2020 SAWE Tech Fair},
pages = {15},
publisher = {Society of Allied Weight Engineers, Inc.},
address = {Virtual Conference},
abstract = {Mass estimation is an essential discipline in the design process of aeronautical vehicles. The maximum take-off mass determines most other design parameters and should therefore be estimated sufficiently precise from the beginning. In the conceptual design phase fast analyses are required in order to allow trade-off studies. In general, this phase is dominated by the use of analytical and statistical methods. At the end of this design stage, a basic external layout has been elaborated and basic design parameters have been determined.During the subsequent preliminary design stage, physics based higher fidelity methods are applied to further elaborate the design and to establish an internal configuration. The constantly increasing computational power allows comparably fast analyses in this design stage that may alter the configuration established in the conceptual design stage.Particular challenges in this design approach arise with unconventional configurations, such as compound rotorcraft, or with different propulsion systems to be integrated, for instance electric or hybrid systems, because of a lack of sufficient statistical data.The German Aerospace Center (DLR) has established the integrated design environment IRIS (Integrated Rotorcraft Initial Sizing) to allow an assessment of virtual rotorcraft configurations. It covers the conceptual and parts of the preliminary design stage and uses the data model CPACS (Common Parametric Aircraft Configuration Schema) for the parametric rotorcraft description.Component masses in IRIS are estimated using various statistical methods during the conceptual design stage. Finite Element (FE) methods are applied in the preliminary design phase to allow a more precise estimation of the structural mass which may influence the maximum take-off mass and therefore the performance characteristics calculated in the conceptual design stage.This paper introduces the design environment IRIS, and in particular the PANDORA framework (Parametric Numerical Design and Optimization Routines for Aircraft) which is used for the statistical estimation of the rotorcraft component masses and the structural sizing process to determine the fuselage mass.},
keywords = {10. Weight Engineering - Aircraft Design, 21. Weight Engineering - Statistical Studies, 24. Weight Engineering - System Design},
pubstate = {published},
tppubtype = {inproceedings}
}
@inproceedings{3760,
title = {3760. Design for Positive Static Margin for a Radio-Controlled Box-Wing Aircraft},
author = {Charlotte Bellerjeau},
url = {https://www.sawe.org/product/paper-3760},
year = {2020},
date = {2020-07-01},
booktitle = {2020 SAWE Tech Fair},
pages = {12},
publisher = {Society of Allied Weight Engineers, Inc.},
address = {Virtual Conference},
abstract = {This paper will detail the aerodynamic design of a small unmanned box-wing aircraft to facilitate the study of turbulence by Dr. Brian Argrow at the CU Boulder. A design with no fuselage was necessary for the data collection, which presented a longitudinal stability challenge. The key to eventually achieving a stable design was weight placement for positive static margin. This paper will include the design process used to confront these issues. The initial choices of stagger, gap, decalage, and relative sweep are made using a simple model leveraging previous box-wing research. These, as well as the airfoil selection, are then investigated further using Athena Vortex Lattice (AVL) to analyze lift, drag, and stability. The final airframe design has a gap and stagger of 1 chord length, decalage of 5 degrees, and relative sweep of 30 degrees. A cambered NACA 6412 airfoil on the top wing and a reflexed NACA23112 airfoil on the bottom wing are selected, which combine to induce a positive pitching moment and aid in longitudinal stability. The resulting box-wing aircraft was flight tested successfully and will serve as an ideal platform for research at CU Boulder.},
keywords = {10. Weight Engineering - Aircraft Design, 34. Advanced Design, Student Papers},
pubstate = {published},
tppubtype = {inproceedings}
}
@inproceedings{3734,
title = {3734. Dynamic Computer Simulation of Aircraft Buoyancy},
author = {Peter Stubbers},
url = {https://www.sawe.org/product/paper-3734},
year = {2020},
date = {2020-07-01},
booktitle = {2020 SAWE Tech Fair},
pages = {97},
publisher = {Society of Allied Weight Engineers, Inc.},
address = {Virtual Conference},
abstract = {IAircraft buoyancy is an important consideration in safe aircraft design. FAR 25.801 requires that in the event of emergency water landings, an aircraft must float long enough for passengers and crew to escape and board life rafts.Current methods do not include any analysis of stability, and each solution must be developed for an exclusive aircraft and configuration.To demonstrate compliance with this regulation, this study describes an improved method using a dynamic computer simulation developed with Simcenter Amesim that models the aircraft's position, orientation, weight, center of gravity, and center of buoyancy during a water landing. Internal geometry is modeled at points where water can leak into the plane as air tanks with variable flow rate orifices, allowing a simulation to show the change in buoyancy characteristics as water leaks into the aircraft and predict how much time passengers and crew will have for safe egress.This method improves upon past methods, allowing for a wider range of testing. Physical validation is beyond the scope of this study.},
keywords = {10. Weight Engineering - Aircraft Design},
pubstate = {published},
tppubtype = {inproceedings}
}
2019
@inproceedings{3714,
title = {3714. Weight and Design Data for World War II - Era United States Military Aircraft},
author = {Dudley M Cate},
url = {https://www.sawe.org/product/paper-3714},
year = {2019},
date = {2019-05-01},
booktitle = {78th Annual Conference, Norfolk, VA},
pages = {39},
publisher = {Society of Allied Weight Engineers, Inc.},
address = {Norfolk, Virginia},
abstract = {Sources of weight data for World War II-era U.S. military aircraft recently were located in the U.S. Federal Archives. The data is to the level of detail found in a short group weight statement. To the author's knowledge, the weight data has not heretofore been publicly available. It was felt to be worthwhile to electronically tabulate the data and then make it available via the SAWE.The paper begins with an introduction that identifies the groundrules and constraints associated with the material in the paper. The rest of the paper presents both weights and weight fractions for the weight empty groups and the useful load items for a wide range of aircraft. The aircraft are arranged by type (fighter, bomber, etc.), military service (Army or Navy), and, in general, chronologically by model (P-40, P-39, P-47, etc.). Also included for each aircraft are the weights of alternate fuel and payload items. For most of the aircraft, the weight empty and gross weight obtained from the archived data are validated by comparing them with weights found in open sources. Values for some of the weight-related design attributes for each aircraft are provided. Accompanying this data is a brief discussion of weight-related considerations for each aircraft.The large number of aircraft for which data are included presents a clear picture of how group and total weights and weight fractions changed with time (e.g., from the pre-war Boeing P-26 to the post-war Lockheed P-80). The data also permit comparison of the differences between, for example, radial-engined and in-line-engined fighters, between Army and Navy fighters, between Navy dive bombers and torpedo bombers, and between biplane and monoplane trainers, to mention just a few of the possibilities.},
keywords = {10. Weight Engineering - Aircraft Design, 30. Miscellaneous},
pubstate = {published},
tppubtype = {inproceedings}
}
@inproceedings{3729,
title = {3729. Application of SAWE Course 'Developing Basic Parametric Methods' to Nacelle Weight Estimating},
author = {Doug Fisher},
url = {https://www.sawe.org/product/paper-3729},
year = {2019},
date = {2019-05-01},
booktitle = {78th Annual Conference, Norfolk, VA},
pages = {17},
publisher = {Society of Allied Weight Engineers, Inc.},
address = {Norfolk, Virginia},
abstract = {This paper details how the learning contained in SAWE course 'Developing Basic Parametric Methods' was applied at Collins Aerospace for estimating nacelle weights of new commercial and business jet aircraft. Collins has decades of experience developing nacelles and a large database of historical weight data, but has not effectively leveraged that data into better weight estimating tools. Learning from this course was applied to develop improved methods of estimating the weight of nacelles for new product proposals. This has allowed us to not only provide better weight estimates but also better understand the limits of our data and estimating methods.},
keywords = {10. Weight Engineering - Aircraft Design, 11. Weight Engineering - Aircraft Estimation, 21. Weight Engineering - Statistical Studies},
pubstate = {published},
tppubtype = {inproceedings}
}
2017
@inproceedings{3690,
title = {3690. Weight Optimization of Environmental Control System of Corporate Jets},
author = {Ragaa Mitry},
url = {https://www.sawe.org/product/paper-3690},
year = {2017},
date = {2017-05-01},
booktitle = {76th Annual Conference, Montreal, Canada},
pages = {20},
publisher = {Society of Allied Weight Engineers, Inc.},
address = {Montreal, Canada},
abstract = {The environmental control system (ECS) is an essential system in the aircraft; it provides air supply, thermal, humidity, ventilation, and cabin pressurization for the crew and passengers. It is also used for engine anti-ice, main door sealing, avionic cooling, and smoke detection.ECS is sized to meet the aircraft mission. It is the highest power-consuming system on the aircraft.The basic designs of the ECS used on most aircraft, in both corporate jets and commercial airliners, are remarkably similar. In simplified terms, air is first compressed to high pressure and temperature in the engine compressors, cooled in a precooler before entering the fuselage then conditioned by an air cycle machine (ACM) where excess moisture is removed and the temperature necessary for heating or cooling the airplane is established. The conditioned air is then delivered to the cabin and cockpit through the duct distribution system to maintain a comfortable environment.To optimize the system from the weight point of view, a complete analysis of each component must be considered and evaluated. The weight of the ECS is driven by the bleed air pressure and temperature which determines the size of the precooler (Reference SAWE Paper $#$ 3648; Engine Integration to Aircraft of Corporate Jets).The thermal heating and cooling load will determine the extracted bleed airflow quantity, which in turn, will impact the ACM size and weight.Most of the ECS components are designed and provided by suppliers but the air distribution ducts are laid out by the airframers and that deserves more attention. The adverse effect of paying little attention to duct optimization is a weight penalty and cost increase. The ducts' layout, size, and shape can lead to increased cabin's noise which is usually treated by additional sound attenuation materials on the account of weight, cost, and maintainability. The duct noise can also lead to other problems such as vibration and passenger's discomfort.This paper will focus on addressing the air distribution duct design and layout as related to weight optimization.},
keywords = {10. Weight Engineering - Aircraft Design, 24. Weight Engineering - System Design},
pubstate = {published},
tppubtype = {inproceedings}
}
2016
@inproceedings{3655,
title = {3655. Weight and Structural Optimization in Aircraft Design},
author = {William Alves and Juliana Silva},
url = {https://www.sawe.org/product/paper-3655},
year = {2016},
date = {2016-05-01},
booktitle = {75th Annual Conference, Denver, Colorado},
pages = {30},
publisher = {Society of Allied Weight Engineers, Inc.},
address = {Denver, Colorado},
abstract = {Given the competitiveness of the current market, there is a growing movement in the sense of increase the efficiency of aeronautical product in an appropriate life cycle for airliners needs.
In the context of aeronautical structures, the challenge is to increase structural efficiency within the number of cycles required for life in service, meeting reliability requirements and loads, without losing sight of the dynamic performance of structural components.
This article is intended to present the main structural optimization techniques and estimating the gains made at various stages of development of the aircraft design.},
keywords = {10. Weight Engineering - Aircraft Design, 22. Weight Engineering - Structural Design, 28. Weight Reduction - Processes, 34. Advanced Design},
pubstate = {published},
tppubtype = {inproceedings}
}
In the context of aeronautical structures, the challenge is to increase structural efficiency within the number of cycles required for life in service, meeting reliability requirements and loads, without losing sight of the dynamic performance of structural components.
This article is intended to present the main structural optimization techniques and estimating the gains made at various stages of development of the aircraft design.@inproceedings{3660,
title = {3660. Development of a Conceptual Flight Vehicle Design Weight Estimation Method Library},
author = {Andy Walker},
url = {https://www.sawe.org/product/paper-3660},
year = {2016},
date = {2016-05-01},
booktitle = {75th Annual Conference, Denver, Colorado},
pages = {171},
publisher = {Society of Allied Weight Engineers, Inc.},
address = {Denver, Colorado},
abstract = {The state of the art in estimating the volumetric size and mass of flight vehicles is held today by an elite group of engineers in the Aerospace Conceptual Design Industry. This is not a skill readily accessible or taught in academia. To estimate flight vehicle mass properties, many aerospace engineering students are encouraged to read the latest design textbooks, learn how to use a few basic statistical equations, and plunge into the details of parametric mass properties analysis. Specifications for and a prototype of a standardized engineering 'tool-box' of conceptual and preliminary design weight estimation methods were developed to manage the growing and ever-changing body of weight estimation knowledge. This also bridges the gap in Mass Properties education for aerospace engineering students. The Weight Method Library will also be used as a living document for use by future aerospace students. This 'tool-box' consists of a weight estimation method bibliography containing unclassified, open -source literature for conceptual and preliminary flight vehicle design phases. Transport aircraft validation cases have been applied to each entry in the AVD Weight Method Library in order to provide a sense of context and applicability to each method. The weight methodology validation results indicate consensus and agreement of the individual methods. This generic specification of a method library will be applicable for use by other disciplines within the AVD Lab, Post- Graduate design labs, or engineering design professionals.},
note = {Mike HackneyBest Paper Award - 2016},
keywords = {10. Weight Engineering - Aircraft Design, 11. Weight Engineering - Aircraft Estimation, Mike Hackney Best Paper Award},
pubstate = {published},
tppubtype = {inproceedings}
}
@inproceedings{3662,
title = {3662. Minimizing Mass of a Spacecraft Structure},
author = {Larry Burkey and Jorge Cervantes and Lewis Gillis and Evan Graser and Megan Howard and Andrei Iskra and Taylor Maurer and Davis Peterson and Margaret Williams},
url = {https://www.sawe.org/product/paper-3662},
year = {2016},
date = {2016-05-01},
booktitle = {75th Annual Conference, Denver, Colorado},
pages = {26},
publisher = {Society of Allied Weight Engineers, Inc.},
address = {Denver, Colorado},
abstract = {The commercialization of the International Space Station (ISS) has created the opportunity for a wider variety of minisatellites to be launched to and deployed from the ISS. By utilizing ISS resupply vehicles, these spacecraft are launched to the ISS in a soft stowed configuration and undergo much lower vibration loads than in a typical launch configuration. The FeatherCraft spacecraft is designed to fully exploit this opportunity by offering a 100-kilogram spacecraft with 45 kilograms available for science payload use. This leaves only 5 kilograms for the required side panels and internal mounting surfaces that constitute the spacecraft structure. Most spacecraft structures represent approximately 20% of the total spacecraft mass, so the reduction of the structure to 5% of the total mass requires innovative mass-relieving techniques. To solve this problem, undergraduate aerospace engineering students at the University of Colorado at Boulder created FISH, the FeatherCraft Integrated Structural Housing, which achieves the required mass reduction and integrates with other spacecraft components. This unprecedented mass reduction is accomplished by utilizing composite materials, minimizing structure area and thickness, and finally using adhesives for attachments on nearly every interface. Critical components of the structure design were preliminarily verified through bending tests, Finite Element Analysis (FEA), and adhesive tests. A complete structural full-scale model will be tested under the expected vibrational loads and acceleration measurements will be taken to verify expected performance. The success of this novel design creates a new cost-effective approach to Low-Earth-orbiting missions.},
keywords = {10. Weight Engineering - Aircraft Design, Student Papers},
pubstate = {published},
tppubtype = {inproceedings}
}
2015
@inproceedings{3648,
title = {3648. Engine Integration to Aircraft of Corporate Jets},
author = {Ragaa Mitry},
url = {https://www.sawe.org/product/paper-3648},
year = {2015},
date = {2015-05-01},
booktitle = {74th Annual Conference, Alexandria, Virginia},
pages = {17},
publisher = {Society of Allied Weight Engineers, Inc.},
address = {Alexandria, Virginia},
abstract = {Engine selection is a crucial part of the preliminary design of the aircraft development to meet the aircraft mission. While significant efforts are focused on the engine characteristics, it is critical not to ignore the impact of the engine integration to the aircraft. Before making the final selection, it is important to evaluate the impact of the individual engine components on the overall aircraft weight and center of gravity (CG) beyond the engine itself.
The engine's main components; fan, compressor, combustor, turbine and nozzle; as developed by different engine manufacturers; typically share a similar architecture from engine to engine. By analyzing the impact of each component on several engine manufacturer proposals on various programs, it was observed that the compressor and the fan have significant impact on the aircraft integration. The compressor design has a large influence on the total engine performance as well as aircraft structure and systems.
This paper focuses on the engine integration to the aircraft and discusses the importance of evaluating the bleed air extracted at various stages of the compressor where manufacturer's provisions for low and high pressure bleed are commonly offered. In most cases, the manufacturers propose an engine solution based on existing design or developed from an existing design. The engine bleed air pressure and temperature impact the Environmental Control System (ECS) and the Cabin Pressurization Control System (CPCS), the higher the pressure and temperature of the extracted air, the bigger and heavier the associated precooler, ducts, and valves; which in turn increase the overall weight of the aircraft. Moreover, for aft engine mounted aircraft; the additional weight will shift the CG further aft.
Weight estimates, based on different manufacturers' design of compressor bleed air extraction stages and fan pressure, should be incorporated in the suppliers' scorecard to ensure that the weight impact driven by the engine integration on the ECS, CPCS, and the airframe structure is within the weight limit, and minimized. If the weight projection exceeds the preliminary estimated weight, it should be immediately acknowledged as a potential problem to avoid a significant weight penalty and a compromised performance later in the program.},
keywords = {10. Weight Engineering - Aircraft Design},
pubstate = {published},
tppubtype = {inproceedings}
}
The engine's main components; fan, compressor, combustor, turbine and nozzle; as developed by different engine manufacturers; typically share a similar architecture from engine to engine. By analyzing the impact of each component on several engine manufacturer proposals on various programs, it was observed that the compressor and the fan have significant impact on the aircraft integration. The compressor design has a large influence on the total engine performance as well as aircraft structure and systems.
This paper focuses on the engine integration to the aircraft and discusses the importance of evaluating the bleed air extracted at various stages of the compressor where manufacturer's provisions for low and high pressure bleed are commonly offered. In most cases, the manufacturers propose an engine solution based on existing design or developed from an existing design. The engine bleed air pressure and temperature impact the Environmental Control System (ECS) and the Cabin Pressurization Control System (CPCS), the higher the pressure and temperature of the extracted air, the bigger and heavier the associated precooler, ducts, and valves; which in turn increase the overall weight of the aircraft. Moreover, for aft engine mounted aircraft; the additional weight will shift the CG further aft.
Weight estimates, based on different manufacturers' design of compressor bleed air extraction stages and fan pressure, should be incorporated in the suppliers' scorecard to ensure that the weight impact driven by the engine integration on the ECS, CPCS, and the airframe structure is within the weight limit, and minimized. If the weight projection exceeds the preliminary estimated weight, it should be immediately acknowledged as a potential problem to avoid a significant weight penalty and a compromised performance later in the program.2014
@inproceedings{3615,
title = {3615. Application Of A Flexible Wing Modeling And Physical Mass Estimation System For Early Aircraft Design Stages},
author = {Felix Dorbath},
url = {https://www.sawe.org/product/paper-3615},
year = {2014},
date = {2014-05-01},
booktitle = {73rd Annual Conference, Long Beach, California},
pages = {23},
publisher = {Society of Allied Weight Engineers, Inc.},
address = {Long Beach, California},
abstract = {State-of-the-art models in preliminary wing design apply physics-based methods for primary structures while using empirical correlations for secondary structures. Using those methods, a detailed optimization such as e.g. rear spar positions or flap size is only possible within a limited design space. Novel structural concepts such as multi-spar flap layouts or the introduction of composite materials cannot be analyzed using statistical methods and require extended higher level structural modeling.
Therefore, a flexible wing modeling and physical mass estimation system for early aircraft design stages is developed - the WINGmass system. The core of the interdisciplinary tool chain is a central model generator that automatically generates all analysis models from the DLR aircraft data format CPACS (Common Parametric Aircraft Configuration Scheme). For the automatic model generation, a large amount of engineering rules are implemented in the model generator, to reduce the amount of required input parameters and therefore to relieve the aircraft designer. Besides the multi-model generator, the tool chain consist of a structural finite element model (incl. wing primary structures, flaps, flap tracks, ailerons, engine pylon and landing gear), a structural sizing algorithm and loads models for aerodynamic, fuel, landing gear and engine loads.
The wing mass estimation system is calibrated against real mass values of the wing primary structures and the trailing edge devices of the Airbus A320 and A340-200. The results of the calibrated tool chain are compared to the masses of the primary structures of the B747-100 and the aluminum baseline version of the MD-90-40X. The calibration factors for composite primary structures are derived from the composite version of the MD-90-40X.
Finally, the benefits of the extended physics-based modeling and the application of the WINGmass system in an interdisciplinary aircraft design environment are shown in an aircraft design study. The objective of this study is to compute the optimal wing shape in terms of mission fuel as a function of the take-off field length. Therefore, a parameter variation of the wing and flap geometry is performed, the engine scaled correspondingly and the mission fuel evaluated.},
keywords = {10. Weight Engineering - Aircraft Design, 23. Weight Engineering - Structural Estimation},
pubstate = {published},
tppubtype = {inproceedings}
}
Therefore, a flexible wing modeling and physical mass estimation system for early aircraft design stages is developed - the WINGmass system. The core of the interdisciplinary tool chain is a central model generator that automatically generates all analysis models from the DLR aircraft data format CPACS (Common Parametric Aircraft Configuration Scheme). For the automatic model generation, a large amount of engineering rules are implemented in the model generator, to reduce the amount of required input parameters and therefore to relieve the aircraft designer. Besides the multi-model generator, the tool chain consist of a structural finite element model (incl. wing primary structures, flaps, flap tracks, ailerons, engine pylon and landing gear), a structural sizing algorithm and loads models for aerodynamic, fuel, landing gear and engine loads.
The wing mass estimation system is calibrated against real mass values of the wing primary structures and the trailing edge devices of the Airbus A320 and A340-200. The results of the calibrated tool chain are compared to the masses of the primary structures of the B747-100 and the aluminum baseline version of the MD-90-40X. The calibration factors for composite primary structures are derived from the composite version of the MD-90-40X.
Finally, the benefits of the extended physics-based modeling and the application of the WINGmass system in an interdisciplinary aircraft design environment are shown in an aircraft design study. The objective of this study is to compute the optimal wing shape in terms of mission fuel as a function of the take-off field length. Therefore, a parameter variation of the wing and flap geometry is performed, the engine scaled correspondingly and the mission fuel evaluated.2013
@inproceedings{3594,
title = {3594. Refined Preliminary Weight Estimation Method for Multidisciplinary Shape Optimization of Lifting Surfaces},
author = {Ali Elham and Michel J. L. Tooren},
url = {https://www.sawe.org/product/paper-3594},
year = {2013},
date = {2013-05-01},
booktitle = {72nd Annual Conference, St. Louis, Missouri},
pages = {27},
publisher = {Society of Allied Weight Engineers, Inc.},
address = {Saint Louis, Missouri},
abstract = {A strategic focus area for NASA is to pursue the development of technologies which support exploration in space beyond the current inhabited region of low earth orbit. An unresolved issue for crewed deep space exploration involves limiting crew radiation exposure to below acceptable levels, considering both solar particle events and galactic cosmic ray contributions to dosage. Galactic cosmic ray mitigation is not addressed in this paper, but by addressing credible, easily implemented, and mass efficient solutions for the possibility of solar particle events, additional margin is provided that can be used for cosmic ray dose accumulation. As a result, NASA's Advanced Engineering Systems project office initiated this Radiation Storm Shelter design activity. This paper reports on the first year results of an expected 3 year Storm Shelter study effort which will mature concepts and operational scenarios that protect exploration astronauts from solar particle radiation events. Large trade space definition, candidate concept ranking, and a planned demonstration comprised the majority of FY12 activities. A system key performance parameter is minimization of the required increase in mass needed to provide a safe environment. Total system mass along with operational assessments and other defined protection system metrics provide the guiding metrics to proceed with concept developments. After a downselect to four primary methods, the concepts were analyzed for dosage severity and the amount of shielding mass necessary to bring dosage to acceptable values. Besides analytical assessments, subscale models of several concepts and one full scale concept demonstrator were created. FY12 work terminated with a plan to demonstrate test articles of two selected approaches. The process of arriving at these selections and their current envisioned implementation are presented in this paper.},
keywords = {10. Weight Engineering - Aircraft Design},
pubstate = {published},
tppubtype = {inproceedings}
}
@inproceedings{3606,
title = {3606. Design Considerations Of Flight Control Systems In High Performance General Aviation Aircraft},
author = {Darrin McCloud},
url = {https://www.sawe.org/product/paper-3606},
year = {2013},
date = {2013-05-01},
booktitle = {72nd Annual Conference, St. Louis, Missouri},
pages = {20},
publisher = {Society of Allied Weight Engineers, Inc.},
address = {Saint Louis, Missouri},
abstract = {The current trend for new business jet designs is for larger, faster aircraft at a minimum price point. Almost all of the slower entry-level planes use manual flight control systems while all of the large business jets are required to use powered flight control systems. What happens in the gray area in- between, when a manual flight control system is preferred but the size and speed of the aircraft make it difficult to design? Many design choices will impact the size, weight and effectiveness of the flight control system and the difference in these choices will determine whether the overall aircraft design is a success. Incorrect choices can lead to costly redesign, poor performance or flutter concerns. This paper will concentrate on design issues with traditionally controlled, manually powered jet aircraft and several design factors to be aware of during the early phase of aircraft development.},
keywords = {10. Weight Engineering - Aircraft Design},
pubstate = {published},
tppubtype = {inproceedings}
}
2012
@inproceedings{3547,
title = {3547. Implementation of a Tool Chain for Extended Physics-Based Wing Mass Estimation in Early Design Stages},
author = {Felix Dorbath and Björn Nagel and Volker Gollnick},
url = {https://www.sawe.org/product/paper-3547},
year = {2012},
date = {2012-05-01},
booktitle = {71st Annual Conference, Bad Gögging, Germany},
pages = {21},
publisher = {Society of Allied Weight Engineers, Inc.},
address = {Bad Gögging, Germany},
abstract = {The state-of-the-art methods in preliminary wing design are using models employing physics-based methods for primary structures while using empirical correlations for secondary structures. Using those methods, detailed optimization as e.g. rear spar positions or flap size is only possible within a limited design space. Novel structural concepts such as multi-spar flap layouts or the introduction of composite materials cannot be analyzed using statistical methods and require extended higher level structural modeling. Therefore an interdisciplinary tool chain is developed for extended physics-based wing mass estimation. The tool chain consists of the following components: one central model generator, a structural finite element model, a structural sizing algorithm and loads models for aerodynamic, fuel, landing gear and engine loads. The structural finite element wing model consists of the following main parts: wing box, fixed trailing edge devices, movable trailing edge devices, spoilers, landing gears and engine pylons. The model generator is able to create several different kinds of track kinematics, covering most of the track types used in state-of-the-art aircrafts. To make the complexity of the model generation process feasible for one aircraft designer, a knowledge based approach is chosen. Therefore the central model generator requires a minimum set of easy-to- understand input parameters. This enables the aircraft designer to focus on the design and not on calculating input parameters. To include the tool chain in a wider multidisciplinary aircraft design environment, the aircraft parameterization CPACS (Common Parametric Aircraft Configuration Scheme) is used as central data model for input and output. The developed tool chain is implemented as flexible as possible to enable the designer to analyze also novel structural concepts or wing configurations. On wing configurational level, the tool chain can handle most types of different wing concepts, such as e.g. blended wing bodies, strut-braced wings and box wings. On the structural concepts side, the tool chain is able to handle various different rib and spar layouts and different materials (incl. composites).},
note = {Mike Hackney Best Paper Award},
keywords = {10. Weight Engineering - Aircraft Design, 23. Weight Engineering - Structural Estimation, Mike Hackney Best Paper Award},
pubstate = {published},
tppubtype = {inproceedings}
}
@inproceedings{3571,
title = {3571. An Advanced Quasi-Analytical Weight Estimation Method for Airplane Lifting Surfaces},
author = {Ali Elham and Gianfranco La Rocca and Michel J. L. Tooren},
url = {https://www.sawe.org/product/paper-3571},
year = {2012},
date = {2012-05-01},
booktitle = {71st Annual Conference, Bad Gögging, Germany},
pages = {19},
publisher = {Society of Allied Weight Engineers, Inc.},
address = {Bad Gögging, Germany},
abstract = {This paper describes a novel weight prediction method for aircraft lifting surfaces, which is able to combine the typical accuracy of finite element (FE) based weight estimation methods, with the computational speed of the classical semi empirical (class II) methods used in conceptual design.
In the proposed method the use of semi empirical equations is limited to the estimation of the secondary weights of wing and tailplanes. The weight prediction of the primary structure is achieved by means of an advanced analytical method, which makes use of the actual geometry of aerodynamic surfaces and structural layout, and the computed lift forces distribution. In particular, a set of mathematical equations has been derived to relate the required structural properties of the wing box to the specific shape of the used airfoils. These equations allow modelling the skin, the spar caps and the stringers of the upper and lower side of a given wing box into two equivalent flat panels, and then calculate their 'effective distance'. This distance is indeed the factor that allows accounting for the effect of the given airfoil shape on the stress distribution in the panels, and enable a more accurate panel weight estimation than other methods proposed in literature.
A realistic estimation of the spanwise lift distribution is another key factor to achieve accurate weight predictions. To this purpose, a commercial Vortex Lattice Method tool has been employed top derive the aerodynamic loads on the given lifting surface. The load cases are defined according to airworthiness regulations. The load relief effects provided by fuel and engine installation, as well as by the weight of the wing structure, are taken into account.
The total weight of the given lifting surface is computed by adding the analytically calculated weight of upper and lower panels, spars and ribs, to the weight of the secondary structure (e.g., movables and fixed leading and trailing edge) and to the so called non-optimum weight group, which accounts for joints, cut-outs, attachments, etc. The last two contributions are estimated by means of semi empirical relations.
The proposed lifting surface weight prediction method has been validated using data of various airplanes of different size, category and manufacturer. The computational time is dramatically lower than any finite element based sizing tool, while the achieved level of accuracy is comparable or even higher. Each weight prediction takes about 10 second on a standard PC. The average error on lifting surface total weight is less than 2%. Besides, the achieved combination of speed, accuracy and high level of design sensitivity (designer can assess the effect on weight of such parameters as airfoil shape, number, position and orientation of structural items, etc.) make the proposed tool suitable for multidisciplinary design optimization studies.},
keywords = {10. Weight Engineering - Aircraft Design},
pubstate = {published},
tppubtype = {inproceedings}
}
In the proposed method the use of semi empirical equations is limited to the estimation of the secondary weights of wing and tailplanes. The weight prediction of the primary structure is achieved by means of an advanced analytical method, which makes use of the actual geometry of aerodynamic surfaces and structural layout, and the computed lift forces distribution. In particular, a set of mathematical equations has been derived to relate the required structural properties of the wing box to the specific shape of the used airfoils. These equations allow modelling the skin, the spar caps and the stringers of the upper and lower side of a given wing box into two equivalent flat panels, and then calculate their 'effective distance'. This distance is indeed the factor that allows accounting for the effect of the given airfoil shape on the stress distribution in the panels, and enable a more accurate panel weight estimation than other methods proposed in literature.
A realistic estimation of the spanwise lift distribution is another key factor to achieve accurate weight predictions. To this purpose, a commercial Vortex Lattice Method tool has been employed top derive the aerodynamic loads on the given lifting surface. The load cases are defined according to airworthiness regulations. The load relief effects provided by fuel and engine installation, as well as by the weight of the wing structure, are taken into account.
The total weight of the given lifting surface is computed by adding the analytically calculated weight of upper and lower panels, spars and ribs, to the weight of the secondary structure (e.g., movables and fixed leading and trailing edge) and to the so called non-optimum weight group, which accounts for joints, cut-outs, attachments, etc. The last two contributions are estimated by means of semi empirical relations.
The proposed lifting surface weight prediction method has been validated using data of various airplanes of different size, category and manufacturer. The computational time is dramatically lower than any finite element based sizing tool, while the achieved level of accuracy is comparable or even higher. Each weight prediction takes about 10 second on a standard PC. The average error on lifting surface total weight is less than 2%. Besides, the achieved combination of speed, accuracy and high level of design sensitivity (designer can assess the effect on weight of such parameters as airfoil shape, number, position and orientation of structural items, etc.) make the proposed tool suitable for multidisciplinary design optimization studies.2010
@inproceedings{3509,
title = {3509. Airframe Wingbox Preliminary Design and Weight Prediction},
author = {JAMES AINSWORTH and CRAIG COLLIER and PHIL YARRINGTON and RYAN LUCKING and JAMES LOCKE},
url = {https://www.sawe.org/product/paper-3509},
year = {2010},
date = {2010-05-01},
booktitle = {69th Annual Conference, Virginia Beach, Virginia},
pages = {41},
publisher = {Society of Allied Weight Engineers, Inc.},
address = {Virginia Beach, Virginia},
abstract = {Currently Collier Research is evaluating the performance of many panel
concepts for highly loaded, commercial transport wingbox structures.
Software development is taking place as well as many new commercial
contracts to further the effort. Simultaneously the HyperSizer commercial
software is being used world-wide on many commercial aircraft for the
analysis and design sizing of composite and metallic aircraft structures. This
paper focuses on trade studies performed on an aircraft wingbox structure.
The wingbox is modeled after a commercial transport jet. The loads on the
upper and lower wing skin surface are axially compression paired with high
shear loading caused by wing twist. Weight trends are quantified considering
all possible design possibilities in order to determine the most structurally
efficient combination of composite layups and panel cross section dimensions
to achieve the lightest weight. Included are results obtained with HyperSizer
for Metallic Integral Blade and Bonded Zee Stiffened panel concepts as well
as Composite Hat and Tee Stiffened panel concepts. The HyperSizer
optimum designs have scored based on the weight maturity level (WML) of
the panel design. The study shows the composite hat stiffened panel is the
lightest concept for a wingbox structure and is 30% lighter than the lightest
metallic design.},
keywords = {10. Weight Engineering - Aircraft Design},
pubstate = {published},
tppubtype = {inproceedings}
}
concepts for highly loaded, commercial transport wingbox structures.
Software development is taking place as well as many new commercial
contracts to further the effort. Simultaneously the HyperSizer commercial
software is being used world-wide on many commercial aircraft for the
analysis and design sizing of composite and metallic aircraft structures. This
paper focuses on trade studies performed on an aircraft wingbox structure.
The wingbox is modeled after a commercial transport jet. The loads on the
upper and lower wing skin surface are axially compression paired with high
shear loading caused by wing twist. Weight trends are quantified considering
all possible design possibilities in order to determine the most structurally
efficient combination of composite layups and panel cross section dimensions
to achieve the lightest weight. Included are results obtained with HyperSizer
for Metallic Integral Blade and Bonded Zee Stiffened panel concepts as well
as Composite Hat and Tee Stiffened panel concepts. The HyperSizer
optimum designs have scored based on the weight maturity level (WML) of
the panel design. The study shows the composite hat stiffened panel is the
lightest concept for a wingbox structure and is 30% lighter than the lightest
metallic design.2009
@inproceedings{3467,
title = {3467. Weight Analytics},
author = {Chuck Higgins},
url = {https://www.sawe.org/product/paper-3467},
year = {2009},
date = {2009-05-01},
booktitle = {68th Annual Conference, Wichita, Kansas},
pages = {13},
address = {Wichita, Kansas},
abstract = {Weight Analytics addresses the gathering, analyzing, reporting and sharing of critical weight data and opening new horizons for the use of this knowledge within the design process. In this paper we will show the use of a cubical data base, allowing the user to look at an infinite number of dimensions of data quickly, easily and intuitively. Automation of the collection, storage, analysis and reporting on this disparate data has until now been challenging at the least. With the flexibility of the Rubix Cube, data is quickly and easily sliced and diced along any number of
relationships thus 'elevating data to knowledge.'},
keywords = {10. Weight Engineering - Aircraft Design, 18. Weight Engineering - Spacecraft Design, 22. Weight Engineering - Structural Design},
pubstate = {published},
tppubtype = {inproceedings}
}
relationships thus 'elevating data to knowledge.'@inproceedings{3474,
title = {3474. U.S. Fighter Aircraft Design, Weight And Performance Trends},
author = {Dudley M Cate},
url = {https://www.sawe.org/product/paper-3474},
year = {2009},
date = {2009-05-01},
booktitle = {68th Annual Conference, Wichita, Kansas},
pages = {95},
address = {Wichita, Kansas},
abstract = {Weight engineers struggle with aircraft weight because it is so critically important to aircraft performance. Nowhere is this truer than for fighter aircraft. The U.S. has been operating fighters since 1917 and designing them since almost that long ago. This paper presents three sets of information for U.S. fighters: the first set consists of quantitative trends versus time for some top-level design, weight and performance parameters for U.S. fighters. The parameters addressed include ones commonly cited in aircraft histories (max speed, combat ceiling, initial climb rate) plus others such as weight empty fraction, fuel fraction, wing loading and power- and thrust-to-weight ratios. The second set of information is the results of searches for correlations between design parameters (e.g., wing loading) and performance parameters (e.g., climb rate). The third set consists of brief descriptions and assessments of the requirements, technologies, design, performance and
operational suitability of each of the fifty-odd aircraft in the database.},
keywords = {10. Weight Engineering - Aircraft Design, 21. Weight Engineering - Statistical Studies},
pubstate = {published},
tppubtype = {inproceedings}
}
operational suitability of each of the fifty-odd aircraft in the database.