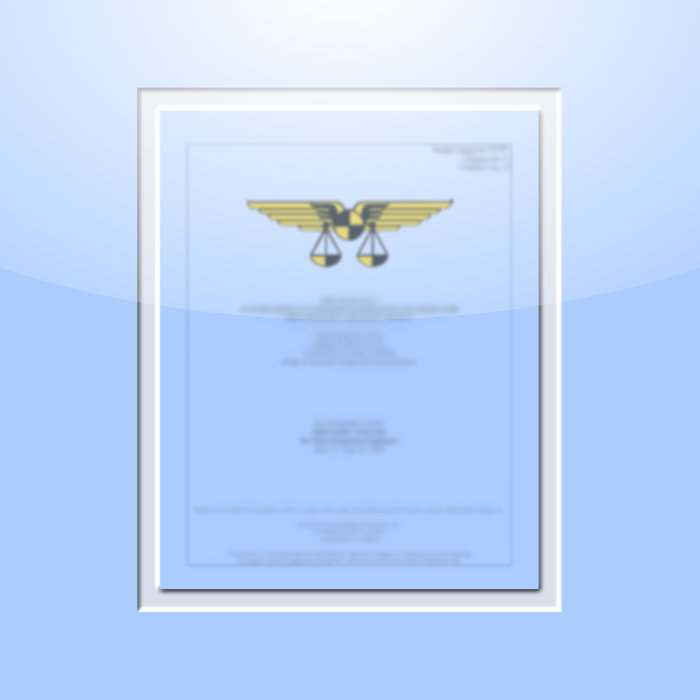
3664. Advanced Lightweight 3D Structures (AL3DS) Manufacturing Design Concept
$20.00
SAWE Members get a $200 store credit each year.*
*Store credit coupon available at checkout, click the button in your shopping cart to apply the coupon.
Not applicable to SAWE textbooks and current conference technical papers.
Paper
Abstract
Weight is one of the factors with the greatest influence on aircraft performance. The Advanced Lightweight 3D Structures design concept proposes to reduce structural frame we ight through the use of novel manufacturing techniques. The primary objective of this paper is to analytically demonstrate the feasibility of using a ‘node and rod’ design for an aircraft wing box section. Preliminary analysis shows that weight reduction is possible by employing carbon-fiber rods connected with aluminum 3D printed ‘nodes’ in place of traditionally manufactured ribs and spars. The ‘nodes’ can be specifically designed in complex shapes while still allowing for mass – production by using CAD and 3D printing technology. This flexibility in rapid-prototyping allows the engineer to vary the geometry of connectivity in order to optimize for a specific design. The ‘node and rod’ technique would enable the design and development of increased complexity structural designs in a simple and repeatable way. Analytical software is developed to model the aerodynamic loads acting on a wing box, as well as to analyze the structural properties of a 3D wing box structure. The computational tools are validated using commercial finite element modeling programs such as ANSYS and SOLIDWORKS. These models are compared for different flight loading conditions imposed by varying angle of attack and flight Mach number. Furthermore, the models are compared for different materials,such as aluminum vs carbon-fiber rods.If successful, the node and rod concept can be implemented across multiple engineering disciplines to reduce weight in a wide range of structural design paradigms. The concept would fit well within existing engineering infrastructure as well: the structures team may design the nodes based on the desired geometry and loading cases, while the manufacturing team is able to rapidly prototype and iterate to a final node design, and of course the rods may be sub contracted out. The applications for lightweight, strong structures are endless – cars, robots, architecture, and so on. However, any possible weight reduction would drastically improve aircraft performance in fuel efficiency, range, cruise speed, and available payload. The Advanced Lightweight 3D Structures design concept would allow for a new and improved method for designing and building aircraft.