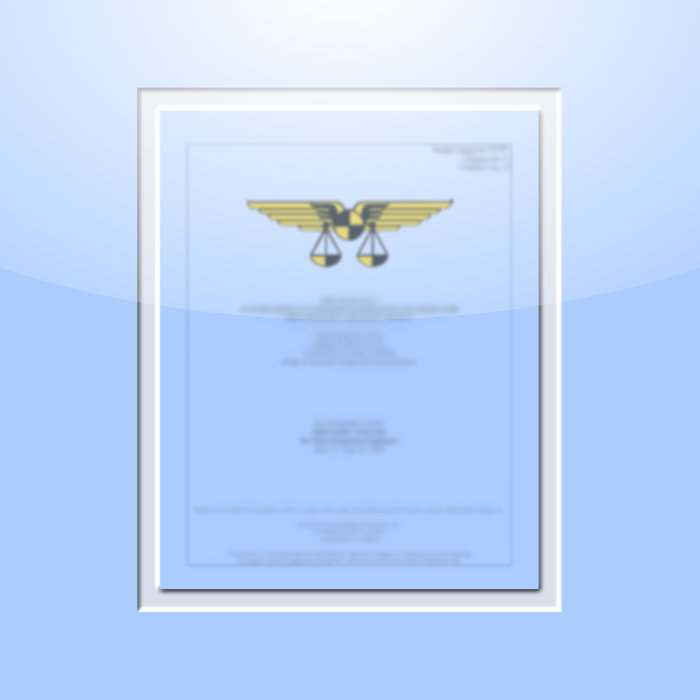
3571. An Advanced Quasi-Analytical Weight Estimation Method for Airplane Lifting Surfaces
$20.00
SAWE Members get a $200 store credit each year.*
*Store credit coupon available at checkout, click the button in your shopping cart to apply the coupon.
Not applicable to SAWE textbooks and current conference technical papers.
Paper
Abstract
This paper describes a novel weight prediction method for aircraft lifting surfaces, which is able to combine the typical accuracy of finite element (FE) based weight estimation methods, with the computational speed of the classical semi empirical (class II) methods used in conceptual design.
In the proposed method the use of semi empirical equations is limited to the estimation of the secondary weights of wing and tailplanes. The weight prediction of the primary structure is achieved by means of an advanced analytical method, which makes use of the actual geometry of aerodynamic surfaces and structural layout, and the computed lift forces distribution. In particular, a set of mathematical equations has been derived to relate the required structural properties of the wing box to the specific shape of the used airfoils. These equations allow modelling the skin, the spar caps and the stringers of the upper and lower side of a given wing box into two equivalent flat panels, and then calculate their ‘effective distance’. This distance is indeed the factor that allows accounting for the effect of the given airfoil shape on the stress distribution in the panels, and enable a more accurate panel weight estimation than other methods proposed in literature.
A realistic estimation of the spanwise lift distribution is another key factor to achieve accurate weight predictions. To this purpose, a commercial Vortex Lattice Method tool has been employed top derive the aerodynamic loads on the given lifting surface. The load cases are defined according to airworthiness regulations. The load relief effects provided by fuel and engine installation, as well as by the weight of the wing structure, are taken into account.
The total weight of the given lifting surface is computed by adding the analytically calculated weight of upper and lower panels, spars and ribs, to the weight of the secondary structure (e.g., movables and fixed leading and trailing edge) and to the so called non-optimum weight group, which accounts for joints, cut-outs, attachments, etc. The last two contributions are estimated by means of semi empirical relations.
The proposed lifting surface weight prediction method has been validated using data of various airplanes of different size, category and manufacturer. The computational time is dramatically lower than any finite element based sizing tool, while the achieved level of accuracy is comparable or even higher. Each weight prediction takes about 10 second on a standard PC. The average error on lifting surface total weight is less than 2%. Besides, the achieved combination of speed, accuracy and high level of design sensitivity (designer can assess the effect on weight of such parameters as airfoil shape, number, position and orientation of structural items, etc.) make the proposed tool suitable for multidisciplinary design optimization studies.