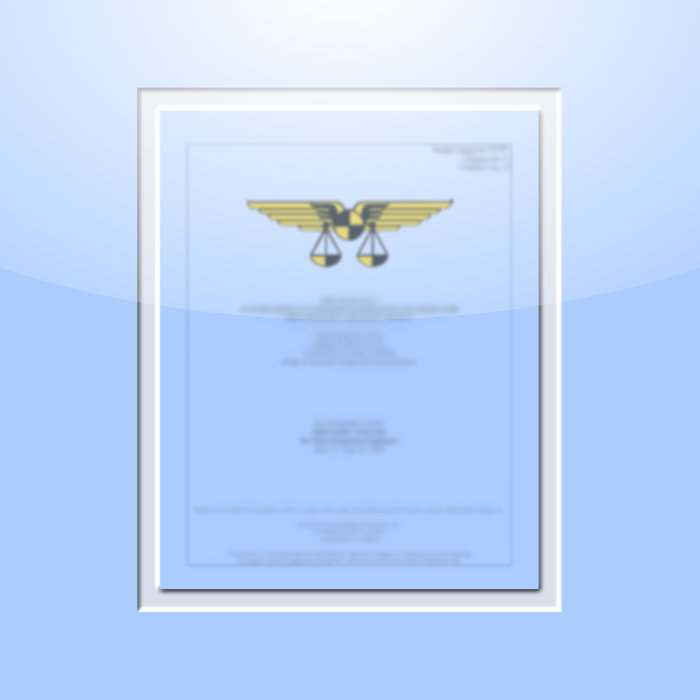
3411. Design Optimization in Aircraft Component Pre-Design
$20.00
SAWE Members get a $200 store credit each year.*
*Store credit coupon available at checkout, click the button in your shopping cart to apply the coupon.
Not applicable to SAWE textbooks and current conference technical papers.
Paper
Abstract
An efficient use of CAE applications in modern aircraft development can lead to shorter development cycles and reduced development costs. This is a sophisticated task for a complex aircraft component with multidisciplinary requirements. In order to get the best possible design, extensive parameter studies are often carried out and the results compared; they may require substantial computations. This situation can often be found in other technical areas and results in the development of a software generation called ?PIDO? (Process Integration and Design Optimization). The traditional CAE development process uses trial and error analysis to find a design that satisfies all of the given requirements. Under normal circumstances, the weight engineer defines the parameters for computing the product attributes. The emerging class of PIDO works, in the opposite direction, by determining the optimal design parameters necessary to meet the target functional performance attributes. This paper is about the primary structure optimization of an aircraft vertical tail. The focus is on the bending-torsion-box variation to find a lightweight solution using a simplified stress model.