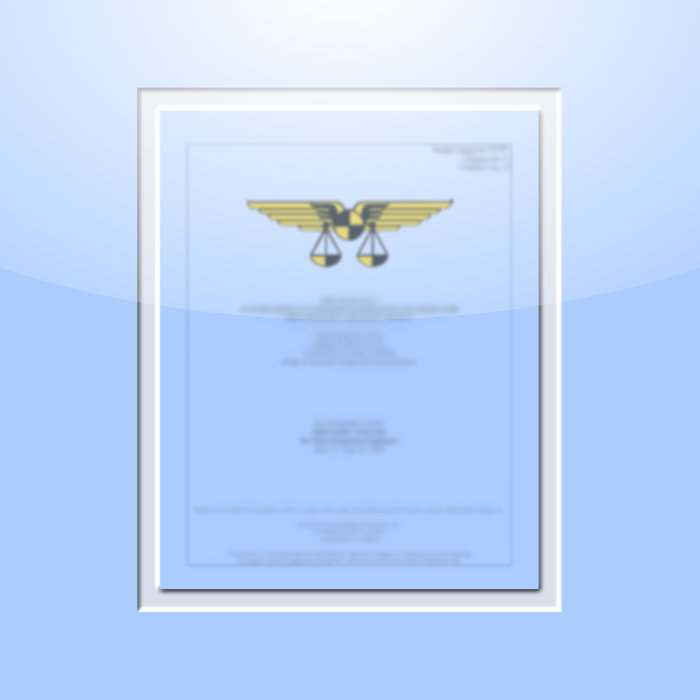
3405. A Methodology of Weight Prediction for Joints in Aircraft Design
$20.00
SAWE Members get a $200 store credit each year.*
*Store credit coupon available at checkout, click the button in your shopping cart to apply the coupon.
Not applicable to SAWE textbooks and current conference technical papers.
Paper
Abstract
For lightweight construction purposes the ideal structure of an aircraft would be a single unit. Due to various constraints (manufacturing, functionality, profitability, etc.), it is composed of thousands of parts via joints. The additional weight of joints is a major part of the non-optimum weight, which implies effects resulting from the practical design. Since it can reach values of 20 to 80 per cent of the assembly component weight, the importance of developing a methodology of weight prediction for joints is obvious. Research activities are focused on two main issues. The first one concentrates on the generalization of existing design rules from literature. These common rules are mostly given for plain geometries and simple load cases and must be adapted to the much more complex joints in aircraft design. The outcome of this step is a determination of the minimum possible weight for a joining technique (e.g., riveting, welding, adhesive bonding) and is presented for a typical longitudinal fuselage lap joint. The second focus is on the numerous constraints that often make aircraft designers deviate from the minimum possible weight solution. These constraints are due to technical, regulative, or other considerations. They may include such different issues as accessibility of the interfaces, availability of production resources, company experience, manufacturing costs, maintenance requirements, etc. To investigate the influence in a structured manner, a method called ?Analytic Hierarchy Process? (AHP) has been applied. The result of this method is a prediction of the joining technology a designer will probably choose for a given problem. The approach of the AHP is demonstrated for the example of a lap joint using joining technologies like riveting, welding, and adhesive bonding. The alternatives are assessed regarding weight, assembling, maintenance, and costs at top level. The result of both focuses is combined whereas the weight information for the AHP is supplied by the analytic or rather semi-empiric approach of the weight calculation of the different joining technologies.