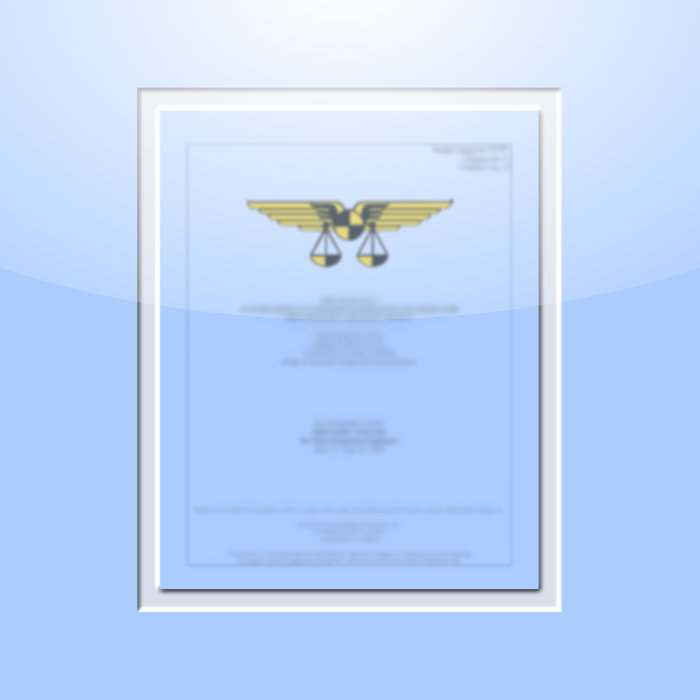
3286. Developing Metal Matrix Composites For Ordnance and Aerospace Applications
$20.00
SAWE Members get a $200 store credit each year.*
*Store credit coupon available at checkout, click the button in your shopping cart to apply the coupon.
Not applicable to SAWE textbooks and current conference technical papers.
Paper
Abstract
Continuous-fiber reinforced metal matrix composites (MMCs) present significant improvements in specific strength and specific stiffness over conventional monolithic alloys. MMC materials offer tremendous potential for U.S. Army applications such as lightweight projectiles and gun systems. For advanced artillery projectiles, MMCs can be used to manufacture shell bodies 50% lighter than steel shells with more payload carrying capacity. MMCs could also play an important part in the development of lightweight jackets for steel-lined gun barrels, which are longer and stiffer, with higher-pressure capability at equivalent weights compared to current designs. In addition, NASA has repeatedly identified metal matrix composite development and lightweight cryogenic compatible materials as high priorities for supporting advanced space transportation requirements. MMC technology could have direct application to cryogenic-compatible propulsion system feed lines and ducts, and could be expanded with further investment to be applied to cryogenic tanks and primary structure as well. Unfortunately, manufacturing difficulties have limited the number of applications and prevented these materials from fully penetrating the marketplace. To address these technology needs and manufacturing shortfalls, Touchstone is developing a new material system and manufacturing method in which the advantages of MMCs are married with the manufacturing techniques of PMCs. This technology demonstrates that MMC structures can be produced in an analogous manner to PMCs utilizing traditional tape/fiber placement processing techniques. Additionally, the process represents both on-the-fly and out-of-autoclave composites technology with potentially large cost savings. This paper describes Touchstone?s current efforts to advance this unique technology.