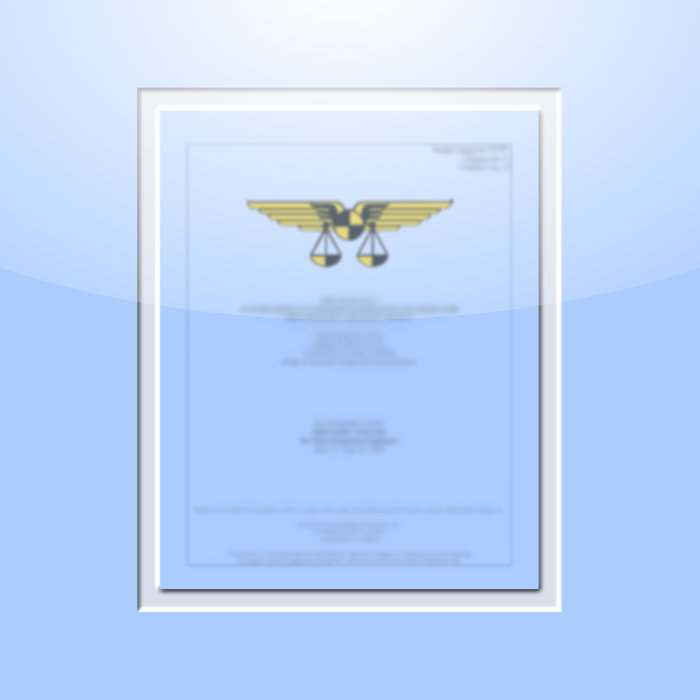
3003. Evaluation of Equivalent Laminated Plate Solution (ELAPS) in HSCT Sizing
$20.00
SAWE Members get a $200 store credit each year.*
*Store credit coupon available at checkout, click the button in your shopping cart to apply the coupon.
Not applicable to SAWE textbooks and current conference technical papers.
Paper
Abstract
The motivation for evaluating ELAPS was to determine its suitability as a quick and reliable tool for conceptual and early preliminary design. The expectation was that ELAPS would predict a better structural weight than parametric weight equations since its weight is determined from structural optimization with both strength and flutter constraints. An additional motivation was to eventually utilize the functional representation of ELAPS in shape optimization. Results from the current version of ELAPS were compared against Elfini. The comparisons included static displacements and stresses, natural vibration frequencies and mode shapes, strength optimization, flutter optimization, and simultaneous strength and flutter optimization. Elfini is a mature, well-understood, FEM tool with many years of development effort behind it. Although previous studies have proven the merits of ELAPS for preliminary structural analysis, little research has been accomplished to formally test an ELAPS based flutter optimization. Optimization with strength constraints worked well and provided final weights comparable to Elfini. But the flutter optimization, and simultaneous strength and flutter optimizations converged to significantly different weights. This could partly be attributable to analytical and model differences. There were differences of up to 10% in a few of the first 10 modal frequencies, primarily due to disagreement in stiffness for the HSCT uniform gauge wing. Thus, for ELAPS to provide an attractive option for structural sizing and shape optimization, there needs to be further investments in (1) improving ELAPS? static stiffness correlation with FEM?s, (2) developing an automated parametric input/output graphical interface for ELAPS, (3) improving the robustness of the ELAPS structural representation, (4) improving the computational efficiency of ELAPS and its associated optimization system, and (5) developing ELAPS flutter and shape optimization capabilities In some sense, it is unfair to compare ELAPS with mature FEM codes with years of development effort. However, unless significant improvement to ELAPS is made soon, it will be difficult for ELAPS to compete with the rapid automation of FEM codes for simplified analysis and design.