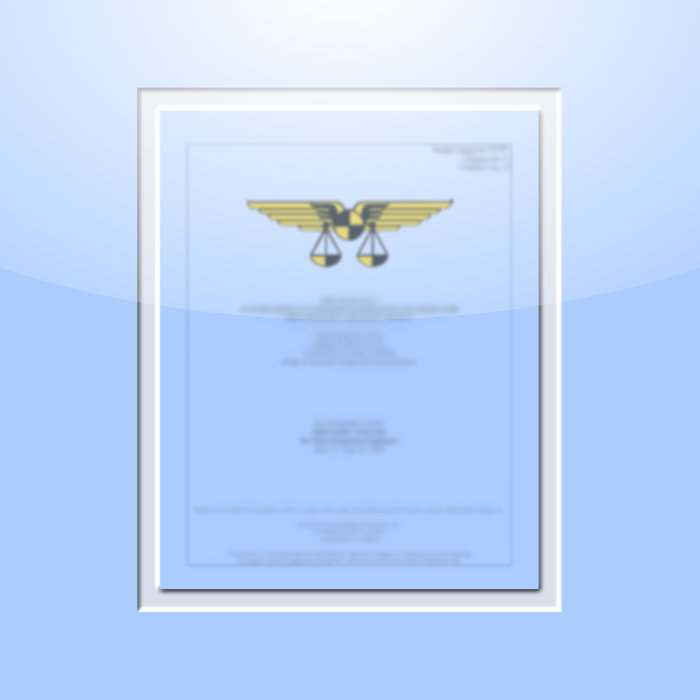
2333. Using a Centrifuge to Create a Precise Linear Acceleration
$20.00
SAWE Members get a $200 store credit each year.*
*Store credit coupon available at checkout, click the button in your shopping cart to apply the coupon.
Not applicable to SAWE textbooks and current conference technical papers.
Paper
Abstract
When a satellite is launched, it experiences a linear acceleration during liftoff and separation of the stages of the rocket. Later it encounters acceleration forces in other directions as thrusters maneuver it into its final position in orbit. The lightweight fragile structure of the satellite must be able to withstand the high G loading during takeoff, while the inertial guidance system must be able to function properly under a wide range of acceleration forces. This paper describes the creation of a centrifuge to simulate the full range of acceleration encountered by the satellite. The rotational speed control of the centrifuge must approach the state of the art in order to provide precisely known values of linear acceleration. This speed must be programmable as a function of time to duplicate the acceleration profile during launch. Slip rings must be provided to power the device being tested during rotation and to monitor the electrical signals relating to the performance of the device. Balance is critical to prevent damage to the payload and to ensure that vibratory forces won’t be introduced during centrifuge tests. This paper points out some effects relating to unbalance which have been overlooked in the past by the majority of those doing centrifuge testing. And finally, a centrifuge creates a truly enormous amount of stored energy. A number of safety features must be incorporated into the device to prevent it from destroying the building and its occupants in the event of catastrophic failure. This paper discusses concepts developed at Space Electronics which provide a controlled deceleration in the event of various modes of failure.