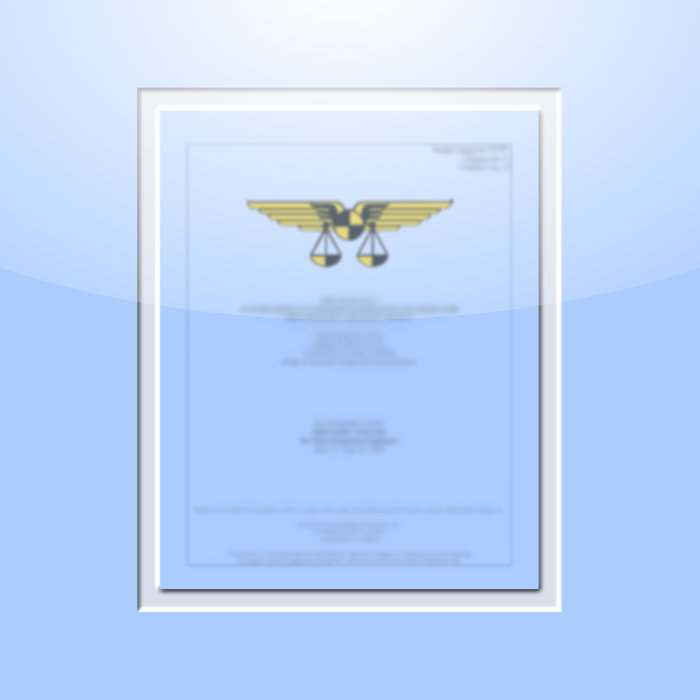
2121. Weight Reduction and Lower Cost Through Innovative Design
$20.00
SAWE Members get a $200 store credit each year.*
*Store credit coupon available at checkout, click the button in your shopping cart to apply the coupon.
Not applicable to SAWE textbooks and current conference technical papers.
Paper
Abstract
This paper describes how Tolo Incorporated reduced the weight, improved the performance, and lowered the cost of extended range fuel tanks for a military fighter-bomber aircraft. This combination of improvements is unusual in modem aerospace hardware. It will be shown that weight savings, reduced cost, and improved performance can be achieved using conventional materials and processing. The key is the use of innovative design and manufacturing methods in a concurrent engineering environment. Tolo’s task was to design, fabricate, and test new fuel tanks to replace the original tanks supplied by the aircraft manufacturer. The original aluminum tanks are complex riveted designs and have developed leaks which are very difficult and expensive to repair. The aircraft operator had requested a new tank design of composite construction to replace the original tanks. Tolo’s experience in designing and building both composite and metal tanks indicated that the best solution would be a metal tank. This paper describes the process by which a welded aluminum fuel tank design was developed. The welded design is shown to be superior to both a composite design and the original riveted design. The use of low-cost 6061 aluminum alloy and proven fabrication methods significantly reduced material and processing costs. Structural components were designed for ease of manufacture. This minimized manufacturing steps and reduced or eliminated tooling requirements. The fuel tanks were designed for ease of assembly to minimize labor and tooling costs. Design simplification also improved repairability, increased service life, reduced weight, and improved access to tank internal hardware such as pumps, level sensors, and wiring. Development and testing of an innovative weld assembly technique was critical to achieving a low-cost, reduced-weight design. Welded assembly reduced the number of fasteners from over 7000 in the original tank structure to only 16 in the Tolo design. Polysulfide tank sealant was eliminated completely.