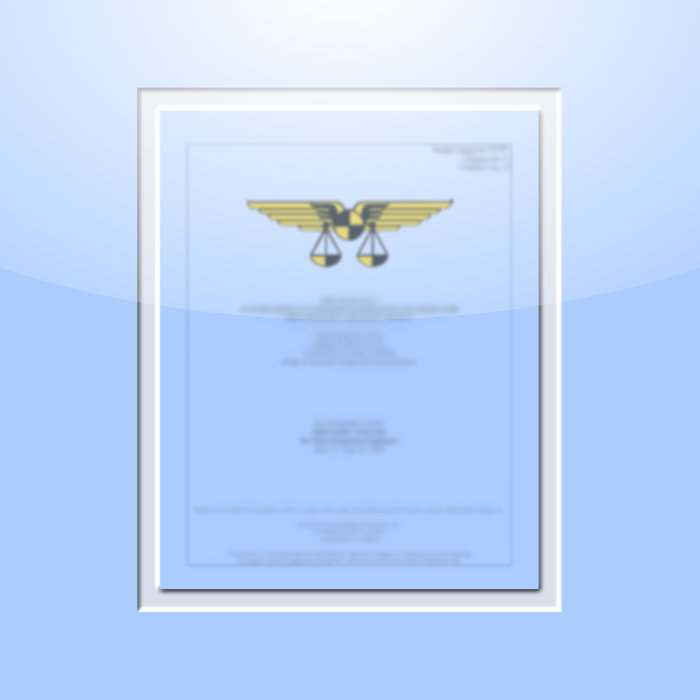
1579. The Weight Reduction Potential of Advanced Composites
$20.00
SAWE Members get a $200 store credit each year.*
*Store credit coupon available at checkout, click the button in your shopping cart to apply the coupon.
Not applicable to SAWE textbooks and current conference technical papers.
Paper
Abstract
This paper presents analytical and empirical analyses of the weight reduction potential of advanced composite materials as applied to aircraft structures. Aerospace use of advanced composite materials has accelerated rapidly for more than a decade. Initially, advanced composites were mostly used in combat aircraft where a large cost penalty for the sake of high performance could be justified. Later, with the declining cost of some advanced composites, their use in commercial aircraft was justified on the basis of fuel savings. In some cases today, the composite component is not only lighter but cheaper than its metallic equivalent. Throughout, the growth factor effect of meeting a specific performance level with a smaller, lighter vehicle by virtue of advanced composites has assured them a promising future in new military and commercial systems. In many reports on advanced composites, data like those presented in Figure 1 (Reference 1) show advanced composites are many times stronger or possess a much higher modulus than conventional materials. For example, some carbon fibers are pound for pound 7 times more rigid than aluminum, and Kevlar fibers are pound for pound 10 times as strong as aluminum. But how large a weight reduction do these advantages translate into after we’ve added a matrix to the fibers, formed the composite into a tape or cloth, laid it up, and applied appropriate aircraft design criteria such as damage tolerance and delamination considerations? This paper explores the weight reduction potential of carbon/epoxy (C/E) tape and cloth, Kevlar/epoxy (K/E) cloth, and boron/epoxy (B/E) tape considering a variety of ply arrangements. The advanced composites are compared to aluminum and E-glass/epoxy (E-G/E) under compression and shear loading. Tension-loaded structural weights are compared assuming damage tolerance criteria. In some instances rigidity is critical for deflection and/or flutter considerations, and this case is also analyzed. Aircraft structural components that were initially constructed of conventional materials have been redesigned using advanced composites, thus providing empirical weight reduction data. Forty of these cases were investigated. The empirical weight reduction data were compared with the analytical weight reduction potentials to evaluate the actual weight reduction performance of advanced composites relative to their inherent capability.