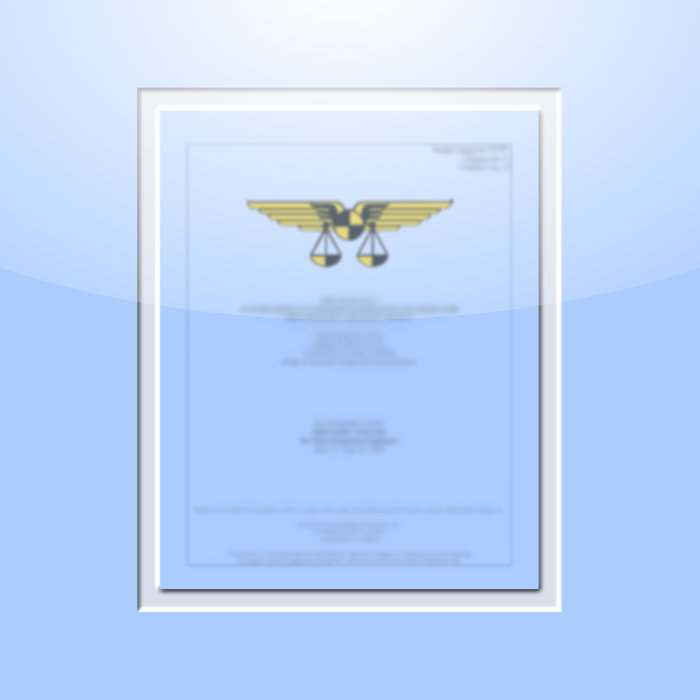
1398. Composite Materials at Avco Specialty Materials
$20.00
SAWE Members get a $200 store credit each year.*
*Store credit coupon available at checkout, click the button in your shopping cart to apply the coupon.
Not applicable to SAWE textbooks and current conference technical papers.
Paper
Abstract
There is today a rapidly expanding demand for advanced lightweight composite materials for both the conventional aerospace market as well as for the many emerging uses in the commercial industries. The authors of this paper and their associates are employed in the development of various types of these advanced materials, specifically concentrating on reducing the cost of established materials, such as the graphite fiber products, and developing new metal matrix materials to meet the challenge of higher temperature exposure and a generally more severe service environment. In each case, our objective is to develop fiber reinforcement preforms that are of the lowest possible cost and of a construction that is more convenient for fabrication of composite parts.
For the graphite fiber market we are developing methods for the manufacture of tow cost PAN based materials, using the large count 160,000 fiber end commercial grade precursor that is readily available in large quantities at low cost. For this large count material we have developed a production facility that is capable of producing many diverse products and is most economical in terms of both material and labor costs. A mainstream production line has been established for conversion of the PAN into graphite epoxy prepregs and from this primary material flow, several intermediary products are removed for alternate processing.
Other composite materials being developed are the boron and silicon carbide monofilament for metal matrix composite applications where high temperature performance is required. In the USA these materials are experiencing a resurgence of interest, being stimulated in part by a shortage of critical aerospace materials and in part by the drive for more energy efficient engines and structures. For both the titanium and aluminum metal structures there are a number of exciting developments in the area of fabrication that offer encouragement for increased use of the composite materials. For titanium structures, the relatively low cost super-plastic forming/diffusion bonding technique is a promising method for fabrication of engine and other high temperature components such as missile structures. Reinforcing fibers, such as the Avco silicon carbide, can be added to the titanium structure during the diffusion bonding procedures or alternatively the composite materials can be brazed in selected positions as a subsequent operation. Super-plastic forming of aluminum alloys is also an attractive concept, however for medium temperature structural applications, we believe our concept of hot molding silicon carbide aluminum material directly to shape even more interesting. Here the concept is to mold the composite directly to net shape by methods analogous to vacuum bag molding of graphite epoxy, where in a one sided heated tool, composite structure is formed by low pressure autoclave techniques without the requirement for subsequent forming and machining.
To support the use of these advanced composite materials, the authors are concentrating on developing fibers and fiber preform materials that are directly amenable to the intended fabrication process and end use. Preformed, yarn, roving, etc; preformed graphite epoxy prepregs and preforms of fibers in metals are being developed for the industry.