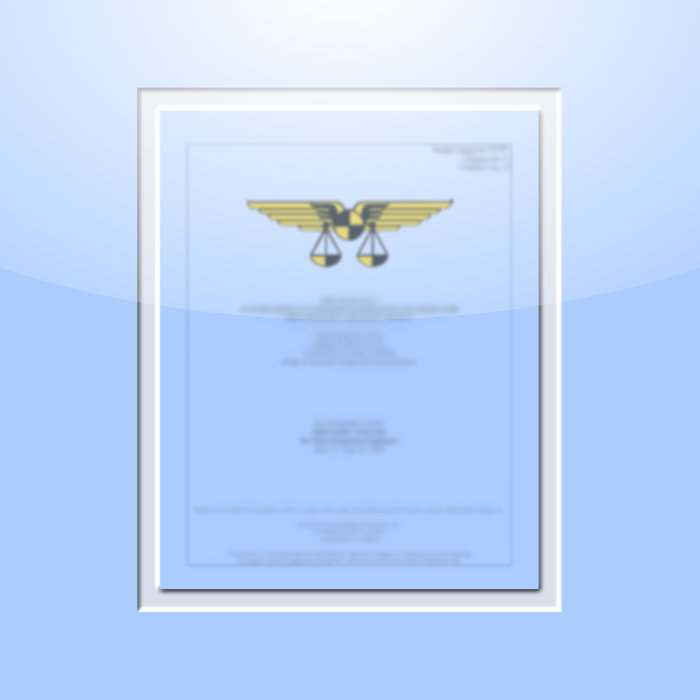
1380. Technologies Involved in Configuring an Advanced Earth-To-Orbit Transport for Low Structural Mass
$20.00
SAWE Members get a $200 store credit each year.*
*Store credit coupon available at checkout, click the button in your shopping cart to apply the coupon.
Not applicable to SAWE textbooks and current conference technical papers.
Paper
Abstract
The current space shuttle is expected to adequately meet Government and industry needs for the transport of cargo to and from orbit well into the 1990’s. However, continual study of potential follow-on shuttle systems is necessary and desirable in order to complement ongoing research in materials, structures, propulsion, aerodynamics, and other related areas. By studying alternate systems well in advance, it will be possible to explore the various technologies and develop those for which there is the greatest apparent payoff.
In this paper a single-stage Earth-to-orbit transport designed for delivery of approximately 29,500 kg (65,000 lb) payload will be described. The vehicle, which takes off vertically and lands horizontally, is 60 m (197 feet) long and weighs approximately 1.8 Gg (4 M lb) at liftoff. In the interest of weight reduction, a simple body of revolution is utilized for the main body shell. In this design the main propulsion tanks serve as a primary load-carrying structure. Further, in order to minimize structural mass, the cargo bay is located between two of the main propellant tanks. The cargo volume, at 396 m3 (14,000 feet3), exceeds that provided by the shuttle; but the bay itself is nonconforming in shape–being approximately 10 m (32 feet) in diameter by 5 m (17 feet) long. Dual-fuel propulsion is employed, since a number of studies have shown that (though lowering performance) the operation of hydrocarbon (RP) engines in parallel with LOX/LH2 engines results in a net reduction in the vehicle’s physical size and structural mass. Other weight-saving features entail the extensive use of honeycomb sandwiches, advanced materials, and advanced fabrication techniques.
Some of the technology issues involved in reducing vehicle mass are: ‘flyability’ and entry heating on bodies of circular shape; compatibility of nonconforming cargo bay geometry to future mission scenarios; fabrication and assembly of large honeycomb sections (particularly of tankage); development of high-pressure RP engines and nozzle extension systems for LOX/LH2 engines. Also critical to the development of a lightweight vehicle is the development of active control systems without which control surfaces become unreasonably large and heavy.
The vehicle presented is utilized only as a means to study and identify various technologies needed in order to develop a low mass Earth- to-orbit transportation system for the future. A key element in this task is the Aerospace Vehicle Interactive Design System (AVID)–a program (or system) which is capable of rapid estimation of mass properties and sytems performance for a given set of mission requirements.
The conclusion of this study is that vehicle geometry and structural/materials technology are critical to the development of efficient single-stage Earth-to-orbit transports.