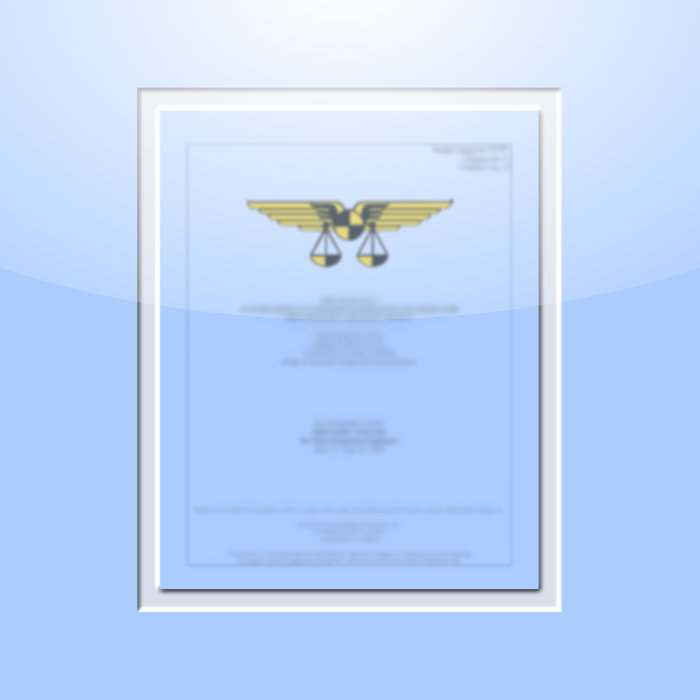
1251. Spacelab Module Structure – Design Problems Related to Weight
$20.00
SAWE Members get a $200 store credit each year.*
*Store credit coupon available at checkout, click the button in your shopping cart to apply the coupon.
Not applicable to SAWE textbooks and current conference technical papers.
Paper
Abstract
The weight control of the Module Structure, the major component of the total weight of the SPACELAB (50%-60% Module only flight configuration) turns out to be one of the most challenging engineering problems encountered in the design of the first European manned spacecraft compartment.
The importance of the weight in the Module Structure design is dictated by the one-to-one relationship it has with the useful weight left for the experiments that is to say the ”users weight’.
Since the early phases of the program, in addition to technical attention, also management attention has been devoted to the weight problem, starting from the preliminary design, in virtue of the fact that contractual implications are annexed to the compliance with an agreed Mass Budget that is part of the Specifications.
The standard systems of weight prediction and control, starting from the estimates in the early phases of design to be replaced by weight calculated on the basis of the definitive drawings, existing AERITALIA, improved in order to keep under strict control the Mass Budget, are briefly described.
The approach followed in the design from the preliminary phase up to the final phase of flight unit hardware design is discussed for what concerns the final phase of flight unit hardware design is discussed for what concerns the implications relative to the weight problem; the trade off studies between sophisticated engineering solutions requiring complex analyses and costly manufacturing and the more traditional ones are briefly recalled, showing the criteria adopted to keep the finally selected solutions within the limits imposed by sound engineering practice, reasonable cost and the required safety. The optimization techniques used in the design of the primary Module shell are briefly outlined as an example of the approach adopted.
Comparison between estimated, calculated and measured weight values are reported to demonstrate the high confidence of the methods applied and to evidentiate the influence of the modification introduced during the evolution of the design.