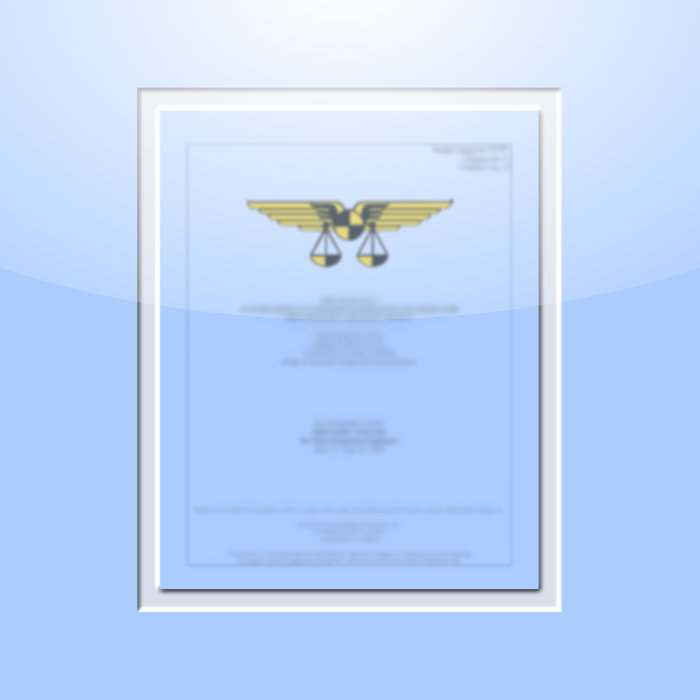
1165. Cost Effective Weight Reduction and Automated Sizing of Highly Loaded, Small Machined Parts
$20.00
SAWE Members get a $200 store credit each year.*
*Store credit coupon available at checkout, click the button in your shopping cart to apply the coupon.
Not applicable to SAWE textbooks and current conference technical papers.
Paper
Abstract
Convair’s boron aluminum tube product occupies 242 primary structural locations in the Space Shuttle Orbiter. Analysis of the first ships et of tubes showed an overall weight reduction of approximately 300 pounds (136 kg) with
this application of advanced composites, but the machined titanium end-fitting portion of the tube assembly was found to contribute a relatively high percentage of the total tube assembly weight for many part numbers. In addition, stress concentrations from the end-fitting clevis blades were found to reduce the fatigue life of the boron-aluminum to titanium diffusion bond. Thus, a program was undertaken to redesign the titanium end-fitting portion of the boron-aluminum tube with the goals of reducing weight, reducing machining costs, and increasing structural efficiency. This paper summarizes what has proven to be a successful cost effective weight reduction effort, and outlines computer techniques developed to optimize the new end-fitting configuration for minimum weight and maximum structural efficiency.