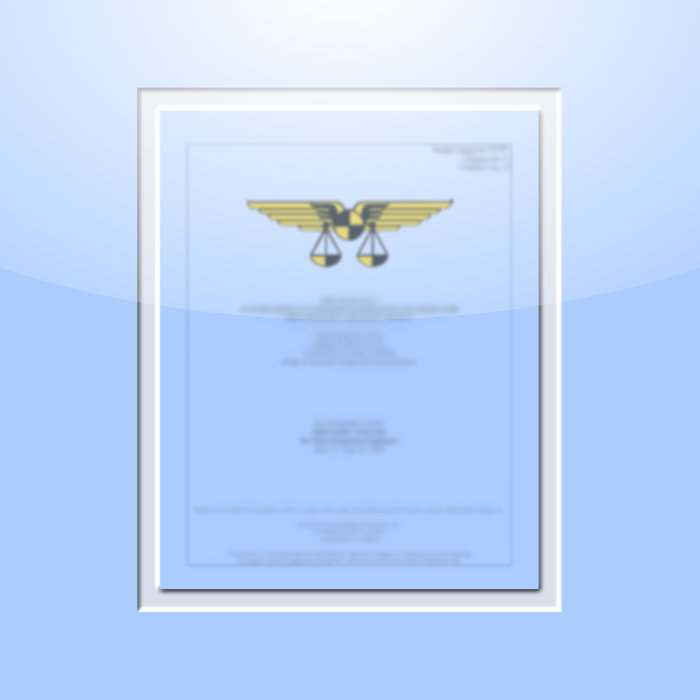
1070. The Integrated Team: Key to Implementing Design-To-Cost
$20.00
SAWE Members get a $200 store credit each year.*
*Store credit coupon available at checkout, click the button in your shopping cart to apply the coupon.
Not applicable to SAWE textbooks and current conference technical papers.
Paper
Abstract
For many years defense programs have been characterized by almost unlimited funding. Emphasis was placed on performance, and nothing but the best was acceptable. During the past several years however, rising technology costs, an inflationary economy, and competition for federal funds have brought on pressure to reduce defense spending. Design-to-cost now appears to be the answer to the dilemma of cost control in the development of future defense systems. The concept of cost as a design
parameter is not totally new. Cost targeting has been used for years by many manufacturers of commercial products. Neither are the techniques used in the design-to-cost new to the mass properties engineer. The traditional approach used for effective weight control is equally applicable to cost control, although cost is a much subtler parameter than weight. Design-to-cost must be implemented properly, or it can fall short as have other DOD cost control procedures. At Convair, we believe that we have carefully designed a management system that provides the framework for successful design-to-cost implementation. The key, we believe, is the integrated team approach. Using an integrated project team organization, Convair product design and system development activities are continuously evaluated against cost requirements with emphasis equal to that placed on technical requirements. Our design-to-cost plan features evolution of the product design to specified cost targets in discretely planned, controlled, and fully traceable steps. This allows us to continuously evaluate progress toward program objectives, technical requirements, and cost goals at predetermined program milestones. These milestones provide a number of performance periods in which our progress can be measured. We complete a design-to-cost cycle within each performance period. Our experiences at Convair in the application of design-to-cost lead us to a number of conclusions and recommendations: Contractual language must reflect carefully delineated requirements and definitions, not only for cost, but also for related performance, reliability, and maintainability requirements. Design-to-cost goals must be established early in the development process. Close coordination between design and manufacturing must begin early and continue throughout the design phase. Vendors and suppliers must also be required to adopt design-to-cost practices. Design-to-cost has demonstrated its effectiveness and value.