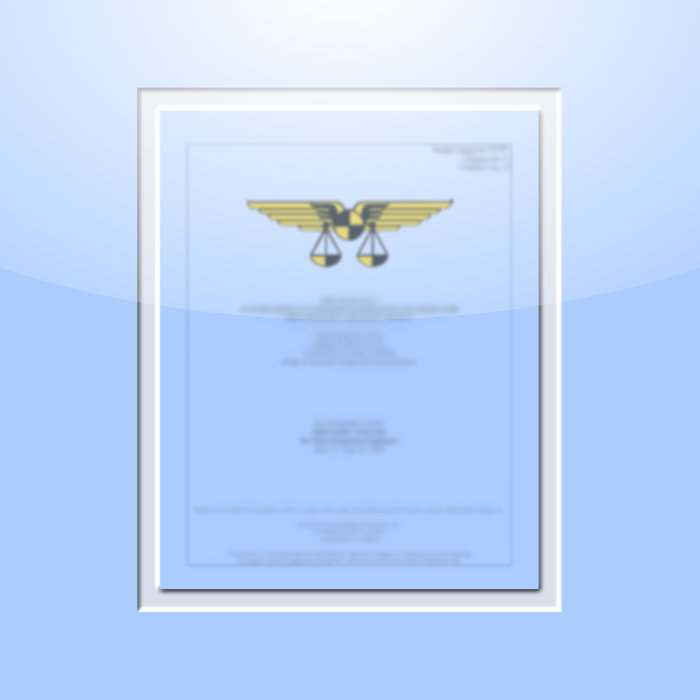
913. Cost Analysis as Applied to Aircraft Synthesis
$20.00
SAWE Members get a $200 store credit each year.*
*Store credit coupon available at checkout, click the button in your shopping cart to apply the coupon.
Not applicable to SAWE textbooks and current conference technical papers.
Paper
Abstract
This paper presents the methods necessary to develop an improved method of estimating airframe manufacturing costs using a unique and fundamental approach originated by Convair Aerospace.
The computerized cost estimation method developed utilizes a technique for generating a detail parts list of a projected vehicle when only configuration concepts are available as input. The detail parts then are analyzed individually to determine their weight and the costs of material and manufacturing. Weights and costs of all detail parts are then summed, adding in the weight and costs of assembly elements, to determine the complete vehicle airframe weight and manufacturing cost. To this cost the engineering and tooling cost are added to complete the cost model.
The cost analysis based at the individual detail part level is made by considering the actual manufacturing operations required to produce that part. A list of shop operations is called out with each detail part, and a series of equations associated with each operation are utilized to compute the shop hours necessary to make the part. By applying the appropriate labor rates to the calculated hours, the direct and indirect manufacturing labor costs can be found. Material costs can be computed based on the amount of material required to manufacture each part, and in this way the total manufacturing costs can be derived.
The detail part-level breakdown of components is attained through the use of several synthesis routines coupled in series. The input consists of generalized vehicle and mission parameters of a type typically known at the preliminary design level, Initially, the overall vehicle is sized and weighed using conventional predesign relationships. This output then is used to drive a routine which sizes, weighs, and derives geometry for major subcomponents (e.g., spars, frames, cover panels, etc.). A detail part definition process follows, which calls out a list of typical detail parts for each of the major subcomponents specified. These detail parts then represent the basis of the fundamental level of weight and cost analysis.
Reasons for developing this cost model with such detail are:
1. Current cost estimating techniques are insensitive to many specific design features, modes of construction, and materials.
2. Technology is increasingly able to take full advantage of computerized techniques to handle large volumes of detailed data.
3. Current computerized accounting techniques generate large amounts of data
for analysis by the cost estimator.
4. Finally, a technique is required that will be a design driver and provide a
least-cost design for a specified level of performance.