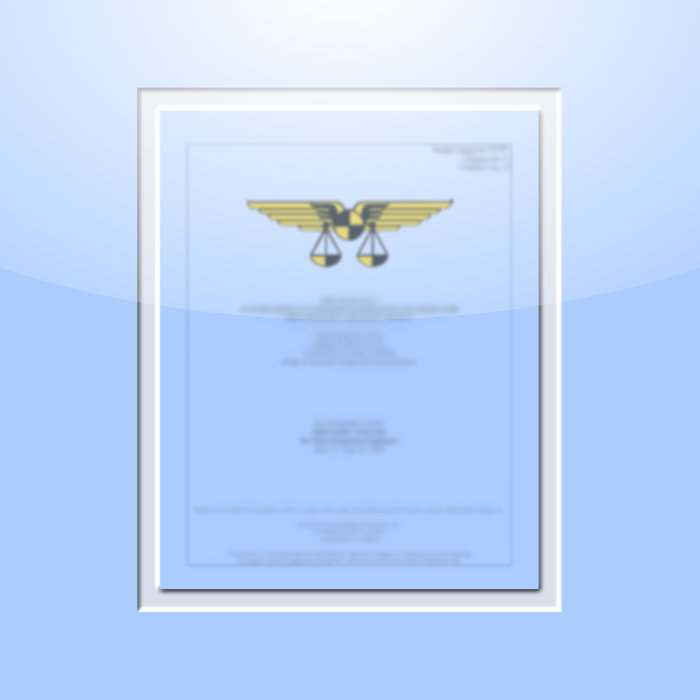
757. Systems Design for Weight Optimization
$20.00
SAWE Members get a $200 store credit each year.*
*Store credit coupon available at checkout, click the button in your shopping cart to apply the coupon.
Not applicable to SAWE textbooks and current conference technical papers.
Paper
Abstract
It is well known that one of the fore most objectives during initial design of a new aircraft is to minimize structural weight. This paper describes a method for reducing structural weight that relies on a more fundamental approach than the typical detail part weight study. The concept reported here was used effectively during design of the trailing edge flap drive system for the 747 airplane. It is based on applying the principles of systems engineering to optimize the weight of a group of related elements, rather than treating each component as an isolated case.
This approach is feasible because for most of the controls equipment, weight is analogous to load, and the design loads can be regulated to a certain extent by the equipment itself.
Aircraft structure is in general, sized to with stand aircraft maneuvering and externally applied loads. Maneuver and external load values are related to the aircraft’s mission requirements, and the resulting weight is, in that -sense, productive. However, it frequently occurs that loads larger than the mission requirement loads are produced by the controls systems used on the aircraft. The systems-produced loads do not enhance mission capability, and the result is a weight penalty. Minimization of these penalty loads is thus a significant weights engineering concern.
It is usually necessary to add load-limiting devices for reducing the control system peak loads that produce weight penalties. This function i s accomplished on the 747 trailing edge flap system by incorporating torque brakes into the drive mechanism. Reduction of systems loads is then possible by eliminating or lessening the influence of dynamic effects, tolerances and other variables such as friction.
The load control analysis involves a unique system. The elements involved must be identified and designed into the load control system with the criterion of minimum load penalty. For the 747 trailing edge flap system this design process included consideration of such factors as overall system arrangement, component location, torque tube stiffness, torque brake capabilities, ball screw characteristics, lubricants and other mechanical performance details.
The concepts described here can be applied to most operating systems for complex aerodynamic control surfaces. As shown by the example given, weights engineering can be used at the design stage or reduce structural loads and the attendant weight penalties. Even though certain component weights may be increased, the result is a significant reduction in overall airplane weight.