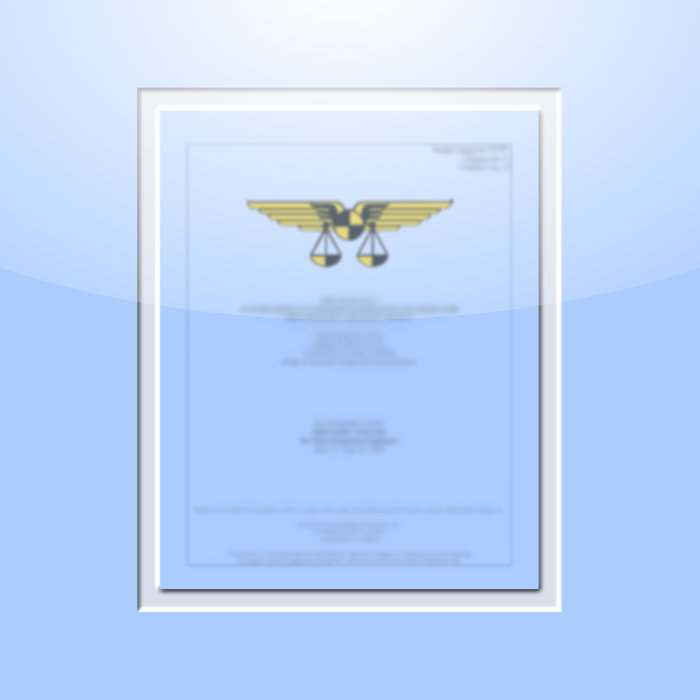
581. Preliminary Design Method for Weight Optimization
$20.00
SAWE Members get a $200 store credit each year.*
*Store credit coupon available at checkout, click the button in your shopping cart to apply the coupon.
Not applicable to SAWE textbooks and current conference technical papers.
Paper
Abstract
Rapidly changing design technology and development of new structural materials necessitate development of high speed computer programs to account for these advances in the preliminary design phase. A standard payoff function used in many current aerospace designs is weight minimization. Although this criteria does not necessarily yield an ‘optimum’ design (including cost effectiveness), it is quite valuable in determining performance effectiveness and often is at least an indicator of optimum design trends.
The technique described in this paper has been successfully applied as a preliminary design method for minimizing the gross weight of a solid rocket propulsion system subject to performance, geometric, and design constraints which are obtained from operational or environmental restrictions. This technique utilizes the method of undetermined multipliers with a modified Newton-Raphson iteration process.
The sample problem was formulated by developing an overall trade-off study mathematical model consisting of several environmental sub- models and a gross weight minimization model. The environmental submodels are used to define the in-flight loading and heating environment and provide design constraints for the gross weight minimization model.
The subject method has been shown to be adequate for use as:
– A preliminary design tool for establishing optimum design parameters
– A design tool for comparative evaluation of structural materials and design concepts
– A method for definition of areas where component research and development should be most fruitful
This method has also been used to demonstrate the concept that to obtain maximum benefit from weight minimization, each structural material must be allowed to operate with its own set of optimum design parameters.
In addition to a general description of the weight optimization method, a sample problem of multistage solid propellant rocket is shown, including details of methodology, types of problems encountered in the optimization process, and sample results. This problem is formulated as a gross weight minimization problem with burn-out velocity, case design, overall length, and burn-out acceleration constraints. Application of this method to turbine engine optimization in aircraft mission analysis is also discussed.