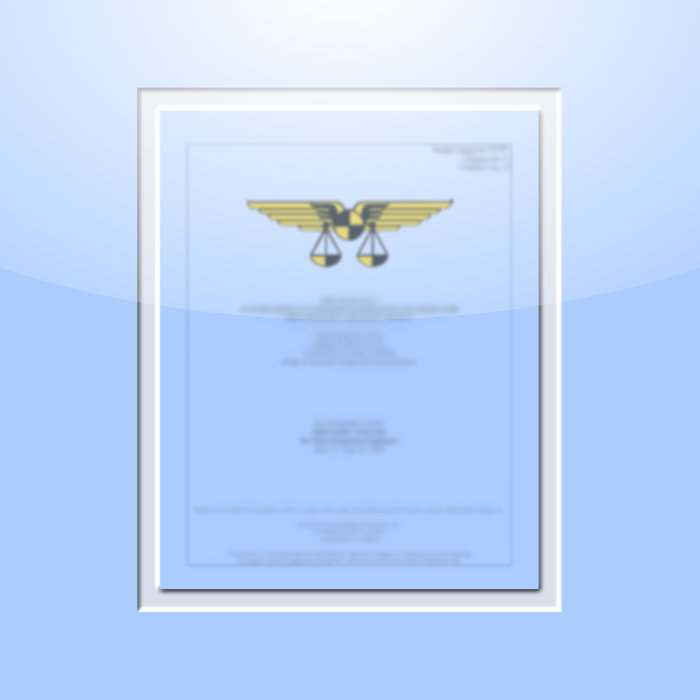
527. The Titanium Sine-Wave Beam – For Minimum Weight
$20.00
SAWE Members get a $200 store credit each year.*
*Store credit coupon available at checkout, click the button in your shopping cart to apply the coupon.
Not applicable to SAWE textbooks and current conference technical papers.
Paper
Abstract
Although developed for the XB-70 aircraft almost a decade ago, the titanium sine-wave shear beam still does not enjoy the widespread application which is warranted by its weight-saving potential. In comparison to conventional aluminum flat-web and stiffener configurations, weight reduction is in the order of from 20 to 40 percent. Such relative efficiencies are evident both theoretically and in hardware comparisons. Beams which have been designed and fabricated by North American Aviation vary dimensionally from .012 thickness and three inches in height, to .052 thickness and seven feet in height. The former was used for spars and ribs in the XB-70 empennage, and the latter structure was an advanced development of a center engine crossbeam typical for a large booster.
Efficiency increases are obtained from both the material application and the design configuration. Material improvement accounts for from 10 to 20 percent of weight reduction, due to increased strength/weight ratio of titanium compared to aluminum. The sine-wave web concept permits an additional approximately equal amount of weight reduction, in that all material is both load-carrying and self-stabilizing. The burn-through weld joint of the web to cap, with minimized material, achieves additional weight savings. In addition the geometry parameters of the sine-wave configuration – web thickness, pitch and height of the wave – can be tailored to achieve optimum structural design, with either simultaneous buckling in both local and general stability modes, or to simultaneously satisfy criteria of both strength and stiffness.
Photographs of typical design applications of the concept for aircraft and space-booster structures are shown. Included are the various methods of attachment of spar caps to the surface panels of wing and empennage which were used on the XB-70. The design equations are presented for optimization of the concept for minimum-weight design for any combination of load and stiffness criteria or geometry constraints.