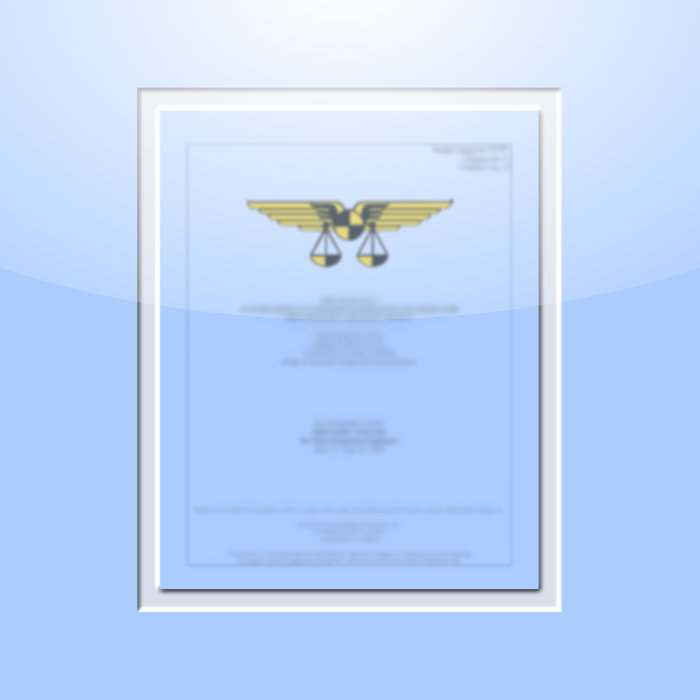
176. Meeting Structural Requirements With Minimum Weight
$20.00
SAWE Members get a $200 store credit each year.*
*Store credit coupon available at checkout, click the button in your shopping cart to apply the coupon.
Not applicable to SAWE textbooks and current conference technical papers.
Paper
Abstract
This paper was originally prepared with the equipments of the B-58 airplane in mind. However it is applicable to all airborne equipment. A structurally adequate minimum weight design requires a great deal of ‘Planning ahead’. This planning starts with the very early assignment of weights and size to the different parts of the aircraft.
It is the attitude of the management of a company toward meeting its weight allotment that is the key to success or failure. Management must price and plan its work to achieve this end, by providing the time and facilities for the Engineer to develop the product to specifications.
Assuming that the way is clear for the Engineer to proceed: First he should read and try to understand all of the applicable specifications. Most serious errors are made by not fully understanding all of the requirements for the design. The specification weight is not an objective, it is a requirement. The structure must develop at the same time or just after the selection of the components so as to take full advantage of the best means possible to arrange and mount the components. Mounting the components is the only reason for creating the structure.
One important thing to consider in the development of an original design is the selection of an economical procedure whereby a given component can be developed so that it will have sufficient strength at every point; but will be no stronger at any point than is considered necessary or desirable. The procedures I would select would be:
1. Paper and pencil methods of stress analysis to secure some initial development that appeared adequate strength-wise and was within the specification weight allowance.
2. Test a full sized structural model to the greatest ultimate, static or shock load conditions that occur in all three planes. The model should be coated each time with brittle Lacquer and loaded with simulated component masses.
3. Refine the design with the knowledge gained from the cracks in the brittle Lacquer, or possible actual structural failure. Redesign so as to relieve points of high stress concentration and also try to reduce the material, both in thickness and by cutting flanged holes in areas of very low stress. Again check the weight of the design and further refine the design if necessary.
4. Vibration test a new model with simulated masses to determine if there are any points of resonance.
5. Refine the design again if required before a model with some actual delicate components is prepared for vibration test. Recheck your weight and further refine if required.
6. Prepare your production design with reasonable assurance that It w)1l meet all of the structural requirements with minimum weight. Recheck your weight and refine, if required.