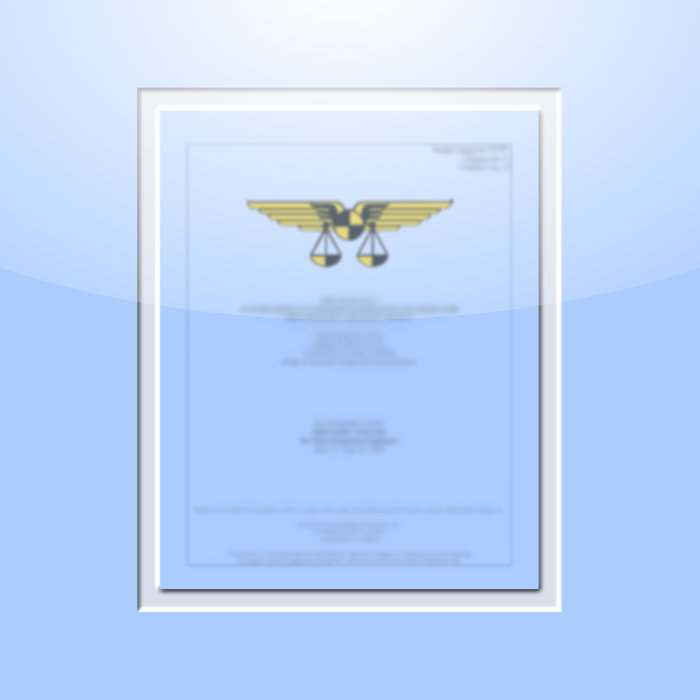
3450. Boeing Optistruct Usage: Challenges of Implementation and the Emergence of a New Design Role
$20.00
SAWE Members get a $200 store credit each year.*
*Store credit coupon available at checkout, click the button in your shopping cart to apply the coupon.
Not applicable to SAWE textbooks and current conference technical papers.
Paper
Abstract
Since 2004, Boeing has been using Altair’s Hypermesh and Optistruct pre- and post- FE processors as a means of reducing airplane weight.
The process consists of two main optimization methodologies: 1) topology, which determines optimal load paths by iteratively re-orienting material within a given design space to maximize stiffness and 2) size & shape, finalizing the geometry by fine-tuning dimensions via gauge property modification or FEM morphing.
Unorthodox part shapes and sizing combinations tend to result from these processes on parts ranging from Flight Control Actuators to Wing Primary Structure to Power Distribution Panels and Racks within the Electronics Bay.
The optimization methods and processes currently in use by Boeing have resulted in average weight savings of 20% on 100+ parts, which usually also exhibit performance improvements with respect to stiffness, stress, and resonant frequency.
While the design process is technically sound and has provided valuable results, several logistical challenges nevertheless arise during implementation. These challenges are systemic in nature and suggest a fundamental re-thinking of the design team structure and the nature of the interactions among its constituent parts.