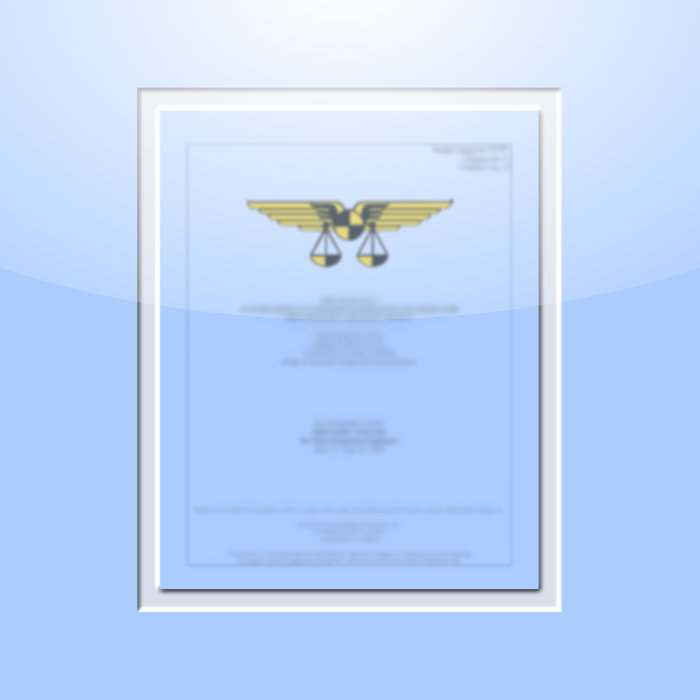
2296. Center of Gravity Determination by Video Photogrammetry
$20.00
SAWE Members get a $200 store credit each year.*
*Store credit coupon available at checkout, click the button in your shopping cart to apply the coupon.
Not applicable to SAWE textbooks and current conference technical papers.
Paper
Abstract
Photogrammetric techniques have been used for industrial measurement for more than a decade. This technique involves the collection of images (either film or digital) from geometrically varied positions. Two dimensional measurements of discrete, identifiable points on the images can then be reduced analytically to three-dimensional coordinates. These coordinates can be determined to an accuracy range of: 1 : 100,000 (0.001” RMS over a 100” Length) 1 : l ,000,000 (0.001” RMS over a 1000” Length) The application of photogrammetry has been quite varied, ranging from ship building to precision antenna alignment. The three-dimensional coordinates can be analyzed to determine, for example, angular or translational displacement, surface conformance to design, and/or many other alignment and quality assurance tasks. In the manufacture of satellites such as the Space Test Experiment Platform (STEP) Mission 4, video photogrammetric techniques have been applied in an effort to satisfy requirements related to the satellite’s mass properties. Specifically discussed in this paper is the combination of photogrammetry with a classic approach to center of gravity (c.g.) determination to achieve rapid, high precision results. In an effort to characterize the satellite’s light weight and semi-flexible deployed wings, it is necessary to make mass properties and shape measurements of each wing. Each wing is suspended by a single support cable at an attach point. Targets on the wing and the cable are measured photogrammetrically. This process is repeated for other attach points on the same wing. The data is then analyzed to determine the c.g. of that wing. A robotic video photogrammetric system is used to speed the acquisition of the data (e.g. – a single attach point measurement set is completed in less than 2 minutes). The c.g. was determined in three dimensions to an accuracy on the order of (0.010” RMS for a 8′ by 4′ multi-paneled wing, which is well within the specified requirements. Photogrammetric techniques and analysis will also be applied to measure wing/spacecraft alignment, to determine required trim weights and adjustments, and finally to determine the product moment of inertia of the spacecraft.