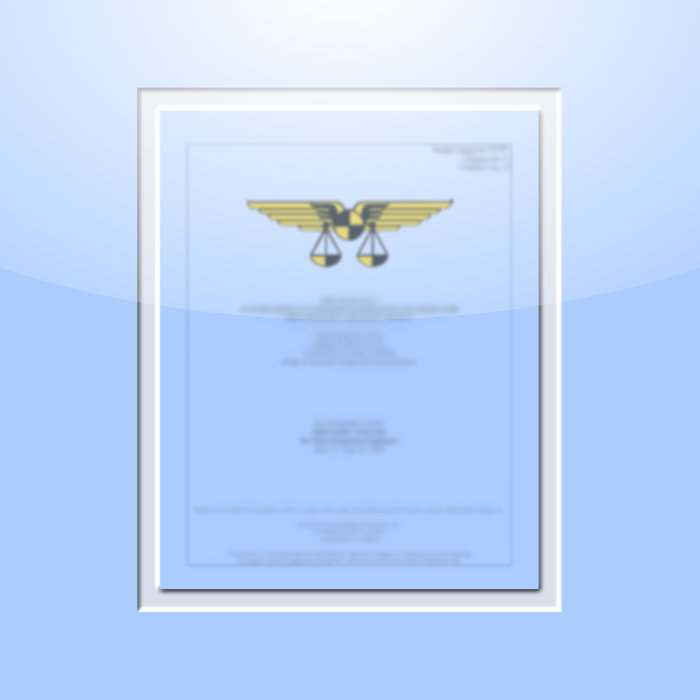
2282. Semi-Analytical Method for Predicting Wing Structural Mass
$20.00
SAWE Members get a $200 store credit each year.*
*Store credit coupon available at checkout, click the button in your shopping cart to apply the coupon.
Not applicable to SAWE textbooks and current conference technical papers.
Paper
Abstract
Depending on the type of aircraft, the structure accounts for between 20-30% of the gross weight, while the wing contribute about 10% of the total structural mass. It is the portion most directly under the control of the designer. Simple wing mass prediction methods developed and used in general are based on empirical information and weighting factors collected over the years for existing aircraft. These methods only require the most fundamental wing data, i.e., wing span, area, etc. It is therefore difficult to use such methods as design tools to assess the affect of various design parameters on wing mass. Examples of such parameters include planform geometry (wing span, root chord, tip chord, wing thickness, wing sweep, wing area, etc.), design operating conditions, and material characteristics (allowable stresses, elastic and rigidity modulus, etc.). It is also true to say that one cannot fully rely on the answers obtained from such methods. All major aircraft manufacturing companies have developed self relying theoretical/empirical mass prediction methods. It is very difficult to obtain details of these methods, and in any case such methods are often only applicable for aircraft made and designed by these organizations. This paper describes a theoretical mass prediction method developed for use as a general tool for preliminary aircraft design work. Design variables that can be tested include wing geometric parameters, design operating conditions and material properties?allowable stresses can be evaluated from a given loading condition. The theory is based on the premise that the wing structural box must be designed to meet both the bending strength and torsional stiffness requirements. The technique accounts for structures made in both and fiber reinforced plastic (FRP) materials. Preliminary test carried out on a number of aircraft made from metallic materials suggest that the method gives results that are consistent with manufacturers? data.