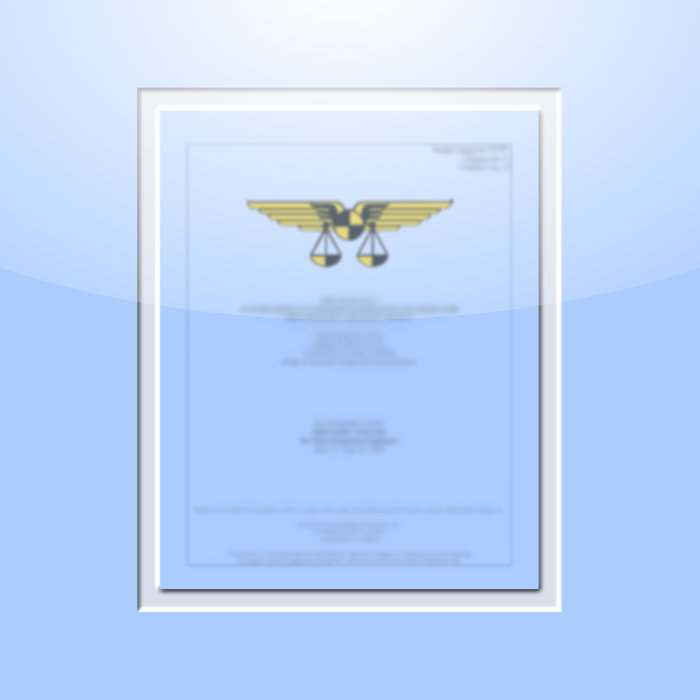
2192. A Non-Contacting Vertical Alignment System for Mass Properties Measuring Instruments
$20.00
SAWE Members get a $200 store credit each year.*
*Store credit coupon available at checkout, click the button in your shopping cart to apply the coupon.
Not applicable to SAWE textbooks and current conference technical papers.
Paper
Abstract
Sandia National Laboratories recently had a need to balance and measure the mass properties of several large, lightweight objects. These objects were too compliant and asymmetric for traditional alignment procedures using contact sensors. Therefore, a non-contact system for alignment of these test objects was developed. Since a well defined geometric axis was not available for these test objects, a reference axis was defined using two planes through the test object. At the bottom plane, noncontacting laser triangulation sensors measure the variation of the surface of the object and a best-fit circle is calculated. The reference axis is defined to pass through the center of this circle at the bottom plane and through the center of a reference target at the top plane. Digital video analysis is used to calculate angular orientation and reference target motion during a slow rotation of the test object. The top and bottom plane offsets of the reference axis from the balancing machine spin axis and the required corrective adjustments are then calculated. This new procedure requires two to three iterations to converge to the final alignment and can be accomplished in less than two hours. The current implementation can align objects to less than .001 inches at the two planes with final requested adjustments of a few ten-thousands of an inch. This procedure also measures several hundred data points around the circumference of the test object, instead of the standard four contact measurements. This allows the procedure to be more robust, since the object does not have to be perfectly symmetric. Also, the increased automation shortens the operator learning curve and lessens the chance of operator error. And finally, since all calculations are performed in software, a record of the measurements and alignment parameters are available for later reference. The hardware and processes developed for non-contact alignment open up a new realm for balancing and testing of very large and lightweight test objects.