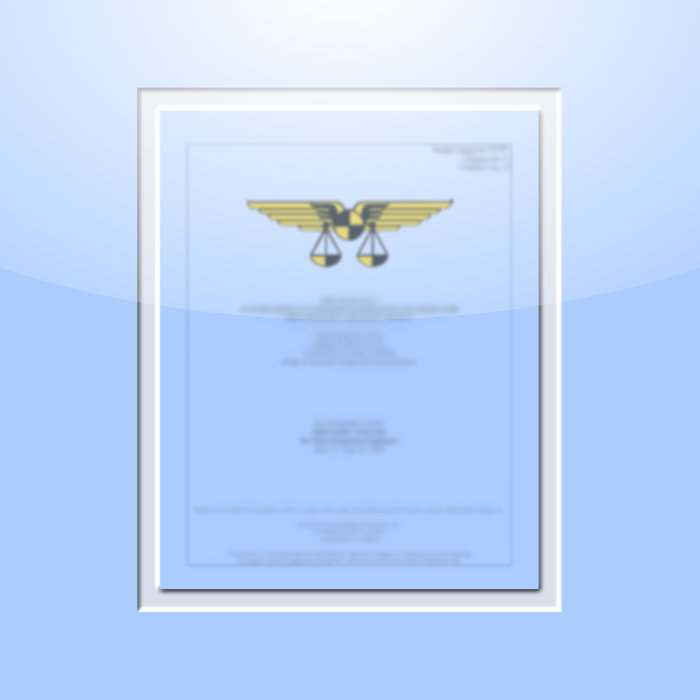
2019. Introduction of Titanium Alloy Into Hydraulic Tubing
$20.00
SAWE Members get a $200 store credit each year.*
*Store credit coupon available at checkout, click the button in your shopping cart to apply the coupon.
Not applicable to SAWE textbooks and current conference technical papers.
Paper
Abstract
The hydraulic system is an essential part of every modem aircraft. The hydraulic lines transport energy in the form of fluids under pressure. Since weight saving has always been paramount in aircraft design, hydraulic circuits are designed to high pressures in order to keep tubing sizes and the total weight of the hydraulic system as low as possible. In commercial aircraft, 3,000 psi (2 1 0 bar) pressure systems are most commonly used worldwide while 4,000 psi (276 bar) systems are being increasingly used in military aircraft. But one cannot increase pressure to save weight without creating other problems. Therefore, lighter materials than currently in use are, of course, most attractive to weight engineers. Until now a CRES alloy with 21 percent chromium, 6 percent nickel, and 9 percent manganese has yielded good results. By the mid 1960s, some aircraft companies had changed their CRES hydraulic tubing to the lighter titanium tubing, although this was still a relatively soft titanium alloy. Today, thanks to continued research, the considerably harder Ti-3Al-2.5V alloy is already used in the U.S. and Europe for high pressure tubing circuits. Therefore, titanium hydraulic tubing may be considered state of the art today. But the transformation into tube assemblies is not without problems. That was the background when Airbus Industrie decided to apply titanium alloy to the high pressure lines of the hydraulic circuits of its Airbus A320. Ti-Al-2.5V alloy has properties nearly as good as CRES 21-6-9 and people not familiar with production problems may have thought of it as a cost effective possibility of weight saving. Except for the obligatory certification tests, only few screening tests have been assumed to be sufficient. The concerned tubing ranges in size from 0.25 inch (6.35 mm) to 1.50 inch (38.1 mm) and the predicted weight saving in the Deutsche Airbus part of the A320 was 106 lb (48 kg).