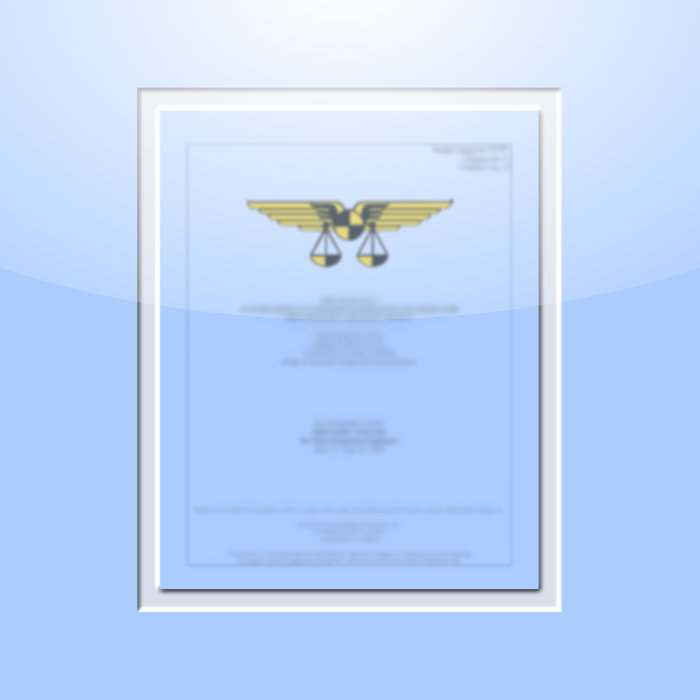
1888. Minimum Weight High Tempterature Joint Design for Reentry Vehicles
$20.00
SAWE Members get a $200 store credit each year.*
*Store credit coupon available at checkout, click the button in your shopping cart to apply the coupon.
Not applicable to SAWE textbooks and current conference technical papers.
Paper
Abstract
High temperature joint design is a subject which has been receiving increased attention as a result of the ongoing national effort to advance hypersonic and materials technologies. Current fastener technology is sufficient for temperatures below 1600′ F, but the development of advanced carbon/carbon (ACC) has created a need for a robust fastening system which can maintain reasonable strength up to temperatures of 3000′ F. High temperature fastener data is limited, and there is a significant need for additional research and development The objective of this paper is to provide directional input to this future work in the form of minimum weight carbon-carbon splice joint design estimates for a given range of load and temperature conditions. The data presented in this paper is based on an analytical model of a single shear C/C splice joint which was evaluated for running loads ranging from 200-4000 lb/in and temperatures ranging from 78-3000′ F. Minimum weight designs were identified at finite intervals within these ranges through an iterative optimization of the major design variables: fastener material, fastener spacing, fastener diameter, panel thickness, and the number of fastener rows. Sixteen different fastener materials were evaluated in the optimization including among others: T-222 tantalum, C129Y columbium, TZM, carbon/carbon, and tungsten hafnium carbide. The results of this analysis indicate that for joint loads of less than 1000 lb/in and temperatures greater than 1800′ F, the minimum weight design includes C/C as the fastener material. Joints with loads greater than 1000 lb/in and temperatures between 1800 and 2200′ F should be designed using T-222 tantalum or TZM. Tungsten hafnium carbide yields the minimum weight design for joints with loads greater than I 000 lb/in and temperatures greater than 2200′ R. The subject of high temperature carbon-carbon joint design includes many issues, of which weight is only one. Oxidation protection, thermal expansion, and a variety of other material and design problems must be considered in the development of a robust high temperature fastening system for carbon/carbon. This paper represents an effort to quantify the weight impacts of various design decisions, and thereby provide input to the future testing and development of high temperature fastener materials.