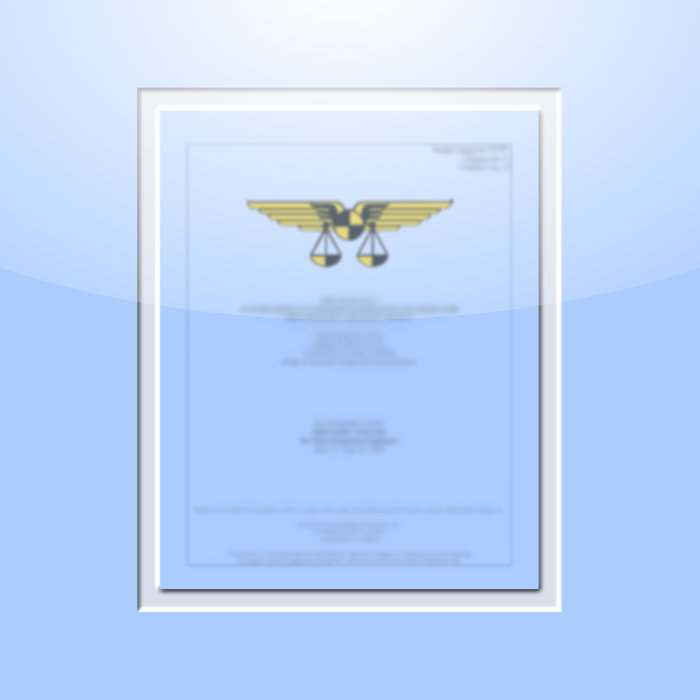
1679. Higher Harmonic Control; Vibration Reduction for Reduced Weight
$20.00
SAWE Members get a $200 store credit each year.*
*Store credit coupon available at checkout, click the button in your shopping cart to apply the coupon.
Not applicable to SAWE textbooks and current conference technical papers.
Paper
Abstract
Higher Harmonic Control (HHC) technology has been successfully applied for helicopter vibration reduction by exercising rotor blade pitch control at frequencies which are high harmonics of rotor rotation. The control motions are generated by three electrohydraulic actuators which are commanded by an airborne microprocessor. This processor receives vibration sensor measurements, estimates the state of the helicopter using a Kalman Filter type algorithm and computes the optimal controls to minimize vibrations.
In contrast to the conventional passive means of vibration control, such as vibration absorbers and vibration isolators, higher harmonic control (HHC) is an active control concept. A passive vibration control device treats the vibratory loads after they have been generated, whereas an active vibration control system, such as HHC, alters aerodynamic loads on the rotor and therefore the vibratory forces and moments which cause the airframe vibration are reduced.
Previous passive means of vibration control are not as effective as higher harmonic control at reducing helicopter vibrations and, at the same time, have imposed significant weight penalties on the aircraft. Since the late 1950’s, the most popular vibration control device has been the airframe-mounted, spring-mass vibration absorber. This is a practical device by which vibrations can be reduced, provided the troublesome frequency remains essentially constant, which is true in the case of the helicopter, if the pilot is able to fly the aircraft, so as to hold constant rpm.
Frequently used in combination with the spring-mass absorber or by itself, has been the pendulum absorber, which is mounted on the hub or blades. It has the added advantage of being effective throughout the helicopter’s rpm range, but the disadvantage of only nulling one of the components of vibratory excitation at the rotor hub.
As lower vibration levels have been sought, there has been an increasing trend in the installed weight of passive vibration control devices. For example, one of the first vibration absorbers installed, that on the H-37, weighed on the order of 20 pounds. A nose absorber used on a later helicopter weighed on the order of 60 pounds. A more advanced vibration absorber used by another helicopter company and installed in pairs weighed about 70 pounds each for an installed weight of 140 pounds. A new helicopter now flying in military service carries about 370 pounds of absorber weight.
In contrast, HHC is an electronic, computer-controlled, vibration suppression system which senses and cancels vibrations in a helicopter airframe by high frequency feathering of the rotor blades. With the advent and rapid evolution of the high-speed, lightweight microcomputer, coupled with advances in servo-actuator technology, the means of achieving a quantum of advance in vibration control has now been demonstrated. For a conventional helicopter to be totally retrofitted for this device would require an estimated weight penalty of 3/4 percent of gross weight, but with many of the new proposed helicopters now being considered with fly-by-wire control systems, the cost penalty of HHC is virtually zero. For these aircraft, only contributing to the weight would be the miniaturized, electronic circuit boards for the HHC system, associated/wiring weight, and the small additional weight of HHC panel on the pilot’s instrument console.