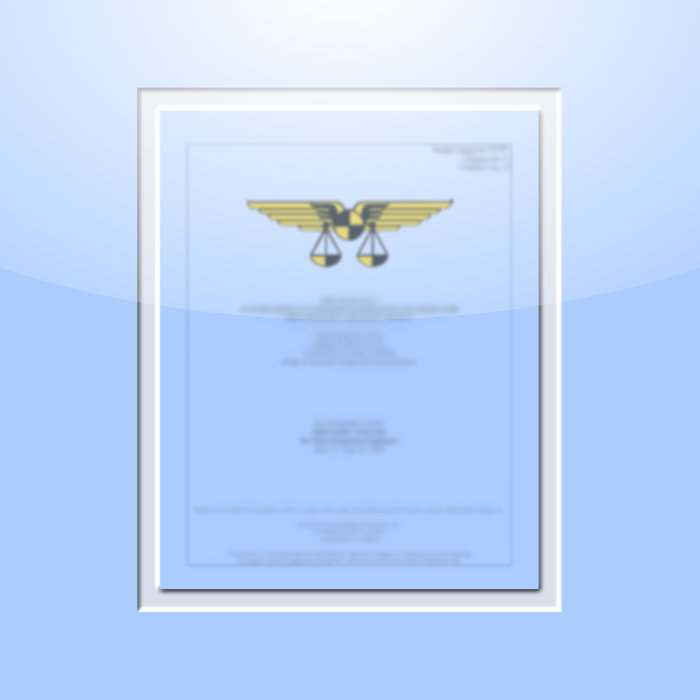
1575. Net-Shape-Full-Density by Injection Molding
$20.00
SAWE Members get a $200 store credit each year.*
*Store credit coupon available at checkout, click the button in your shopping cart to apply the coupon.
Not applicable to SAWE textbooks and current conference technical papers.
Paper
Abstract
Evermore rapid strides into new, barely explored areas of technology result in an incessant demand for high performance materials with superior, often unprecedented properties e.g. biocompatibility for surgical implants, controlled thermal expansion or porosity, hot-corrosion resistance, hermeticity for space environment, cryogenic and superconducting materials, etc.
Cost-effective manufacturing of net-shape-fully-dense system components would considerably assist in resolving some of these challenging difficulties and technologies claiming to achieve this are eagerly sought after by those who want to get or remain at the foremost of progress.
Injection molding, because of its relative freedom to shape intricate geometries has recently-drawn a great deal of attention. In this country alone well over a dozen firms are actively producing or experimenting with metal or ceramic injection molding. Similar efforts are taking place in Europe and Japan.
Regardless of their patents, all injection molding technologies have in common three basic process steps:
– Finding suitable metal or ceramic powders
– Mixing powders with an organic binder and molding ‘green’ parts
– Extracting the binder from the parts and sintering to high density.
The use of micron-sized powders allows for greater packing density or ‘loading’ which results in reduced residual porosity higher density. This in turn amounts to improved strength, fatigue life, wear and stress corrosion resistance and better electro-magnetic properties.
Cost comparison with traditional forming technologies requires the exclusion of part designs which are either unmoldable, too large, too thick as well as those which can easily or satisfactorily be made by conventional P/M. For many applications injection molding is the only viable technology. Between those two groups each case requires individual cost analysis.
Applications include high temperature structural ceramics, mechanical components for high cycle fatigue service, biomedical implants, stainless steels, refractory metals, cemented carbides, electronic and magnetic materials. An updated table of properties on presently available injection molded materials is presented. Some of these materials were only available by fusion metallurgy before. Their advent is an important breakthrough for the P/M industry.