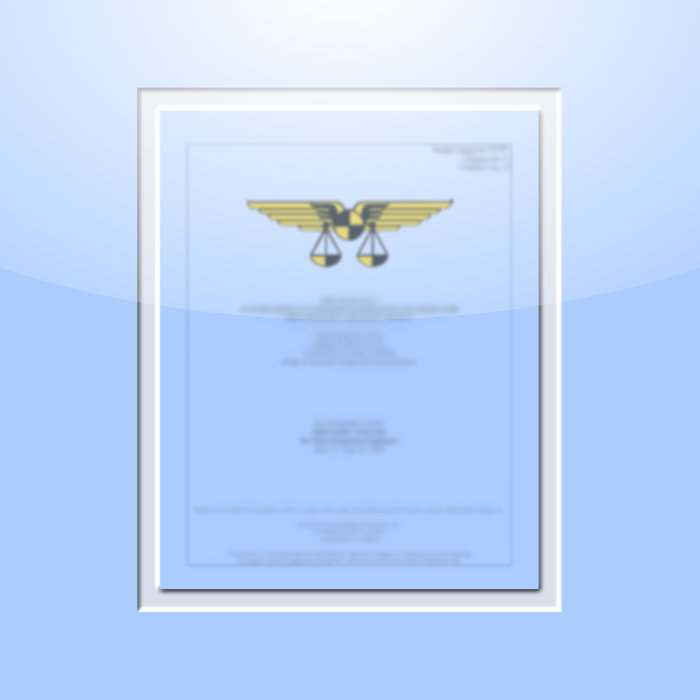
1468. Optimization of Fire Blocking Layers for Aircraft Seating
$20.00
SAWE Members get a $200 store credit each year.*
*Store credit coupon available at checkout, click the button in your shopping cart to apply the coupon.
Not applicable to SAWE textbooks and current conference technical papers.
Paper
Abstract
The use of ablative materials in various forms, such as cellular structures, coating and films to provide thermal protection for heat sensitive substrates against the action of large jet fuel fires is well established (1). Low density foam polymers with low thermal conductivity, high temperature stability and high thermo chemical char yields or high transpirational cooling rates, such as those foam fabricated from isocyanurates, phenolics, imides and hydrated chlorprenes, all have been found to be effective in extend the times required for fuel tank cook off and fire penetration to the structures of transport aircraft immersed in large fuel fires. Char forming ablative coatings, are widely used in extending the time before detonation of military ordinance exposed to similar fire threats. The use of functional fabrics as ablatives is new.
Among existing, commercial polymers, one would be hard pressed to find a more thermally sensitive substrate than conventional flexible polyurethane foams, and probably from a mechanical point of view no better cushioning material with a cost of something like $ 0.15 per board foot . These polymers because of their easily pyrolyzed urethane groups and thermally oxidizable aliphatic linkages exhibit polymer decomposition temperatures of the order of 250’C, and encounter a maximum pyrolysis rate at 300 C with a total yield of pyrolysis vapor of about 95%, most of which is combustible. One should expect these materials to ignite easily with low power energy sources of 2.5 watts/cm2 or less and when ignited effects sustained flame propagation even after removal of heat source. To be sure all non-fire retarded flexible urethane foams that we have examined to date confirm these expectations. From thermogravimetric studies (2), it is evident that the addition of standard fire retardant additives have little or no effect on the maximum decomposition rate, the temperature at which it occurs or the vapor production yield. In fact, one observes the same average mass injection rates of combustible gases under a sustained radiant heating rate from f lexible polyurethane foams whether fire retarded or not. This gas production rate can amount to as much as 10-20×10-5 Grams/cm2/sec at heating rates of 2.5 watts/cm2 even when covered with contemporary upholstery. Kourtides has shown that this flammable gas production rate increase almost linearly with the applied heating rate up to about 6 watt/cm2, heating rates which are fairly typical of a usual trash or jet fuel fire. A value of 4×10-4 grams/cm2/sec for hydrocarbon injection as surfaces has been found to effect sustained propagation and flame spread.
A sustained heating rate of approximately 5 watts/cm2 applied to one seat of a three seat transport array comprising flexible polyurethane foam, fire retarded or not will produce flame spreading and ignition to the adjacent seat in less than one minute, resulting in sufficient fire growth to permit flames to impinge on the aircraft ceiling in less than two minutes. This time required to produce these events and the resulting increases in cabin air temperatures should be expected to fix the allowable egress times fore passengers attempting to escape the aircraft in a post crash fuel fire.
This paper then examines the question of the possibility of increasing the available egress time for passengers, from a transport aircraft, in which the flexible polyurethane seating is exposed to the action of a large pool fire which we must assume can provide at least 5 watts/cm2 radian heat flux to the seats, by providing sufficient ablative protection for polyurethane cushioning. These fire blocking layers must suppress the combustible mass injection rates of the polyurethane below the somewhat critical values of 4×10-4 grams/cm2/sec at 5 watts/cm2 as a performance criteria to prevent flame spread and subsequently flash over.