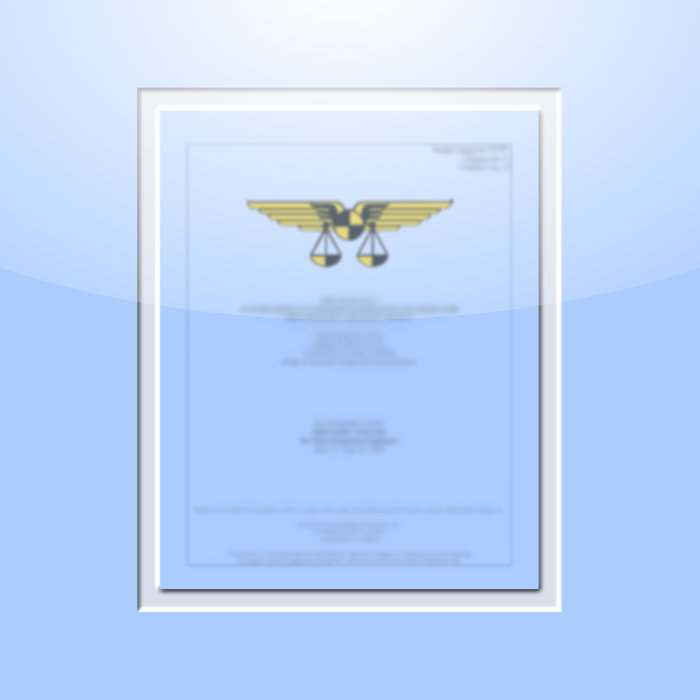
887. Weight Prediction Techniques and Trends for Composite Material Structure
$20.00
SAWE Members get a $200 store credit each year.*
*Store credit coupon available at checkout, click the button in your shopping cart to apply the coupon.
Not applicable to SAWE textbooks and current conference technical papers.
Paper
Abstract
The weight reduction potential of advanced composite materials in aerospace structures is without
parallel. No other material that has been considered or that is presently being investigated combines such high-strength and stiffness with ease of fabrication to result in a practical, light-weight structure. Almost without exception, every study published on the application of composites in aircraft structures indicates at least a 30% weight saving. To date no less than 21 structural components, ranging from a missile inter stage to a rudder have been built and tested. One of these items, the F-4 boron/epoxy rudder, was selected by the Air Force to demonstrate boron/epoxy’s ability to endure actual flight loads and environmental conditions. Fifty rudders were built under this program and forty five have since been placed in operation with F-4 squadrons throughout the world. In 6000 hours of flight time the boron/epoxy rudders have fulfilled all expectations and no problems have been encountered.
Use of boron/epoxy on the F-4 rudder saved 16.2 lb of structure and 6.3 lb of balance weights for a total saving of 22.5 lb or 35%. Most of the hardware development programs achieved weight savings of about 30%, which is in agreement with most of the analytical studies. However, nearly all of the composite application studies investigated replacing existing metal components with similar parts made from composites. This approach is usually taken because it readily identifies the weight saving from substituting composites for metals. Unfortunately this process does not quantify the true weight saving potential of advanced filamentary composites in aerospace structures. Existing metal structural arrangements do not allow the unique properties of composites, such as their high anisotropic mechanical properties, to be used in their most efficient manner.
Maximum weight savings from composites will occur in uni-axially loaded struts and/or trusses and in stiffness-critical components. Also, when reductions are quoted for composite structures it must be realized that not all of the component is composite. So far most development programs used composites only in the cover skins. The substructure and leading and trailing edges were usually not changed. Even with this restricted use, 30% weight savings are common. Studies conducted at McDonnell Aircraft Company (MCAIR) indicate that the weight savings in individual components changed to boron/epoxy are as high as 50% to 60%.
Because advanced composite materials such as boron/epoxy, graphite/epoxy, and boron/aluminum are relatively new and because they possess unfamiliar anisotropic properties, the foremost questions are how to best use them and how to estimate the weight of composite structures. Generally, weight estimation methods are based on statistical or analytical techniques or a combination of each. A large enough database does not yet exist for a meaningful statistical method to be developed for composite structure. The analytical technique involves developing non-optimum factors which can be applied to theoretical results to yield a realistic weight. Unfortunately, non-optimum factors are usually derived from previously built structures of similar arrangement and loading. Once again the data base from which to develop realistic non-optimums is limited, and therefore, the confidence level of the analytical method will be somewhat low until more operational composite structures are built. The weight estimation technique proposed here first estimates the structural weighs as though it were aluminum and then modifies the estimate through several factors, accounting for the different mechanical properties and construction techniques, to arrive at a composite material structural weight. This approach accounts for non-optimum weight by using reliable and proven methods for aluminum structure. It is then logical that the weight change from aluminum to composite structure will be a function of the mechanical properties of each material and any change in construction that might occur.
The factors previously mentioned account for the weight to strength comparison between the materials in various failure modes. The fraction of each component weight designed by the various failure modes is related to construction techniques, geometry, and loading. All of these items can readily be identified with reasonable accuracy during conceptual design studies.