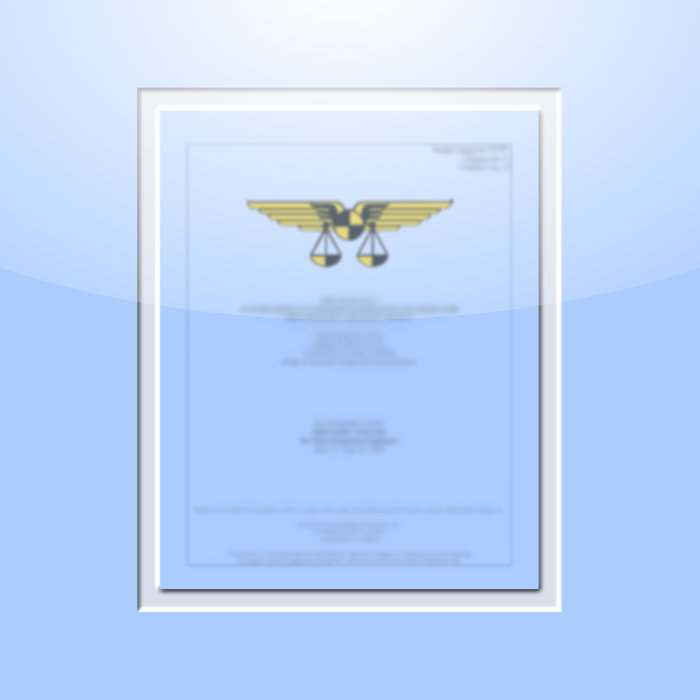
363. Brazed Stainless Steel Honeycomb Saves Weight in High Temperature Application
$20.00
SAWE Members get a $200 store credit each year.*
*Store credit coupon available at checkout, click the button in your shopping cart to apply the coupon.
Not applicable to SAWE textbooks and current conference technical papers.
Paper
Abstract
This paper was presented at the Twenty-second Annual National Conference of the Society of Aeronautical Weight Engineers at St. Louis, Missouri, April 29-May 1, 1963. Stainless steel sandwich structures are not newcomers to the aerospace industry. In fact, they have been covered by theories and texts for approximately 35 years. It is only within the past decade, however, that manufacturing techniques have been developed to the extent that brazed sandwich structures have become economically feasible. Their use is primarily in compression structures but the isolative qualities can be used advantageously in the proper applications. This paper deals with the application of brazed stainless sandwich for a design condition that developed external compression loads on the tailpipe which were created by rapid power setting changes on the engine. Conventional single-skin tailpipe design, under this condition, would have resulted in an excessively heavy piece of structure. Because of space limitations external frames would have been quite ineffective.
Selection of the brazed sandwich structure involved several problems that were overcome with proper design. The insulative qualities of this structure were held to a minimum by selection of a high conductivity braze alloy and a minimum overall sandwich height. An additional problem was associated with the insulative qualities to the extent that the differential temperatures between the inner and outer skin resulted in differential axial and circumferential growth. The tailpipe is fixed at the forward end so all axial growth is aft. To avoid high shear stresses in the core, a structural ring was added to the aft end for distribution of axial growth loads.
Use of brazed stainless steel sandwich structure for this application resulted in a weight saving of approximately 30 pounds/unit over a conventional skin-frame combination, and a 110 pound/unit saving over a single-skin structure.