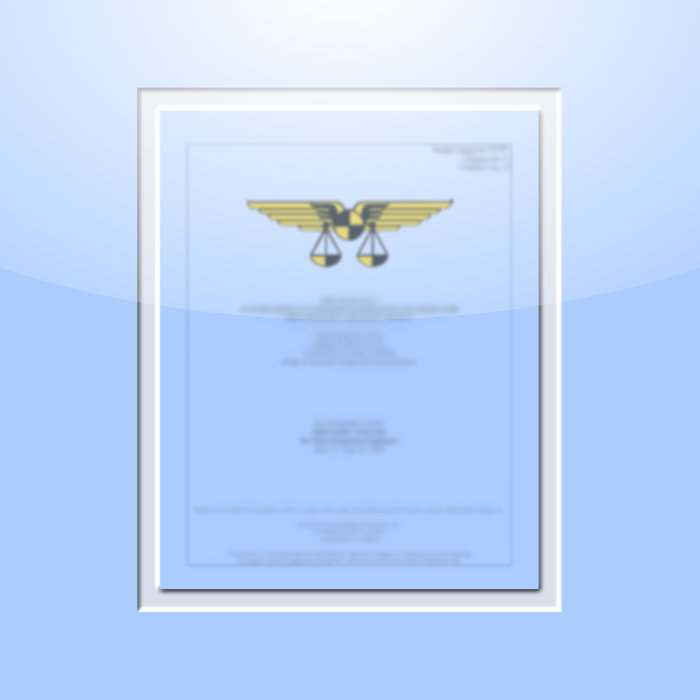
368. Learning to Live With Electronic Weighing
$20.00
SAWE Members get a $200 store credit each year.*
*Store credit coupon available at checkout, click the button in your shopping cart to apply the coupon.
Not applicable to SAWE textbooks and current conference technical papers.
Paper
Abstract
This paper was presented at the Twenty-second Annual National Conference of the Society of Aeronautical Weight Engineers at St. Louis, Missouri, April 29-May 1, 1963. The decision by Douglas Aircraft Company to rely chiefly on electronic rather than mechanical systems for its overall research and development (R & D) missiles and space weighing operations was based on several considerations. These included convenience of use, portability, accuracy, and relative cost.
Application of the earlier electronic systems, however, left much to be desired. End-to-end calibration was mandatory. Repairs usually necessitated return of the entire unit to the manufacturer. Additional weighing requirements, involving different capacity load cells, meant procuring a complete new system. Still another problem, although not the fault of the systems themselves, was the lack of adequate calibration and evaluation test facilities. The whole operation thus was costly, time-consuming, and otherwise unacceptable.
The solution to these problems called for a re-evaluation of the overall weighing requirements. It was then possible to specify a system which would meet these requirements. Interchangeability of components was the most essential prerequisite, and upon this concept the universal system was founded.
In order to verify the characteristics and capabilities of the universal system, certain tests were necessary. By establishing dead weight loading facilities at its Santa Monica, California, location, Douglas not only could perform these tests, but could also assume the responsibility for accurate periodic certification, a function previously either delegated to the National Bureau of Standards, performed by inaccurate methods, or foregone altogether.
Test results did, in fact, demonstrate that load cells, cables, and even the indicating instruments themselves could be interchanged without any significant loss of accuracy. ‘Creep’, the change in load cell output with time, was found to vary from one cell to another; in some cells, as much as 0.05 percent creep was present. The lack of a direct reading capability, a consequence of the internal design of the universal system, necessitated the use of correction curves or tables in order to obtain the desired accuracy of 0.1 percent, but due to the nature of R&D operations, this did not detract appreciably from the system.
Further tests uncovered errors in the order of 0.2 percent due to misalignment of the load cell and mechanical fittings. These tests were repeated using various flexures or pivots for isolation of loads into the cells, the results of which showed that the effect of misalignment could be virtually eliminated.
Efficiency of the weighing operations was improved by initiating an IBM computer program to handle and process data. Additional improvement could be realized by standardization of test procedures, facilities, and equipment. Continued investigations are recommended to further the ‘state of the art’ of electronic weighing, particularly with respect to compression load application.